Festool DWC 18: CAUTION
CAUTION: Festool DWC 18
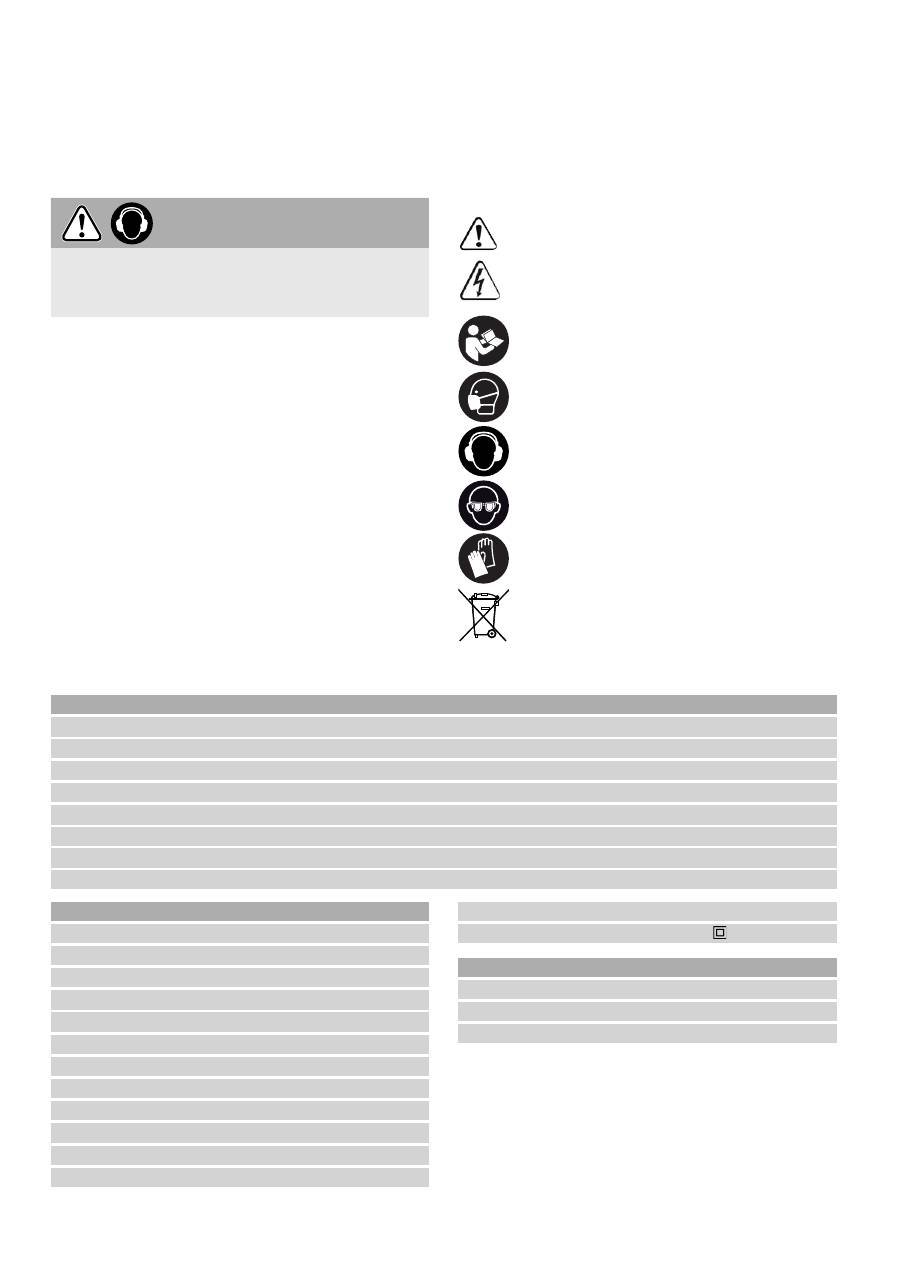
14
1.3 Emission
levels
Levels determined in accordance with EN 60 745
are typically:
Sound pressure level
L
PA
= 78 dB (A)
Noise level
L
WA
= 89 dB (A)
Measuring uncertainty allowance
K = 3 dB
CAUTION
The noise produced during work can damage
your hearing.
Always use ear protection.
Overall vibration levels (vector sum for three direc-
tions) measured in accordance with EN 60 745:
DWC 18-2500
Vibration emission level
(3 directions)
a
h
= 2.8 m/s
2
Uncertainty
K = 1.5 m/s
2
DWC 18-4500
Vibration emission level
(3 directions)
a
h
= 3.5 m/s
2
Uncertainty
K = 1.5 m/s
2
The specifi ed emissions values (vibration, noise)
– are used to compare machines.
– They are also used for making preliminary es-
timates regarding vibration and noise loads
during operation.
– They represent the primary applications of the
power tool.
Increase possible for other applications, with oth-
er insertion tools or if not maintained adequately.
Take note of idling and downtimes of machine!
2 Symbols
Warning of general danger
Risk of electric shock
Read the operating instructions/notes!
Wear a dust mask!
Wear ear protection!
Wear eye protection!
Wear protective gloves!
Do not throw in the household waste!
Advice or tip
3 Technical
data
Cordless drywall screwdriver
DWC 18-2500
DWC 18-4500
Motor voltage
18 V
18 V
Idle speed*
0 – 2500/min
0 – 4500/min
Torque (hard / soft)
7 / 18 Nm
5 / 14 Nm
Chuck
¼” DIN 3126 / ISO 1173
Weight (without battery pack)
1.1 kg
1.1 kg
Weight with depth stopper (without battery pack)
1.2 kg
1.2 kg
Weight with auto feed attachment
(without battery pack)
1.5 kg
1.5 kg
Charger TCL
3
Mains voltage (input)
220 - 240 V ~
Mains frequency
50/60 Hz
Charging voltage (output)
10.8 - 18 V=
Rapid charging
max. 3 A
Conservation charging,
intermittent (NiCd, NiMH)
approx. 0,06 A
Charging times for BP, BPS and BPC battery packs
Li-ion 1,5 Ah, 80 %/100 % approx. 25/35 min.
Li-ion 3,0 Ah, 80 %/100 % approx. 55/70 min.
Li-ion 4,2 Ah, 80 %/100 % approx. 70/90 min.
Permitted operating temperature range
-5 °C to + 45 °C
Temperature monitoring
via NTC resistor
Safety class
/ II
Battery pack
BPC 18 Li
Voltage 1
18 V
Capacity
4.2 Ah
Weight
0.7 kg
* Speed specifi cations with fully charged battery
pack.
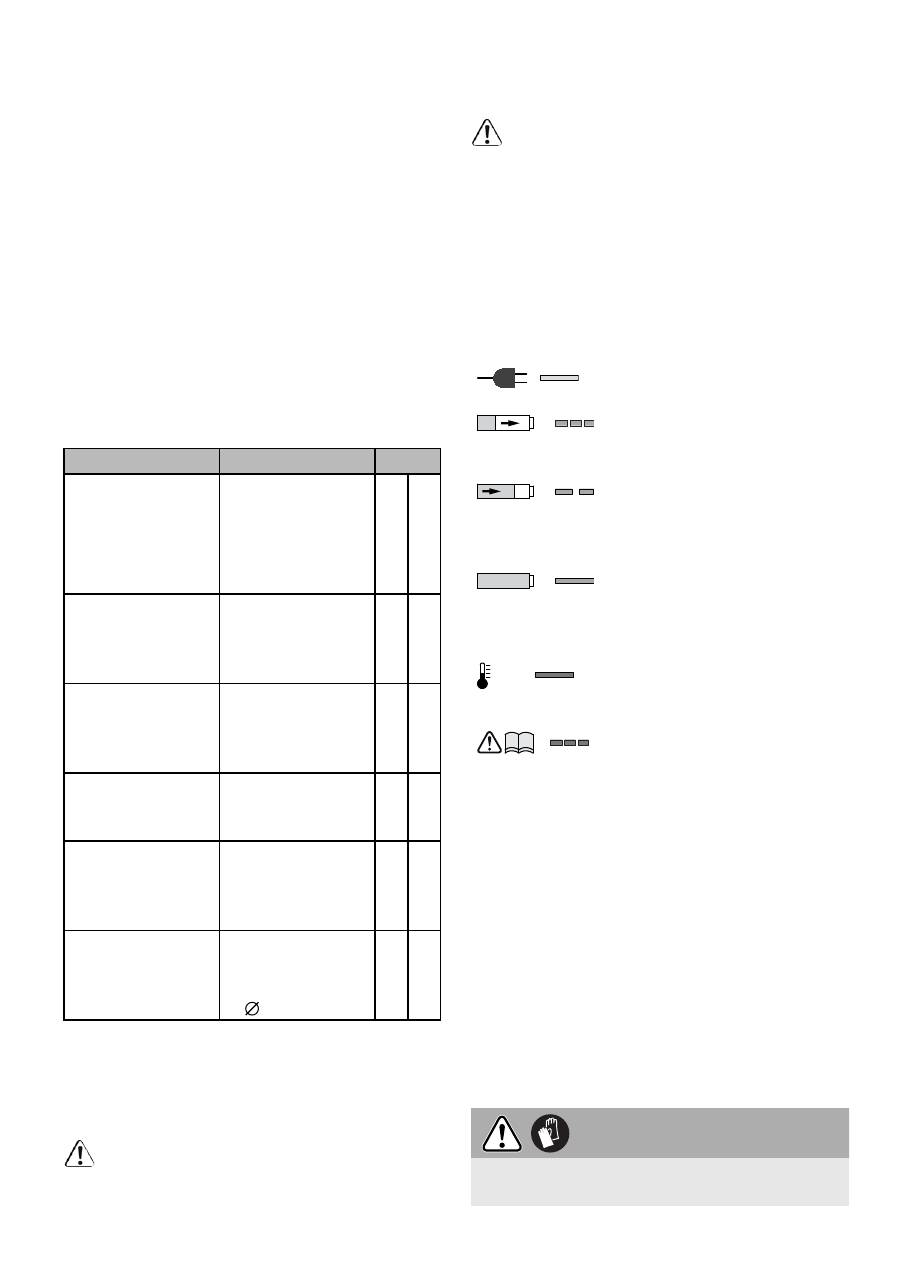
15
4 Machine
features
[1-1]
Bit
storage
[1-2]
Switch
[1-3]
Forward / reverse switch
[1-4]
AUTO/MAN
switch
[1-5]
Depth
stopper
[1-6]
Bit
[3-1]
LED
[3-2]
Cable
holder
[3a]
Wall
mount
The accessories shown or described do not have
to be included with the supplied tool. The speci-
fi ed illustrations appear at the beginning of the
Operating Instructions.
5 Intended
use
The drywall screwdriver is designed for the fol-
lowing works:
Main application
Screw types
Type
D
W
C
18-2500
D
W
C
18-4500
Gypsum plas-
ter boards on
metal profi le rails
(≤ 0.88 mm)
Drywall screws
with fi ne thread
×
Gypsum plas-
ter boards on
metal profi le rails
(≤ 2.25 mm)
Drywall screws,
self-drilling
×
Gypsum plaster
boards on wooden
constructions
Drywall screws
with coarse
thread
×
Gypsum fi bre
boards on metal
and wooden con-
structions
Drywall screws
with milling ribs
×
Chip boards/OSB
on wooden con-
structions
Wood construc-
tion and chip
board screws up
to 5 mm
×
Charger TCL 3 suitable for
– charging Festool battery packs: BP, BPS and
BPC (NiMH, NiCd, li-ion are recognised auto-
matically.)
– indoor use only.
The user is liable for improper or non-in-
tended use; this also includes continuous
industrial operation.
6
Commissioning
6.1
Charger cable holder [3-2]
Unwind the cable completely from the re-
cess before using the charger.
6.2
Changing the battery pack
Removing the battery pack [2 A]
Inserting the battery pack [2 B]
Battery pack is ready for use immediately upon
delivery and can be charged at any time.
6.3 Charging the battery pack [3]
The LED
[3-1]
on the charger indicates the re-
spective operating status of the charger.
LED yellow – lit continuously
Charger is ready to use.
LED green – fl ashing quickly
Battery pack is charged to max-
imum capa city.
LED green – fl ashing slowly
Battery pack is charged with re-
duced current, LiIon is charged
to 80 %.
LED green – lit continuously
Charging is complete or is not
restarted as current charge
status is greater than 80%.
LED red – lit continuously
Battery temperature is outside
the permitted range.
LED red – fl ashing
General fault display, e. g. in-
complete contact, short circuit,
battery pack faulty, etc..
7
Power tool settings
Setting must be done only when the power tool
is turned off and will be accepted only after
restarting it.
6.1
Changing the direction of rotation [1-3]
Move switch from right to left = clockwise rotation;
Move switch from left to right = anticlockwise ro-
tation.
8
Tool holder, attachments
8.1 Bit
holder
The bit holder is used for fast replacement of bits.
CAUTION
Risk of cutting injuries when changing the tool!
Wear protective gloves!

16
Bit holder assembly
Set the switch
[1-4]
into MAN position.
Set the bit holder
[4-2]
completely to the hex-
agonal spindle opening
[4-4]
.
Attach bit into the holder
[4-3]
.
Then attach the depth stopper on the gear box
as specifi ed in chapter 9.2.
Bit holder disassembly
Remove the depth stopper as specifi ed in chap-
ter 9.2.
Use power to pull out the holder from the spin-
dle opening.
8.2 Bit
replacement
You can use the depth stopper
[1-5]
for the bit
replacement
[1-6]
.
Attach the depth stopper on the bit (see fi gure
[4 b]
).
By means of jamming the depth stopper with
the bit and concurrent pulling, it is possible to
pull out the bit.
Then attach a new bit in the holder.
9 Operation
9.1
Switching on and off
Pressing only the switch
[1-2]
does not start
the machine –
it is not a machine fault!
Upon screwing to the required depth, the power
tool switches off!
The machine can be switched on by means of sev-
eral methods:
a)
Set the forward / reverse switch
[1-3]
into ma-
chine clockwise operation.
Set the switch
[1-4]
into MAN position. In order
to switch on the power tool, apply the switch
[1-
2]
and concurrently press the bit on the screw.
Use the switch
[1-2]
to gradually regulate the
speed.
b)
Set the forward / reverse switch
[1-3]
into ma-
chine clockwise operation.
Set the switch
[1-4]
into AUTO position.
Press the bit on the screw and the power tool
will switch on.
Switch
[1-2]
does not need to be pressed. Maxi-
mum speed is set automatically.
c)
Set the forward / reverse switch
[1-3]
into ma-
chine anti-clockwise operation.
In order to start the power tool, press the
switch
[1-2]
. The switch MAN/AUTO
[1-4]
is
in any position.
Use the switch
[1-2]
to gradually regulate the
speed.
If the forward / reverse switch
[1-3]
is set to
anti-clockwise operation, the screwdriver can
be started only by pressing the switch
[1-2]
–
without additional pressure on the bit!
It is not necessary to remove the depth stopper
in order to unscrew screws!
9.2 Depth
stopper
Turning the depth stopper sets the screwing depth
– see fi gure
[5]
. The setting accuracy is approx ±
0.1 mm.
Anti-clockwise rotation =
screws are insert-
ed deeper
Clockwise rotation
=
screws are insert-
ed to lower depth
Upon setting the depth, set some screws to test
and adjust the depth.
Depth stopper assembly
Fit the depth stopper
[4-1]
on the gear box
[4-
5]
, until it engages in the groove.
Depth stopper disassembly
Remove the depth stopper from the gear box
by pulling it.
9.3
Hook and clip
Use the clip
[6-1]
to temporarily attach the screw-
driver on the working clothing – it can be attached
by means of a screw
[6-2]
to the left or right of
the power tool, and it is suitable for right and left
handed people – see fi gure
[6]
.
The screwdriver is equipped with a hook
[7-1]
,
which is used for occasional machine suspension.
It can be attached to the left or right of the power
tool, by means of a screw
[7-2]
– see fi gure
[7]
.
9.4
Auto feed attachment
The auto feed attachment enables to work con-
tinuously, without unnecessary delays.
Fitting the auto feed attachment
At fi rst remove the depth stopper
[4-1]
, bit
holder
[4-2]
and bit, as specifi ed in chapter 8.
Set the switch
[1-4]
into MAN position.
Push the long bit
[8-1]
completely to the hex-
agonal spindle opening
[4-4]
.
Then fi t the auto feed attachment on the gear
box.
Push the attachment until it engages in the
groove of the gear box.
The attachment can be mounted at 30° steps.
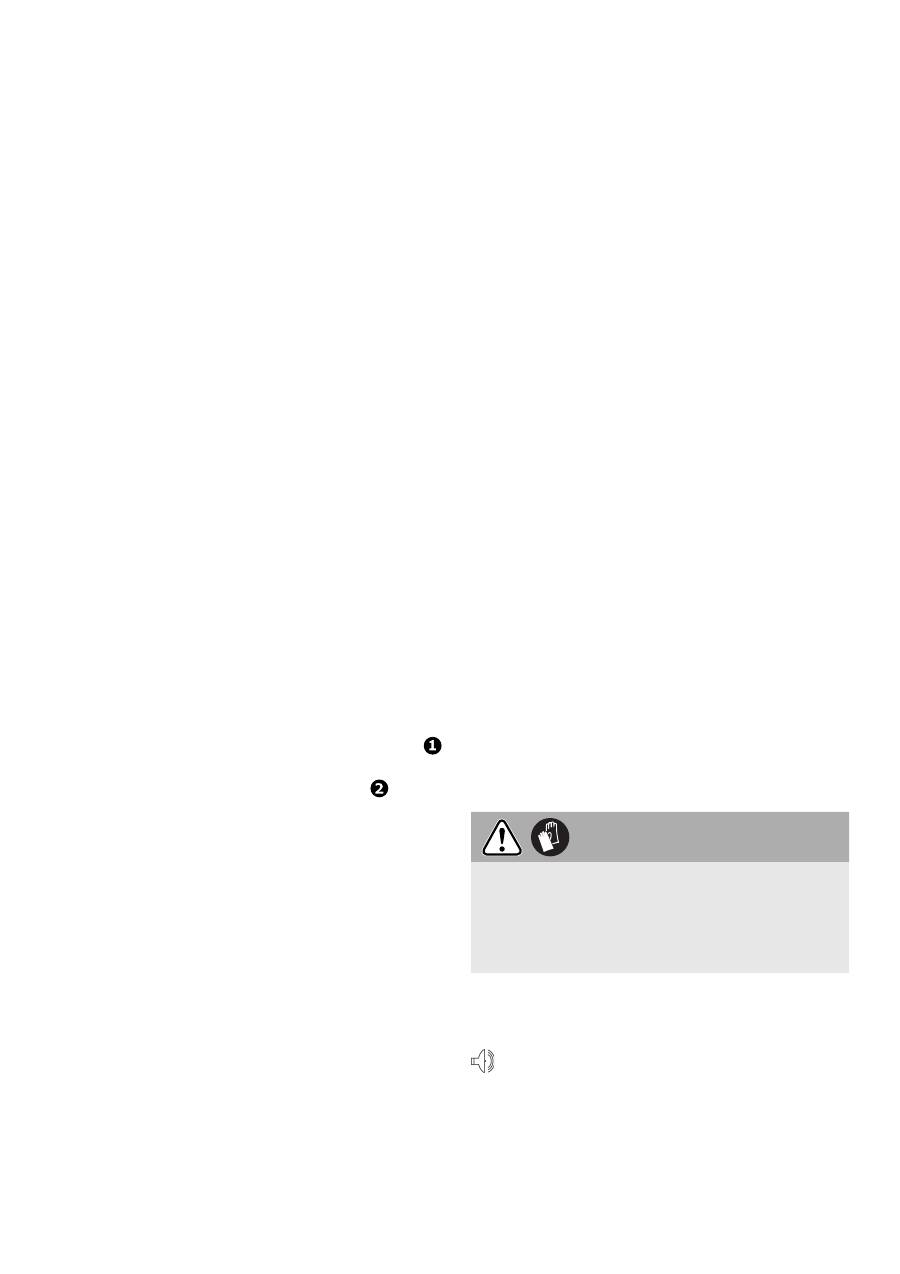
17
Removing the auto feed attachment
Use power to carefully pull the attachment
from the gear box.
Setting the screw length
Press button
[9-1]
to remove and insert the
depth stopper
[9-2]
and set the required screw
length.
Read the set screw length on the stopper sides
[9-3]
.
Inserting collated screw strips
Pull the collated screws
[10-3]
through the
bottom guiding of the attachment, then push
the strip through the second guiding until it
engages in the working position.
Pull the belt slightly to make sure that it is
safely fi tted.
Make sure that the fi rst screw is in the screw-
ing axes – see fi gure
[10]
.
Use the wheel
[10-1]
to set the required screw-
ing depth. Turn to the right for inserting the
screws deeper, and to the left to screw to lower
depth. The actual setting position is visible on
the presetting indicator
[10-2]
.
Upon setting, set some screws for testing and use
the wheel
[10-1]
to adjust the depth, if required.
Each setting change complies with the stopper
shift o ± 0.1 mm.
We recommend to screw in automatic mode –
see point 9.1 b).
Removing the collated screws
Pull upwards to remove the belt (fi gure
[11]
) or press the transport lever and concurrently
pull the belt downwards (fi gure
[11]
).
10 Working
instructions
-
The auto feed attachment must not be held in
the depth stopper area as there are moving
parts!
-
Each screw adjustment must be completed. In-
terrupted fastening or releasing of the pressure
during adjustment can result in unsatisfactory
machine function.
-
The collated screws and the auto feed attach-
ment can only be replaced when the power tool
is turned off.
-
Never use the auto feed attachment in any other
way than specifi ed in this instruction manual.
-
Use only original screwing bits.
-
Use only original collated screws.
-
Always store the collated screws in original
packaging.
-
Always work in right angle against the attached
board.
Maintenance of the auto feed attachment
The attachment generally does not require any
maintenance. After long period use, we recom-
mend to clean with pressurized air.
The auto feed attachment may be lubricated in
the area of the carriage guide (see picture
[12 b]
).
Prior to cleaning, dismantle the attachment, as
specifi ed above.
Prior to cleaning, remove the collated screws
from the attachment, as specifi ed in the point
Removing the collated screws.
Pull the auto feed attachment from the drywall
screwdriver.
Disassembly of the slides
1. Push the depth stopper
[9-2]
into the housing
until the arresting button
[12-1]
is at the level
of the sign for dismantling the slides
[12-2]
–
see fi gure
[12 a]
.
2. Press the arresting button
[12-1]
and concur-
rently remove the slides from the holder – see
fi gure
[12 b]
.
3. Press the button
[9-1]
and concurrently re-
lease the depth stopper – see fi gure
[12 c]
.
Transport lever disassembly
1. Press the button
[13-1]
and concurrently pull
it out– see fi gure
[13 a]
.
2. Remove the released button
[13-1]
(figure
[13 b]
) with the transport lever
[13-2]
and the
spring
[13-3]
from the slides (fi gure
[13 c]
).
Clean individual parts, replace defective or worn
parts, and assemble in the opposite sequence.
CAUTION
During reassembly of the transport lever into
the slides, pay due care to correct fi tting of the
spring [13-3] in the transport lever. Incorrect
assembly may result in dysfunction of the belt
transport.
Acoustic warning signal
Acoustic warning signals sound and the machine
switches off in the following operating states:
peep
- Battery
fl at or machine
overloaded
• Change the battery pack.
• Place the machine under
reduced stress.