Karcher HD 7-16-4 ST: Troubleshooting
Troubleshooting: Karcher HD 7-16-4 ST

-
7
In order to guarantee a reliable operation
og the equipment, we success, you signed
a maintenance agreement. Please refer to
you local Kärcher service department.
Who may perform maintenance?
Operator
Work designated with the sign “Opera-
tor” may only be carried out by persons
who have been instructed in the safe
operation and maintenance on the high
pressure plant.
Electricians
Only persons with a professional train-
ing in the electro-technical area.
Customer Service
Work designated with the sign “Cus-
tomer Service” may only be done by the
fitters of Kärcher Customer Service.
WARNING
Risk of burns due to hot oil or hot parts of
the plant. Allow the pump to cool down for
minutes before oil change.
Note:
Used oil must only be disposed of by the
designated collection points. Please turn in
used oil there. Polluting the environment
with used oil is prosecutable.
For oil type refer to technical specifica-
tions.
1 Oil tank
2 Oil drain screw
Place the collection trough under the oil
drain screw.
Remove the lid of the oil container.
Unscrew the oil drain screw and collect
oil.
Fix in the oil drain screw and tighten it.
Slowly fill in new oil until the "MAX"
marking on the oil container.
Attach the lid of the oil container.
Dispose of old oil ecologically or turn it
in at a collection point.
Calcium deposits can lead to:
– higher pipe resistances
– even to failure of the components with
heavy calcium deposits
DANGER
–
Risk of explosion due to combustible
gases! Smoking strictly prohibited dur-
ing decalcification. Ensure proper ven-
tilation.
–
Risk of chemical burns on account of
acid! Wear protective glasses and pro-
tective gloves.
Note:
– Follow the specifications of the accident
prevention regulation BGV A1.
– Follow instructions for use on the lable
of the decalcifying agent.
According to statutory requirements, only
tested and approved boiler decrusting
agents may be used.
– RM 100 (Order No. 6.287-008) dis-
solves chalk and simple compounds of
chalk and detergents residues.
– RM 101 (Order No. 6.287-013) dis-
solves the deposits that cannot be dis-
solved using RM 100.
Note:
As an anti-corrosion measure and for neu-
tralising the acid residue, we recommend
that you finally pump an alkaline solution
through the machine (for e.g. RM 81) via
the detergent tank.
First decalcify the swimmer tank.
Shut off water supply.
Remove the lid of the swimming tank.
Remove the hose from the suction site
of the pump for the swimming tank on
the pump site.
Seal the free end of the hose.
Fill in 7 percent decalcification solution.
Remove resin completely from the tank
after decalcification.
Decalcify the high pressure installation:
Remove the high pressure hose from
the network supply and hang it in the
swimmer tank.
Run the calcium dissolving acid mixture
prepared in the tank through the instal-
lation's cycle, allow it to take effect,
rinse.
DANGER
Risk of electric shock.
Risk of injury! Switch off the power switch
with all maintenance and repair work.
Pull the mains plug and secure it against
being plugged in again
DANGER
Risk of injury on account of the emanating
water jet that could be hot!
DANGER
Risk of accident while working on the unit!
During all tasks:
–
Close locking tap of fresh water.
–
Let the hot parts of the plant cool down.
–
Depressurise the plant by opening all
hand-spray guns.
Who may remedy faults?
Operator
Work designated with the sign “Opera-
tor” may only be carried out by persons
who have been instructed in the safe
operation and maintenance on the high
pressure plant.
Electricians
Only persons with a professional train-
ing in the electro-technical area.
Customer Service
Work designated with the sign “Cus-
tomer Service” may only be done by the
fitters of Kärcher Customer Service.
Maintenance contract
Maintenance Works
Oil change
Descaling
Troubleshooting
24
EN
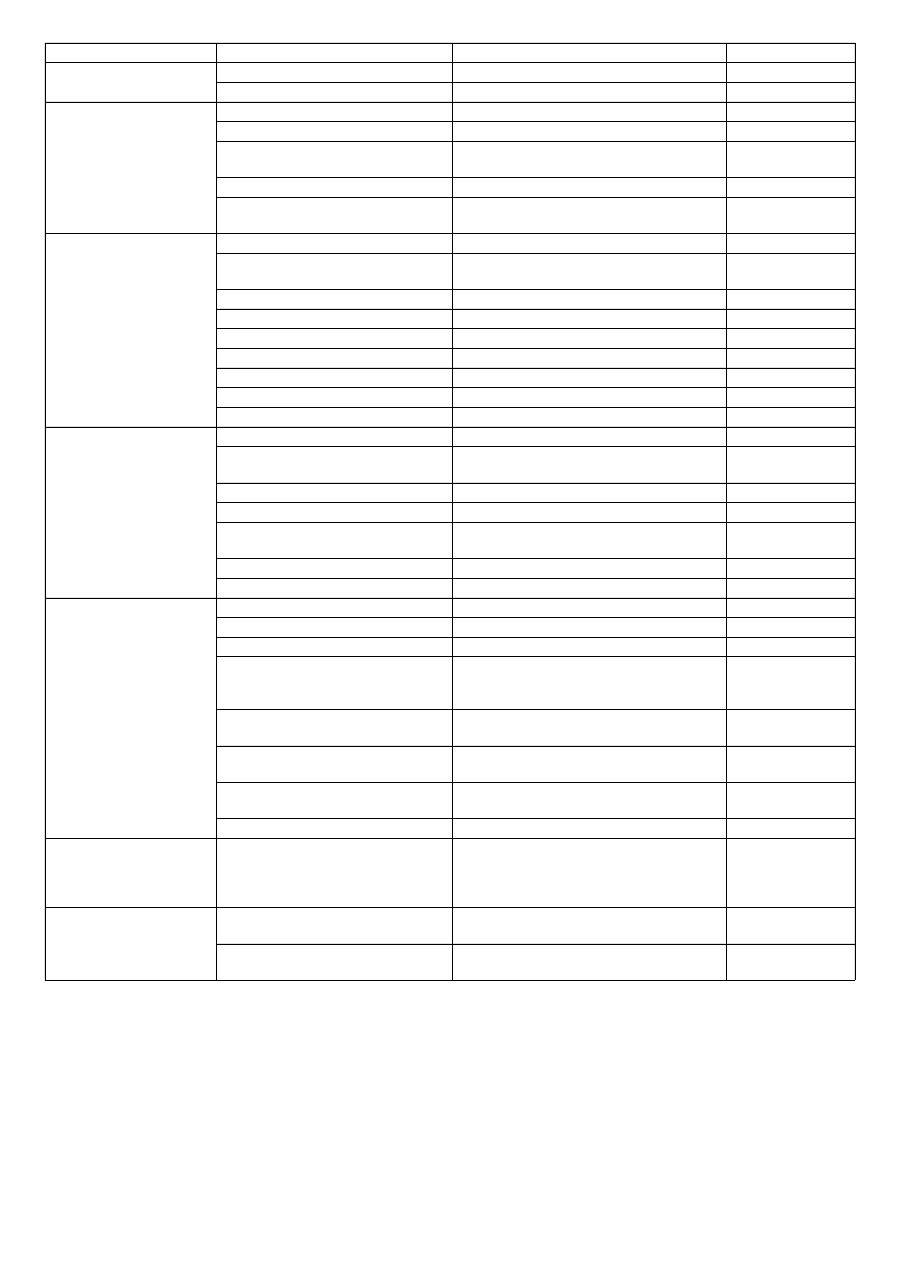
-
8
Fault
Possible cause
Remedy
of whom
Water stream is uneven.
Nozzle is blocked.
Clean the nozzle.
Operator
Amount of water supply is too low.
Check water supply.
Operator
Inadequate or no flow of de-
tergent
Dosage adjusted too low.
Increase dose.
Operator
Nozzle is set to "High pressure".
Set nozzle to "CHEM".
Operator
Suction filter in the detergent tank is
dirty.
Clean the suction filter.
Operator
Detergent suck hose leaking.
Replace suck hose.
Customer Service
Manual detergent dispensing valve oc-
cluded, defective.
Check; clean, replace, if required.
Customer Service
Pressure does not build up
in the pump
Nozzle is set to "CHEM"
Set nozzle to "High pressure".
Operator
Air in the high pressure pump
Ventilate the appliance (see "System start-
up")
Operator
Suction site pipe leaking.
Check screw fittings and hoses.
Operator
Not enough water
Ensure adequate water supply.
Operator
Sieve in the water inlet is dirty
Clean sieve.
Operator
High pressure hose leaking.
Replace high pressure hose.
Customer Service
Piping leaking.
Repair piping system.
Customer Service
Flow regulator defective.
Test flow regulator, repair.
Customer Service
The valve in the pump is defective.
Replace valve.
Customer Service
High pressure pump is
knocking; manometer (op-
tion) is swaying wildly
Vibration dampener is defective.
Replace vibration dampener.
Operator
Water pump does not suck in adequate
air.
Check suction system and remove leaks.
Operator
Detergent container is empty
Refill detergent tank.
Operator
Water flow temperature too hot.
Lower water temperature.
Operator
Water flow blocked.
Clean sieve in the water inlet, check the water
flow.
Operator
Valve plate or valve spring is defective. Replace parts
Customer Service
Advance pump calcified or defective. Check advance pump.
Operator
The installation does not
start when switched on or
when pressing the remote
control (optional).
Appliance switch is switched off
Turn it on.
Operator
On-board electricity supply interrupted. Turn it on.
Operator
Pressure switch is defective
Replace pressure switch.
Customer Service
Motor protection switch was trigged by
overflow or loss of a phase of the elec-
tricity supply.
Check the voltage of the three phases.
Electrician/ Custom-
er Service
Motor protection switch is set incorrect-
ly.
Adjust according to circuit diagram.
Electrician/ Custom-
er Service
Motor protection switch for controls and
advance pressure pump triggered.
Check motor protection switch.
Electrician/ Custom-
er Service
Control safety transformer defective.
Examine the cause, replace the control safety
device.
Electrician/ Custom-
er Service
Circuit board defective.
Check circuit board, replace if required.
Customer Service
Pump starts during the
stand-by period and not
when the hand spray gun is
opened.
Pressure switch or pressure switch ca-
ble defective.
Replace the pressure switch or cable.
Customer Service
Installation does not switch
off.
Pump is drawing in air over the empty
detergent tank.
Refill the detergent tank, ventilate suction
line.
Operator
Pressure switch is defective.
Replace pressure switch.
Electrician/ Custom-
er Service
25
EN
Оглавление
- Inhaltsverzeichnis
- Bestimmungsgemäße Verwendung
- Funktion
- Geräteelemente
- Transport Lagerung des Gerätes Pflege und Wartung
- Hilfe bei Störungen
- Technische Daten
- Zubehör
- Anlageninstallation
- EG-Konformitätserklärung
- Kundendienst
- Contents
- Proper use
- Function
- Device elements
- Transport Storing the device Maintenance and care
- Troubleshooting
- Technical specifications
- Accessories
- Installing the plant
- EC Declaration of Conformity
- Customer Service
- Πίνακας περιεχομένων
- Χρήση σύμφωνα με τους κανονισμούς
- Λειτουργία
- Στοιχεία συσκευής
- Μεταφορά Αποθήκευση της συσκευής Φροντίδα και συντήρηση
- Αντιμετώπιση βλαβών
- Τεχνικά χαρακτηριστικά
- Εξαρτήματα
- Εγκατάσταση μονάδας
- Δήλωση Συμμόρφωσης των Ε . Κ .
- Υπηρεσία εξυπηρέτησης πελατών
- İ çindekiler
- Kurallara uygun kullan ı m
- Fonksiyon
- Cihaz elemanlar ı
- Ta ş ı ma Cihaz ı n depolanmas ı Koruma ve Bak ı m
- Ar ı zalarda yard ı m
- Teknik Bilgiler
- Aksesuar
- Sistem tesisat ı
- AB uygunluk bildirisi
- Mü ş teri hizmeti
- Оглавление
- Использование по назначению
- Назначение
- Элементы прибора
- Транспортировка Хранение прибора
- Уход и техническое обслуживание
- Помощь в случае неполадок
- Технические данные
- Принадлежности
- Инсталляция оборудования
- Заявление о соответствии ЕС
- Сервисная служба
- Spis tre ś ci
- U ż ytkowanie zgodne z przeznaczeniem
- Funkcja
- Elementy urz ą dzenia
- Transport Przechowywanie urz ą dzenia Czyszczenie i konserwacja
- Usuwanie usterek
- Dane techniczne
- Akcesoria
- Instalacja urz ą dzenia
- Deklaracja zgodno ś ci UE
- Serwis firmy
- Sisukord
- Sihipärane kasutamine
- Funktsioon
- Seadme elemendid
- Transport Seadme ladustamine Korrashoid ja tehnohooldus
- Abi häirete korral
- Tehnilised andmed
- Tarvikud
- Seadme installeerimine
- EÜ vastavusdeklaratsioon
- Klienditeenindus
- Satura r ā d ī t ā js
- Noteikumiem atbilstoša lietošana
- Darb ī ba
- Apar ā ta elementi
- Transport ē šana Apar ā ta uzglab ā šana Kopšana un tehnisk ā apkope
- Pal ī dz ī ba darb ī bas trauc ē jumu gad ī jum ā
- Tehniskie dati
- Piederumi
- Iek ā rtas instal ā cija
- EK Atbilst ī bas deklar ā cija
- Klientu apkalpošanas dienests
- Turinys
- Naudojimas pagal paskirt į
- Veikimas
- Prietaiso dalys
- Transportavimas Į renginio laikymas Prieži ū ra ir aptarnavimas
- Pagalba gedim ų atveju
- Techniniai duomenys
- Dalys
- Prietaiso į rengimas
- EB atitikties deklaracija
- Klient ų aptarnavimo tarnyba
- Зміст
- Правильне застосування
- Призначення
- Елементи приладу
- Транспортування Зберігання пристрою Догляд та технічне обслуговування
- Допомога у випадку неполадок
- Технічні характеристики
- Аксесуари
- Монтаж обладнання
- Заява при відповідність Європейського співтовариства
- Служба підтримки користувачів