Rothenberger ROWELD P 160 SANILINE: ENGLISH 13
ENGLISH 13 : Rothenberger ROWELD P 160 SANILINE
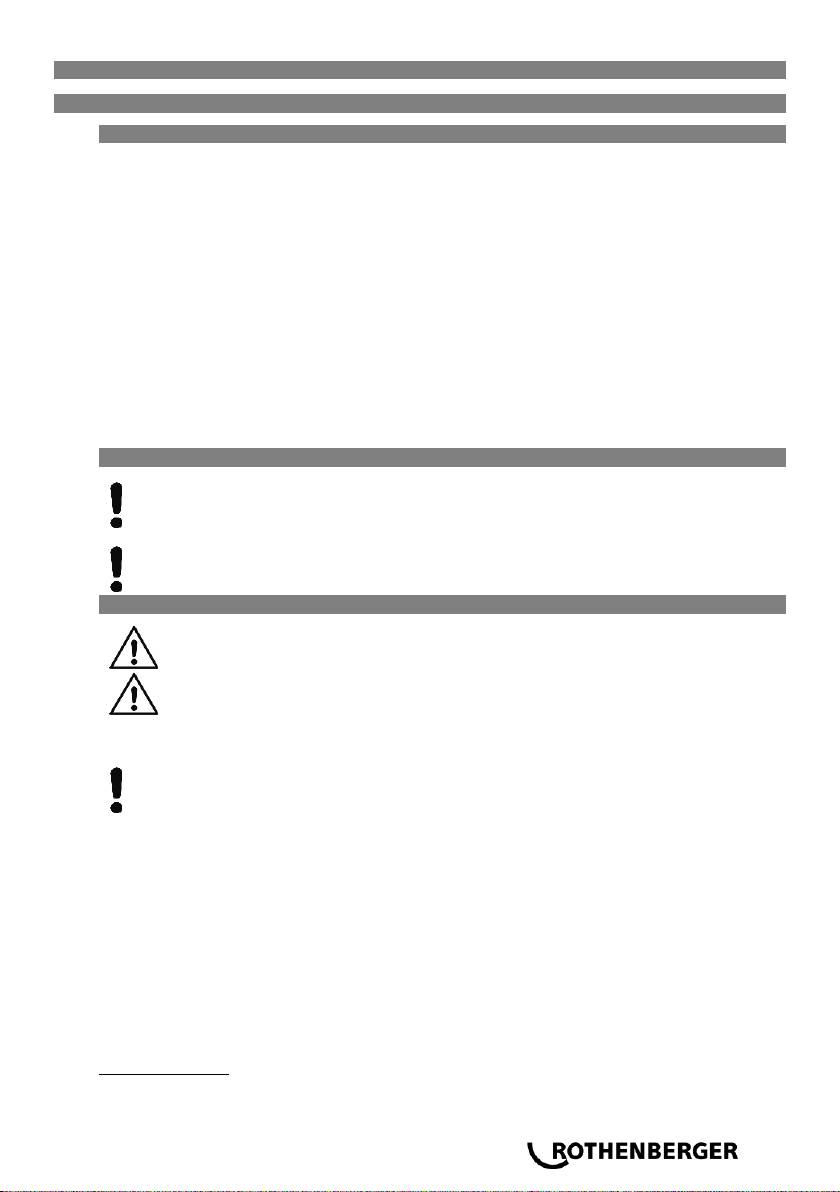
2 Technical Data, see „technical data“ book
3 Function of the Unit
3.1 Overview (ill. A)
1 Trimmer unit 8 Main clamp Version A
2 Heating element 8.1 Adjusting nut
3 Machine housing 8.2 Tensioning screw
4 Movable table 9 Main clamp Version B
5 Clamping lever 9.1 Clamping insert, bracket
6 Grip bar 10 Support brackets
7 Safety catch 11 Knob
Welded joints for house installations, chimney renovations and roof drainage systems made of
PE, PVDF and PP pipes with outer diameters of 40 - 160mm/ 1“- 5“ can be safely produced with
the machine.
Depending on the version (Version A = clamping plates, knee lever version, Version B =
clamping plates, screw version), clamping elements can be used instead of the support forks for
the exterior clamping positions. Threads are provided for this purpose in the machine base and
in the movable table.
3.2 Operating instructions
ENGLISH 13
In accordance with national or EU ordinances and guidelines, e. g. DVS 2212,
Section I, only duly qualified and authorised personnel are allowed to operate the
ROWELD welding machines!
Only trained and authorised welders are allowed to operate the machine!
3.2.1 Putting into operation
Please read through the operating instructions and safety instructions atten-
tively before you put the butt fusion welding machine into operation!
Do not use the heating element in explosive environments or bring it into
contact with easily flammable materials!
Put the machine on a level, solid surface.
Pull the knob (11), swing the machine upward, and allow the locking bolts to click in.
Make sure that both bolts are engaged in the holes in the frame!
Pull the trimmer lock (7) to the front and swivel the trimmer (1) to the back.
Swivel heating element (2) to the back.
Connect power plug of trimmer unit (1) and heating element (2) to the power supply stated
on the type plate.
The red diode “Stand by“ lights up. That is: there is a voltage being applied. Switch on the heater
element using the large pushbutton (lights up green) and select the desired temperature (160°C
to 285°C) using the “+“ or “-“ button.
Heating up of the heater element is displayed by a yellow diode on the heater element. A hori-
zontal bar also appears on the temperature indicator. The yellow diode goes out shortly before
reaching the set temperature (tolerance +/-3°C) and the green one lights up. After a further 10
minutes the heating element is ready to use. Check the temperature using a temperature meas-
uring instrument.
Setting the off-set: press the “+“ and “-“ button at the same time. The heater element can subse-
quently be calibrated using one of these buttons and an external temperature measuring instru-
ment.
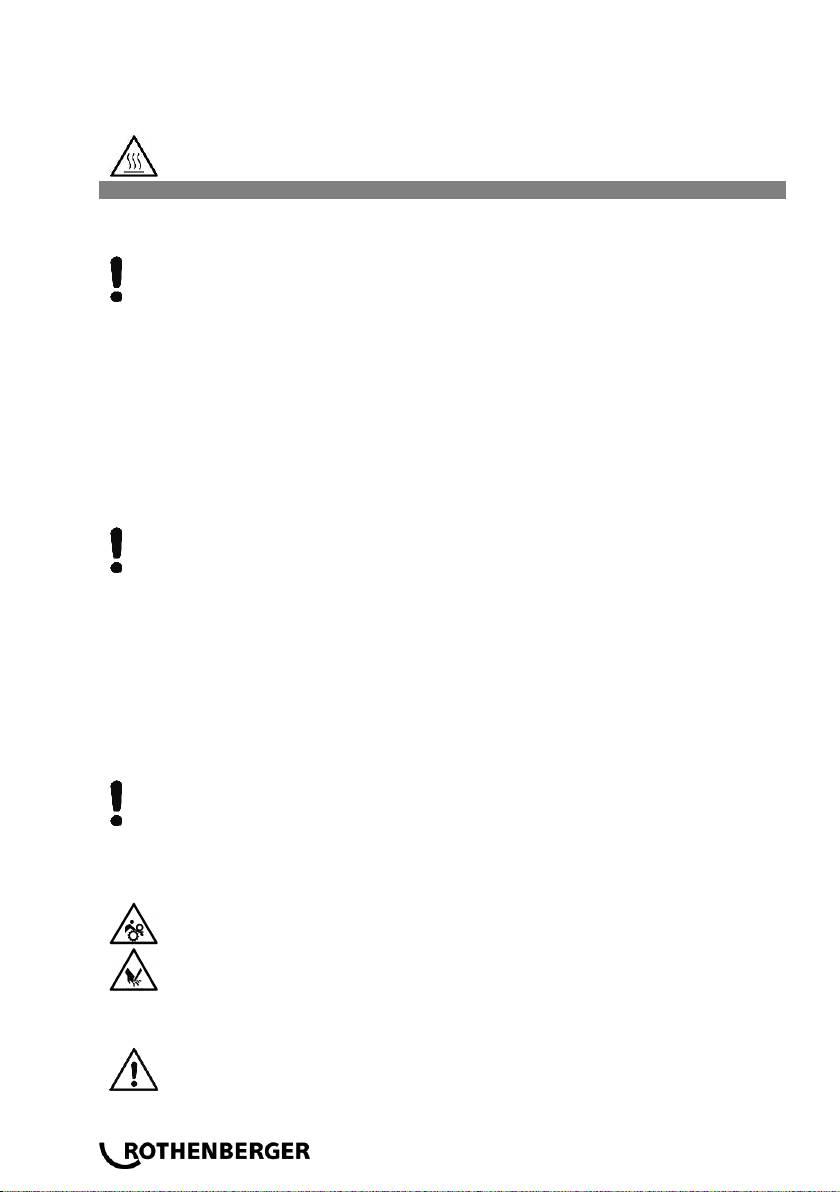
If the heater element displays a smaller value than that on the external temperature measuring
instrument then the difference must be adjusted using the “+“ button. For indicated values in the
other direction adjust the difference using the “-“ button. If “Er1“ appears it means that the elec-
tronics are defective. “Er2“ means that the resistance thermometer is defective or not connected.
14 ENGLISH
Very hot – Do not touch! The heating element can reach a temperature of
approx. 290°C!
3.2.2 Measures for preparing welding
For pipes which are smaller than the maximum diameter of 160 mm to be welded the clamp-
ing inserts / bracket of the corresponding diameter are to be inserted in the main clamps.
Be sure to use the correct reduction clamping inserts! The upper reduction clamp-
ing inserts, or the bracket + lower reduction clamping inserts + support fork in-
serts, must match!
Version A: Open the clamping plates (8) and swing them to the rear position. Press the up-
per reducing insert against the rear stop and tighten the tensioning screw (8.2).
Version B: Open the clamping plates (9) and insert the upper clamping element (9.1) and
tip forward (the clamping pin is the rotation axis).
Insert the lower reduction.
Supports bracket inserts are to be inserted in the support brackets (10) and fastened with
the knurled screws.
Insert the plastic pipes or fittings to be welded into the clamps.
Put the support brackets (10) under the pipe or fitting, loosen hexagonal screw with multi-
purpose spanner SW 17, and move the support bracket accordingly and turn if required.
For straight pipes to be welded align the support brackets with the front surface
parallel to the centre of the groove in the tables!
Version A: Close the clamping plates (8). Using the adjusting nut (8.1) adjust the tension
and bring the handle to the end position until the maximum force is reached.
Version B: Untwist the clamping plates (9), swing the bracket backward and bring the
clamping device to the operating position. When tensioning, be sure that the wings of the
wing nut are always at 90° to the axis of the pipe.
Check whether the workpieces are tight in the clamping tool by moving the workpieces to-
gether. When applied max. welding pressure must not slip through pipes! Thus, a successful
welding process it is ensured.
Also check whether the heating element has reached operating temperature. Heating is
ended when the yellow pilot lamp on the temperature regulator flashes.
To guarantee even distribution of heat over the entire surface of the heating plate,
it is required to wait a period of approx. 10 minutes after the lamp flashes (accord-
ing to DVS). You must check the temperature with an appropriate temperature
measurement device!
Swing the trimmer (1) between the pieces of pipe until the ratchet pawl (7) snaps in and turn
on with the handle.
Risk of injury! Do not grasp into the running knife while the trimmer is put into
operation. Operate trimmer only in swivelled in state (work position) and swiv-
el back again afterwards. The operativeness of the safety switch in the trim-
mer must be guaranteed at all times to prevent unintentional starting outside
the work position!
With the grip bar (6) move the ends of the workpieces carefully against the rotating knives of
the trimmer disks.
An excessively high milling pressure can lead to overheating and damage to
the miller drive. When the milling drive is overloaded or at rest, raise the ma-
chine and reduce the pressure!
Оглавление
- DEUTSCH 3
- DEUTSCH 5
- DEUTSCH 7
- DEUTSCH 9
- ENGLISH 11
- ENGLISH 13
- ENGLISH 15
- ENGLISH 17
- FRANÇAIS 19
- FRANÇAIS 21
- FRANÇAIS 23
- FRANÇAIS 25
- ESPAÑOL 27
- ESPAÑOL 29
- ESPAÑOL 31
- ESPAÑOL 33
- ITALIANO 35
- ITALIANO 37
- ITALIANO 39
- ITALIANO 41
- NEDERLANDS 43
- NEDERLANDS 45
- NEDERLANDS 47
- NEDERLANDS 49
- PORTUGUES 51
- PORTUGUES 53
- PORTUGUES 55
- PORTUGUES 57
- DANSK 59
- DANSK 61
- DANSK 63
- DANSK 65
- SVENSKA 67
- SVENSKA 69
- SVENSKA 71
- SVENSKA 73
- NORSK 75
- NORSK 77
- NORSK 79
- NORSK 81
- SUOMI 83
- SUOMI 85
- SUOMI 87
- SUOMI 89
- POLSKI 91
- POLSKI 93
- POLSKI 95
- POLSKI 97
- ČESKY 99
- ČESKY 101
- ČESKY 103
- ČESKY 105
- MAGYAR 107
- MAGYAR 109
- MAGYAR 111
- MAGYAR 113
- PУCCKИЙ 115
- PУCCKИЙ 117
- PУCCKИЙ 119
- PУCCKИЙ 121
- ROTHENBERGER Worldwide