HEIDENHAIN PWM 20: 5 Operation
5 Operation: HEIDENHAIN PWM 20
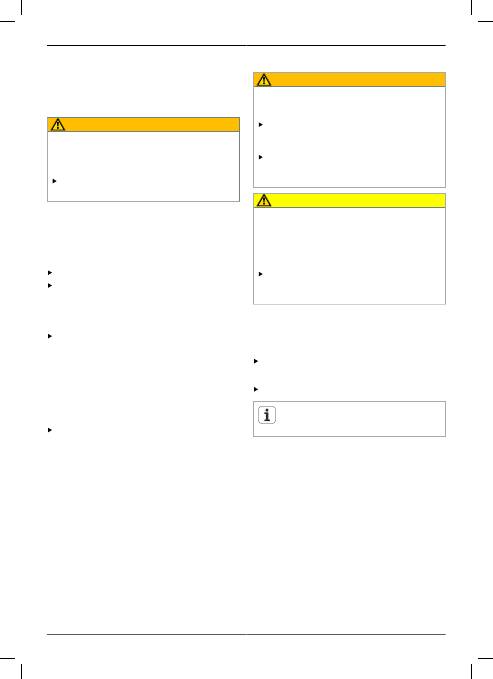
Operating Instructions
en
PWM 20
26
4.4.2 Connecting the PWM 20 into the control loop of an NC-controlled machine
For diagnostic purposes, the device can be integrated
into the control loop of an NC-controlled machine via
the encoder input and output (see "Encoder output X2",
page 25).
WARNING
Danger of electric shock!
If the device is integrated into the control loop of an
NC-controlled machine, the grounding conditions can
change.
Adapt the grounding and any specifics to the
respective conditions of use.
Depending on the ATS software version and under
compliance with the notes on the grounding conditions, the
device can be operated in a closed loop.
However, a signal adapter (e.g. SA 100, SA 110, …) must
always be used, or is recommended for use.
Connect the device in the following order:
First switch off the machine.
Then disengage the connecting elements.
4.5 Connecting a computer
A computer can be connected to the USB port X5 (USB
Type B) via its High-Speed USB 2.0 interface.
Connect the USB port of the computer to port X5 using
a USB cable (see "Items supplied", page 21).
For information on the location of the connections, see
"Rear panel", page 23.
For pin layout of X5, see "Q".
4.6 Connecting an external device
An external device with a 6-pin mini-DIN connection can be
connected to port X3.
Use a standard cable with a 6-pin mini-DIN connector to
connect the mini-DIN connection of the external device
to port X3.
For information on the location of the connections, see
"Front panel", page 23.
For pin layout of X3, see "O".
5 Operation
WARNING
Danger of damage to the machine or personal injury
when changing the encoder voltages during operation or
with unsecured vertical axes.
Do not change any parameters or encoder voltages
at the device while the machine tool is moving and a
PWM is connected to the control loop!
Always secure vertical axes to prevent them from
falling down before measurements are performed on
these axes!
CAUTION
Danger of damage to the machine or personal injury
when memory areas are not adapted.
Some interfaces, e.g. EnDat, offer the possibility
of storing machine- or system-specific data in the
customer's memory area. The data may comprise safety-
relevant information.
If servicing becomes necessary, ensure that the
memory areas with machine- or system-specific data
are adapted.
5.1 Switch-on / Switch-off Switch-on
For information on the location of the power switch, see
"Rear panel", page 23
Set the power switch to the
I
position.
Switch-off
Set the power switch to the
0
position.
The power switch is protected by all-pole fusing.
To disconnect the unit completely from power,
the power connector must be disengaged.
Оглавление
- 1 Zu dieser Anleitung
- 2 Sicherheit
- 3 Montage
- 4 Installation
- 5 Bedienung
- 6 Wartung
- 7 Demontage, Umweltschutz undEntsorgung
- 8 Technische Daten
- 1 About these instructions
- 2 Safety
- 3 Mounting
- 4 Installation
- 5 Operation
- 6 Maintenance
- 7 Removal, environmental protectionand disposal
- 8 Specifications
- 1 A propos de cette notice
- 2 Sécurité
- 3 Montage
- 4 Installation
- 5 Utilisation
- 6 Maintenance
- 8 Caractéristiques techniques
- 1 Informazioni contenute nel presentemanuale
- 2 Sicurezza
- 3 Montaggio
- 4 Installazione
- 5 Funzionamento
- 6 Manutenzione
- 8 Dati tecnici
- 1 Acerca de este manual
- 2 Seguridad
- 3 Montaje
- 4 Instalación
- 5 Manejo
- 6 Mantenimiento
- 8 Características técnicas
- 1 Om denna manual
- 2 Säkerhet
- 3 Montage
- 4 Installation
- 5 Handhavande
- 6 Underhåll
- 7 Demontering, miljöskydd ochavfallshantering
- 8 Tekniska data
- 1 Over deze handleiding
- 2 Veiligheid
- 3 Montage
- 4 Installatie
- 5 Bediening
- 6 Onderhoud
- 7 Demontage, milieubescherming enafvoer
- 8 Technische gegevens
- 1 O tomto návodu
- 2 Bezpečnost
- 3 Montáž
- 4 Instalace
- 5 Ovládání
- 6 Údržba
- 7 Demontáž, životní prostředí alikvidace
- 8 Technické parametry
- 1 この説明書について
- 2 安全
- 3 組立て
- 4 設置
- 5 操作
- 6 メンテナンス
- 7 解体、環境保護および廃棄
- 8 技術仕様
- 1 О настоящей инструкции
- 2 Безопасность
- 3 Монтаж
- 4 Установка
- 5 Эксплуатация
- 6 Техобслуживание
- 8 Технические характеристики
- 1 关于这些说明
- 2 安全
- 3 安装
- 4 系统安装
- 5 操作
- 6 维护
- 8 技术参数
- 1 關於這些手冊
- 2 安全
- 3 安裝
- 4 安裝
- 5 操作
- 6 保養
- 8 規格
- 1 본 지침 정보
- 2 안전
- 3 장착
- 4 설치
- 5 작업
- 6 유지관리
- 7 제거, 환경 보호 및 처리
- 8 사양
- *I_1125089-90*