Rothenberger ROWELD P 110: ENGLISH 13
ENGLISH 13 : Rothenberger ROWELD P 110
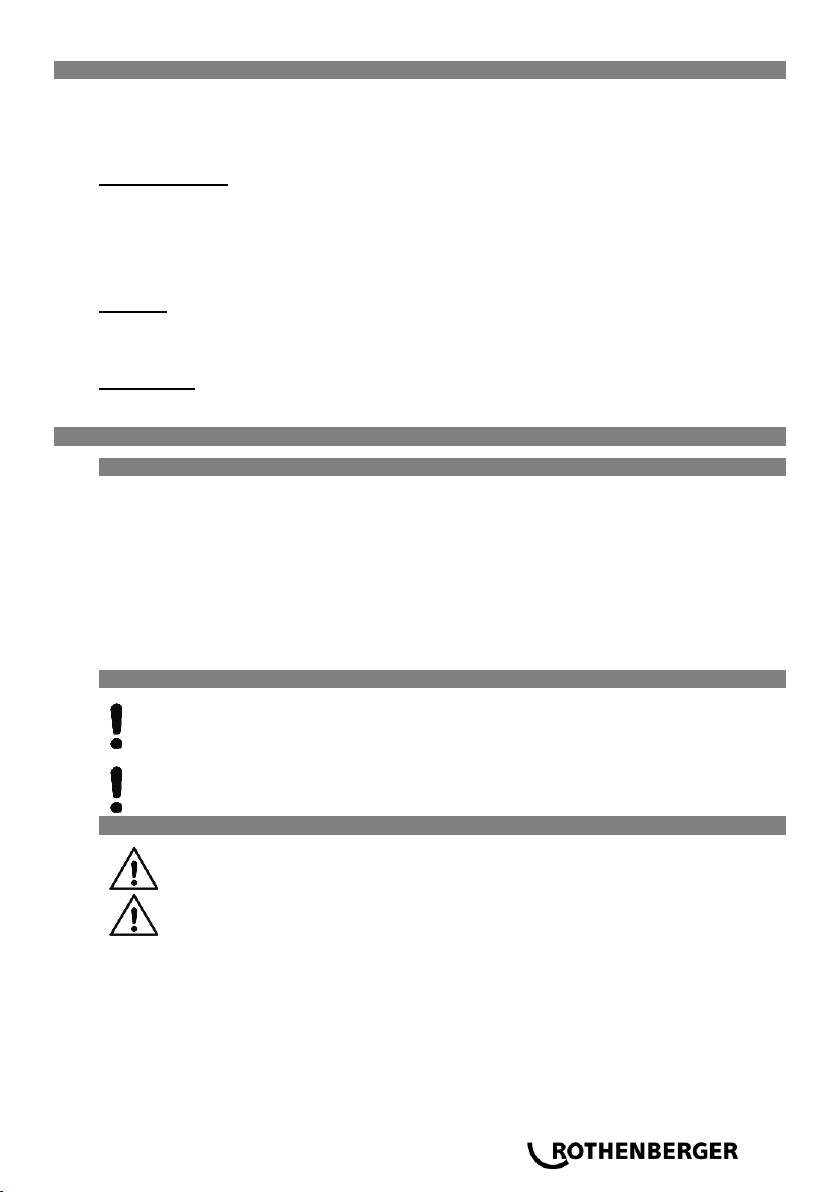
2 Technical Data
ENGLISH 13
Welding range Ø (mm) ....................................
20 - 110
Pressure range ...............................................
SDR series see welding parameter book
Max. traverse path (mm) ................................
165
Heating element:
Power supply ..................................................
230V AC, 50/60Hz, 800W
Heating plate dimension (mm) ........................
180 x 130
Protection / Protection class ............................
I / IP20
Weight (kg) .....................................................
2,6
Weights:
Complete machine (kg) ...................................
11,3
Complete machine with transport box (kg) ......
43,0
Dimensions:
Machine in transport box (mm). ......................
540 x 345 x 355 (LxWxH)
3 Function of the Unit
3.1 Description
ROWELD P 110 is a compact, easy to handle and easy to transport heating plate butt fusion
plastic pipe welding machine. Welding joints on pipes made of PE-, PVDF- and PP with outer
Diameter of 20 to 110 mm can be produced with the machine safely.
The machine basically consists of:
Basic unit with bench mounting fixture, hand operated trimmer, electronically controlled heating
plate, main clamp set for pipe-to-pipe (110 mm) and left side fittings clamp (110 mm) for pipe to
fitting weldings, reduction clamping inserts, tools, table clamp and steel carrying case.
For precise welding of flanges and pre-fabrication a flange adaptor (Art.No.: 55199) is available
as an option.
3.2 Operating instructions
In accordance with national or EU ordinances and guidelines, e. g. DVS 2212,
Section I, only duly qualified and authorised personnel are allowed to operate the
ROWELD welding machines!
Only trained and authorised welders are allowed to operate the machine!
3.2.1 Putting into operation
Please read through the operating instructions and safety instructions atten-
tively before you put the butt fusion welding machine into operation!
Do not use the heating element in explosive environments or bring it into
contact with easily flammable materials!
Either fasten the basic unit on a workbench by using the included screws or fasten it by us-
ing an existing vice.
Fasten the table clamp on the workbench and put the heating element in it.
Connect power plug to the power supply stated on the type plate.
The red diode “Stand by“ lights up. That is: there is a voltage being applied. Switch on the
heater element using the large pushbutton (lights up green) and select the desired tempera-
ture (160°C to 285°C) using the “+“ or “-“ button.
Heating up of the heater element is displayed by a yellow diode on the heater element. A hori-
zontal bar also appears on the temperature indicator. The yellow diode goes out shortly before
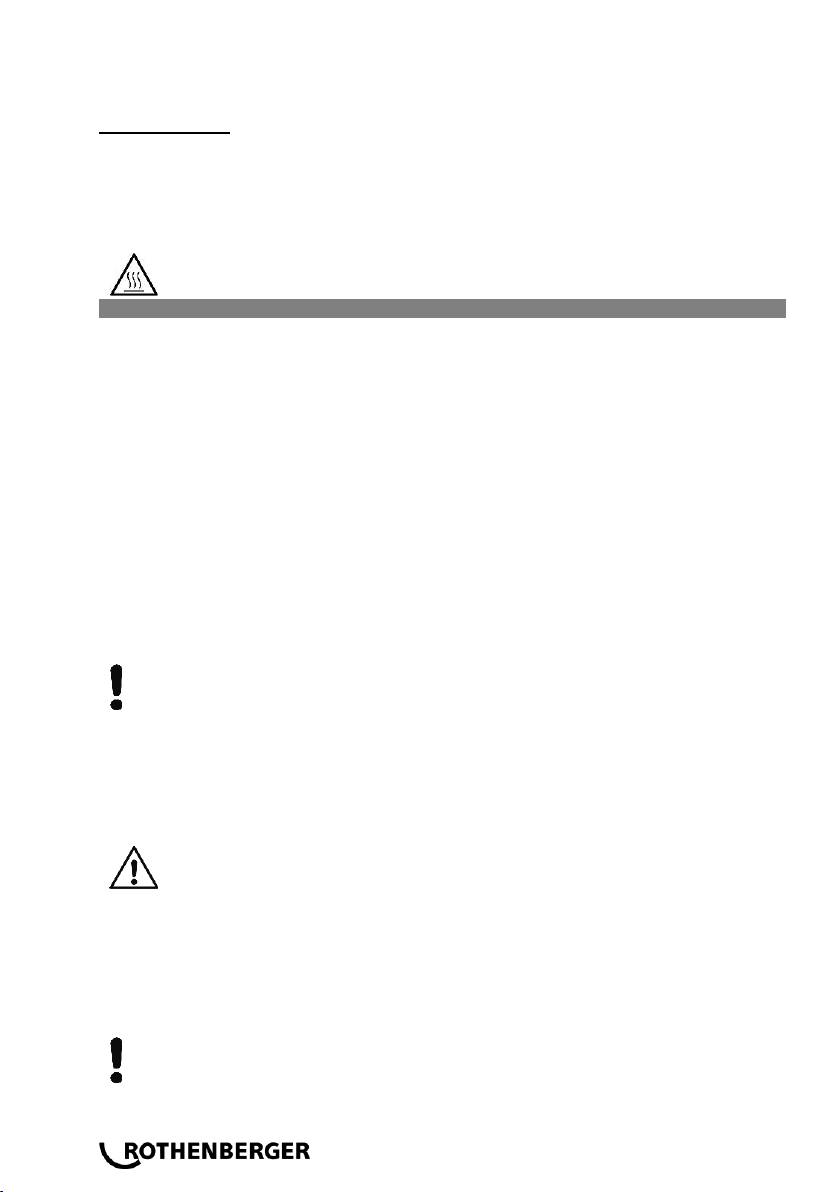
reaching the set temperature (tolerance +/-3°C) and the green one lights up. After a further 10
minutes the heating element is ready to use. Check the temperature using a temperature meas-
uring instrument.
Setting the off-set: press the “+“ and “-“ button at the same time. The heater element can subse-
quently be calibrated using one of these buttons and an external temperature measuring instru-
ment.
If the heater element displays a smaller value than that on the external temperature measuring
instrument then the difference must be adjusted using the “+“ button. For indicated values in the
other direction adjust the difference using the “-“ button. If “Er1“ appears it means that the elec-
tronics are defective. “Er2“ means that the resistance thermometer is defective or not connected.
14 ENGLISH
Very hot – Do not touch! The heating element can reach a temperature of
approx. 290°C!
3.2.2 Measures for preparing welding
For Pipe-to-Pipe welding the two wide main clamps are remaining in the machine.
For Pip-to-Fitting welding the left hand side wide main clamp has to be changed against small
Fitting main clamp.
For Fitting-to-Fitting welding both wide main clamps have to be changed against small fitting
main clamps.
The right hand side small fitting main clamp is available as an option (art. No. 55809).
Loosen winged handle at main clamp set and swivel away to the front. Then move upper
main clamps up and backwards.
For pipes which are smaller than the maximum diameter of 110 mm insert reduction clamp-
ing inserts and fix them by using the knurled screw.
Insert the plastic pipes or fittings to be welded into the clamps. Close upper clamps swivel in
winged handle, align pipe or fitting and screw up the winged handle tightly.
Check whether the workpieces are tight in the clamping tool by moving the workpieces to-
gether.
Also check whether the heating element has reached operating temperature. Heating is
ended when the yellow pilot lamp on the temperature regulator flashes.
To guarantee even distribution of heat over the entire surface of the heating plate,
it is required to wait a period of approx. 10 minutes after the lamp flashes (accord-
ing to DVS). You must check the temperature with an appropriate temperature
measurement device!
Place the trimmer between the pipe sections to be welded and fix it by the swivel.
With the hand wheel move the pipe ends carefully against the trimmer blades of the trimmer
discs and turn the trimmer around by moving the handle up and down.
Pipes and fittings can be machined on one side only by turning the block screws on the front
bottom side of the machine towards the side, which is not to be machined.
Risk of injury! Do not grasp into the running knife while the trimmer is put into
operation!
After the front sides are trimmed flat, which can be recognized by an uniform and unbroken
chip, slowly move the pipe ends apart. Unlock the trimmer by the swivel and remove it.
Move workpieces together and check whether the welded surfaces are flat. If this is not the
case, trimming must be repeated.
The axial offset between the workpieces must not be more than 10% of the wall thicknes and the
gap between the flat pipe surfaces must be more than 0,5 mm (according DVS). Otherwise ad-
just with help of the clamping screws and repeat trimming.
The trimmed surfaces prepared for welding must not be touched with the hands
and must be kept free of dirt!
Оглавление
- DEUTSCH 3
- DEUTSCH 5
- DEUTSCH 7
- DEUTSCH 9
- ENGLISH 11
- ENGLISH 13
- ENGLISH 15
- ENGLISH 17
- FRANÇAIS 19
- FRANÇAIS 21
- FRANÇAIS 23
- FRANÇAIS 25
- ESPAÑOL 27
- ESPAÑOL 29
- ESPAÑOL 31
- ESPAÑOL 33
- ITALIANO 35
- ITALIANO 37
- ITALIANO 39
- ITALIANO 41
- NEDERLANDS 43
- NEDERLANDS 45
- NEDERLANDS 47
- NEDERLANDS 49
- PORTUGUES 51
- PORTUGUES 53
- PORTUGUES 55
- PORTUGUES 57
- DANSK 59
- DANSK 61
- DANSK 63
- DANSK 65
- POLSKI 67
- POLSKI 69
- POLSKI 71
- POLSKI 73
- ČESKY 75
- ČESKY 77
- ČESKY 79
- ČESKY 81
- MAGYAR 83
- MAGYAR 85
- MAGYAR 87
- MAGYAR 89
- PУCCKИЙ 91
- PУCCKИЙ 93
- PУCCKИЙ 95
- PУCCKИЙ 97
- ROTHENBERGER Worldwide