HEIDENHAIN PWM 20: 4 Installation
4 Installation: HEIDENHAIN PWM 20

Operating Instructions
en
PWM 20
22
3.2 Installation location NOTICE
Damage to the device may result from incorrect
placement.
Always position the device horizontally.
Place the device in a location where it is easily
accessible during operation.
Ensure sufficient ventilation.
Do not block the vents on the rear and side panels or
impair airflow.
The device features a temperature-controlled
fan, which is activated if the maximum internal
temperature is exceeded and deactivated when
the temperature has cooled down sufficiently.
For information on the installation position, see "C" on the
front fold-out page.
4 Installation
NOTICE
Risk of damage to internal components!
Do not engage or disengage any connecting elements
while the product is under power.
Depending on the product's equipment, the
installation may differ from the procedure
described in this chapter. If the Addendum
included with the product contains information
on the installation, the information given in
the Addendum takes precedence over the
information in this chapter.
The illustrations of pin layouts always show
the pin assignments of the connections on the
product, and not of the connectors.
The safety of any system incorporating the
use of this product is the responsibility of the
operator of the system.

PWM 20
Operating Instructions
en
23
4.1 Product overview
Front panel
See "A" on the front fold-out page.
X1
15-pin D-sub input for HEIDENHAIN en-
coders with
11 µA
PP
/25 µA
PP
interface 1 V
PP
/3 V
PP
interface (1 V
PP
/Z1, 1 V
PP
with limit positions, 1 V
PP
with clock/data) EnDat/SSI interface TTL interface with limit positions HTL interface (connection only for ser- vice purposes via external adapter, e.g. ID 1093210-01) Fanuc, Mitsubishi, Yaskawa, or Panasonic interface
X2
15-pin D-sub output for feed-through mode
of the encoder signals from X1
X3
6-pin mini-DIN connection for external func-
tions
X4
8+2-pin RJ-45 connection for encoders with
a DRIVE-CLiQ interface
L1
Status display for operating readiness
Off: Not ready
On (green): Ready
L2
Status display for encoder supply
Off: Encoder supply switched off
On (green): Encoder supply switched on
Rear panel
See "B" on the front fold-out page.
1
Power switch
X5
USB Type B socket (USB 2.0), data interface
X6
Power connection
4.2 Connecting the line voltage WARNING
Risk of electric shock!
Improper grounding of electrical devices involves a risk of
serious injury or death by electric shock.
Always use 3-wire power cables.
Make sure the ground wire is correctly connected to
the ground of the building's electrical installations.
WARNING
Fire hazard from the use of power cables that do not
meet the minimum requirements!
Use only power cables that fulfill or exceed the
specified minimum requirements.
Use the supplied power cable to connect the power
connection X6 to a 3-wire grounded power outlet.
For information about the location of the power connection
on the rear panel, see "Rear panel", page 23.
For signal assignment of the power connection X6, see "R".
4.3 Electrostatic discharge NOTICE
This product contains components
that can be destroyed by electro-
static discharge (ESD).
It is essential to observe the safety
precautions for handling ESD-sensiti-
ve components.
Never touch connector pins without
ensuring proper grounding.
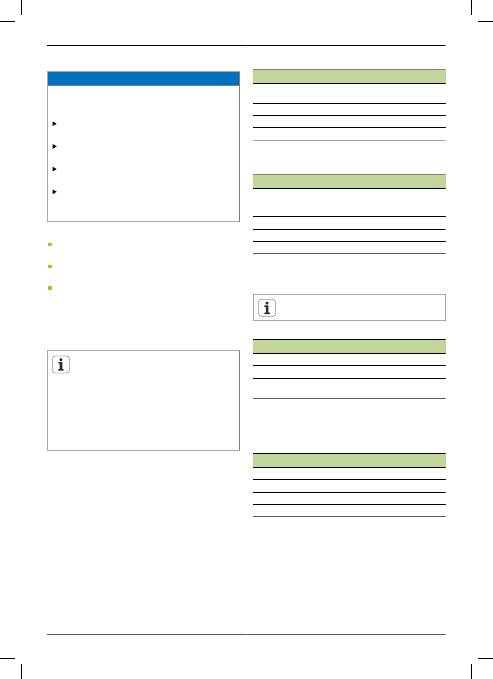
Operating Instructions
en
PWM 20
24
4.4 Connecting encoders NOTICE
Danger of damage to the device and encoder damage
due to incorrect voltage supply range and incorrect
wiring!
Note the voltage supply range of the connected
encoder.
Check whether the cable between the encoder and
device is correctly wired.
The cable between the encoder and the device must
not be connected or disconnected while under power.
The connection and operation of the device with
encoders that are not from HEIDENHAIN is the user‘s
own risk.
Connections
Encoders with a 15-pin interface are connected to
encoder input X1 on the front panel.
When connected to the control loop, encoder output X2
is used for encoders with a 15-pin interface.
Encoders with 8+2-pin DRIVE-CLiQ interfaces are
connected to encoder input X4 on the front panel.
For information on the location of the connections, see
"Product overview", page 23.
The pin layouts of the connecting cables are described in
the catalog.
Notes on the signal assignment of the pins in the
annex:
Cable shield connected to housing;
U
P
= Power supply
Sensor: The sensor lines are connected
internally with the corresponding voltage
supply, depending on the settings in the
ATS software ("ATS Software Operating
Instructions" document, see "Notes on reading
the documentation", page 18).
EnDat/SSI interface Pin Function
1, 3, 7, 9, 11, 14
Incremental signals (only with ordering
designations EnDat 01 and EnDat 02)
2, 4, 10, 12
Voltage supply
5, 8, 13, 15
Position values
6
Internal shield
For signal assignment of EnDat/SSI, see "F".
Fanuc, Mitsubishi, Yaskawa, or Panasonic interface Pin Function
1, 3, 7, 9, 11, 14
Incremental signals (if available, only
for adjusting; do not use in normal ope-
ration)
2, 4, 10, 12
Voltage supply
5, 8, 13, 15
Position values
6
/
For signal assignment of Fanuc, see "G".
For signal assignment of Mitsubishi, see "H".
For signal assignment of Yaskawa and Panasonic, see "I".
Fanuc and Mitsubishi: Do not use pins 5 and 13
for one-pair transmission.
1 V
pp
/ 3 V
pp
interface Pin Function
1, 3, 7, 9, 11, 14
Incremental signals
2, 4, 10, 12
Voltage supply
5, 6, 8, 13, 15
Other device-dependent signals
(switched internally)
For signal assignment of 1 V
pp
with limit positions, see "J".
For signal assignment of 1 V
pp
/Z1, see "K".
For signal assignment of 1 V
pp
with clock/data, see "L".
11 µA
pp
/ 25 µA
pp
interface Pin Function
1, 3, 7, 9, 11, 14
Incremental signals
2, 4
Voltage supply
5, 6, 8, 10, 12, 13, 15
/
6
Internal shield
For signal assignment of 11 µA
pp
(25 µA
pp
), see "M".

PWM 20
Operating Instructions
en
25
TTL interface (with limit positions) and HTL interface Pin Function
1, 3, 7, 9, 11, 14
Incremental signals
2, 4, 10, 12
Voltage supply
3, 13, 15
/
6, 8
Limit signals
(if supported by the encoder)
For signal assignment of TTL and HTL, see "N".
Connection X4
For signal assignment of DRIVE-CLiQ, see "P".
Encoder output X2
The encoder input X1 of the device is electrically connected
with the encoder output X2. The signals and the pin layout
at the output correspond to the respective signals at the
input (signals are picked off or actively emulated).
There is no galvanic isolation of the signals. The supply and
sensor lines are switched via the ATS software as of version
V2.6 depending on the respective mode of operation and
may be connected (see examples below). It is always
ensured that the supply voltage generated by the device is
not present at X2.
Example 1
–
Device in feed-through mode (the encoder is
powered by the subsequent electronics) / ATS software not
started.
Example 2
–
The device powers the encoder via X1:
Connecting the encoder cables
Connect the cables of the encoders tightly to the
respective connections.
If the cable connectors include mounting screws, do not
overtighten them.
Do not subject the plug connections (encoder input X4)
to mechanical load.
Vacant pins or wires must not be used.
4.4.1 Grounding conditions when connected to the control loop
The device has an internal wide-range switching power
supply. The PE terminal (protective earth), which is also
connected with the housing of the device, is therefore
required. If the device is integrated in the control loop
of an NC-controlled machine, it constitutes an additional
grounding point, which changes the shielding concept.
The following measures can be taken to prevent this:
Supply the device via an isolating transformer, or
Supply the device with 24 V DC
To evaluate the measuring data of the device, a PC is
connected to the device's USB interface. The 0 V potential
and the protective earth terminal are usually connected to
each other in the PC (also USB). If the device is integrated in
the control loop of an NC-controlled machine, the conditions
on the 0 V connection change, too.
The following measures can be taken to prevent this:
Use a battery-operated laptop as PC, or
Use a laptop with a power supply unit without protective
earth terminal
Оглавление
- 1 Zu dieser Anleitung
- 2 Sicherheit
- 3 Montage
- 4 Installation
- 5 Bedienung
- 6 Wartung
- 7 Demontage, Umweltschutz undEntsorgung
- 8 Technische Daten
- 1 About these instructions
- 2 Safety
- 3 Mounting
- 4 Installation
- 5 Operation
- 6 Maintenance
- 7 Removal, environmental protectionand disposal
- 8 Specifications
- 1 A propos de cette notice
- 2 Sécurité
- 3 Montage
- 4 Installation
- 5 Utilisation
- 6 Maintenance
- 8 Caractéristiques techniques
- 1 Informazioni contenute nel presentemanuale
- 2 Sicurezza
- 3 Montaggio
- 4 Installazione
- 5 Funzionamento
- 6 Manutenzione
- 8 Dati tecnici
- 1 Acerca de este manual
- 2 Seguridad
- 3 Montaje
- 4 Instalación
- 5 Manejo
- 6 Mantenimiento
- 8 Características técnicas
- 1 Om denna manual
- 2 Säkerhet
- 3 Montage
- 4 Installation
- 5 Handhavande
- 6 Underhåll
- 7 Demontering, miljöskydd ochavfallshantering
- 8 Tekniska data
- 1 Over deze handleiding
- 2 Veiligheid
- 3 Montage
- 4 Installatie
- 5 Bediening
- 6 Onderhoud
- 7 Demontage, milieubescherming enafvoer
- 8 Technische gegevens
- 1 O tomto návodu
- 2 Bezpečnost
- 3 Montáž
- 4 Instalace
- 5 Ovládání
- 6 Údržba
- 7 Demontáž, životní prostředí alikvidace
- 8 Technické parametry
- 1 この説明書について
- 2 安全
- 3 組立て
- 4 設置
- 5 操作
- 6 メンテナンス
- 7 解体、環境保護および廃棄
- 8 技術仕様
- 1 О настоящей инструкции
- 2 Безопасность
- 3 Монтаж
- 4 Установка
- 5 Эксплуатация
- 6 Техобслуживание
- 8 Технические характеристики
- 1 关于这些说明
- 2 安全
- 3 安装
- 4 系统安装
- 5 操作
- 6 维护
- 8 技术参数
- 1 關於這些手冊
- 2 安全
- 3 安裝
- 4 安裝
- 5 操作
- 6 保養
- 8 規格
- 1 본 지침 정보
- 2 안전
- 3 장착
- 4 설치
- 5 작업
- 6 유지관리
- 7 제거, 환경 보호 및 처리
- 8 사양
- *I_1125089-90*