Karcher HDS 13-20-4 S – страница 2
Инструкция к Автомойке Karcher HDS 13-20-4 S
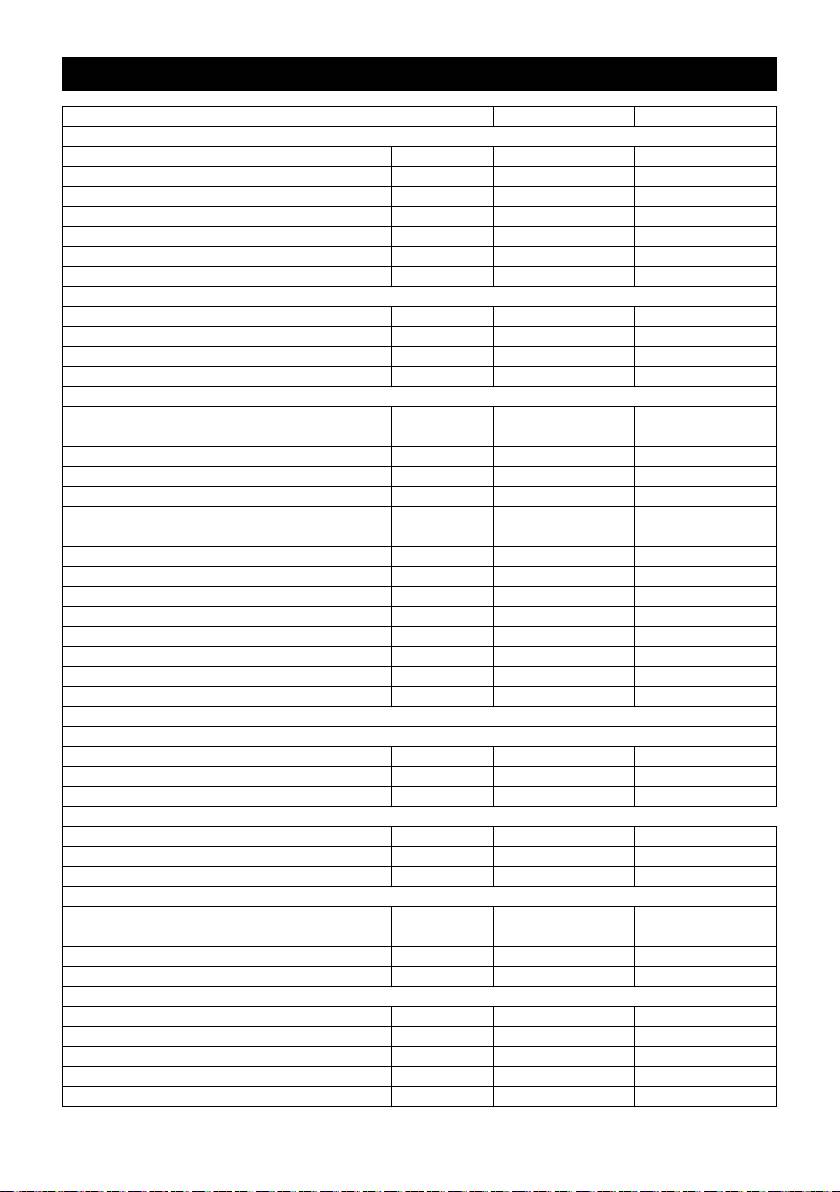
Technische Daten
HDS 13/20 HDS 13/20
Netzanschluss
Spannung V 230 400
Stromart Hz 3~ 50 3~ 50
Anschlussleistung kW 9,3 9,3
Absicherung (träge) A 55 32
Schutzart -- IPX5 IPX5
Schutzklasse -- I I
Maximal zulässige Netzimpedanz Ohm (0.159+j0.100) (0.159+j0.100)
Wasseranschluss
Zulauftemperatur (max.) °C 30 30
Zulaufmenge (min.) l/h (l/min) 1500 (25) 1500 (25)
Saughöhe aus offenem Behälter (20 °C) m 0,5 0,5
Zulaufdruck (max.) MPa (bar) 0,6 (6) 0,6 (6)
Leistungsdaten
Fördermenge Wasser l/h (l/min) 600-1300 (10-
600-1300 (10-
21,6)
21,6)
Arbeitsdruck Wasser (mit Standarddüse) MPa (bar) 3-20 (30-200) 3-20 (30-200)
Max. Betriebsüberdruck (Sicherheitsventil) MPa (bar) 24 (240) 24 (240)
Fördermenge Dampfbetrieb l/h (l/min) 600-650 (10-10,8) 600-650 (10-10,8)
Max. Arbeitsdruck Dampfbetrieb (mit Dampf-
MPa (bar) 3,2 (32) 3,2 (32)
düse)
Teile-Nr. Dampfdüse -- 2.885-043.0 2.885-043.0
Max. Arbeitstemperatur Heißwasser °C 98 98
Arbeitstemperatur Dampfbetrieb °C 155 155
Reinigungsmittelansaugung l/h (l/min) 0-78 (0-1,3) 0-78 (0-1,3)
Brennerleistung kW 108 108
Maximaler Heizölverbrauch kg/h 8,3 8,3
Rückstoßkraft der Handspritzpistole (max.) N 40,3 40,3
Düsengröße (SX) -- 070 (072) 070 (072)
Ermittelte Werte gemäß EN 60335-2-79
Geräuschemission
Schalldruckpegel L
pA
dB(A) 74 74
Unsicherheit K
pA
dB(A) 2 2
Schallleistungspegel L
WA
+ Unsicherheit K
WA
dB(A) 91 91
Hand-Arm Vibrationswert
2
Handspritzpistole m/s
1,66 1,66
2
Strahlrohr m/s
5,85 5,85
2
Unsicherheit K m/s
1,0 1,0
Betriebsstoffe
Brennstoff -- Heizöl EL oder
Heizöl EL oder
Diesel
Diesel
Ölmenge l 1,0 1,0
Ölsorte -- SAE 90 SAE 90
Maße und Gewichte
Länge x Breite x Höhe mm 1330 x 750 x 1060 1330 x 750 x 1060
Typisches Betriebsgewicht, S kg 200 200
Typisches Betriebsgewicht, SX kg 205 205
Brennstofftank l 25 25
Reinigungsmitteltank l 10+20 10+20
– 15
21DE
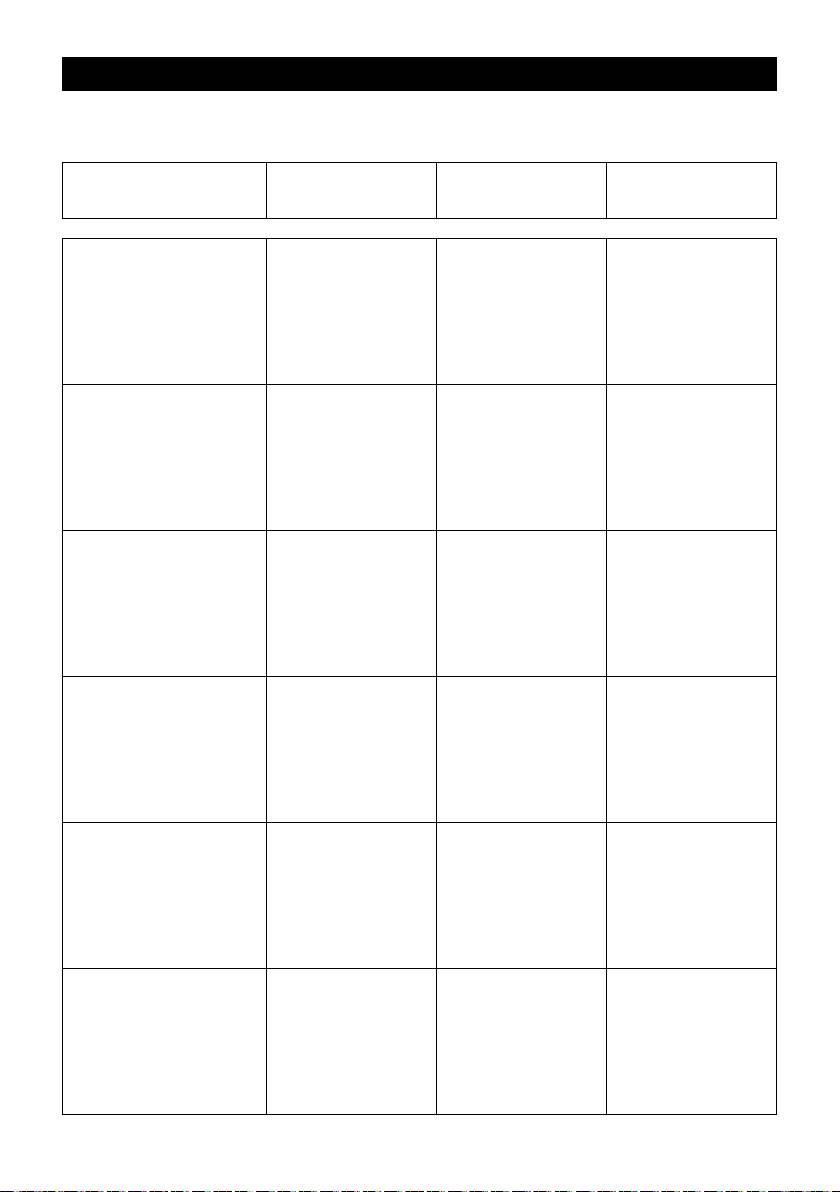
Wiederkehrende Prüfungen
Hinweis: Die Prüffristempfehlungen entsprechend der jeweiligen nationalen Anforderun-
gen des Betreiberlandes sind zu beachten.
Prüfung durchge-
Äußere Prüfung Innere Prüfung Festigkeitsprü-
führt durch:
fung
Name Unterschrift der be-
Unterschrift der be-
Unterschrift der be-
fähigten Person/
fähigten Person/
fähigten Person/
Datum
Datum
Datum
Name Unterschrift der be-
Unterschrift der be-
Unterschrift der be-
fähigten Person/
fähigten Person/
fähigten Person/
Datum
Datum
Datum
Name Unterschrift der be-
Unterschrift der be-
Unterschrift der be-
fähigten Person/
fähigten Person/
fähigten Person/
Datum
Datum
Datum
Name Unterschrift der be-
Unterschrift der be-
Unterschrift der be-
fähigten Person/
fähigten Person/
fähigten Person/
Datum
Datum
Datum
Name Unterschrift der be-
Unterschrift der be-
Unterschrift der be-
fähigten Person/
fähigten Person/
fähigten Person/
Datum
Datum
Datum
Name Unterschrift der be-
Unterschrift der be-
Unterschrift der be-
fähigten Person/
fähigten Person/
fähigten Person/
Datum
Datum
Datum
22 DE
– 16
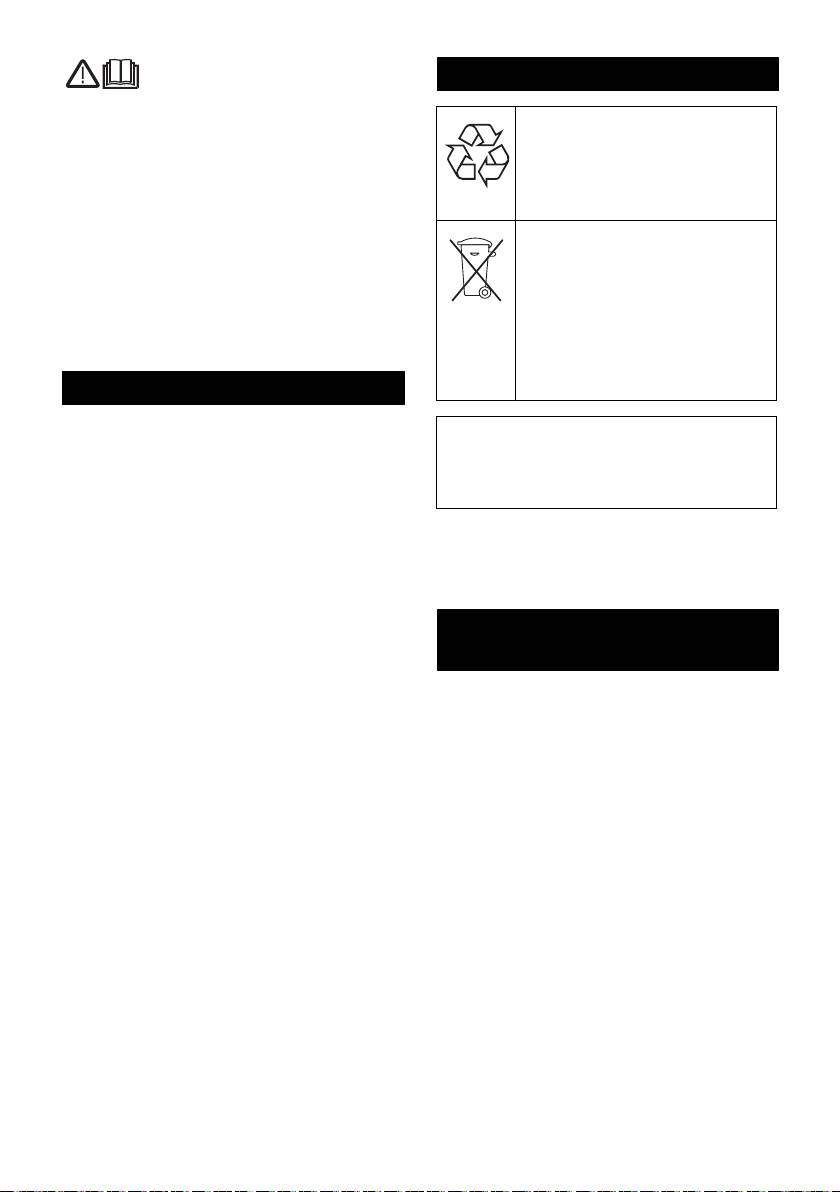
Please read and comply with
Environmental protection
these original instructions prior
to the initial operation of your appliance and
The packaging material can be
store them for later use or subsequent own-
recycled. Please do not throw
ers.
the packaging material into
– Before first start-up it is definitely nec-
household waste; please send it
essary to read the operating instruc-
for recycling.
tions and safety indications Nr. 5.951-
Old appliances contain valuable
949.0!
materials that can be recycled;
– In case of transport damage inform ven-
these should be sent for recy-
dor immediately
cling. Batteries, oil, and similar
– Check the contents of the pack before
substances must not enter the
unpacking. For scope of delivery see il-
environment. Please dispose of
lustration 1.
your old appliances using ap-
Contents
propriate collection systems.
Environmental protection . . EN . . .1
Please do not release engine oil, fuel oil,
diesel and petrol into the environment Pro-
Symbols in the operating in-
structions . . . . . . . . . . . . . . EN . . .1
tect the ground and dispose of used oil in
Overview . . . . . . . . . . . . . . EN . . .2
an environmentally-clean manner.
Symbols on the machine . . EN . . .3
Notes about the ingredients (REACH)
Proper use . . . . . . . . . . . . . EN . . .3
You will find current information about the
Safety instructions . . . . . . . EN . . .3
ingredients at:
Safety Devices . . . . . . . . . . EN . . .4
www.kaercher.com/REACH
Start up. . . . . . . . . . . . . . . . EN . . .4
Symbols in the operating
Operation . . . . . . . . . . . . . . EN . . .6
instructions
Storage. . . . . . . . . . . . . . . . EN . .10
Transport . . . . . . . . . . . . . . EN . .10
Danger
Maintenance and care . . . . EN . .10
Immediate danger that can cause severe
Troubleshooting . . . . . . . . . EN . .11
injury or even death.
Warranty. . . . . . . . . . . . . . . EN . .13
몇 Warning
Accessories and Spare Parts EN . .13
Possible hazardous situation that could
EC Declaration of Conformity EN . .14
lead to severe injury or even death.
Technical specifications . . . EN . .15
Caution
Recurring tests . . . . . . . . . . EN . .16
Possible hazardous situation that could
lead to mild injury to persons or damage to
property.
– 1
23EN
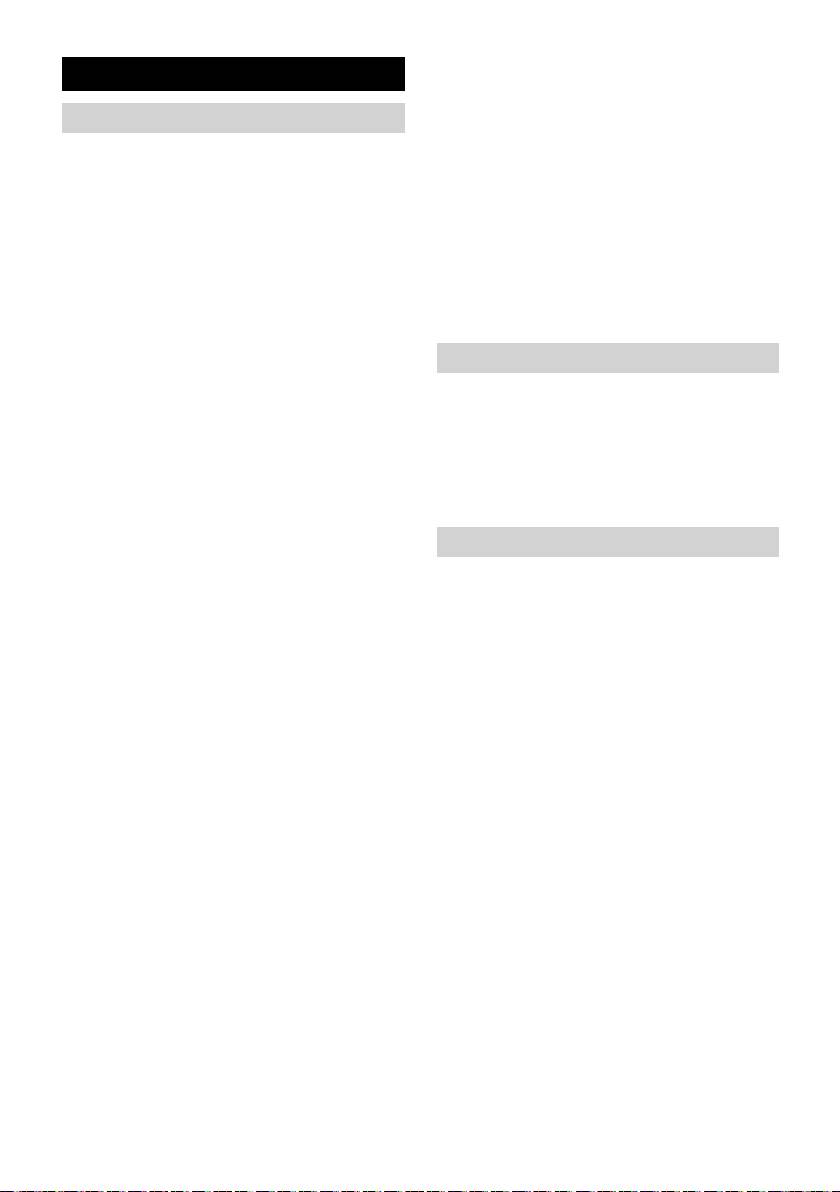
33 Oil tank
Overview
34 Pressure/quantity regulation of the
pump unit
Device elements
35 Oil drain screw
Figure 1
36 Backflow valve of the detergent infeed
1 Cover
37 Detergent suction hose 1 with filter
2 Support for spray lance
38 Detergent suction hose 2 with filter
(both sides)
39 Fuel filter
3 System care Advance RM 110/RM 111
40 Service switch
4 Steering roller with fixed position brake
41 Water shortage safe guard with sieve
5 Mounting location for transport
42 Float tank
(both sides)
43 Fine filter (water)
6 Wheel
Operating field
7 Water supply set
8 High pressure connection
Figure 2
(nur S)
A Power switch
9 O-ring set (for replacement)
B Temperature controller
10 High pressure hose
C Dosage valve for detergent
11 Hand spray gun
D Manometer
12 Spray lance
E Display
13 High-pressure nozzle (stainless steel)
Colour coding
14 Steam nozzle (brass)
– The operating elements for the cleaning
15 Pressure/ quantity regulation at the
process are yellow.
hand spray gun
– The controls for the maintenance and
16 Safety latch of the hand spray gun
service are light gray.
17 Power supply
18 Folding compartment
(nur S)
19 Connection for water supply with filter
20 Exit opening of the high-pressure hose
(SX only)
21 Step depression
22 Pouring vent for detergent 2
23 Hand crank for hose drum
(SX only)
24 Pouring vent for detergent 1
25 Hose drum
(SX only)
26 Pouring vent for fuel
27 Handle
28 Operating field
29 Closing flap for storage compartment
30 Storage compartment for accessories
31 Nameplate
32 Cover lock
24 EN
– 2
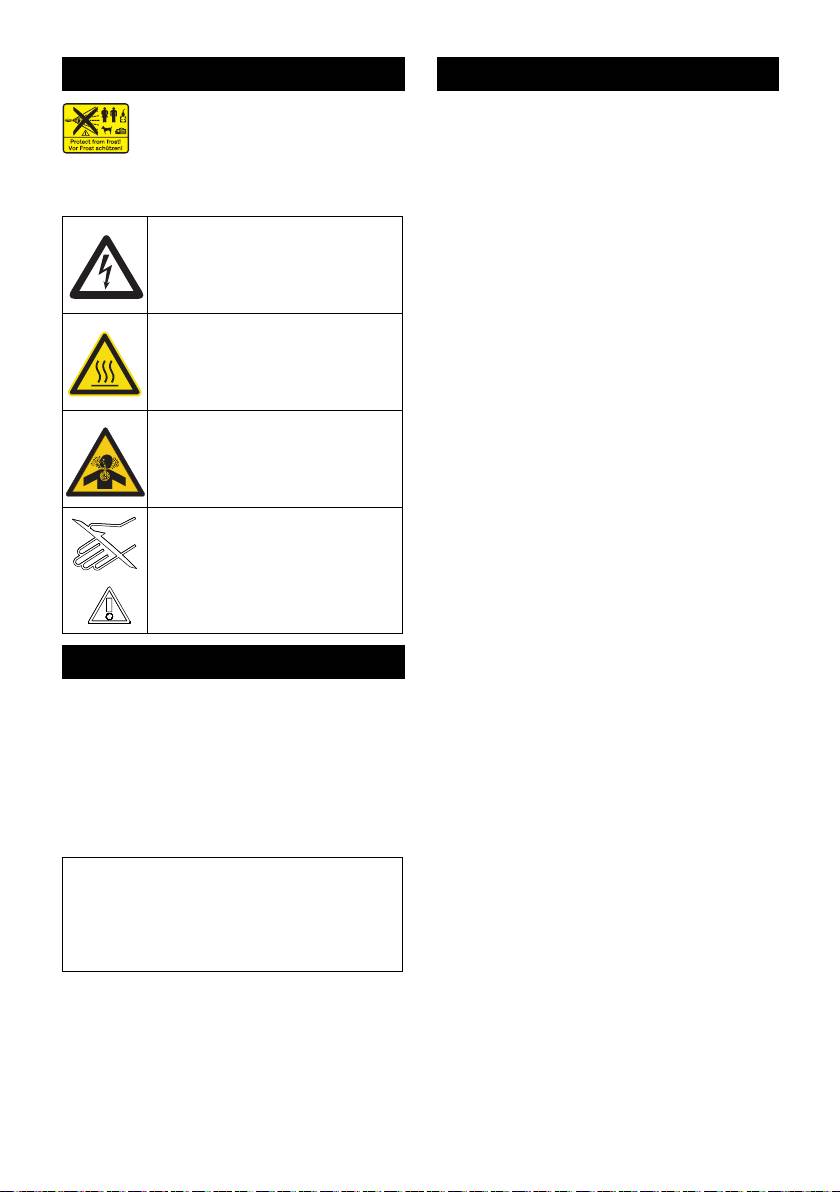
Symbols on the machine
Safety instructions
High-pressure jets can be dan-
– Please follow the national rules and
gerous if improperly used. The
regulations for fuel spray jets of the re-
jet may not be directed at per-
spective country.
sons, animals, live electrical equipment or
– Please follow the national rules and
at the appliance itself.
regulations for accident prevention of
the respective country. Fuel spray jets
Risk of electric shock!
must be tested regularly and the results
Only electricians or authorised
of these tests must be documented in
technicians are permitted to
writing.
work on parts of the plant.
– The heating appliance of the machine is
Risk of burns on account of hot
an ignition plant. All national laws and
surfaces!
regulations about heating systems must
also be followed.
– As per the applicable national guide-
Risk of poisoning! Do not
lines, the first time this high-pressure
breathe in the exhaust fumes.
cleaner must be taken into operation by
a skilled person. KÄRCHER has al-
ready performed this initial start-up for
you and has documented it accordingly.
Risk of injury! Do not reach in.
The documentation can be requested at
your KÄRCHER partner. Please have
the part and plant number of the appli-
ance available when enquiring about
the documentation.
– We would like to point out that the appli-
Proper use
ance must be repeatedly checked by a
skilled person as prescribed by the ap-
Cleaning of: Machines, Vehicles, Struc-
plicable national regulations. Please
tures, Tools, Facades, Terraces, Garden-
contact your KÄRCHER partner.
ing tools, etc.
Danger
Risk of injury! Follow the respective safety
regulations when operating at gas stations
or other dangerous areas.
Please do not let mineral oil contaminated
waste water reach soil, water or the sew-
age system. Perform engine cleaning and
bottom cleaning therefore only on speci-
fied places with an oil trap.
– 3
25EN
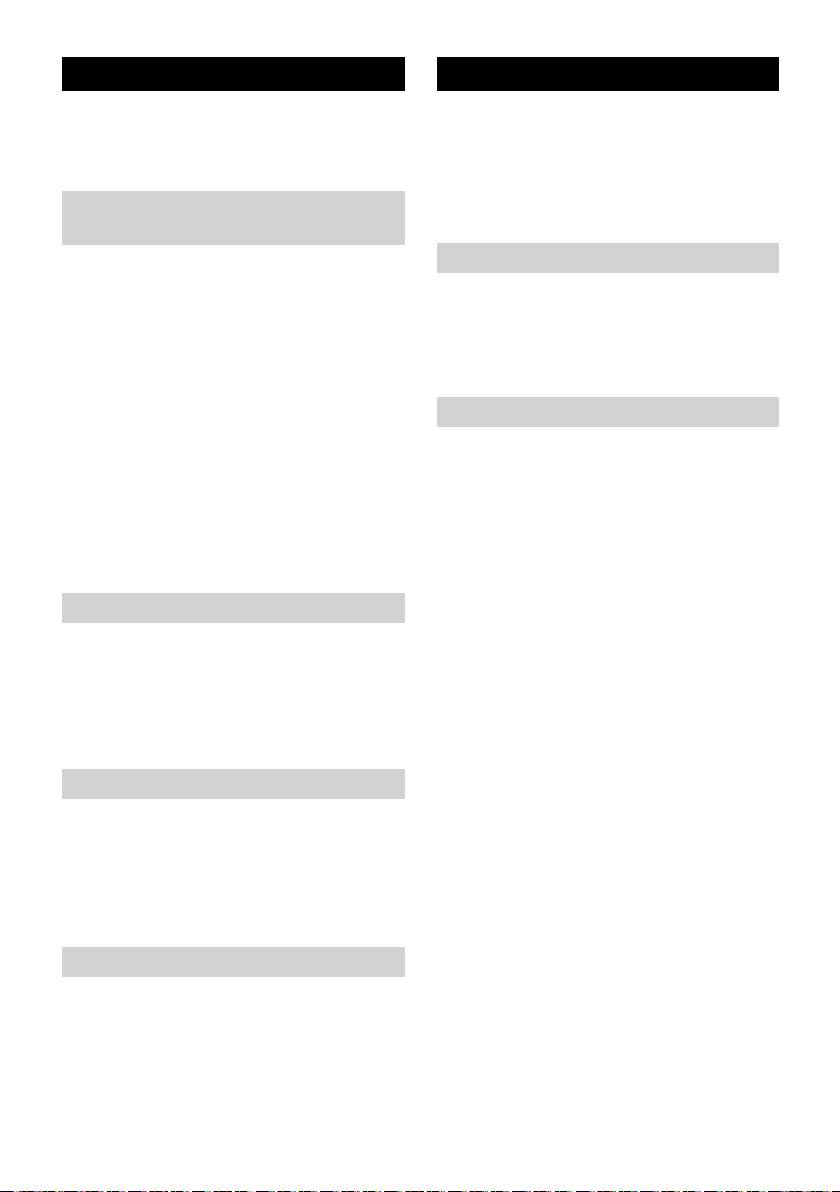
Safety Devices
Start up
Safety devices serve for the protection of
몇 Warning
the user and must not be put out of opera-
Risk of injury! Device, tubes, high pressure
tion or bypassed with respect to their func-
hose and connections must be in faultless
tion.
condition. Otherwise, the appliance must
Overflow valve with two pressure
not be used.
Lock parking brake.
switches
Installing the handle
– While reducing the water supply at the
pump head or with the Servopress -
Figure 3
regulation the overflow valve opens and
Caution
part of the water flows back to the pump
Hook the electric supply line into the cable
suck side.
guide of the right handle bow. Ensure that
– If the hand-spray gun is closed, so that
the cable is not damaged.
the whole water flows back to the pump
Replace the system care bottle
suck side, the pressure switch at the
overflow valve shuts down the pump.
Note: Push the bottle in securely to pene-
– If the hand spray gun is opened, the
trate the closure. Do not remove bottle until
pressure switch on the cylinder head
it is empty.
turns the pump back on.
Note: To protect the device, the burner is
The overflow valve is set by the manufac-
switched off 5 hours after the system care
turer and sealed. Setting only by customer
bottle is empty.
service.
– The system care prevents the calcifica-
tion of the heating spiral while operating
Safety valve
with calciferous tap water. It is dosed
into the supply in the float container
– The safety valve opens, when the over-
drop by drop.
flow valve resp. the pressure switch is
– The metering is set to medium water ri-
broken.
gidity by the manufacturer
The safety valve is set by the manufacturer
Note: A system care bottle is included in
and sealed. Setting only by customer ser-
the delivery.
vice.
Replace the system care bottle.
Water shortage safeguard
– The water shortage safeguard prevents
the burner to be turned on when there is
water shortage.
– A sieve prevents the contamination of
the safeguard and must be cleaned reg-
ular.
Temperature stop for exhaust gases
– The temperature stop switches off the
machine when the waste gases have
reached very high temperatures.
26 EN
– 4
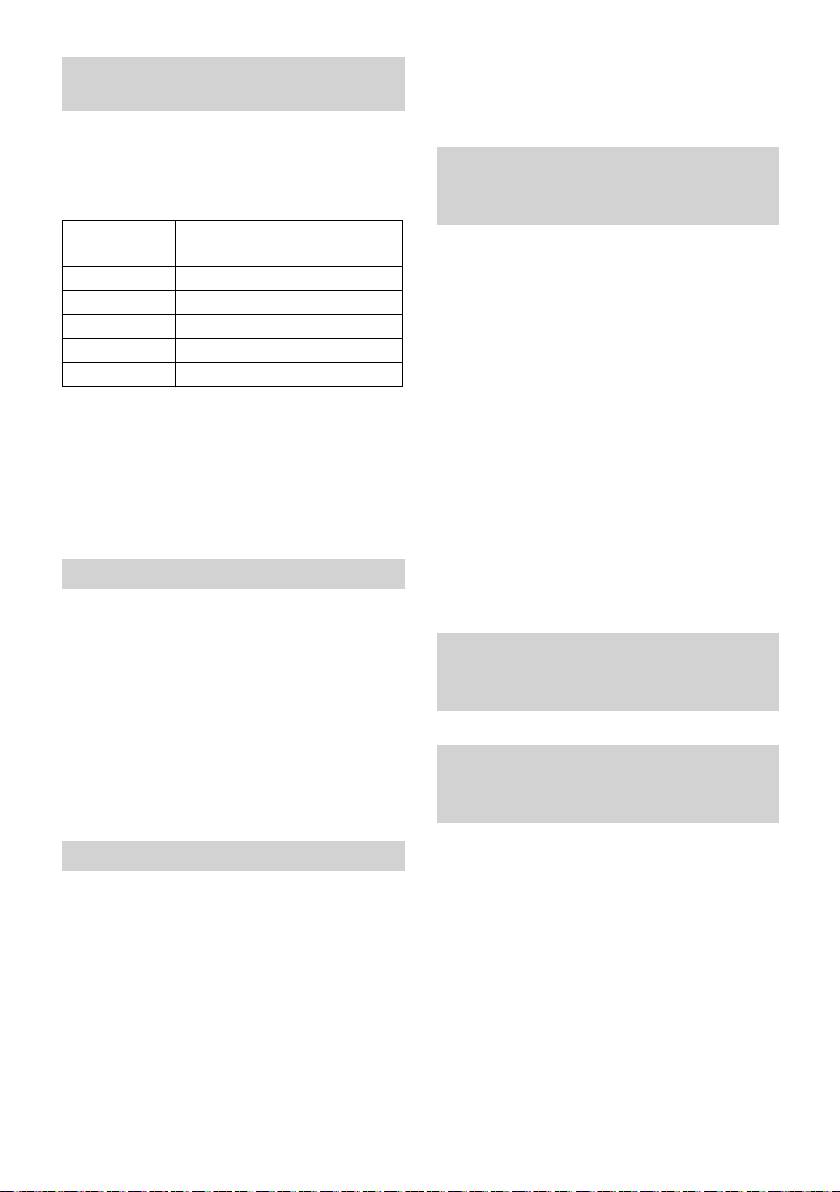
Kärcher offers an individual cleaning
Adjusting the dosage of the system
and care appliances program.
care Advance RM 110/RM 111
Your dealer will consult you gladly.
Determining the hardness of tap water:
Refill detergent.
– through the public water supply works,
Install the hand-spray gun, the jet
– using a hardness tester (order no.
pipe, the nozzle and the high
6.768-004)
pressure hose
Water hard-
Scale on the service switch
Figure 4
ness (°dH)
Connect ray tube with hand spray gun
<3 OFF (no dosing)
Tighten the screw connection of the
3...7 1
spray lance finger tight.
7...14 2
Insert high pressure nozzle into cover-
14...21 3
ing nut
>21 4
Install covering nut and tighten firmly
Set the service switch according to the
– Appliance without hose drum:
water hardness in the table.
Connect the high pressure hose to the
Note: Observe the following when using
high pressure connection point of the
system care Advance 2 RM 111:
machine.
– Calcification protection: See table
– Device with hose drum:
– Pump care and black water protection:
Connect the high pressure hose to the
Set the service switch to at least setting 3.
hand-spray gun.
Caution
Refill fuel
Always unwind high pressure hose com-
Danger
pletely
Risk of explosion! Only refill diesel oil or
Installing the replacement
light fuel oil. Unsuitable fuels, e.g. petrol,
high-pressure hose (appliances
are not to be used.
without hose drum)
Caution
Never operate device with empty fuel tank
Figure 5
The fuel pump will otherwise be destroyed.
Installing the replacement
Refill fuel.
high-pressure hose (appliances
Close tank lock.
with hose drum)
Wipe off spilled fuel.
Figure 6
Refill detergent
Completely roll off the high-pressure
hose from the hose drum.
Caution
Rotate the hose drum until the screwed-
Risk of injury!
on semi bowl is pointing toward the top.
– Use Kärcher products only.
Loosen all three screws and remove the
– Under no circumstances fill solvents
loosened semi bowl.
(petrol, aceton, diluting agent etc.)
Figure 7
– Avoid eye and skin contact.
Unlatch the fastening clamp for the
– Observe safety and handling instruc-
high-pressure hose and pull the hose
tions by the detergent manufacturer.
out.
– 5
27EN
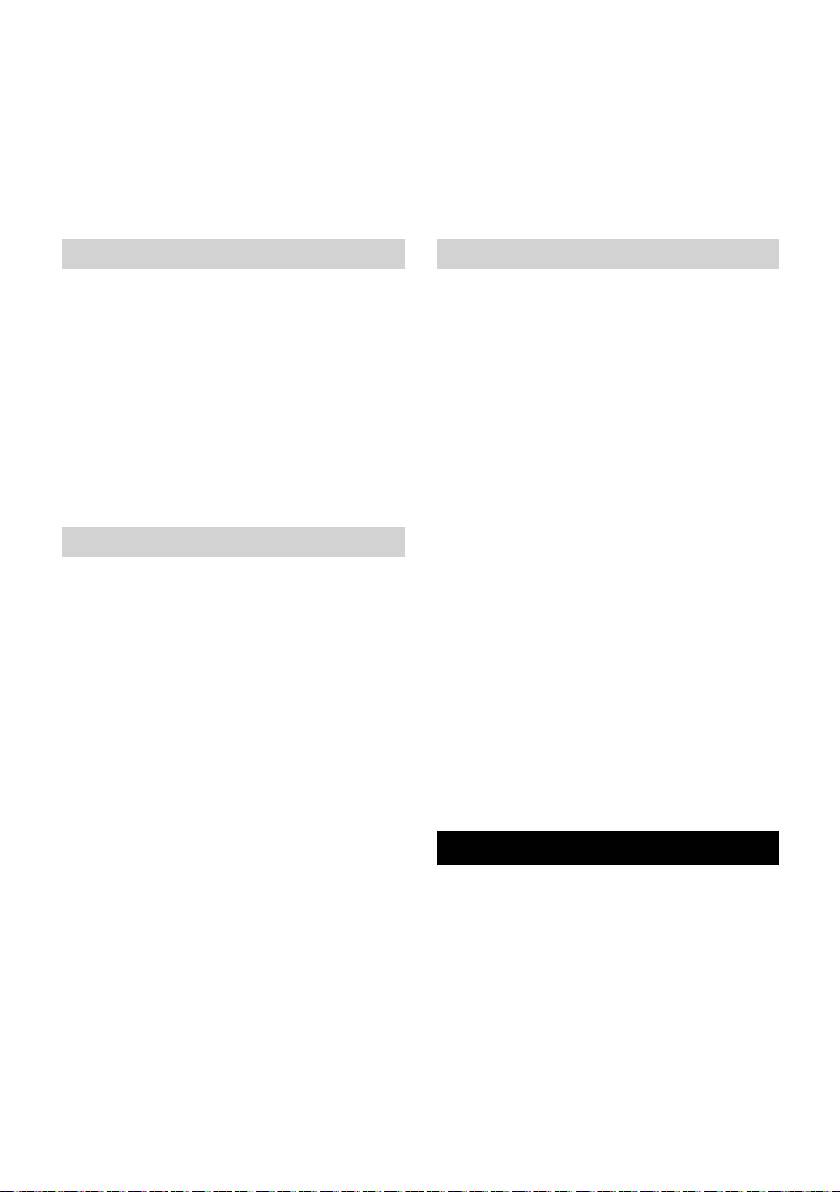
Route the new high-pressure hose
Danger
through the intended hose guide and
Never suck in water from a drinking water
the deflection pulley at the bottom of the
container. Never suck in liquids which con-
appliance.
tain solvents like lacquer thinner, petrol, oil
Slide the hose nipple all the way into the
or unfiltered water. The sealings within the
knot section of the hose drum and se-
device are not solvent resistant. The spray
cure with the fastening clamp.
mist of solvents is highly inflammable, ex-
Replace the half bowl.
plosive and poisonous.
Water connection
Power connection
For connection values refer to technical
– For connection values, see technical
specifications
data and type plate.
Attach supply hose (minimum length
– The electrical connections must be
7.5 m, minimum diameter 3/4“) to the
done by an electrician according to IEC
water supply set by means of a hose
60364-1.
clamp.
Danger
Connect the supply hose to the water
Danger of injury by electric shock.
connection point of the machine and at
– Unsuitable electrical extension cables
the water supply point (for e.g. a tap).
can be hazardous. Only use electrical
Note: The supply hose and the hose clamp
extension cables outdoors which have
are not included in the scope of delivery.
been approved and labelled for this pur-
Suck in water from vessel
pose and have an adequate cable
cross-section.
If you want to suck in water from an exter-
– Always unwind extension lines com-
nal vessel, the following modification is
pletely.
necessary:
– The plug and coupling of the extension
Figure 8
cable used must be watertight.
Remove water connection from the
Caution
pump head.
The highest allowed net impedance at the
Unscrew the upper supply hose to the
electrical connection point (refer to techni-
swimmer container at the fine filter and
cal data) is not to be exceeded. In case of
connect it to the pump head.
confusion regarding the power impedance
Replug the rinse line of the detergent
present on your connection, please contact
dosing valve.
your utilities provider.
Connect suction hose (minimum diame-
ter 3/4“) with filter (accessory) to the
Operation
water connection point.
Danger
– Max. suck height: 0.5 m
Risk of explosion!
Until the pump sucked in water, you should:
Do not spray flammable liquids.
Set the pressure/quantity regulation at
the pump unit to maximum quantity.
Danger
Close the dosing valve for the deter-
Risk of injury! Never use the appliance
gent.
without the spray lance attached. Check
and ensure proper fitting of the spray lance
prior to each use. The screw connection of
the spray lance must be fingertight.
28 EN
– 6
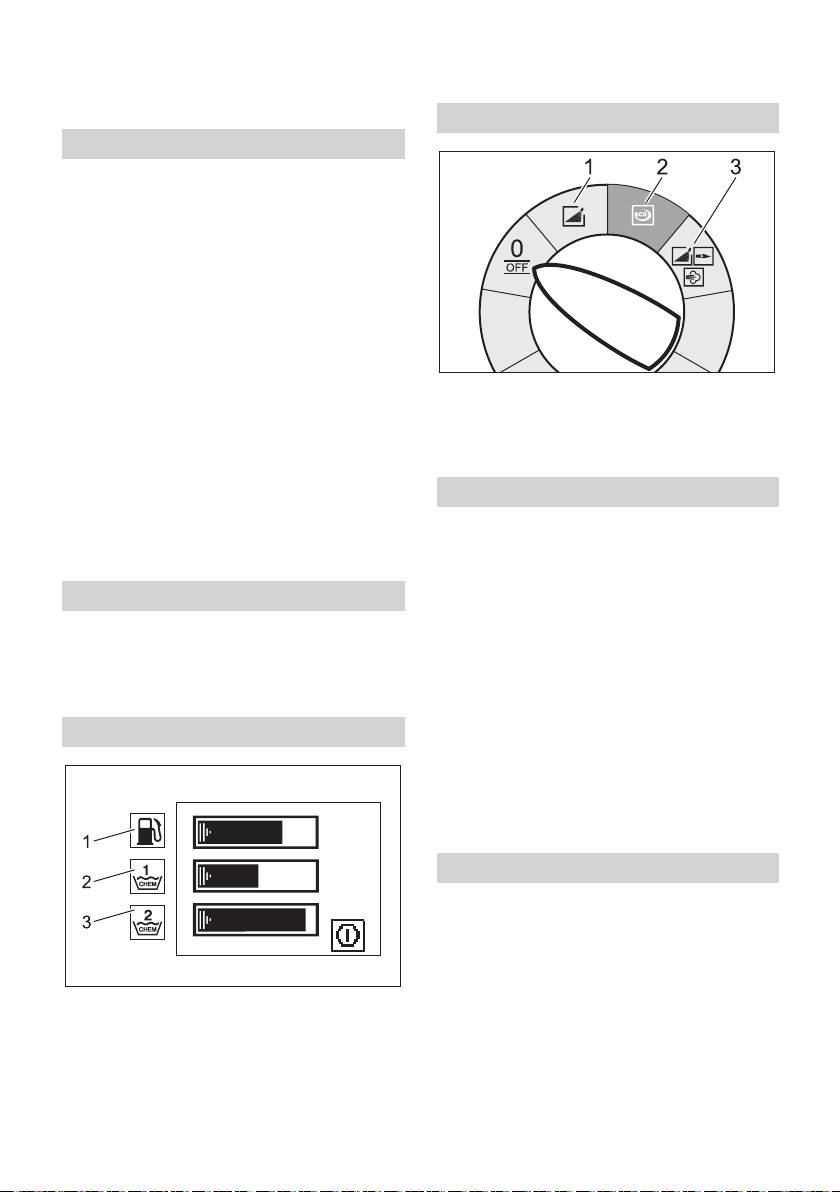
Caution
– The error symbols remain until the ap-
pliance is switched off.
Never operate device with empty fuel tank
The fuel pump will otherwise be destroyed.
Operating modes
Safety instructions
몇 Warning
Long hours of using the appliance can
cause circulation problems in the hands on
account of vibrations.
It is not possible to specify a generally valid
operation time, since this depends on sev-
eral factors:
– Proneness to blood circulation deficien-
cies (cold, numb fingers).
– Low ambient temperature. Wear warm
0/OFF =Off
gloves to protect hands.
1 Operating with cold water
– A firm grip impedes blood circulation.
2 Eco operation (hot water max. 60 °C)
– Continuous operation is worse than an
3 Operating with hot water/steam
operation interrupted by pauses.
Turning on the Appliance
In case of regular, long-term operation of
the device and in case of repeated occur-
Set appliance switch to desired operat-
rence of the symptoms (e.g. cold, numb fin-
ing mode.
gers) please consult a physician.
The device starts briefly and turns off, as
Replace the nozzle
soon as the working pressure is reached.
Note: If the error symbol appears on the
Danger
display during operation, immediately
Switch the appliance off prior to replacing
switch off the appliance and remove the er-
nozzle and activate hand spray gun until
ror; see "Help for errors".
device is pressureless.
Release the trigger gun.
When activating the hand spray gun the de-
Display
vice switches back on.
Note: If no water comes out of the high
pressure nozzle, vent pump. Refer to "Help
with malfunctions - appliance is not building
up pressure".
Adjust cleaning temperature
Set temperature regulator to desired
temperature.
30 °C to 98 °C
– Clean with hot water.
100 °C to 150 °C
1 Bar graph - fuel fill level
– Clean using steam.
2 Bar graph - detergent 1 fill level
3 Bar graph - detergent 2 fill level
– The operation and maintenance sym-
Follow the instructions given in the sec-
bols are displayed consecutively for 3
tion "Operation with steam"!
seconds each, just like in a slide show.
– 7
29EN
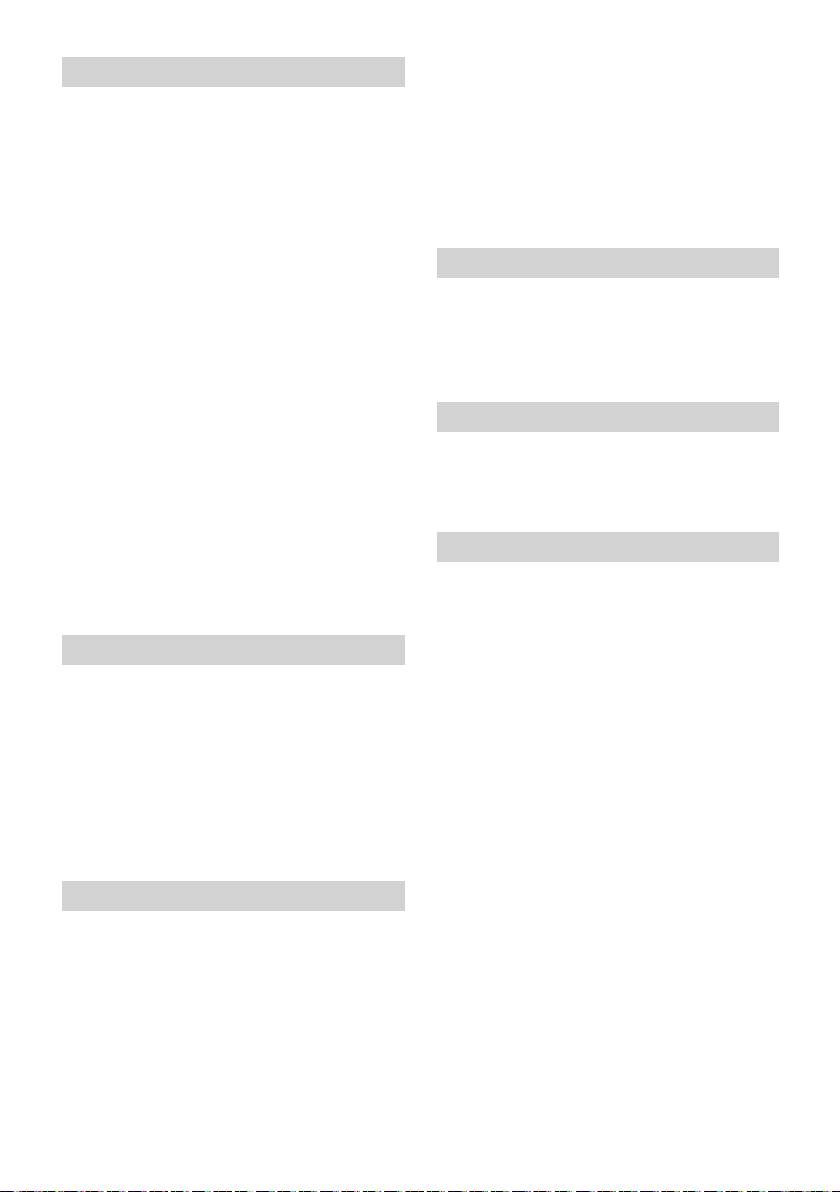
Set working pressure and flow rate
Recommended cleaning method
– Loosen the dirt:
Pressure/quantity regulation of the
Spray detergent economically and let it
pump unit
work for 1...5 minutes but do not let it
Turn the regulation spindle in a clock-
dry up.
wise direction: Increase working pres-
– Remove the dirt:
sure (MAX).
Spray off loosened dirt with the high
Turn the regulation spindle in an anti-
pressure jet.
clockwise direction: Reduce working
Operating with cold water
pressure (MIN).
Pressure/ quantity regulation at the
Removal of light contaminations and clear
hand spray gun
rinse, i.e.: Gardening tools, terrace, tools,
Set thermostat to max. 98 °C.
etc.
Set operating pressure according to
Set the operating pressure on the pump
need.
unit to the maximum value.
Set the working pressure and feed
Eco operation
quantity by turning (steplessly) the
The appliance works in the most economi-
pressure/quantity regulation mecha-
cal temperature range.
nism at the hand spray gun (+/-).
Note: The temperature can be regulated
Danger
up to 60 °C.
When adjusting the pressure/quantity regu-
Operating with hot water/steam
lation, make sure that the screw connection
of the spray lance does not become loose.
We recommend the following cleaning tem-
Note: For long term work with low pres-
peratures:
sure, set pressure at the pump unit.
– Light contaminations
Operation with detergent
30-50 °C
– Contaminations containing protein, i.e.
– For considerate treatment of the envi-
in the food processing industry
ronment use detergent economically.
max. 60 °C
– The detergent must be suitable for the
– Vehicle cleaning, machine cleaning
surface to be cleaned.
60-90 °C
With support of the detergent dose
– De-preserve, contaminations contain-
valve set detergent concentration as
ing strong fat contents
determined by the manufacturer.
100-110 °C
Note: Recommended values at the control
– De-frosting of surcharge substances,
panel at maximum working pressure.
partially facade cleaning
Cleaning
up to 140 °C
Set pressure/temperature and deter-
Operating with hot water
gent concentration according to the sur-
Danger
face to be cleaned.
Scalding danger!
Note: To prevent damage due to too much
Set temperature regulator to desired
pressure, always position high pressure ray
temperature.
first from a greater distance towards object
to be cleaned.
30 EN
– 8

Operating with steam
Storing the Appliance
Danger
Lock in the steel pipe into the holder of
Scalding danger! The operating pressure
the appliance hood.
must not exceed 3,2 MPa (32 bar) when
Roll up high pressure hose and electri-
operating with temperatures above 98 °C.
cal conduit and hang them into the re-
Therefore the following measures must
spective holders.
definitely be performed:
Device with hose drum:
Before rolling up, stretch out the high
Replace high pressure nozzle (stain-
pressure hose.
less steel) with steam nozzle (brass,
Turn the hand crank clockwise (Direc-
order see specification).
tion of the arrow).
Open up the pressure/ quantity regula-
Note: Do not twist high pressure hose and
tor on the hand spray gun completely,
electrical conduit.
direction + until stop.
Frost protection
Set the operating pressure on the pump
unit to the minimum value.
Caution
Set temperature regulator to min.
Frost will destroy the not completely water
100 °C.
drained device.
Store in a frost free area.
After operation with detergent
If the device is connected to a chimney, the
Set dosing value for detergent to "0".
following must be observed:
Set the appliance switch to "1" (opera-
Caution
tion with cold water).
Threat of damage by penetrating cold air
Open the hand spray gun and rinse the
through the chimney.
appliance for at least 1 minute.
Disconnect device from chimney when
Turn off the appliance
outside temperature drops below 0 °C.
If it is not possible to store frost free, shut
Danger
down device.
Danger of scalding by hot water. After the
Shutdown
operation with hot water or steam, the de-
vice must be operated with opened gun
For longer work breaks or if a frost free stor-
with cold water for at least two minutes.
age is not possible:
Shut off water supply.
Drain water.
Turn on pump shortly (appr. 5 seconds)
Flush device with anti-freeze agent.
by activating the hand spray gun.
Empty detergent tank.
Set the appliance switch to "0/OFF“.
Dump water
Pull main plug out of socket with dry
Screw off water supply hose and high
hands only.
pressure hose.
Remove water connection.
Screw off supply hose at boiler bottom
Activate hand spray gun until device is
and drain heating spiral empty.
pressure less.
Operate device for max. 2 minutes until
Lock the trigger gun.
the pump and lines are empty.
– 9
31EN

Flush device with anti-freeze agent
Maintenance intervals
Note: Observe handling instructions of the
anti-freeze agent manufacturer.
Weekly
Fill anti-freeze agent of the trade into
Clean the sieve in the water connection.
swimmer container.
Clean the fine filter.
Switch on appliance (without heater) till
Check oil level.
the appliance has been completely
Caution
rinsed.
In case of lacteous oil inform Kärcher cus-
A certain corrosion protection is achieved
tomer service immediately
with this as well.
Monthly
Storage
Clean sieve in the water shortage safe
guard.
Caution
Clean filter at the detergent suck hose.
Risk of injury and damage! Note the weight
After 500 operating hours, at least annu-
of the appliance in case of storage.
ally
Transport
Oil change.
Figure 9
At least every 5 years, recurring
Caution
Perform the pressure test as per manu-
facturer's instructions.
Risk of damage! When loading the appli-
ance with a forklift, observe the illustration.
Maintenance Works
Maintenance and care
Clean the sieve in the water connection
Take out sieve.
Danger
Clean sieve in water and reinstall.
Risk of injury by inadvertent startup of ap-
pliance and electrical shock.
Cleaning the fine filter
First pull out the plug from the mains before
Unpressurize the appliance.
carrying out any tasks on the machine.
Unscrew lid with filter.
Shut off water supply.
Clean the filter with clean water or com-
Turn on pump shortly (appr. 5 seconds)
pressed air.
by activating the hand spray gun.
Reinstall in reverse sequence.
Set the appliance switch to "0/OFF“.
Clean sieve in the water shortage safe
Pull main plug out of socket with dry
guard
hands only.
Unpressurize the appliance.
Remove water connection.
Loosen covering nut and take off hose.
Activate hand spray gun until device is
Take out sieve.
pressure less.
Note: If necessary turn in screw M8 appr.
Lock the trigger gun.
5 mm inwards and therewith pull out sieve.
Allow device to cool down.
Clean sieve in water.
Your Kärcher vender will inform you
Push sieve inwards.
about the performance of a periodic
Put on hose.
safety inspection resp. signing of a
Tighten covering nut firmly.
maintenance contract.
Clean filter at the detergent suck hose
Take out detergent suck supports.
Clean filter in water and reinstall.
32 EN
– 10
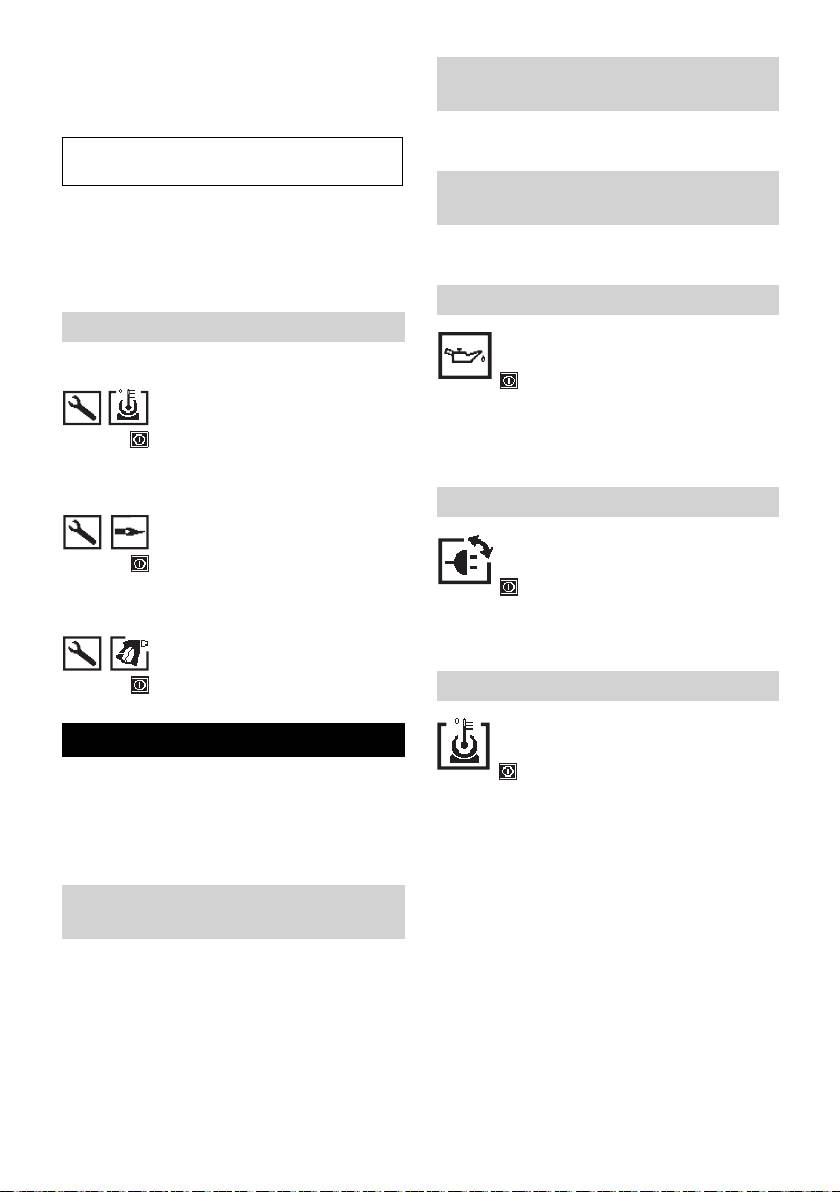
Oil change
Bar graph - detergent 1 fill level -
Ready a catch bin for appr 1 Litre oil.
switches off
Loosen release screw.
– Detergent tank 1 is empty.
Dispose of old oil ecologically or turn in at
Refill detergent.
a gathering point.
Bar graph - detergent 2 fill level -
Tighten release screw.
switches off
Fill oil slowly up to the MAX marking.
– Detergent tank 2 is empty.
Note: Air pockets must be able to leak out.
Refill detergent.
For oil type refer to technical specifica-
tions.
Pump symbol
Maintenance work using the display
Symbol pump maintenance
– Lack of oil
Replenish oil.
Note: In case of lack of oil, the appliance
Perform maintenance procedure.
will not switch off.
Symbol burner maintenance
Rotation direction symbol
Perform maintenance procedure.
Figure 10
Symbol accessory maintenance
Exchange the poles at the appliance
plug.
Engine symbol
Perform maintenance procedure.
Troubleshooting
Danger
– Engine overload/overheat
Risk of injury by inadvertent startup of ap-
Set the appliance switch to "0/OFF“.
pliance and electrical shock.
Allow device to cool down.
First pull out the plug from the mains before
Turn on the appliance.
carrying out any tasks on the machine.
– Error occurs repeatedly.
Bar graph - fuel fill level - switches
Inform Customer Service
off
– Fuel tank empty.
Refill fuel.
– 11
33EN
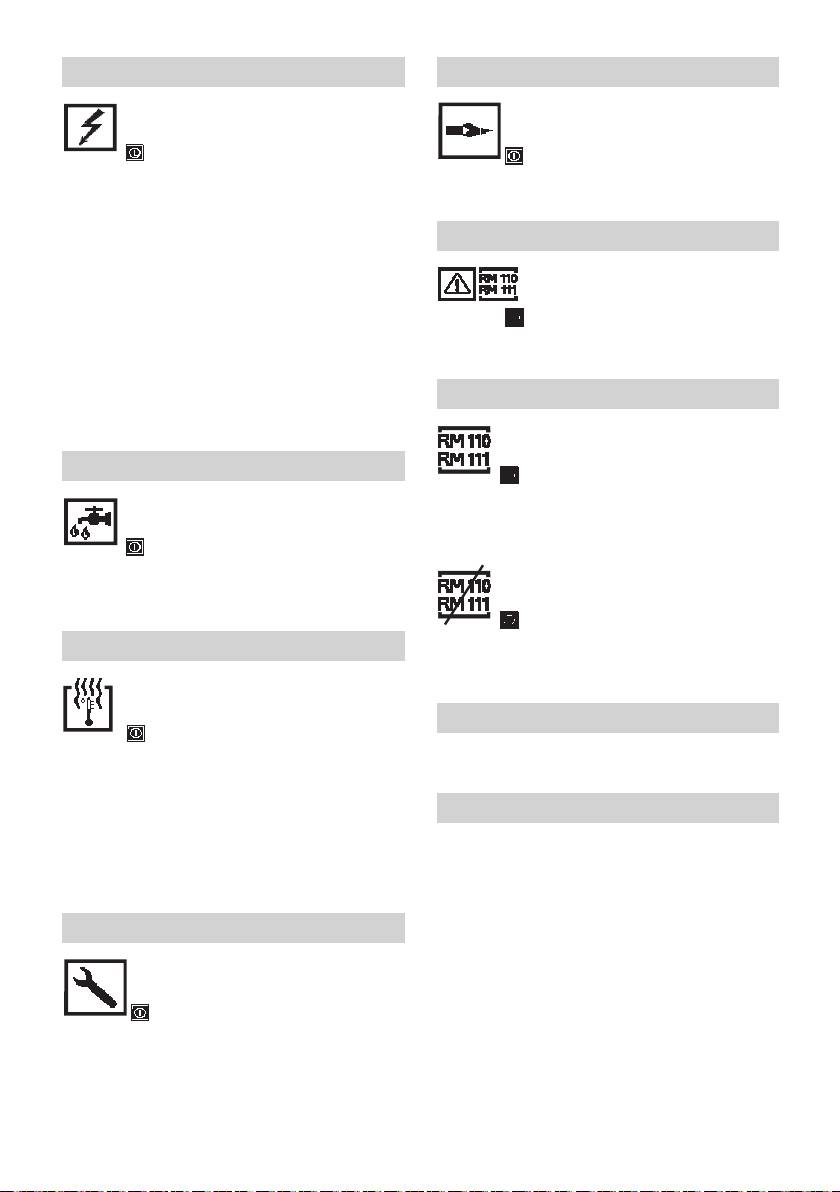
Electrical symbol
Flame sensor symbol
– Contactor error
– The flame sensor turned the burner off.
Set the appliance switch to "0/OFF“.
Inform Customer Service
Turn on the appliance.
System care detection symbol
– Error occurs repeatedly.
Inform Customer Service
– Fault in the voltage supply.
Check main connections and mains
fuse.
– System care detection defective
– Excessive power consumption.
Inform Customer Service
Check main connections and mains
System care symbol
fuse.
Inform Customer Service
Water shortage symbol
Note: Burner can operate 5 more hours.
– System care bottle empty.
Replace the system care bottle.
– Water shortage
Check water supply, check connec-
tions.
Note: Burner operation no longer possible.
Burner error symbol
– System care bottle empty.
Replace the system care bottle.
Appliance is not running
– The exhaust temperature limiter has
– No power
been triggered.
Check power connection/conduit.
Set the appliance switch to "0/OFF“.
Device is not building up pressure
Allow device to cool down.
– Air within the system
Turn on the appliance.
Vent pump:
– Error occurs repeatedly.
Set dosing value for detergent to "0".
Inform Customer Service
With open hand spray gun turn device
Error symbol
on and off multiple times with the device
switch.
Open and close the pressure/quantity
regulation at the pump unit with the
hand spray gun open.
– Leak in the high pressure system
Note: By dismantling the high pressure
Check high pressure system and con-
hose from the high pressure connection the
nections for tightness.
venting process is accelerated.
Inform Customer Service
34 EN
– 12
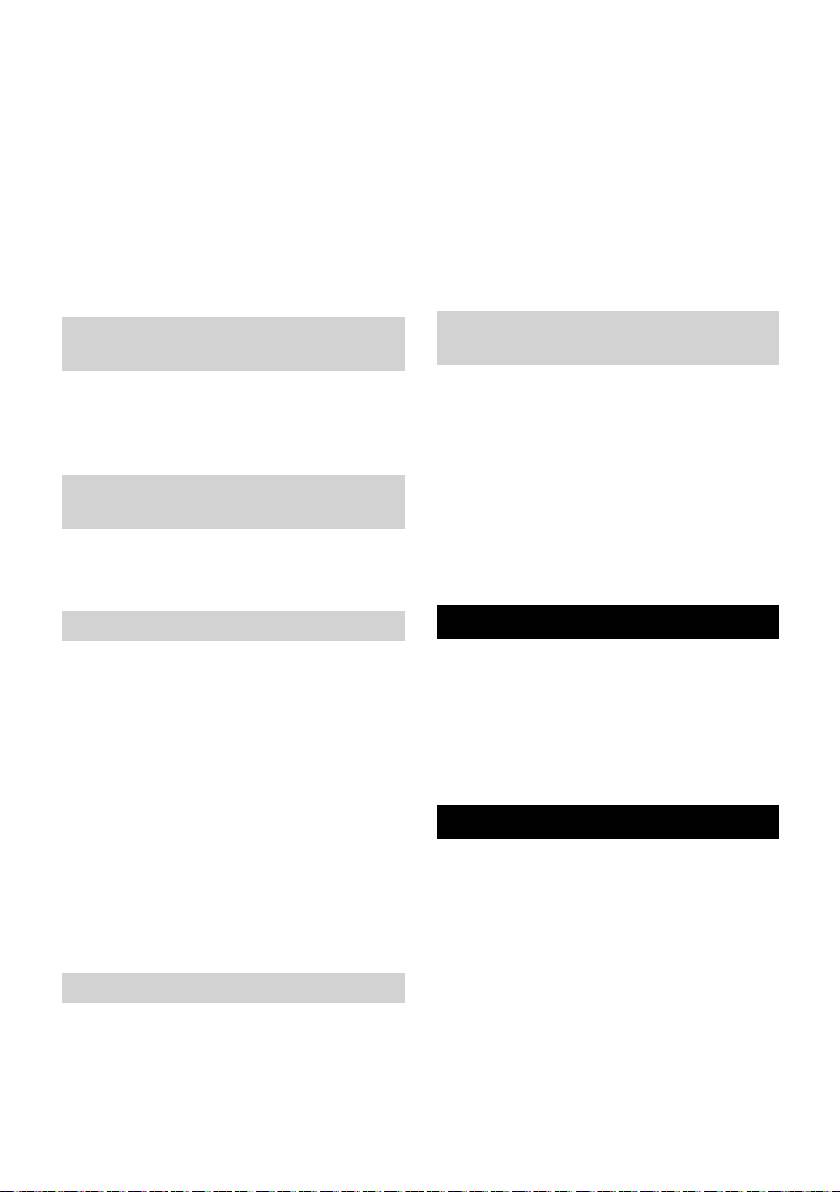
If detergent tank is empty, refill.
Check water supply, check connec-
Check connections and conduits.
tions.
– Pressure is set to MIN
Clean sieve in the water shortage safe
guard.
Set pressure to MAX.
– Fuel filter dirty
– Sieve in the water connection is dirty
Change fuel filter.
Clean sieve.
– No ignition spark
Clean the fine filter; replace it, if neces-
sary.
If device is in use and no ignition spark
can be seen through the viewing glass,
– Amount of water supply is too low.
have device checked by customer ser-
Check water supply level (refer to tech-
vice.
nical data).
Set temperature is not achieved
Device leaks, water drips from the
while using hot water
bottom of the device
– Working pressure/flow rate to high
– Pump leaky
Reduce working pressure/flow quantity
Note: 3 drops/minute are allowed.
at the pressure/volume regulator in the
With stronger leak, have device
pump unit.
checked by customer service.
– Sooty heating spiral
Device turns on and off while hand
Have device de-sooted by customer
spray gun is closed
service.
– Leak in the high pressure system
If malfunction can not be fixed, the de-
vice must be checked by customer ser-
Check high pressure system and con-
vice.
nections for tightness.
Device is not sucking in detergent
Warranty
Leave device running with open deter-
The warranty terms published by our com-
gent dosage valve and closed water
petent sales company are applicable in
supply, until the swimmer tank is
each country. We will repair potential fail-
sucked empty and the pressure falls to
ures of the appliance within the warranty
"0".
period free of charge, provided that such
failure is caused by faulty material or de-
Open the water supply again.
fects in fabrication.
If the pump still is not sucking in any deter-
gent, it could be because of the following
Accessories and Spare Parts
reasons:
– Only use accessories and spare parts
– Filter in the detergent suck hose dirty
which have been approved by the man-
Clean filter.
ufacturer. The exclusive use of original
– Backflow valve stuck
accessories and original spare parts
Remove the detergent hose and loosen
ensures that the appliance can be oper-
the backflow valve using a blunt object.
ated safely and trouble free.
Burner does not start
– At the end of the operating instructions
you will find a selected list of spare parts
– System care bottle empty.
that are often required.
Replace the system care bottle.
– For additional information about spare
– Fuel tank empty.
parts, please go to the Service section
Refill fuel.
at www.kaercher.com.
– Water shortage
– 13
35EN

Name of the appointed agency:
EC Declaration of Conformity
for 97/23/EG
TÜV Rheinland Industrie Service GmbH
We hereby declare that the machine de-
Am Grauen Stein
scribed below complies with the relevant
51105 Köln
basic safety and health requirements of the
ID No. 0035
EU Directives, both in its basic design and
construction as well as in the version put
Certificate no.:
into circulation by us. This declaration shall
01 202 111/Q-08 0003
cease to be valid if the machine is modified
without our prior approval.
Sound power level dB(A)
Measured: 89
Product: High pressure cleaner
Guaranteed: 91
Type: 1.071-xxx
5.957-902
Relevant EU Directives
97/23/EC
2006/42/EC (+2009/127/EC)
The undersigned act on behalf and under
2004/108/EC
the power of attorney of the company man-
1999/5/EC
agement.
2000/14/EC
Applied conformity evaluation method
for 2000/14/EG
Appendix V
CEO
Head of Approbation
Component category
II
Authorised Documentation Representative
Conformity procedure
S. Reiser
Module H
Heating coil
Alfred Kärcher GmbH Co. KG
Conformity assessment Module H
Alfred-Kärcher-Str. 28 - 40
Safety valve
71364 Winnenden (Germany)
Conformity assessment Art. 3 para 3
Phone: +49 7195 14-0
control block
Fax: +49 7195 14-2212
Conformity assessment Module H
various pipes
Conformity assessment Art. 3 para 3
Winnenden, 2013/05/01
Applied harmonized standards
EN 55014–1: 2006+A1: 2009+A2: 2011
EN 55014–2: 1997+A1: 2001+A2: 2008
EN 60335–1
EN 60335–2–79
EN 61000–3–2: 2006+A1: 2009+A2: 2009
EN 61000–3–11: 2000
EN 62233: 2008
EN 300 330-2 V1.5.1 : 2010
EN 301 489-1 V1.8.1 : 2008
EN 301 489-3 V1.4.1 : 2002
Applied specifications:
Based on AD 2000
Based on TRD 801
36 EN
– 14
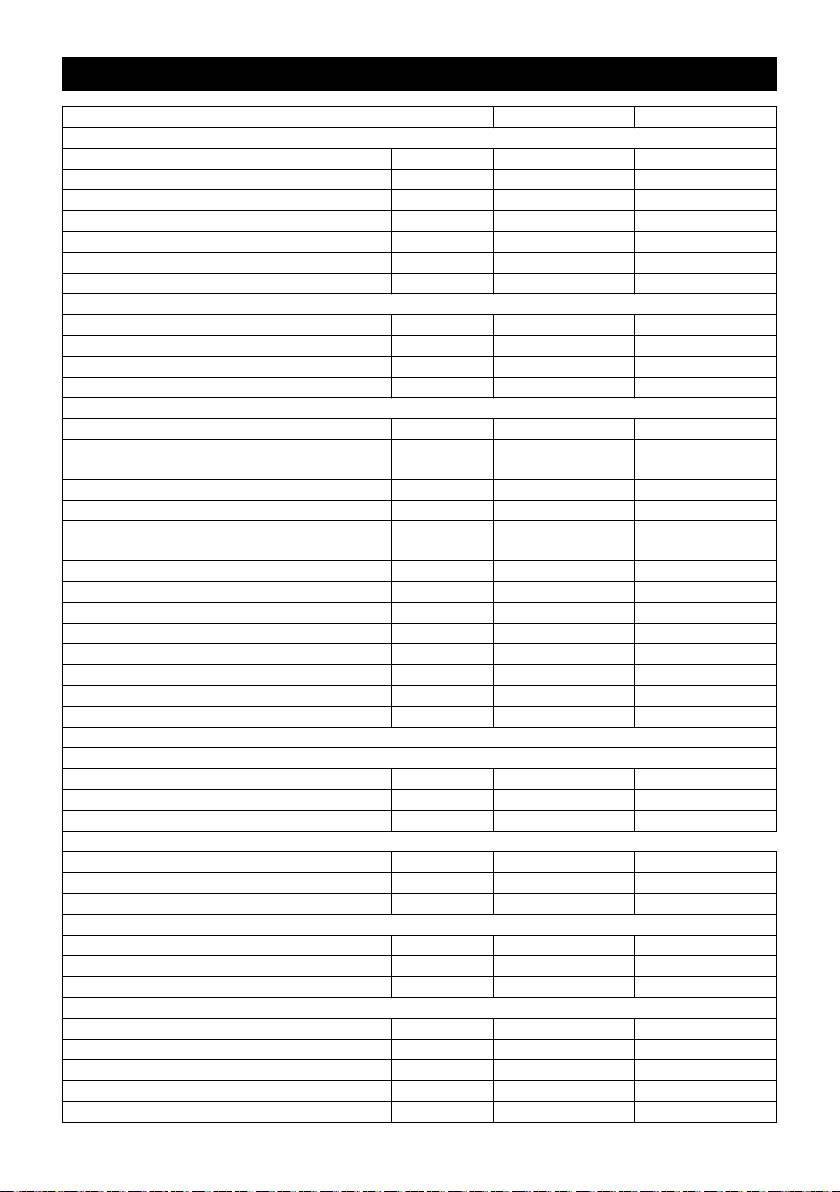
Technical specifications
HDS 13/20 HDS 13/20
Main Supply
Voltage V 230 400
Current type Hz 3~ 50 3~ 50
Connected load kW 9,3 9,3
Protection (slow) A 55 32
Type of protection -- IPX5 IPX5
Protective class -- I I
Maximum allowed net impedance Ohm (0.159+j0.100) (0.159+j0.100)
Water connection
Max. feed temperature °C 30 30
Min. feed volume l/h (l/min) 1500 (25) 1500 (25)
Suck height from open container (20 °C) m 0,5 0,5
Max. feed pressure MPa (bar) 0,6 (6) 0,6 (6)
Performance data
Water flow rate l/h (l/min) 600-1300 (10-21,6) 600-1300 (10-21,6)
Operating pressure of water
MPa (bar) 3-20 (30-200) 3-20 (30-200)
(using standard nozzle)
Max. excess operating pressure (safety valve) MPa (bar) 24 (240) 24 (240)
Steam flow rate l/h (l/min) 600-650 (10-10,8) 600-650 (10-10,8)
Max. operating pressure for working with steam
MPa (bar) 3,2 (32) 3,2 (32)
(using steam nozzle)
Part no. of steam nozzle -- 2.885-043.0 2.885-043.0
Max. operating temperature of hot water °C 98 98
Working temperature steam operation °C 155 155
Detergent suck in l/h (l/min) 0-78 (0-1,3) 0-78 (0-1,3)
Burner performance kW 108 108
Maximum consumption of heating oil kg/h 8,3 8,3
Max. recoil force of hand spray gun N 40,3 40,3
Nozzle size (SX) -- 070 (072) 070 (072)
Values determined as per EN 60355-2-79
Noise emission
Sound pressure level L
pA
dB(A) 74 74
Uncertainty K
pA
dB(A) 2 2
Sound power level L
WA
+ Uncertainty K
WA
dB(A) 91 91
Hand-arm vibration value
2
Hand spray gun m/s
1,66 1,66
2
Spray lance m/s
5,85 5,85
2
Uncertainty K m/s
1,0 1,0
Fuel
Fuel -- Fuel oil EL or Diesel Fuel oil EL or Diesel
Amount of oil l 1,0 1,0
Oil grade -- SAE 90 SAE 90
Dimensions and weights
Length x width x height mm 1330 x 750 x 1060 1330 x 750 x 1060
Typical operating weight, S kg 200 200
Typical operating weight, SX kg 205 205
Fuel tank l 25 25
Detergent Tank l 10+20 10+20
– 15
37EN
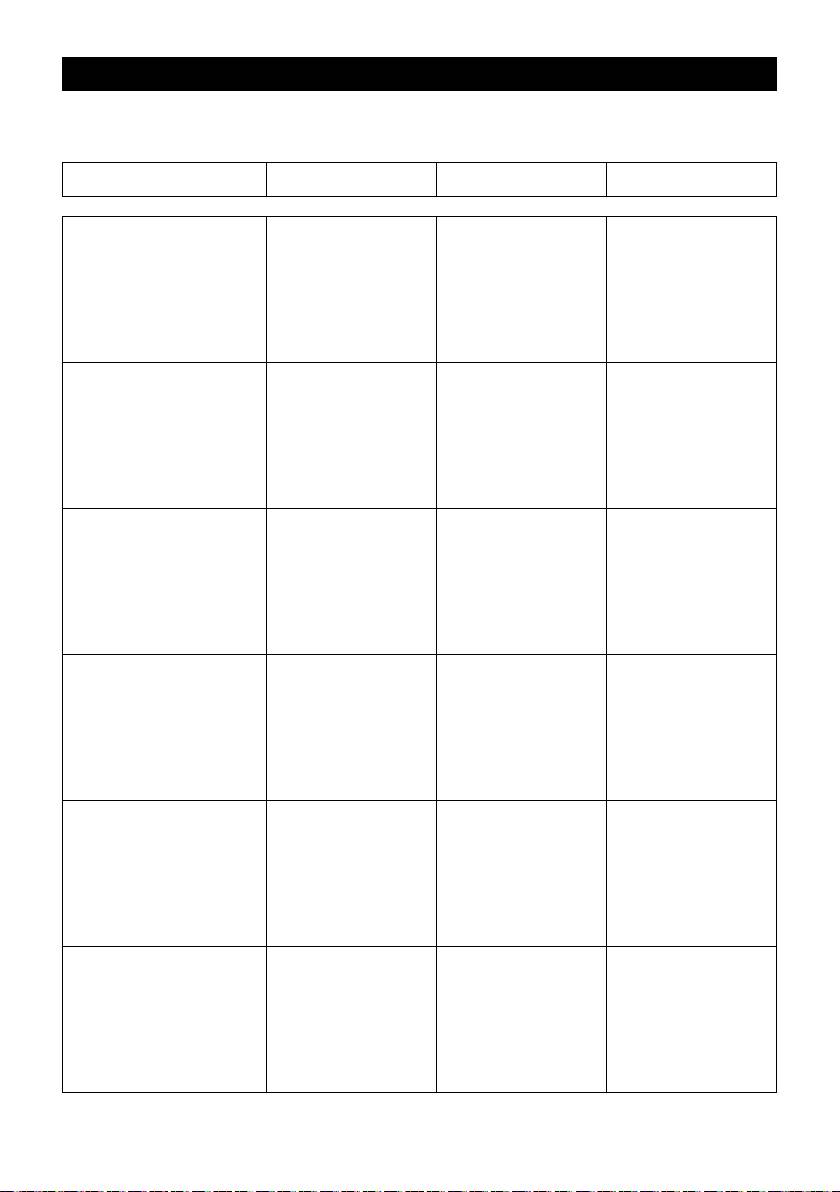
Recurring tests
Note: The recommended testing frequencies of the respective statutory regulations of the
country of operation are to be followed.
Testing done by: External testing Internal testing Leak-proof tests
Name Signature of the
Signature of the
Signature of the
authorised person/
authorised person/
authorised person/
date
date
date
Name Signature of the
Signature of the
Signature of the
authorised person/
authorised person/
authorised person/
date
date
date
Name Signature of the
Signature of the
Signature of the
authorised person/
authorised person/
authorised person/
date
date
date
Name Signature of the
Signature of the
Signature of the
authorised person/
authorised person/
authorised person/
date
date
date
Name Signature of the
Signature of the
Signature of the
authorised person/
authorised person/
authorised person/
date
date
date
Name Signature of the
Signature of the
Signature of the
authorised person/
authorised person/
authorised person/
date
date
date
38 EN
– 16
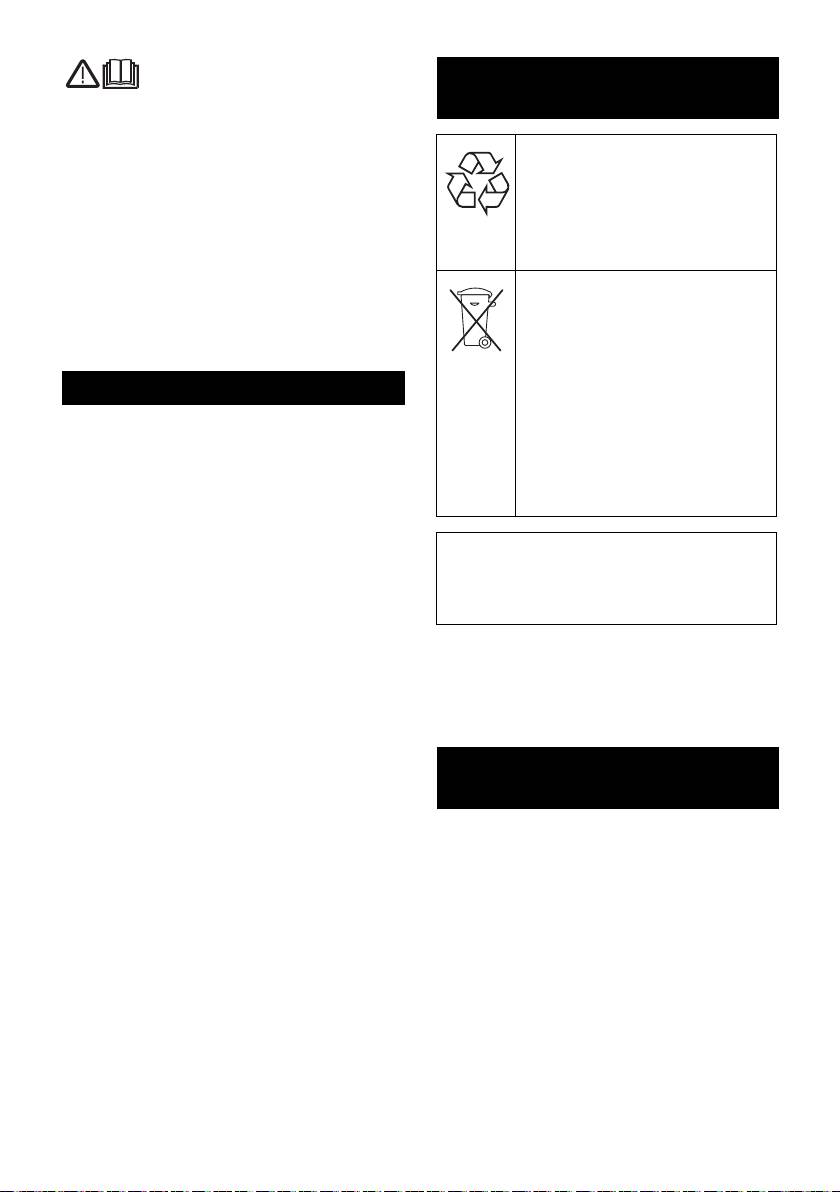
Lire ces notice originale avant la
Protection de
première utilisation de votre ap-
l’environnement
pareil, se comporter selon ce qu'elles re-
quièrent et les conserver pour une
Les matériaux constitutifs de
utilisation ultérieure ou pour le propriétaire
l’emballage sont recyclables.
futur.
Ne pas jeter les emballages
– Avant la première mise en service, vous
dans les ordures ménagères,
devez impérativement avoir lu les
mais les remettre à un système
consignes de sécurité N° 5.951-949.0 !
de recyclage.
– Contactez immédiatement le revendeur
en cas d'avarie de transport.
Les appareils usés contiennent
des matériaux précieux recy-
– Vérifier le contenu de l'emballage à l'ou-
clables lesquels doivent être ap-
verture. Étendue de livraison cf. figure
portés à un système de
1.
recyclage. Il est interdit de jeter
Table des matières
les batteries, l'huile et les subs-
tances similaires dans l'environ-
Protection de l’environnement FR . . .1
nement. Pour cette raison,
Symboles utilisés dans le mode
utiliser des systèmes de collecte
d'emploi . . . . . . . . . . . . . . . FR . . .1
adéquats afin d'éliminer les ap-
Aperçu général. . . . . . . . . . FR . . .2
pareils hors d'usage.
Symboles sur l'appareil . . . FR . . .3
Utilisation conforme . . . . . . FR . . .3
Ne jetez pas l'huile moteur, le fuel, le die-
Consignes de sécurité . . . . FR . . .3
sel ou l'essence dans la nature. Protéger
le sol et évacuer l'huile usée de façon fa-
Dispositifs de sécurité . . . . FR . . .3
vorable à l'environnement.
Mise en service . . . . . . . . . FR . . .4
Utilisation . . . . . . . . . . . . . . FR . . .7
Instructions relatives aux ingrédients
Entreposage. . . . . . . . . . . . FR . . 11
(REACH)
Transport . . . . . . . . . . . . . . FR . . 11
Les informations actuelles relatives aux in-
grédients se trouvent sous :
Entretien et maintenance . . FR . .11
www.kaercher.com/REACH
Assistance en cas de panne FR . .12
Garantie . . . . . . . . . . . . . . . FR . .15
Symboles utilisés dans le
Accessoires et pièces de re-
mode d'emploi
change . . . . . . . . . . . . . . . . FR . .15
Déclaration de conformité CE FR . .16
Danger
Caractéristiques techniques FR . .17
Pour un danger immédiat qui peut avoir
Essais périodiques . . . . . . . FR . .18
pour conséquence la mort ou des bles-
sures corporelles graves.
몇 Avertissement
Pour une situation potentiellement dange-
reuse qui peut avoir pour conséquence des
blessures corporelles graves ou la mort.
Attention
Pour une situation potentiellement dange-
reuse qui peut avoir pour conséquence des
blessures légères ou des dommages maté-
riels.
– 1
39FR
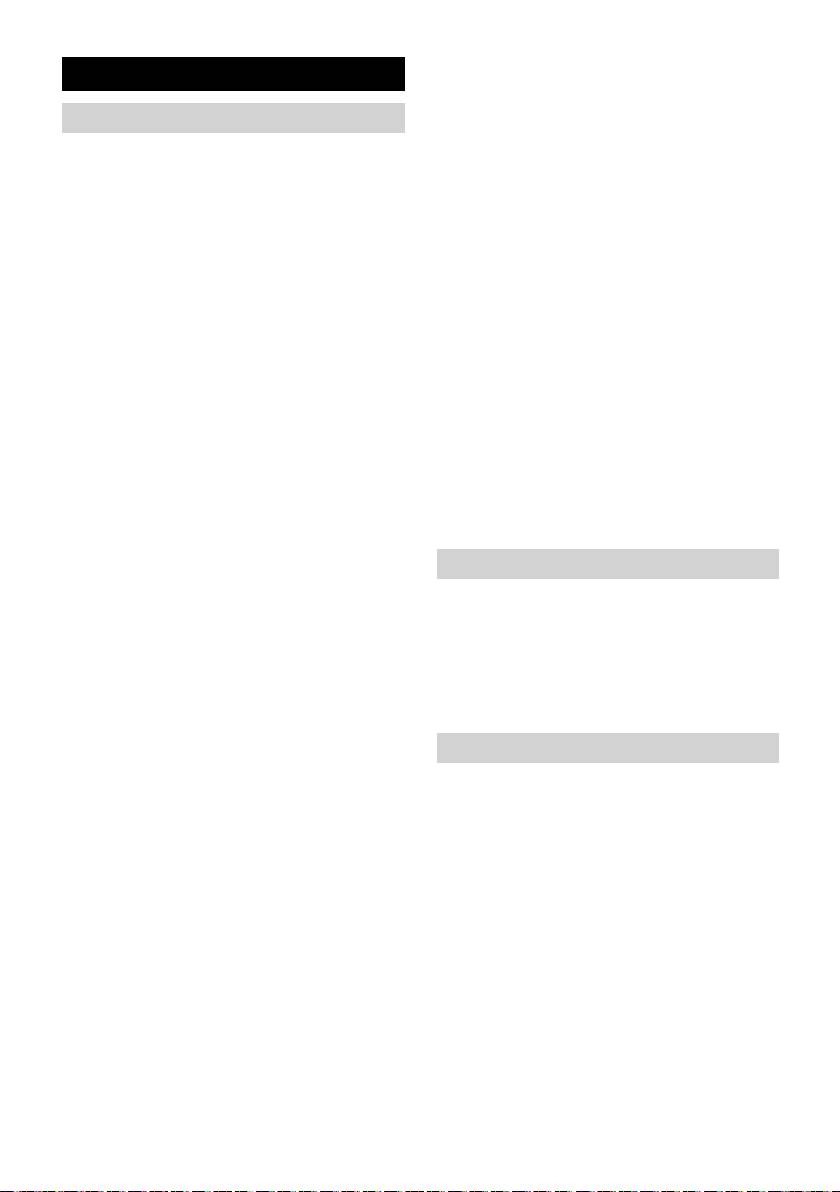
29 Capot du compartiment de rangement
Aperçu général
30 Compartiment de rangement pour ac-
cessoires
Éléments de l'appareil
31 Plaque signalétique
Figure 1
32 Fermeture du capot
1 Capot
33 Réservoir d'huile
2 Dispositif de fixation de la lance
34 Réglage de la pression/ du débit de
(bilatéral)
l'unité de pompe
3 Entretien système Advance RM 110/
35 Bouchon de vidange d'huile
RM 111
36 Soupape anti-retour de l'aspiration de
4 Roulettes pivotantes et frein de station-
détergent
nement
37 Flexible d'aspiration du détergent 1
5 Point de fixation pour le transport
avec filtre
(bilatéral)
38 Flexible d'aspiration du détergent 2
6 Roue
avec filtre
7 Kit de raccord d'alimentation en eau
39 Filtre de combustible
8 Raccord haute pression
40 Commutateur de service
(uniquement S)
41 Protection contre le manque d'eau avec
9 Kit joint torique (pour le remplacement)
tamis
10 Flexible haute pression
42 Réservoir flottant
11 Poignée-pistolet
43 Filtre fin (eau)
12 Lance
Zone de commande
13 Buse haute pression (acier inoxydable)
Figure 2
14 Buse de vapeur (laiton)
A Interrupteur principal
15 Réglage de la pression/ du débit à la
B Thermostat
poignée-pistolet.
C Vanne de dosage du détergent
16 Cran de sécurité de la poignée-pistolet
D Manomètre
17 Alimentation électrique
E Ecran
18 Compartiment pliant
(uniquement S)
Repérage de couleur
19 Arrivée d'eau avec tamis
– Les éléments de commande pour le
20 Ouverture de sortie du flexible haute
processus de nettoyage sont jaunes.
pression
– Les éléments de commande pour la
(uniquement SX)
maintenance et l'entretien sont en gris
21 Cavité de marche
clair.
22 Orifice de remplissage pour détergent 2
23 Manivelle pour dévidoir
(uniquement SX)
24 Orifice de remplissage pour détergent 1
25 Dévidoir
(uniquement SX)
26 Orifice de remplissage pour combus-
tible
27 Poignée
28 Pupitre de commande
40 FR
– 2