Rothenberger ROWELD P 160 SANILINE: ENGLISH 15
ENGLISH 15 : Rothenberger ROWELD P 160 SANILINE
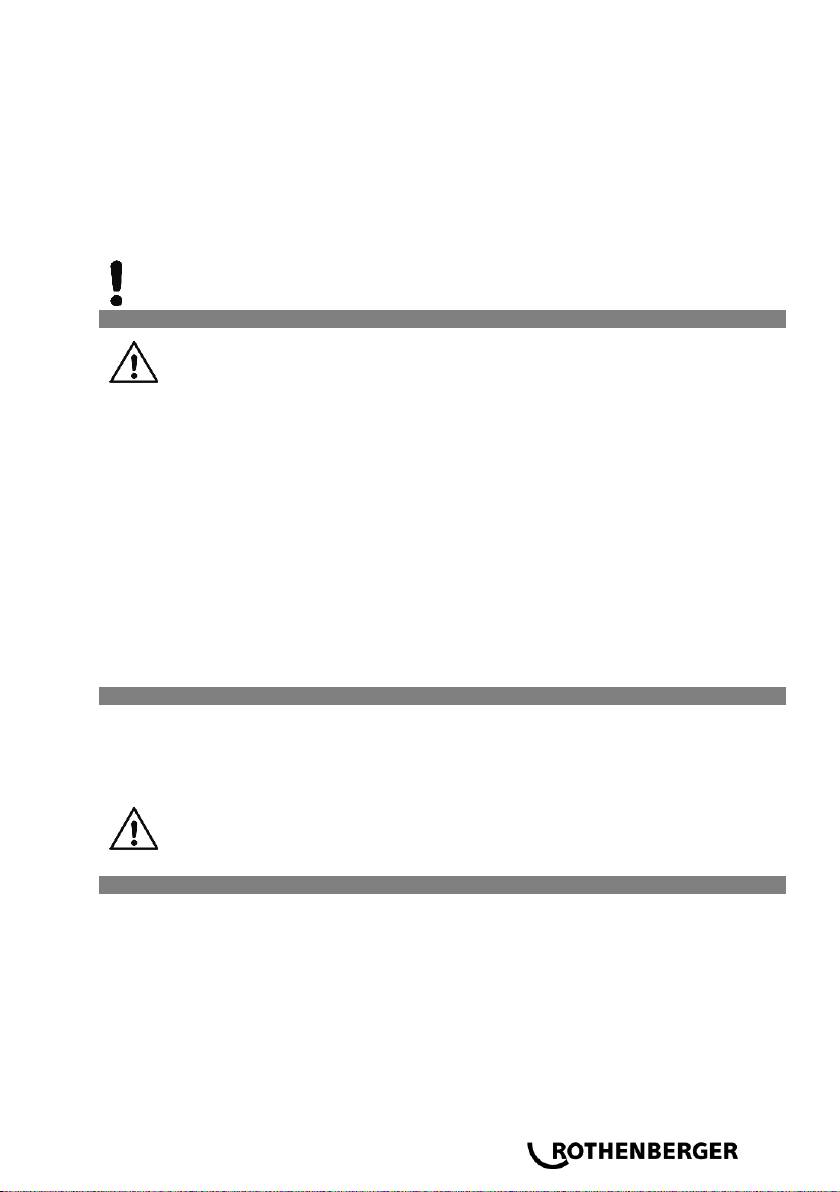
For one-sided milling, turn the stop on the underside of the milling machine to the side that is
NOT to be worked on.
After the front sides are trimmed flat, which can be recognized by a uniform and unbroken
chip, slowly move the pipes ends apart. Unlock the trimmer (1) by pulling out the ring (7) and
swivel it.
Move workpieces together and check whether the welded surfaces are flat. If this is not the
case, trimming must be repeated.
The axial offset between the workpieces must not be greater than 10% of the wall thickness and
the gap between the flat surfaces must not be greater than 0.5 mm (according to DVS). If this is
not the case, adjust with the help of the clamping screws and pipe supports and repeat trimming.
ENGLISH 15
The trimmed surfaces prepared for welding must not be touched with the hands
and must be kept free of dirt!
3.2.3 Welding
Risk of crushing! Always maintain a safe distance from the machine when
moving clamping tools and pipes together! Never reach into the working area!
Swivel the heating element (2) between the two workpieces.
Bring the pipe ends together, put force to the grip bar (6) and stop the driveshaft by pulling
the clamping lever (5).
As soon as the required bead height is reached evenly over the entire circumference at the
pipe ends, disengage the clamping lever (5), reduce the force to the corresponding preheat-
ing force (near 0) and screw up the clamping lever (5) tightly again. It must be ensured that
the workpiece ends abut evenly to the heating plate.
After the preheating time is over, disengage clamping lever (5) move workpieces apart,
swivel out the heating element (2) and move the workpiece ends together again. While do-
ing this, increase the corresponding joining force as linearly as possible until the nominal
force is reached (see the accompanying book for welding parameters) and pull the clamping
lever (5). The joining force must be maintained during the entire cooling period.
At the end of the cooling period, disengage the clamping lever (5) and release the spring via
the grip bar. Unclamp and take out the welded tube sections.
All welding parameters can be found in the enclosed welding tables.
3.2.4 Putting out of operation
Unplug the trimmer and heating element.
Swivel trimmer into the space between the main clamps.
Wind up flex.
Insert the heating element into the mounting provided in the underframe.
The hotplate must be cooled off!
Pull the knob (11) and swing the machine downward until the locking bolts have clicked in.
3.3 General requirements
As weather and ambient conditions can seriously effect welding procedures and joints, it is es-
sential to duly observe national welding guidelines and ordinances, e. g. DVS Guideline 2207,
Sections 1, 11 and 15.
Welding requires continuous and due supervision and monitoring!

3.4 Important information on welding parameters
For welding parameters such as temperature, pressure and time, consult your national welding
guidelines and ordinances, e. g. DVS Guideline 2207, Sections 1, 11 and 15.
Ordering: DVS Media GmbH, Aachener Str. 172, 40223 Düsseldorf
Postfach 10 19 65, 40010 Düsseldorf, Tel.: +49 (0) 211 / 15 91 – 0
Email: media@dvs-hg.de internet: www.dvs-media.info
In the event of doubt, consult the pipe manufacturer for material-specific welding parameters.
The welding parameters specified in the welding tables are strictly reference values. ROTHEN-
BERGER cannot assume any liability for their accuracy or completeness!
4 Care and maintenance
To ensure that the welding machine functions properly, observe the following maintenance rec-
ommendations:
Keep the guide rods for the skids or for the heating element holder and milling unit free of
dirt.
The electric drives of the trimmer and heating element must be operated only with the volt-
age stated on the type plate.
To achieve perfect welding results, it is essential to keep the heating plate clean. If the sur-
face is damaged or shows signs of erosion, the surface must be recoated or replaced. Mate-
rial residues on the heating plate surface reduces the non-sticking properties of the coating.
Remove all residues with non-linting paper and alcohol (heating plate must be cool!).
The trimmer is equipped with two double-sided ground knives. When cutting capacity starts
decreasing, the knives can be turned over or replaced by new ones.
It must always be ensured that the pipe or workpiece ends to be machined, especially the
face surfaces, are free of soiling because otherwise the service life of the knives will be
shortened.
16 ENGLISH
It is recommendable to have repairs done only by a service workshop or by
the manufacturer!
4.1 Machine and tool care
(Follow the maintenance instructions in item 4!)
Sharp and clean tools produce better work results and are safer.
Replace blunt, broken or lost parts immediately. Check whether the accessories are securely
connected to the machine.
Use only original spare parts from the manufacturer for maintenance work. Repairs must be car-
ried out only by professionally qualified personnel.
Disconnect the machine from the mains when it is not in use, prior to care and maintenance
work and before changing accessory parts.
Prior to reconnection to the mains, it must be ensured that the machine and the accessory tools
are switched off.
When extension cables are used, they must be checked for their safety and operativeness. Only
cables approved for outdoor use must be used.
Tools and machines whose housing or handles, especially those made of plastic, are cracked or
warped must not be used.
Dirt and moisture in such cracks conduct electric current. This can lead to an electric shock if the
insulation is damaged in the tools or in the machine.
Note: Furthermore, we refer to the accident prevention regulations.
Оглавление
- DEUTSCH 3
- DEUTSCH 5
- DEUTSCH 7
- DEUTSCH 9
- ENGLISH 11
- ENGLISH 13
- ENGLISH 15
- ENGLISH 17
- FRANÇAIS 19
- FRANÇAIS 21
- FRANÇAIS 23
- FRANÇAIS 25
- ESPAÑOL 27
- ESPAÑOL 29
- ESPAÑOL 31
- ESPAÑOL 33
- ITALIANO 35
- ITALIANO 37
- ITALIANO 39
- ITALIANO 41
- NEDERLANDS 43
- NEDERLANDS 45
- NEDERLANDS 47
- NEDERLANDS 49
- PORTUGUES 51
- PORTUGUES 53
- PORTUGUES 55
- PORTUGUES 57
- DANSK 59
- DANSK 61
- DANSK 63
- DANSK 65
- SVENSKA 67
- SVENSKA 69
- SVENSKA 71
- SVENSKA 73
- NORSK 75
- NORSK 77
- NORSK 79
- NORSK 81
- SUOMI 83
- SUOMI 85
- SUOMI 87
- SUOMI 89
- POLSKI 91
- POLSKI 93
- POLSKI 95
- POLSKI 97
- ČESKY 99
- ČESKY 101
- ČESKY 103
- ČESKY 105
- MAGYAR 107
- MAGYAR 109
- MAGYAR 111
- MAGYAR 113
- PУCCKИЙ 115
- PУCCKИЙ 117
- PУCCKИЙ 119
- PУCCKИЙ 121
- ROTHENBERGER Worldwide