Rothenberger ROWELD P160-630B Plus Professional – страница 2
Инструкция к Rothenberger ROWELD P160-630B Plus Professional

3.2.2 Welding preparations
Pipes smaller than the maximum welding range (diameter) of the machine, mount the
adapter clamping inserts suited for the pipe diameter with the Allen screws found in the
accessories kit.
ROWELD P200B: Ø63-140mm: consisting of six wide-surface shells and two small-surface
shells. Ø160-180mm: consisting of 8 wide-surface shells.
ROWELD P160-355/5-12B: consisting of six wide-surface shells and two small-surface shells.
ROWELD P500-630/18-24B Plus: consisting of six wide-surface shells and two small-surface
shells (for diameters up to 450 mm) or 8 wide-surface shells (for diameters >500 mm).
In so doing, please observe that the small-surface shells are mounted to the two lower
external main clamps. These are used in the left basic clamping element below and above
only for pipe to pipe bend connections.
Insert the plastic pipe or fitting in the clamping device (use dolly with longer pipe < 2,5m
sections) and tighten brass nut on the upper clamps. Adjust brass nuts (tighten or loosen) to
compensate for any ovalness.
For P200B:
The machine is operated with 4 basic clamping jaws in the case of
pipes / pipe connections
(welding position A).
The 4th basic clamping jaw can be removed in the case of narrow
pipes / fitting connections (welding position B). To do this,
initially remove the screws (3) and then slightly loosen the screws
(5). The 4th jaw can now be pulled out together with the sub-
construction. Finally, unscrew the spacers (4) and replace them by
the screws (3).
For pipe-to-pipe connections, the two spacers must be
engaged in both left clamping elements (standard
configuration at delivery).
Attention: Under no circumstances should the spacers be
installed diagonally offset!
The pipes are each held by two clamping elements.
Pipe / Fitting P160/5B:
For pipe-to-fitting connections, the two spacers must be
engaged in both middle clamping elements.
Attention: Under no circumstances should the spacers be
installed diagonally offset!
The pipe is inserted into three clamping elements, and the fitting is held by one
clamping element. Thus, the movable clamping element can be shifted on the rod as space
requirements demand during clamping.
Pipe / Fitting P250-355/8-12B:
For pipe-to-fitting connections, the two spacers must be
engaged in both middle clamping elements, and the heating
element take-off device is suspended into the left clamping
elements.
Attention: Under no circumstances should the spacers be installed diagonally offset!
The pipe is inserted into three clamping elements, and the fitting is held by one clamping
element. Thus, the movable clamping element can be shifted on the rod as space
requirements demand during clamping.
ENGLISH 19
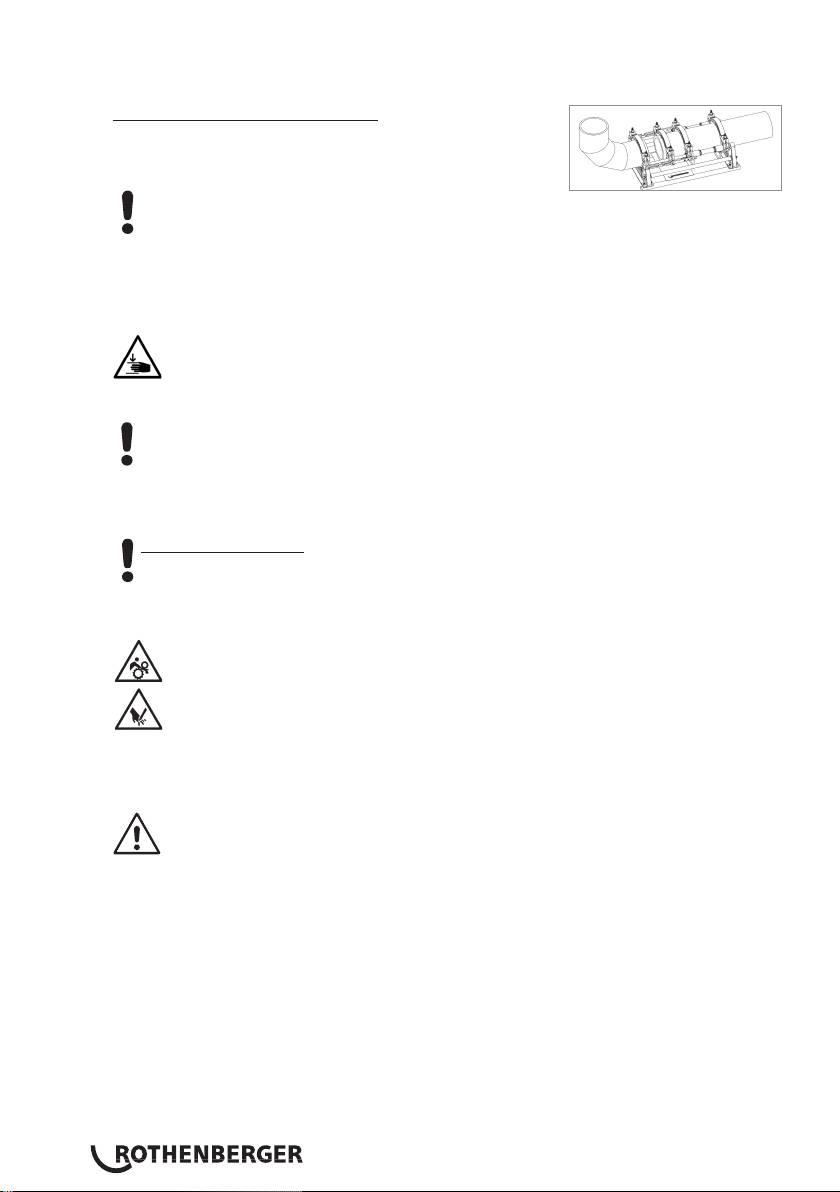
When some fittings are being processed in certain positions, such as horizontal bends or
welding necks, it is necessary to remove the heating element take-off device.
Pipe / Fitting P500-630/18-24B Plus:
For pipe-to-fitting connections, the spacers must be swivelled
to the other side and engaged in the middle clamping
elements.
Attention: Under no circumstances should the spacers be
installed diagonally offset!
The pipe is inserted into three clamping elements, and the fitting is held by one clamping
element. Thus, the movable clamping element can be shifted on the rod as space
requirements demand during clamping.
Verify secure fit by moving the workpieces together.
Stay a safe distance away from the machine. Do not stand or reach into the
machine. Keep other people away from the work area.
Check to ensure that the heating plate has reached the setpoint operating temperature.
CAUTION!!! To guarantee uniform heat distribution over the entire heating element,
the heating element must not be used until at least 10 minutes after it reaches the
target temperature. Check and verify the temperature with a temperature meter and
readjust if necessary!
Position the electrical trimmer between the two workpieces.
P500-630/18-24B Plus: Verify the direction of rotation! The machines were polarised
to turn clockwise before leaving our factory!
Switch on trimmer unit. The planing discs should turn in the cutting direction; if not, use
suitable tools to change over the phase inverter in the mains plug.
Risk of serious injury! During operation trimmer unit, stay a safe distance away
from the machine, and do not reach into the rotating knife. Use trimmer in
working position only and return it into the designated carrying frame
immediately after use. Ensure that the safety switch functions properly at all
times to avoid any accidental starting of the trimmer away from the basic
machine.
Turn the pressure adjustment valve counter-clockwise all the way.
Press the control lever leftward and slowly increase the milling pressure to the optimal value.
An excessively high milling pressure can lead to overheating and damage to the
miller drive. When the milling drive is overloaded or at rest, raise the machine
and reduce the pressure.
Once shavings with a thickness of < = 0.2mm are steadily exiting the milling machine, press
the control lever rightward and guide the machine apart.
Turn off the milling equipment, and wait for the planing disks to stop. Remove the milling
equipment from the basic machine, and place it in the storage case.
Bring the work pieces together, and let up on the pressure by opening the pressure release
valve.
Check to see that the welding surfaces are flat, parallel and axially aligned.
Should the joint surfaces show any misalignment, repeat the trimming procedure. For
best results the workpiece ends should not be mismatched by more than 10% of the wall
thickness and the maximum gap between the joint surfaces no more than 0.5 mm. This
recommendation does not release you from your obligation to observe national welding
guidelines. Clear away any remaining shavings with a clean brush.
ENGLISH20
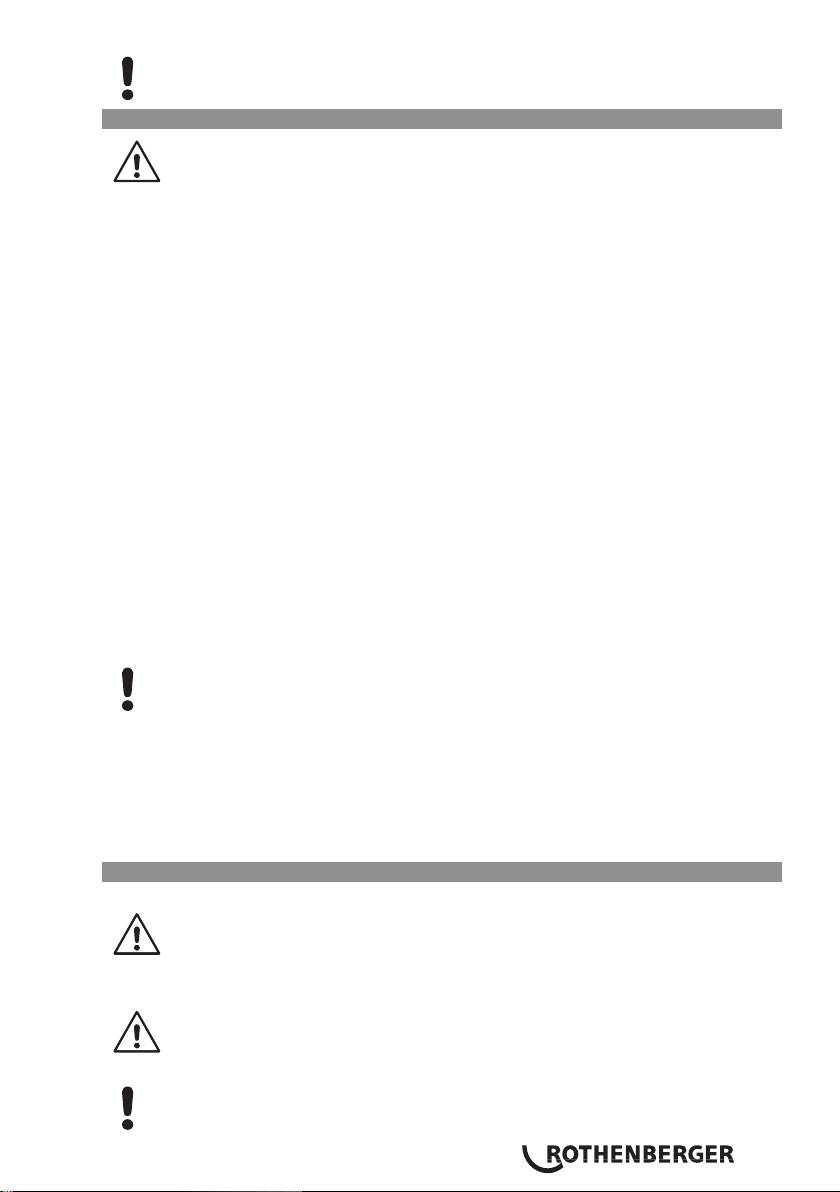
CAUTION! Do not touch the trimmed, ready to weld surfaces. Ensure that the surfaces are
free of any and all containments and foreign objects!
3.2.3 Welding
Risk of injury! Keep a safe distance from the machine when mechanically closing
clamps and moving workpieces. Keep hands, limbs and objects such as clothing,
tools etc. away from running machine!
While moving workpiece ends to welding position, read the workpiece drag pressure from the
manometer on the hydraulic unit.
The workpiece drag pressure is the minimum amount of pressure required to set the work-
piece – depending on weight and length – in axial motion. This value must be precisely de-
termined; it will be necessary to engage and disengage the machine and workpieces several
times and to set the pressure adjustment valve until the machine almost comes to a standstill.
Add the drag pressure to the conformation, heat-penetration and joint pressure.
Insert the heating plate into the basic unit between the two workpiece ends and make sure
that the heating plate’s supports are seated in the notches on the take-off device.
Engage the machine, set and maintain the required conformation pressure plus drag pressure.
As soon as sufficient bead has formed around the entire circumference of the workpiece
ends, slowly release the pressure by slowly opening the relief valve.
Set the pressure so that workpiece ends have uniform almost pressureless contact to the
heating plate (warm up).
Now close the relief valve. Ensure that the workpiece ends still have contact with the heating
plate.
After the warm-up phase, disengage workpieces, remove the heating plate and re-engage
the workpieces. Increase the pressure linear to the respective joint pressure and maintain that
pressure until the joint is fully cooled.
Regularly check the pressure and pump it back up when necessary. If the pressure loss is
excessive, have the hydraulic system checked.
CAUTION: Press and hold the control lever for the first 20 to 100 seconds then release
(neutral switch position).
Put the heating element back into the storage case.
After the joint has fully cooled, slowly release the pressure by opening the relief valve,
unclamp the workpieces and remove from the machine.
Disengage the basic unit, write protocol. The machine is now ready for the next welding
cycle.
All welding parameters can be found in the enclosed welding tables.
3.2.4 Putting out of operation
Switch off heating plate.
Let the heating element cool or stow it in such a way that no adjacent materials
can be ignited!
Remove trimmer unit, heating plate and hydraulic unit mains plugs from power outlet and roll
up cables.
Transport and set the hydraulic unit only in a horizontal position. If it is set at an
angle, oil escapes from the vented plugs with the dipstick!
Disconnect and roll up hydraulic hoses.
Important! Protect couplings from damage and dirt!
ENGLISH 21
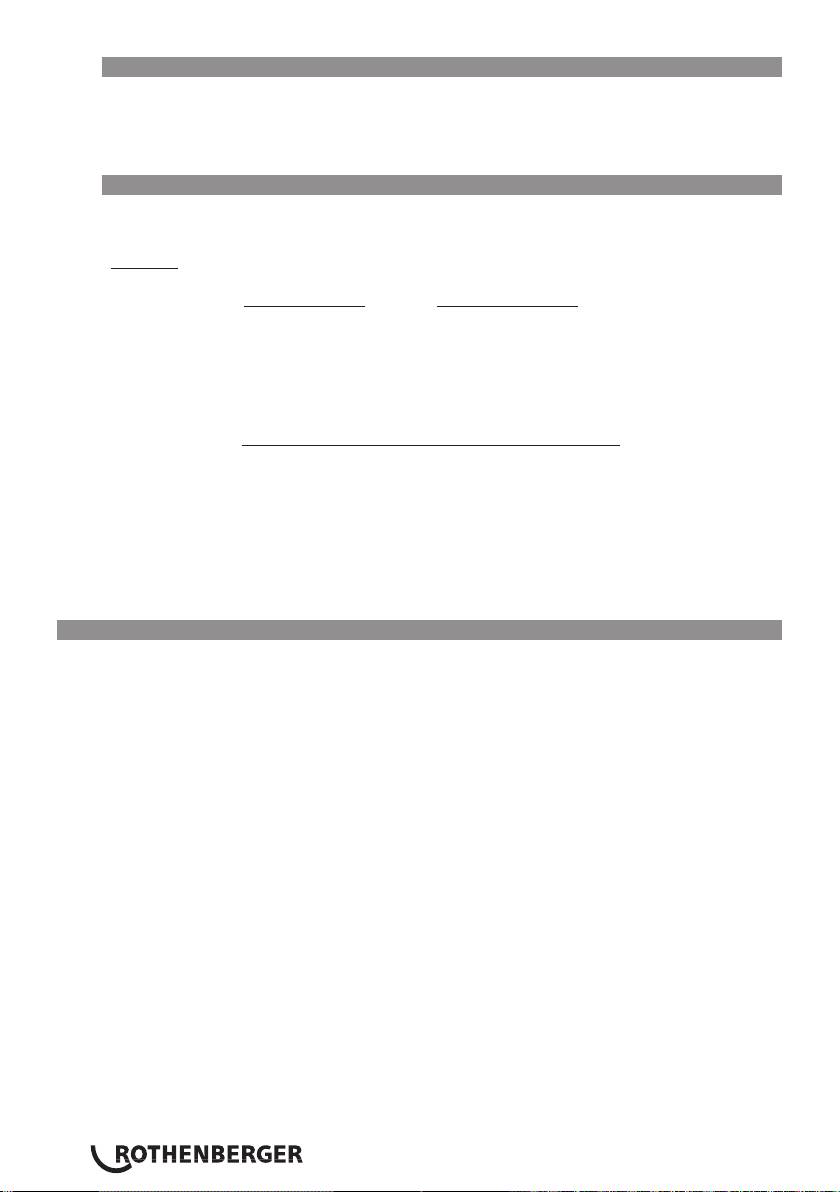
3.3 General requirements
As weather and ambient conditions can seriously effect welding procedures and joints, it is
essential to duly observe national welding guidelines and ordinances, e. g. DVS Guideline 2207,
Sections 1, 11 and 15.
(Welding requires continuous and due supervision and monitoring!)
3.4 Important information on welding parameters
For welding parameters such as temperature, pressure and time, consult your national welding
guidelines and ordinances, e. g. DVS Guideline 2207, Sections 1, 11 and 15.
Ordering: DVS Media GmbH, Aachener Str. 172, 40223 Düsseldorf
Postfach 10 19 65, 40010 Düsseldorf, Tel.: +49 (0) 211 / 15 91 – 0
Email: media@dvs-hg.de internet: www.dvs-media.info
In the event of doubt, consult the pipe manufacturer for material-specific welding parameters.
The welding parameters specified in the welding tables are strictly reference values.
ROTHENBERGER cannot assume any liability for their accuracy or completeness!
The compensation and joint pressure values specified in the welding tables were calculated using
the following formula:
pressure P [bar] = welding surface A [mm²] x welding factor SF [N/mm²]
surface of cylinder Az [cm²] x 10
Welding factors (SF): PE = 0,15 N/mm², PP = 0,10 N/mm², PVDF = 0,10 N/mm²
(ROWELD P 160/5 B: the total cylinder surface is 3.53 cm²)
(ROWELD P 200 B: the total cylinder surface is 3.53 cm²)
(ROWELD P 250/8 B: the total cylinder surface is 6.26 cm²)
(ROWELD P 355/12 B: the total cylinder surface is 6.26 cm²)
(ROWELD P 500/18 B and P 630/24 B: the total cylinder surface is 14.13 cm²)
(ROWELD P 630/24 B Plus: the total cylinder surface is 22.38 cm²)
4 Care and maintenance
To ensure that the welding machine functions properly, observe the following maintenance
recommendations:
• The guide rods must be kept free of dirt and grime. Replace guide rods whenever surface
shows signs of erosion or damage, otherwise hydraulic system may loose pressure.
• Trimmer unit, heating plate, hydraulic unit may only be supplied with the voltage specified on
the type plates.
• To achieve perfect welding results, it is essential to keep the heating plate clean. If the surface
is damaged or shows signs of erosion, the surface must be recoated or replaced. Material
residues on the heating plate surface reduces the non-sticking properties of the coating.
Remove all residues with non-linting paper and alcohol (heating plate must be cool!).
• Before every start-up, check the oil level of the hydraulic unit (oil level should lie between full
and empty marks). Replenish hydraulic oil whenever necessary (HLP – 46, no.: 53649).
• Change hydraulic oil (HLP – 46, no.: 53649) every six months.
• To avoid malfunctions, regularly check the hydraulic unit for leaks, proper fit of connections
as well as the power cable for signs of damage or wear.
• Protect the fast-on couplings on both the hydraulic unit as well as the hydraulic hoses from
dirt and grime. Remove any dirt or foreign objects prior to connecting.
• The trimmer unit is equipped with two bi-directional blades. Rotate or replace blades
whenever trimming performance is no longer up to expectations.
• Always ensure that the pipe and workpiece ends, in particular the butt surfaces are clean.
Dirt or other foreign substances will shorten the serviceable life of the blades considerably
ENGLISH22
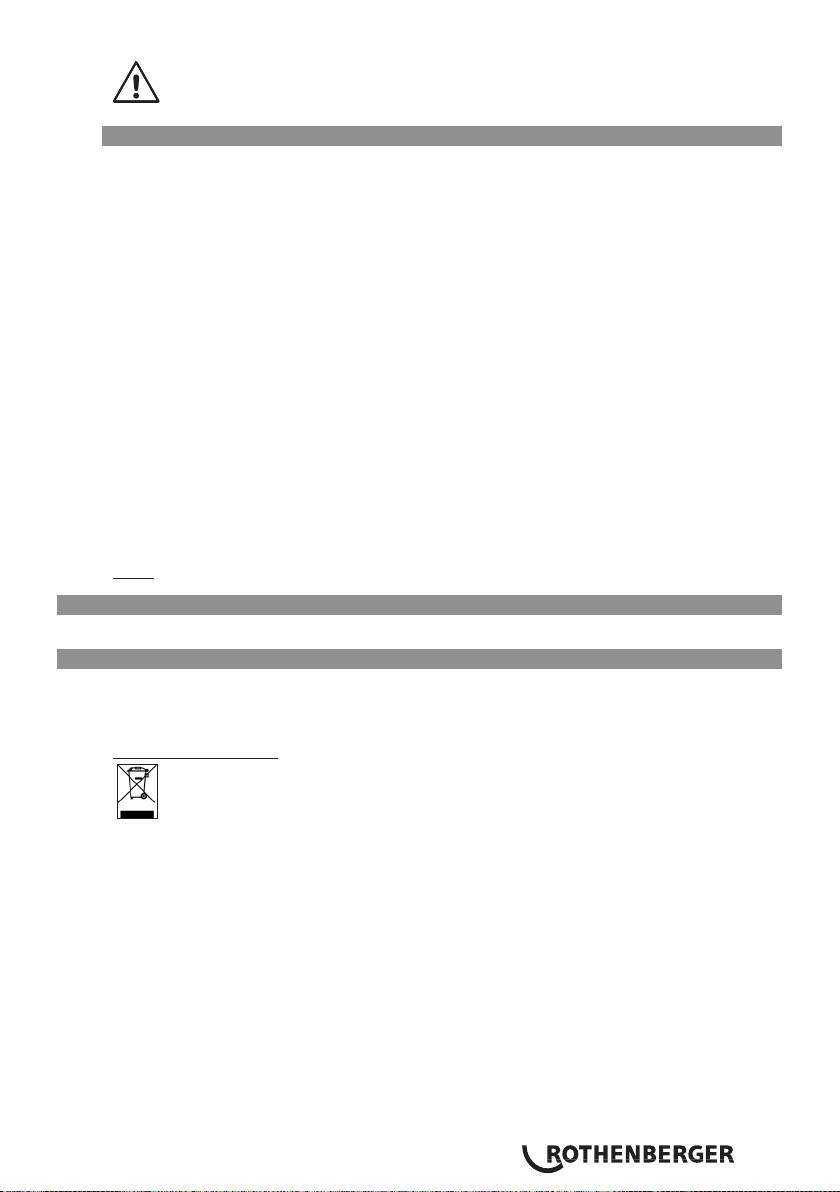
Pursuant to welding guidelines the welding machine must be inspected annually
by the manufacturer or an authorised service workshop. Machines subjected to
above average use or strain should be inspected at shorter intervals.
4.1 Machine and tool care
(Follow the maintenance instructions in item 4!)
Sharp and clean tools produce better work results and are safer.
Replace blunt, broken or lost parts immediately. Check whether the accessories are securely
connected to the machine.
Use only original spare parts from the manufacturer for maintenance work. Repairs must be
carried out only by professionally qualified personnel.
Disconnect the machine from the mains when it is not in use, prior to care and maintenance
work and before changing accessory parts.
Prior to reconnection to the mains, it must be ensured that the machine and the accessory tools
are switched off.
When extension cables are used, they must be checked for their safety and operativeness. Only
cables approved for outdoor use must be used.
Tools and machines whose housing or handles, especially those made of plastic, are cracked or
warped must not be used.
Dirt and moisture in such cracks conduct electric current. This can lead to an electric shock if the
insulation is damaged in the tools or in the machine.
Note: Furthermore, we refer to the accident prevention regulations.
5 Accessories
The relevant accessories and an order form can be found from Page 147 onwards.
6 Disposal
Components of the unit are recyclable material and should be put to recycling. For this purpose
registered and certified recycling companies are available. For an environmentalfriendly disposal of
the non-recyclable parts (e.g. electronic waste) please contact your local waste disposal authority.
For EU countries only:
Do not dispose of electric tools with domestic waste. In accordance with European
Directive 2012/19/EC on waste electrical and electronic equipment and its implementation
as national law, electric tools that are no longer serviceable must be collected separately
and utilised for environmentally compatible recycling.
ENGLISH 23
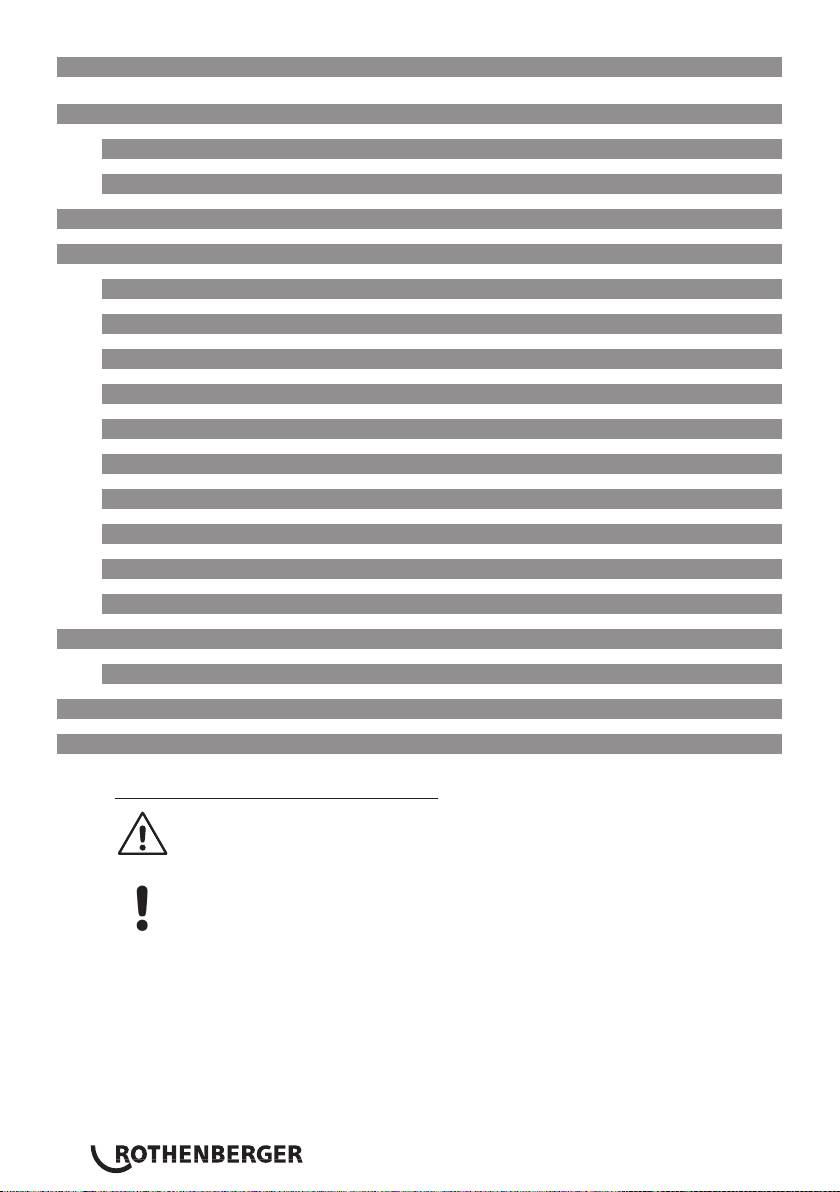
Table des matières Page
1 Consignes de sécurité 25
1.1 Utilisation conforme aux dispositions 25
1.2 Consignes générales de sécurité 25
2 Données techniques, voir livret „données techniques“
3 Fonctionnement de l’appareil 27
3.1 Description de l’appareil 27
3.1.1 Machine de base (fig. A) 27
3.1.2 Unité hydraulique (fig. B) 27
3.2 Mode d’emploi 28
3.2.1 Mise en service 28
3.2.2 Mesures de préparation du soudage 30
3.2.3 Soudage 32
3.2.4 Mise hors service 32
3.3 Exigences générales 33
3.4 Remarques importantes concernant les paramètres de soudage 33
4 Entretien et maintenance 33
4.1 Entretien de la machine et des outils 34
5 Accessoires 34
6 Elimination des déchets 34
Pictogrammes contenus dans ce document:
Danger!
Ce pictogramme signale un risque de blessure pour les personnes.
Attention!
Ce pictogramme signale un risque de dommage matériel ou de préjudice
pour l’environnement.
Nécessité d’exécuter une action
FRANÇAIS24
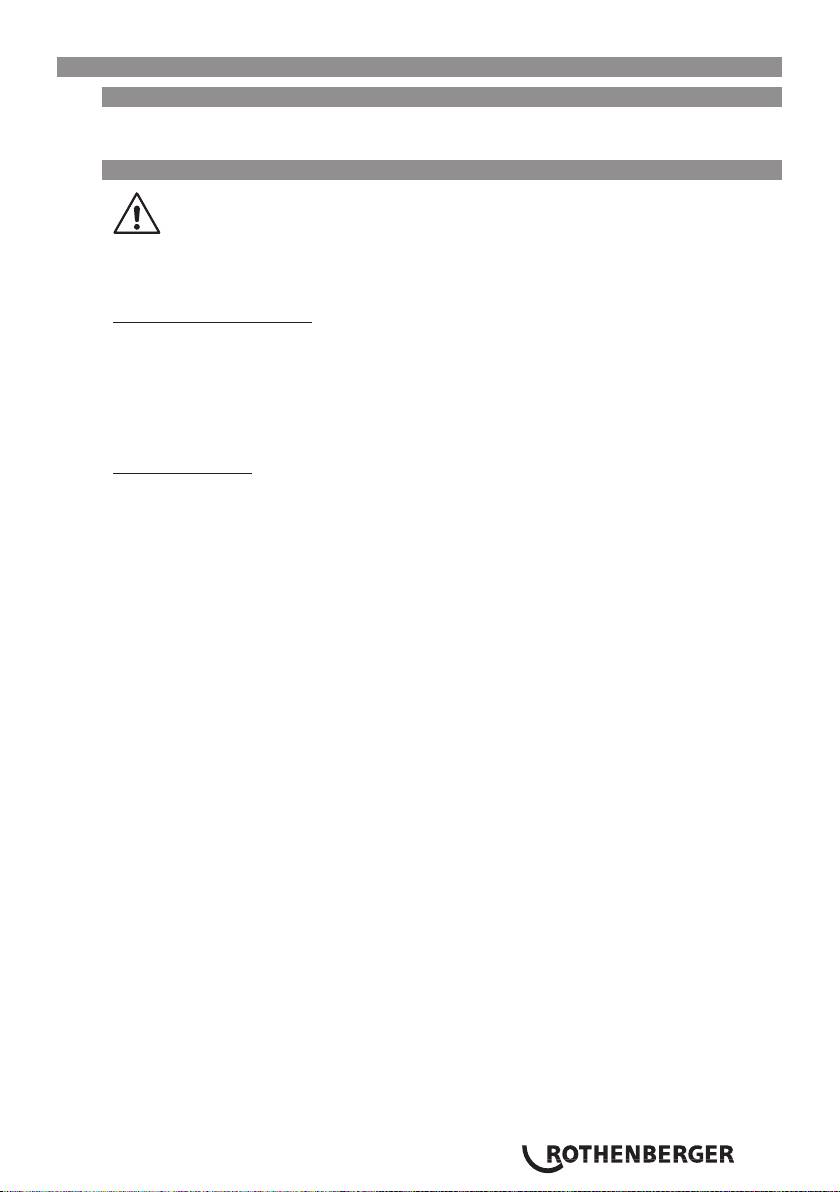
1 Consignes de sécurité
1.1 Utilisation conforme aux dispositions
Les ROWELD P160-630/5-24B Plus Professional sont spécialement conçues pour effectuer les
soudures des tuyaux en PE - PP et PVDF selon les données techniques.
1.2 Consignes générales de sécurité
ATTENTION ! Veuillez observer les mesures de sécurité suivantes afin d’éviter les
électrocutions et les dangers de blessures ou d’incendies pendant l’utilisation des outils
électriques.
Veuillez lire ces consignes avant d’utiliser cet outil électrique et conservez-les
soigneusement.
Entretien et maintenance :
1 Nettoyage, entretien et graissage réguliers. Débranchez avant tous les réglages, les
travaux de maintenance ou les réparations.
2 Confiez la réparation de votre appareil uniquement à des personnes qualifiées
utilisant des pièces de rechange d’origine Ceci permet de garantir la sécurité de l’appareil
à long terme.
Travaux sécurisés :
1 Maintenez l’espace de travail en ordre. Le désordre dans l’espace de travail peut
provoquer des accidents.
2 Tenez compte des influences de l’environnement. N’exposez pas votre outil électrique
à la pluie. N’utilisez pas votre outil électrique dans un environnement humide ou mouillé.
Assurez un bon éclairage à votre espace de travail. N’utilisez pas votre outil électrique à des
endroits soumis à des risques d’incendie ou d’explosion.
3 Protégez-vous d’une électrocution. Évitez les contacts corporels avec des parties mises à
terre (par. ex. tubes, radiateurs, cuisinières électriques, appareils de refroidissement).
4 Ne laissez pas d’autres personnes s’approcher. Interdisez à d’autres personnes, aux
enfants en particulier, de toucher l’outil électrique ou le câble. Maintenez-les à distance de
l’espace de travail.
5 Rangez l’outil électrique inutilisé dans un endroit protégé. Les outils électriques
inutilisés doivent être déposés dans un endroit sec, surélevé et fermé, hors de portée des
enfants.
6 Ne surchargez pas votre outil électrique. Le travail est plus sûr et plus facile dans la zone
de puissance.
7 Utilisez l’outil électrique adéquat. N’utilisez pas une machine à faible puissance pour des
travaux lourds. N’utilisez pas l’outil électrique à des fins non prévues pour lui. Par exemple,
n’utilisez pas de scie circulaire manuelle pour couper des troncs d’arbres ou des bûches.
8 Portez des vêtements adéquats. Ne portez pas de vêtements larges ou de bijoux,
ils pourraient être saisis par les pièces mobiles. Des chaussures antidérapantes sont
recommandées pour les travaux effectués en plein air. Mettez vos cheveux dans un filet.
9 Utilisez l’équipement de protection. Portez des lunettes de sécurité. Portez un masque
respiratoire pendant les travaux provoquant de la poussière.
10 Raccordez le dispositif d’aspiration. Au cas où des raccords pour les dispositifs d’aspiration
et de collection sont disponibles, vérifiez qu’ils sont bien branchés et correctement utilisés.
11 N’utilisez pas l’outil électrique à des fins non prévues pour lui. Ne tirez pas sur le
FRANÇAIS 25
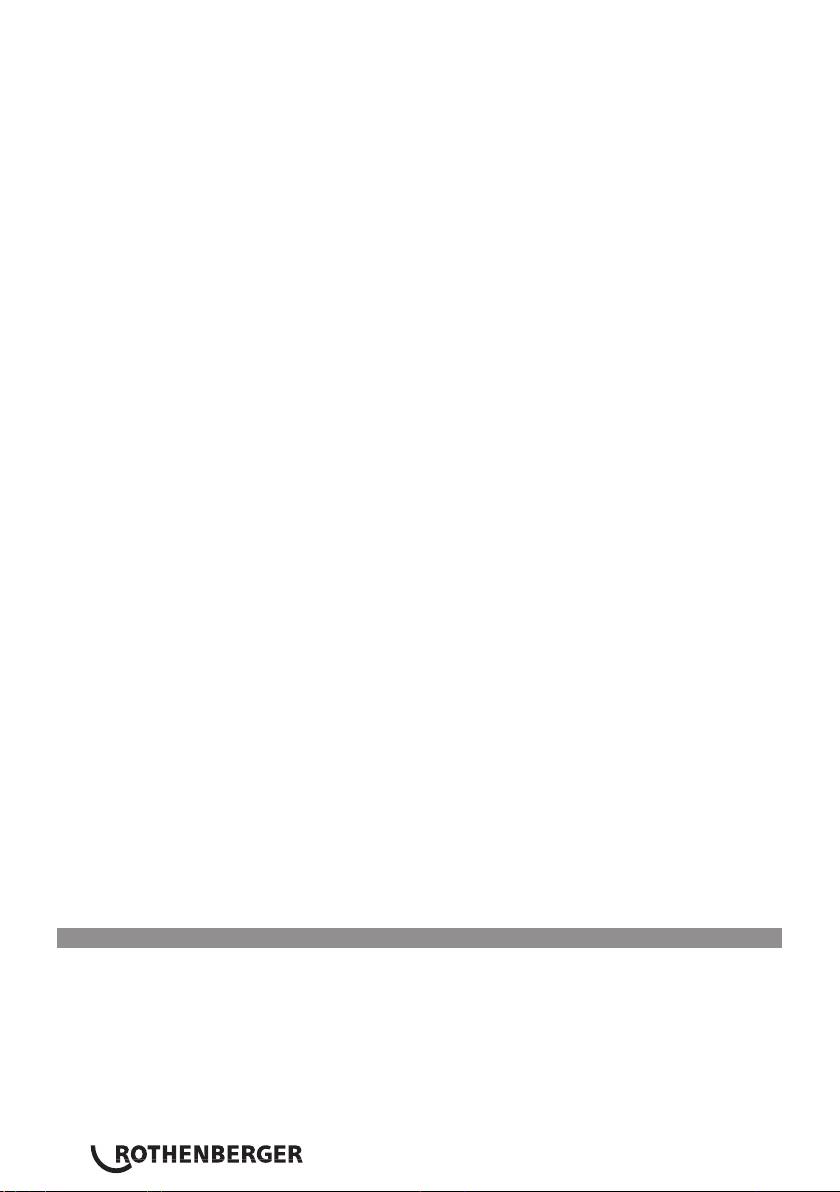
câble pour débrancher l’appareil. Protégez le câble de la chaleur, de l’huile et des arêtes
tranchantes.
12 Assurez la pièce usinée. Utilisez le dispositif de tension ou un étau à vis afin de maintenir la
pièce usinée. Elle est maintenue plus sûrement qu’à la main.
13 Évitez les positions corporelles anormales. Veillez à vous assurer une position sûre et
gardez toujours l’équilibre.
14 Soignez minutieusement vos outils. Maintenez les outils de coupes propres et tranchants
afin de vous faciliter le travail. Suivez les consignes pour le graissage et le changement d’outil.
Contrôlez régulièrement les conduites de raccordement des outils électriques et faites les
réparer par un professionnel agréé en cas de détérioration. Contrôlez régulièrement les
rallonges et remplacez-les en cas de détériorations. Maintenez la poignée sèche, propre et
exempte de graisse ou d’huile.
15 Retirez la fiche de la prise de courant. Lorsque vous n’utilisez pas l’outil électrique, avant
l’entretien ou lors du changement d’outils comme la scie, la perceuse, la fraise.
16 Ne laissez pas la clé d’outil à l’intérieur. Vérifiez que la clé et l’outil de réglage soient
retirés avant la mise en marche.
17 Évitez les mises en marche involontaire. Assurez-vous que l’interrupteur est éteint lorsque
vous insérez la fiche dans la prise.
18 Utilisez la rallonge lors de travaux à l’extérieur. Utilisez uniquement des rallonges
homologuées et marquées en conséquence pour les travaux à l’air libre.
19 Soyez attentif. Soyez concentré sur votre travail. Faites preuve de bon sens lorsque vous
travaillez. N’utilisez aucun outil électrique si vous n’êtes pas concentré.
20 Vérifiez le bon état de l’outil électrique. Avant de continuer à utiliser l’outil électrique,
vérifiez soigneusement les dispositifs de sécurité ou les pièces légèrement endommagées
et assurez-vous que le fonctionnement est impeccable et adéquat. Vérifiez que les parties
mobiles fonctionnent de manière impeccable et ne coincent pas ainsi que le parfait état des
pièces. Toutes les pièces doivent être montées correctement et remplir toutes les conditions
afin de garantir un fonctionnement impeccable de l’outil électrique.
Les pièces et les dispositifs de sécurité endommagés doivent être réparés ou changés par
un atelier agréé, à moins que le mode d’emploi donne d’autres consignes. Les interrupteurs
endommagés doivent être remplacés dans un atelier pour notre clientèle.
N’utilisez pas un outil électrique qui ne peut être mis en marche ou arrêté.
21 Attention. L’utilisation d’autres outils et accessoires peut provoquer des blessures.
22 Faites réparer les outils électriques par un électricien qualifié. Cet outil électrique
correspond aux dispositions de sécurités applicables. Les réparations doivent uniquement être
effectuées par un électricien qualifié et avec les pièces de rechange originales ; dans le cas
contraire, cela pourrait provoquer des accidents.
2 Données techniques, voir livret „données techniques“
FRANÇAIS26
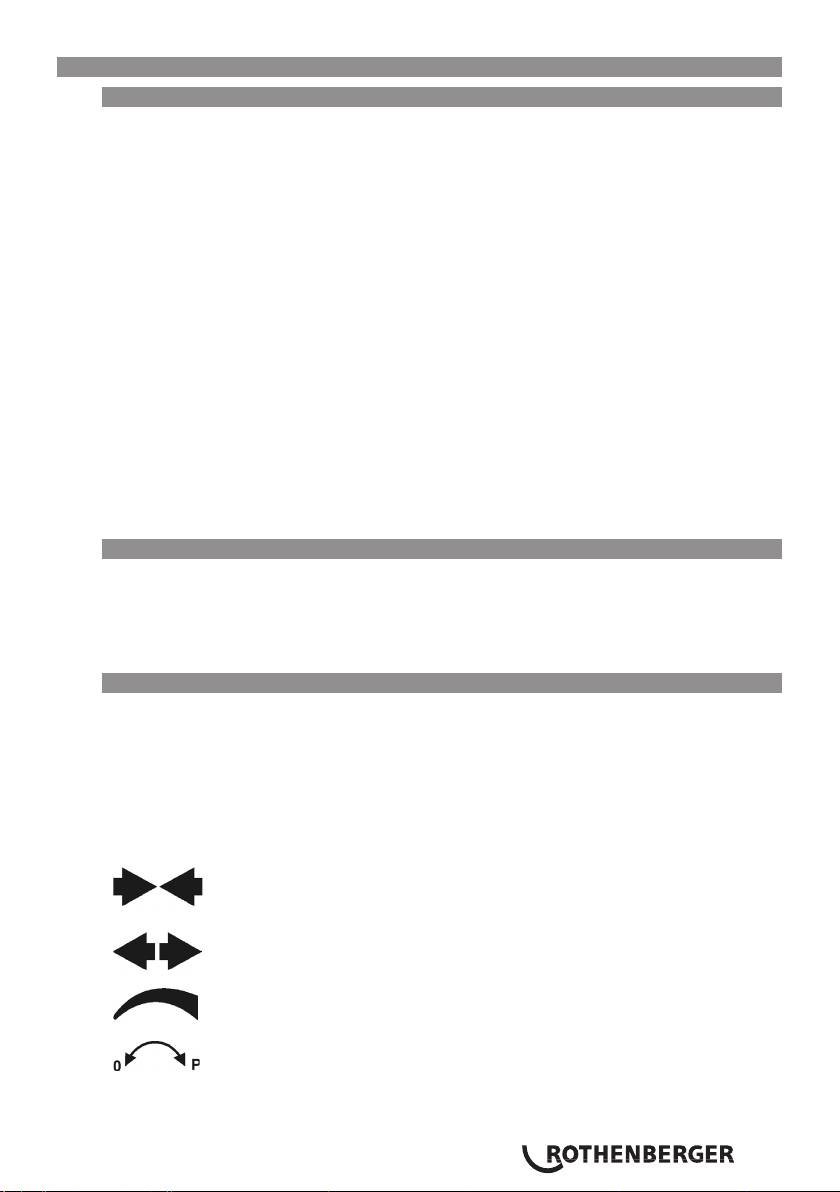
3 Fonctionnement de l’appareil
3.1 Description de l’appareil
Les ROWELD P160-630/5-24B Plus Professional sont des soudeuses bout à bout à élément
thermique compactes et transportables spécialement conçues pour l’utilisation dans le domaine
des chantiers – et ici plus spécialement dans des tranchées pour canalisations. Les machines
peuvent bien sûr également être utilisées dans des ateliers.
Les fonctions multiples des soudeuses de « type ROWELD » permettent de fabriquer de manière
sûre les joints soudés de tubes en PE, PP et en PVDF suivants avec des diamètres extérieurs de 40
à 630 mm/ 1 1/4-24“ dans tous les domaines d’utilisation :
I. tube - tube
II. tube - coude de tube
III. tube - pièce en T
IV. tube - collerette à souder
Les machines sont essentiellement composées des éléments suivants :
machine de base, jeux d’inserts de serrage de réduction, unité hydraulique, équipement de
fraisage, élément thermique, caisson de rangement.
Pour souder des collerettes à souder, la rondelle de serrage à quatre mâchoires livrable comme
accessoire doit être utilisée.
ROWELD P160-250/5-8B: Lors du soudage de tubes coudés à rayon réduit ayant le diamètre
maximal de la machine, il convient d’utiliser l’outil de serrage en biseau (partie supérieure)
disponible en tant qu’accessoire.
ROWELD P500-630/18-24B Plus: pour mettre en place et soulever la fraise et l’élément
thermique, le dispositif de soulèvement électrique livrable comme accessoire peut être utilisé.
3.1.1 Machine de base (fig. A)
1 Eléments de serrage mobiles 5 Elément de serrage amovible
2 Elément de serrage déplaçable 6 Vis de fixation supérieures
3 Pièce d’écartement avec entailles d’arrêt 7 Pièce d‘écartement
4 Dispositif d’évacuation de l’élément thermique 8 Vis de fixation inférieures
3.1.2 Unité hydraulique (fig. B)
1 Tubulure de remplissage d’huile et jauge 5 Câble de réseau
2 Raccord express connecteur 6 Manomètre
3 Soupape de décharge 7 Levier de commande, gauche-
rapprochement, droit-éloignement
4 Raccord express manchon 8 Soupape de reglage de pression
L’unité hydraulique permet d’activer les fonctions de la soudeuse désignées par les symboles
suivants :
Pour la jonction des éléments de serrage pousser le levier de commande vers la
gauche. La vitesse d‘avance et de montée en pression dépend de l‘angle
d‘orientation
Pour écarter les éléments de serrage pousser le levier de commande vers la droite.
La vitesse d‘avance dépend de l‘angle d‘orientation
Valve de réglage de pression pour le fraisage, l’ajustement, le préchauffage et le
soudage. Affichage de la pression sur le manomètre
Détendeur. Pour délester tourner à gauche. La vitesse de délestage de la pression
dépend du nombre de tours. Tourner vers la droite - maintien de la pression
FRANÇAIS 27
OIL
Bouchon fileté de la tubulure de remplissage d’huile avec jauge d’huile

3.2 Mode d’emploi
La soudeuse doit uniquement être utilisée par des spécialistes qualifiés et ayant reçu
les instructions correspondantes, conformément à la directive de contrôle DVS 2212,
ère
1
partie!
Seules des personnes formées à cet effet et autorisées peuvent utiliser la machine !
3.2.1 Mise en service
Veuillez lire attentivement le mode d’emploi et les remarques concernant la
sécurité avant la mise en service de la soudeuse bout à bout !
Ne pas utiliser pas l‘élément thermique en atmosphère explosible et ne pas le
faire entrer en contact avec des substances facilement inflammables.
Garder une bonne distance de sécurité par rapport à la machine. Ne pas se placer
pas dans celle-ci et ne pas y mettre les mains. Tenir les autres personnes à distance
de la zone de travail.
Contrôler le niveau d’huile du groupe hydraulique avant chaque mise en service.
Il doit se situer entre les marques min.et max. du bouchon de remplissage muni
d’une jauge. Le cas échéant, faire l’appoint d’huile HLP 46.
Le groupe hydraulique doit être transporté et stocké à la verticale. Lorsqu’il est
positionné en biais, de l’huile s’échappe au niveau du bouchon de ventilation
muni d’une jauge.
Relier la machine de base et l’unité hydraulique à l’aide des deux flexibles hydrauliques.
Protéger les raccords rapides des salissures. Les raccords présentant des défauts
d’étanchéité doivent être remplacés immédiatement!
Raccorder les fiches de secteur de l’équipement de fraisage, de l’unité hydraulique et de
l’élément thermique à l’alimentation en courant conformément aux indications données sur la
plaque signalétique.
Pour P160-250/5-8B:
La diode rouge „Veille“ est allumée, c-à-d : L‘appareil est sous tension. A l‘aide du gros
interrupteur poussoir (allumé vert), allumer l‘élément de chauffe et régler la température
voulue (160°C à 285°C) avec le bouton „+“ ou „-“.
La mise en chauffe de l‘élément de chauffe est indiquée par une diode jaune sur l‘élément de
chauffe. Des barres horizontales apparaissent également sur l‘indicateur de température. Peu
avant que la température définie soit atteinte, (tolérance +/-3°C) la diode jaune s‘éteint et la
verte s‘allume. Après 10 minutes, l‘élément de chauffe est prêt à l‘emploi. La température est
contrôlée à l‘aide d‘un thermomètre.
Réglage du Off-set: Appuyer simultanément sur les touches „+“ ou „-“. L‘élément de chauffe
peut ensuite être calibré à l‘aide d‘une de ces touches et d‘un thermomètre extérieur.
Si l‘élément de chauffe indique une valeur plus petite que celle du thermomètre extérieur,
la différence doit être réglée à l‘aide de la touche „+“. Dans le cas contraire, la différence
est réglée à l‘aide de la touche „-“. Si „Er1“ est affiché, cela indique une défaillance
électronique. Si c‘est „Er2“, cela indique que le thermomètre à résistance est défectueux ou
non raccordé.
Risque de brûlure ! L’élément thermique peut atteindre une température de 290°C
et doit être replacé dans le caisson de rangement prévu à cette effet
immédiatement après son utilisation!
Pour P355/12B:
Mettre en marche l‘interrupteur principal du boîtier de commandes, l‘interrupteur s‘éclaire
en vert et la température effective de la plaque chauffante s‘affiche sur l‘écran. Régler la
température désirée entre 160 et 270 °C à l‘aide des touches - et +.
Lorsque la température préréglée est atteinte, l’affichage passe de « set » à « actual » et
FRANÇAIS28
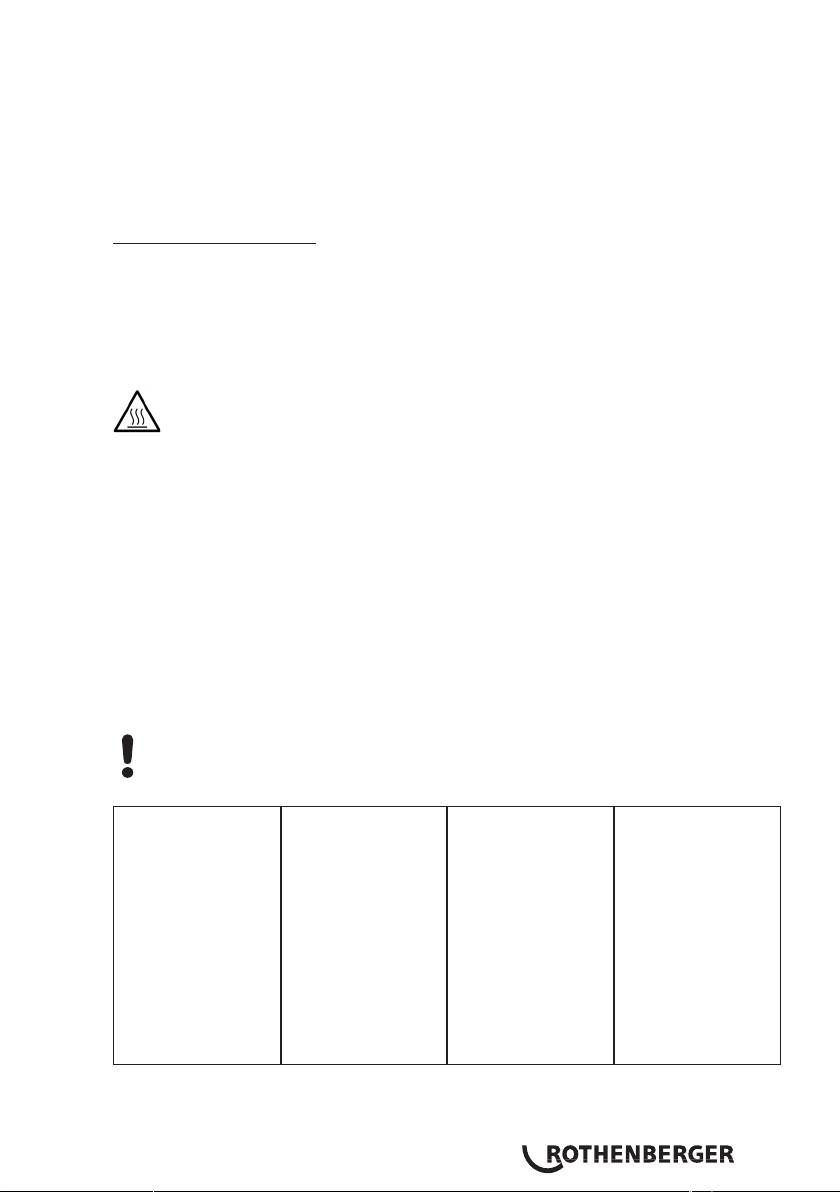
l’affichage « heat » clignote. L’élément de chauffe est prêt à l’emploi après 10 minutes
supplémentaires. Contrôlez la température avec un instrument de mesure thermométrique.
Par défaut, le régulateur de température est réglé de façon optimale ; il est possible
d’effectuer un offset si la température de surface effective de l’élément de chauffe ne
correspond pas à la valeur affichée. À cet effet, placez l’interrupteur basculant sur 0,
appuyez sur les touches – et + et mettre en marche l’interrupteur basculant. « OFF », « SET »
s’affichent sur l’écran puis la valeur Offset préréglée. Réglez l’Offset avec la touche - et +
correspondante et sauvegarder en appuyant sur - et +, ensuite la valeur effective s’affiche à
nouveau.
Pour P500-630/18-24B Plus:
Connecter le commutateur principal de la boîte de commande/’élément thermique (le
commutateur s’allume en vert). Régler éventuellement la température souhaitée (voir
thermostat).
L’affichage dans l’unité de visualisation indique généralement la température effective.
Conformément à DVS, l’élément thermique est prêt à être utilisé 10 minutes après que la
température de consigne a été atteinte pour la première fois. La température être contrôlée
avec un thermomètre.
Risque de brûlure ! L’élément thermique peut atteindre une température de 300°C
et doit être replacé dans le caisson de rangement prévu à cette effet
immédiatement après son utilisation!
La soudeuse est équipée d’un thermostat numérique de type 400.
Le thermostat numérique est configuré et réglé de manière optimale en usine. Pour régler la
température, il suffit d’appuyer sur la touche F jusqu’à ce que l’affichage indique « _SP ».
La température de consigne peut maintenant être modifiée dans la plage de 0 à 300 °C avec les
touches à flèches.
Si aucune autre touche n’est actionnée, l’affichage indique à nouveau la température effective,
le thermostat règle automatiquement la nouvelle température choisie. Tant que la température
effective est inférieure à la température de consigne réglée, la flèche rouge (low) clignote. Si
la température effective est supérieure, la flèche rouge (high) clignote. Si la valeur de consigne
réglée correspond à la valeur effective, la barre verte s’allume. Si la température effective de la
surface de l’élément thermique ne correspond pas à la valeur effective affichée, un « offset »
peut être entré. Pour cela, maintenir la touche F enfoncée jusqu’à ce que « InP » apparaisse
sur l’unité de visualisation (env.7 s) ; relâcher la touche F. Ensuite, actionner la touche F
jusqu’à ce que « oFS » apparaisse. Adapter ensuite cette valeur en conséquence. Pour achever la
modification, actionner la touche F jusqu’à ce que la valeur effective soit à nouveau affichée
Attention ! Tous les autres paramètres ne devraient pas être modifiés!
Réglage en usine :
Menü „CFG“
Menü „InP“
Menü „Out“
Menü „PAS“
„S.tu“ 0
„Ctr“ 8
„AL.n“ 0
„Prot“ 32
„h.Pb“ 1.0
„tYP“ 16
„r.o.1“ 0
„h.lt“ 0.68
„FLt“ 0.1
„r.o.2“ 0
„h.dt“ 0.17
„FLd“ 0.5
„Ct.1“ 20
„h.P.H“ 100
„dP.S.“ 0
„Ct.2“ 20
„rst“ 0
„Lo.S“ 0
„rEL.“ 0
„P.rE“ 0
„HI.S“ 300
„SoF“ 0
„oFS“ xx
„Lb.t“ 0
„HI.A“ 0
„Lb.P“ 25
„Lo.L“ 0
„FA.P“ 0
„HI.L“ 280
Rem:
du fait de la fonction « autotuning », les indications données sous CFG peuvent diverger faiblement.
Si des pompages importants surviennent, la fonction « Autotuning » pourra être activée à l’état froid
de l’élément thermique (dans le menu CFG régler le point « S.tu » sur 2 ; la remise à zéro se fera
automatiquement).
FRANÇAIS 29
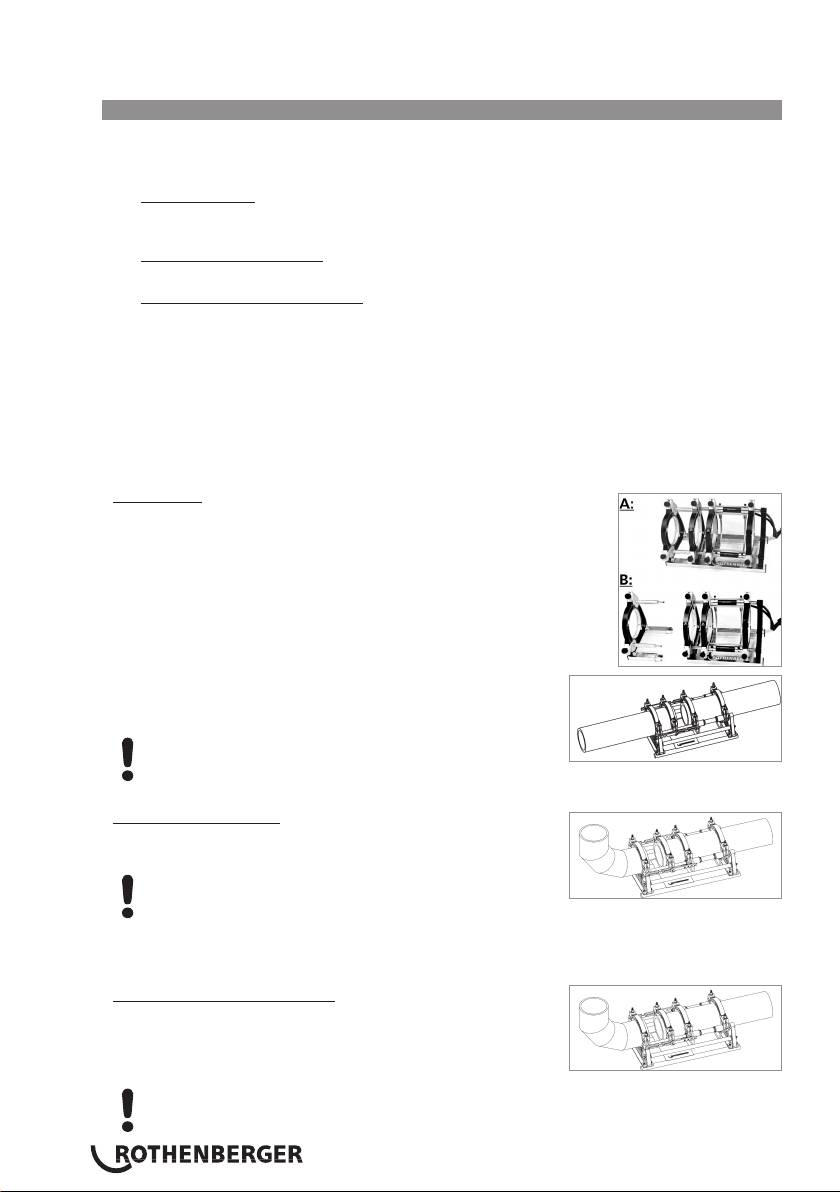
Utiliser le dispositif de levage 53410 ou 53323 (ou un autre outil adapté) pour soulever
l’équipement de fraisage et l’élément thermique.
3.2.2 Mesures de préparation du soudage
Pour les tubes plus petits que le diamètre maxi. à souder de la machine, les inserts de
réduction du diamètre de tube à usiner doivent être montés avec les boulons à six pans creux
fournis avec les accessoires.
ROWELD P200B: Ø63-140mm: respectivement composés de 6 demi-coquilles à surface
de serrage large et de 2 demi-coquilles à surface de serrage étroite. Ø160-180mm:
respectivement composés de 8 demi-coquilles à surface de serrage large à partir.
ROWELD P160-355/5-12B: respectivement composés de 6 demi-coquilles à surface de serrage
large et de 2 demi-coquilles à surface de serrage étroite
ROWELD P500-630/18-24B Plus: respectivement composés de 6 demi-coquilles à surface de
serrage large et de 2 demi-coquilles à surface de serrage étroite jusqu’à 450 mm de diamètre
et de 8 demi-coquilles à surface de serrage large à partir de 500 mm
Il faut veiller à ce que les demi-coquilles à surface de serrage étroite soient insérées dans les
deux éléments de serrage de base extérieurs. C’est uniquement dans le cas d’une liaison tube/
coude que ceux-ci sont insérés dans l’élément de serrage de base gauche en haut et en bas.
Mettre les tubes en plastique ou les raccords à souder dans le dispositif de serrage (pour les
tubes longs < 2,5m des chevalets à rouleaux doivent être utilisés) et serrer les écrous en laiton
sur les outils de serrage supérieurs. Des excentricités des tubes peuvent être compensées en
serrant ou en desserrant les écrous en laiton.
Pour P200B:
Pour les liaisons tube / tube, la machine est utilisée avec 4 mâchoires
de serrage de base
(position de soudage A).
Pour les liaisons étroites tube / raccord (position de soudage B),
il est possible d‘enlever la 4e mâchoire de serrage de base. Pour
ce faire, enlever d‘abord les vis (3) et desserrer légèrement les vis
(5). A présent, il est possible de retirer la 4e mâchoire avec sa base.
Pour finir, dévisser les pièces d‘écartement (4) et remplacer par les
vis (3).
Dans le cas de liaisons tube/tube, les entretoises doivent être
engagées dans les deux éléments de serrage situés à gauche
(état de livraison).
Attention : les entretoises ne doivent en aucun cas être
montées en étant décalées en diagonale!
Chaque tube est maintenu par deux éléments de serrage.
Tube/raccord P160/5B:
Dans le cas de liaisons tube/raccord, les entretoises doivent
être engagées dans les deux éléments de serrage médians.
Attention : les entretoises ne doivent en aucun cas être
montées en étant décalées en diagonale!
Le tube est inséré dans trois éléments de serrage et le raccord est maintenu en place par un
élément de serrage. Ce faisant, l‘élément de serrage coulissant peut être déplacé sur la barre
en fonction des besoins en espace lors du serrage et du soudage.
Tube/raccord P250-355/8-12B:
Dans le cas de liaisons tube/raccord, les entretoises doivent
être engagées dans les deux éléments de serrage médians et
le dispositif d‘évacuation de l‘élément thermique doit être
accroché dans les éléments de serrage gauche.
Attention : les entretoises ne doivent en aucun cas être montées en étant décalées
en diagonale!
FRANÇAIS30
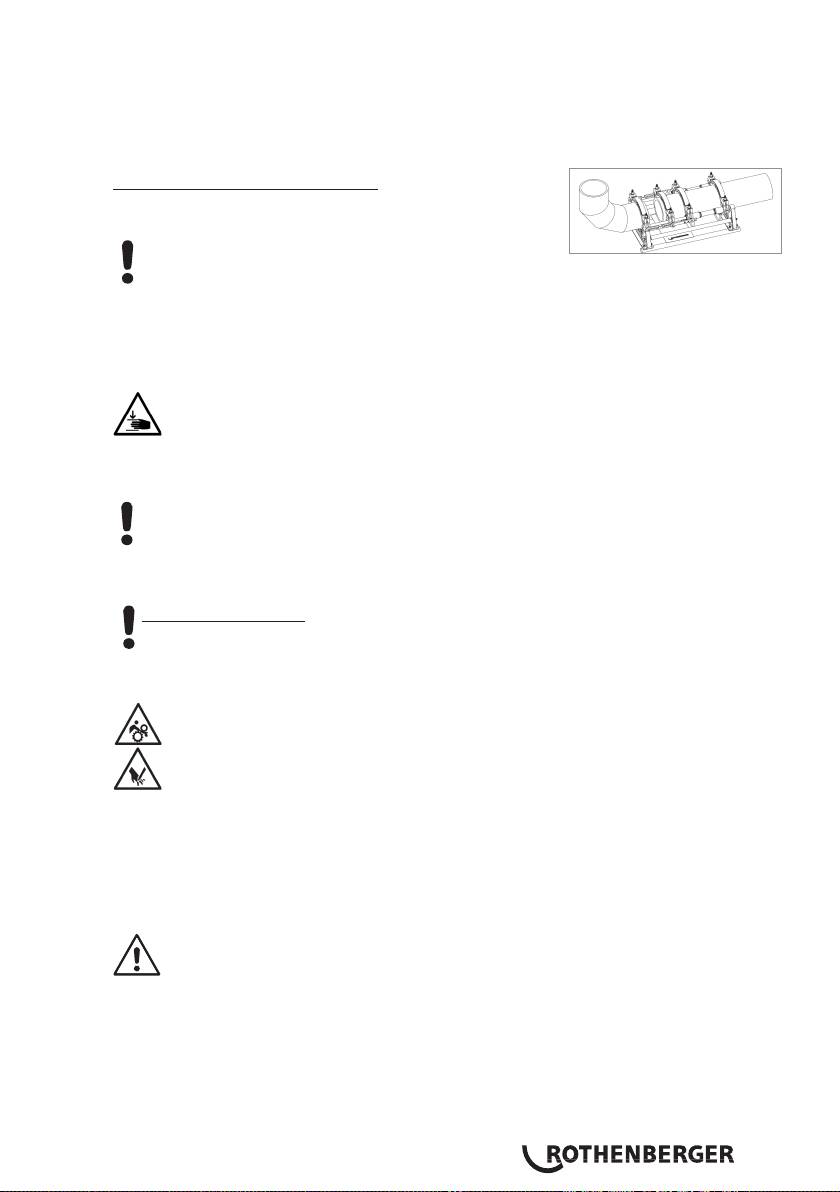
Le tube est inséré dans trois éléments de serrage et le raccord est maintenu en place par un
élément de serrage. Ce faisant, l‘élément de serrage coulissant peut être déplacé sur la barre
en fonction des besoins en espace lors du serrage et du soudage.
Lors du traitement de certains raccords dans des positions précises (p. ex. coude à
l’horizontale, collets de présoudage), il est nécessaire de retirer l’élément thermique du
dispositif d’évacuation.
Tube/raccord P500-630/18-24B Plus:
Dans le cas de liaisons tube/raccord, les entretoises doivent
être retournées et insérées dans l‘élément de serrage médian.
Attention : les entretoises ne doivent en aucun cas être
montées en étant décalées en diagonale!
Le tube est inséré dans trois éléments de serrage et le raccord est maintenu en place par un
élément de serrage. Ce faisant, l‘élément de serrage coulissant peut être déplacé sur la barre
en fonction des besoins en espace lors du serrage et du soudage.
Approcher les pièces à usiner pour contrôler si elles sont bien bloquées dans l’outil de serrage.
Garder une bonne distance de sécurité par rapport à la machine. Ne pas se placer
pas dans celle-ci et ne pas y mettre les mains. Tenir les autres personnes à distance
de la zone de travail.
Il faut également contrôler si l’élément thermique a bien atteint sa température de service.
ATTENTION!!! Afin de garantir une répartition uniforme de la chaleur dans l’ensemble de
l’élément thermique, celui-ci ne doit mis en route qu’au moins 10 minutes après avoir atteint
la température théorique. Vérifier la température à l’aide d’un thermomètre et ajuster le
réglage si nécessaire!
Placer l’équipement de fraisage électrique entre les pièces à usiner à souder.
P500-630/18-24B Plus: Contrôler les sens de rotation! En usine les machines sont
connectées aux bornes pour une rotation à droite.
Connecter l’équipement de fraisage. Les disques de rabotage doivent fonctionner dans le sens
de la coupe, sinon commuter l’inverseur de phase sur la fiche de secteur avec un outil adapté
Risque de blessure ! Garder une bonne distance de sécurité par rapport à la
l’équipement de fraisage lorsqu’elle fonctionne et ne pas mettre les mains dans
les lames rotatives. N’actionner la fraise qu’après l’avoir rentrée (position de
travail) puis la remettre dans le caisson de rangement prévu à cet effet. Le bon
fonctionnement du commutateur de sécurité dans l’équipement de fraisage doit
être garanti à tout moment, afin d’éviter un démarrage par inadvertance en
dehors de la position de travail.
Faire complètement sortir la soupape de réglage de pression en la tournant dans le sens
antihoraire.
Pousser le levier de commande vers la gauche et augmenter progressivement la pression de
fraisage jusqu‘à ce qu‘elle atteigne sa valeur optimale.
Une pression de fraisage peut engendrer la surchauffe et l’endommagement du
mécanisme de fraisage. En cas de surcharge ou d’arrêt de l’entraînement de
l’équipement de fraisage, mettre en marche la machine et réduire la pression.
Pousser le levier de commande vers la gauche et débrayer/arrêter la machine lorsque des
copeaux longs d‘une épaisseur < = à 0,2 mm sortent de manière ininterrompue de la
fraiseuse.
Arrêter l‘équipement de fraisage et attendre l‘arrêt des disques de rabotage. Retirer
l‘équipement de fraisage de la machine de base et la déposer dans la caisse de transport.
Rassembler les pièces, enlever la pression en ouvrant la soupape de décharge.
FRANÇAIS 31

Vérifier que les surfaces de soudage sont planes, parallèles et alignées dans l’axe.
Le décalage axial entre les extrémités des pièces à usiner ne doit pas (conformément à DVS )
dépasser 10 % de l’épaisseur de paroi et l’interstice maxi. entre les surfaces planes ne doit pas
être supérieur à 0,5 mm. Enlever d’éventuels copeaux dans le tube avec un outil propre (par
ex. pinceau).
Attention! Les surfaces fraisées préparées pour le soudage ne doivent pas être touchées avec
les mains et doivent être exemptes de toute impureté!
3.2.3 Soudage
Risque de coincement! Toujours respecter un écart sûr par rapport à la machine
lors du rapprochement des outils de serrage et des tubes. Ne jamais se placer dans
la machine!
Pendant un nouveau rapprochement des extrémités des tubes, la pression de mouvement des
pièces (pression d’entraînement) peut être lue sur le manomètre de l’unité hydraulique.
On appelle pression de mouvement des pièces (pression d’entraînement) la pression la plus
minimale nécessaire pour assurer le déplacement axial – indépendamment de la longueur et
du poids. Cette valeur doit être déterminée avec une très grande précision, pour cela il faut
ouvrir et fermer plusieurs fois la machine et régler la soupape de réglage de pression jusqu’à
ce que la machine s’arrête presque. Cette pression d’entraînement déterminée doit être
ajoutée à la pression de compensation, de réchauffage à cœur et d’assemblage.
Introduire l’élément thermique dans la machine de base entre les deux pièces à usiner
et veiller à ce que les assises de la plaque thermique soient placées dans les encoches du
dispositif d’évacuation.
Fermer la machine, régler et maintenir la pression de compensation plus la pression
d’entraînement nécessaires.
Dès que la hauteur de cordon nécessaire est atteinte de manière homogène sur tout le
pourtour des deux tubes, réduire la pression en ouvrant lentement la soupape de décharge.
Régler la pression de manière à ce qu’un contact homogène, presque sans pression des
extrémités des pièces à usiner avec l’élément thermique soit assuré (chauffage).
Refermer alors la soupape de décharge. Veiller à ce que les extrémités des pièces à usiner
restent en contact avec l’élément thermique.
A la fin du temps de chauffage, les pièces à usiner sont à nouveau éloignées l’une de l’autre,
l’élément thermique est enlevé et les extrémités des pièces à usiner sont rapprochées. La
pression doit maintenant être augmentée le plus linéairement possible jusqu’à la pression
d’assemblage nécessaire et maintenue pendant toute la période de refroidissement.
Contrôler régulièrement la pression et l’ajuster par pompage si nécessaire. Faire vérifier le
système hydraulique en cas de perte excessive de pression.
Attention: Pendant les 20 à 100 premières secondes, maintenir le levier de
commande enfoncé puis le relâcher (en position médiane).
Remettre l’élément thermique dans la caisse de transport.
Lorsque le temps de refroidissement est écoulé, enlever entièrement la pression en ouvrant la
soupape de décharge, desserrer les pièces soudées et les enlever.
Ouvrir la machine de base, établir un procès-verbal. La machine est prête pour le cycle de
soudage suivant.
Tous les paramètres de soudage sont indiqués dans les tableaux de soudage ci-joints.
3.2.4 Mise hors service
Déconnecter l’élément thermique.
Laisser refroidir l’élément thermique ou le ranger de manière à ce qu’il ne puisse
enflammer de subtances situées à proximité!
Débrancher l’équipement de fraisage, l’élément thermique et l’unité hydraulique et enrouler
les câbles.
FRANÇAIS32

Le groupe hydraulique doit être transporté et stocké uniquement à la verticale.
Lorsqu’il est positionné en biais, de l’huile s’échappe au niveau du bouchon de
ventilation muni d’une jauge!
Détacher les flexibles hydrauliques et les enrouler.
Attention! Protéger les raccords contre les impuretés!
3.3 Exigences générales
Etant donné que les conditions atmosphériques et ambiantes ont une influence décisive sur
ère
ème
ème
le soudage, les prescriptions correspondantes des directives DVS 2207, 1
, 11
et 15
parties, doivent absolument être respectées. En dehors de l’Allemagne, les directives nationales
correspondantes sont valides.
( Les travaux de soudage doivent être constamment et soigneusement surveillés !)
3.4 Remarques importantes concernant les paramètres de soudage
Tous les paramètres de soudage nécessaires comme la température, la force et la durée sont
ère
ème
ème
indiqués dans les directives DVS 2207, 1
, 11
et 15
parties. En dehors de l’Allemagne, les
directives nationales correspondantes sont valides.
Achat: DVS Media GmbH, Aachener Str. 172, 40223 Düsseldorf
Postfach 10 19 65, 40010 Düsseldorf, Tel.: +49 (0) 211 / 15 91 – 0
Email: media@dvs-hg.de internet: www.dvs-media.info
Au cas par cas, les paramètres d’usinage spécifiques aux matériaux des fabricants de tubes
devront absolument être demandés.
Les paramètres de soudage mentionnés dans les tableaux de soudage joints sont des valeurs
indicatives pour lesquelles la société ROTHENBERGER décline toute garantie !
Les valeurs pour la pression de compensation et d’assemblage indiquées dans les tableaux de
soudage ont été calculées avec la formule suivante:
Surface soudée A [mm²] x facteur de soudage SF [N/mm²]
Pression P [bar]=
Surface des vérins Az [cm²] x 10
Facteur de soudage (SF): PE = 0,15 N/mm², PP = 0,10 N/mm², PVDF = 0,10 N/mm²
(La surface totale des vérins de ROWELD P 160/5 B est de 3, 53 cm²)
(La surface totale des vérins de ROWELD P 200 B est de 3, 53 cm²)
(La surface totale des vérins de ROWELD P 250/8 B est de 6, 26 cm²)
(La surface totale des vérins de ROWELD P 355/12 B est de 6, 26 cm²)
(La surface totale des vérins de ROWELD P 500/18 B et de P 630/24 B est de 14, 13 cm²)
(La surface totale des vérins de ROWELD P 630/24 B Plus est de 22, 38 cm²)
4 Entretien et maintenance
Les points suivants doivent être respectés pour assurer le bon fonctionnement de la machine:
• les tiges conductrices doivent être maintenues exemptes d’impuretés. Les tiges conductrices
doivent être remplacées si leur surface est endommagée, étant donné que ceci peut
éventuellement entraîner une perte de pression.
• les entraînements électriques de l’équipement de fraisage et de l’élément thermique ne
doivent fonctionner qu’avec la tension indiquée sur la plaque signalétique.
• pour obtenir des résultats de soudage parfaits, il est nécessaire de maintenir l’élément
thermique propre. Si sa superficie est endommagée, l’élément thermique doit être doté
d’un nouveau revêtement et/ou remplacé. Des résidus de matériaux sur le miroir de chauffe
réduisent les propriétés antiadhésives et doivent être enlevés avec du papier qui ne s’effiloche
pas et de l’alcool à brûler (seulement quand l’élément thermique est froid).
• Le niveau d’huile du groupe hydraulique doit être contrôlé avant chaque mise en service (le
niveau d’huile devrait se situer entre les marques mini. et maxi.). Si nécessaire, rajouter de
l’huile hydraulique ( HLP – 46, réf.: 53649 ).
FRANÇAIS 33
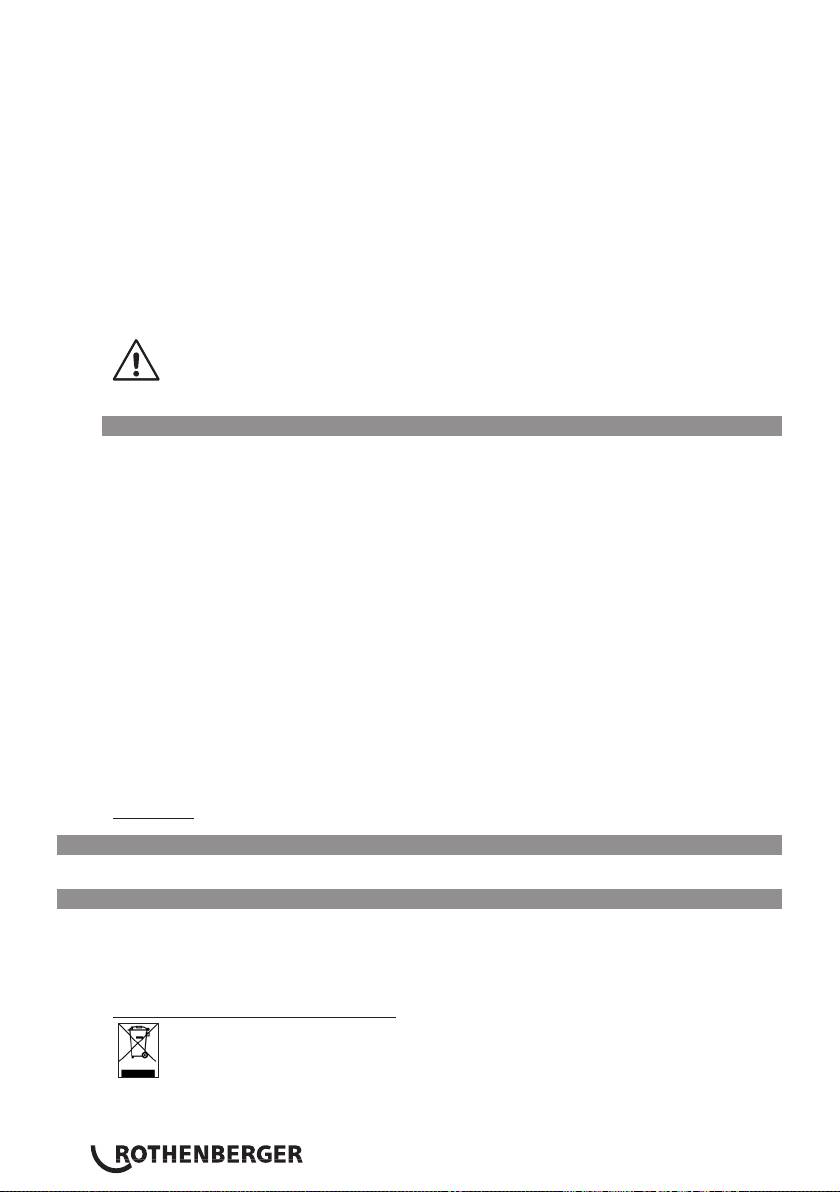
• L’huile hydraulique ( HLP – 46, réf.: 53649 ) doit être vidangée tous les 6 mois.
• Pour éviter des défaillances de fonctionnement, l’unité hydraulique doit être vérifiée
régulièrement afin de s’assurer de son étanchéité, du bon serrage des raccords à vis ainsi que
de l’état parfait du câble électrique.
• Les raccords hydrauliques express de l’unité hydraulique et du paquet de flexibles doivent
être protégés contre les impuretés. S’ils sont sales, ils devront être nettoyés avant d’être
raccordés.
• L’équipement de fraisage est doté de deux lames affûtées des deux côtés. Lorsque la
performance de coupe diminue, les lames peuvent être tournées et/ou remplacées par des
lames neuves.
• Il faut toujours veiller à ce que les extrémités de tubes et/ou de pièces à usiner, en particulier
les surfaces de contact, soient exemptes d’impuretés étant donné que sinon la durée de vie
des lames est fortement raccourcie.
Une vérification annuelle de la soudeuse doit être effectuée par le fabricant ou
par un point de service après-vente homologué, conformément à DVS 2208. Le
cycle de contrôle devrait être raccourci pour les machines soumises à une
sollicitation supérieure à la moyenne.
4.1 Entretien de la machine et des outils
(Tenir compte des instructions de maintenance du point 4!)
Des outils affûtés et propres donnent de meilleurs résultats de travail et sont plus sûrs.
Remplacer immédiatement des pièces émoussées, cassées ou perdues. Contrôler que les
accessoires sont attachés de manière sûre à la machine.
Utiliser uniquement des pièces de rechange originales lors des travaux de maintenance. Seul du
personnel spécialisé qualifié est autorisé à effectuer des réparations.
Débrancher la machine lorsqu’elle n’est pas utilisée, avant des travaux d’entretien et de
maintenance et avant le remplacement de pièces accessoires.
Avant raccorder à nouveau la machine au réseau électrique, il faut s’assurer que la machine et les
outils accessoires sont bien déconnectés.
Si des câbles de rallonge sont utilisés, leur sécurité et leur bon fonctionnement doivent être
contrôlés. Seule l’utilisation de câbles homologués pour le plein air est autorisée.
Il est interdit d’utiliser des outils et des machines si le bâti ou des poignées, en particulier en
plastique, sont déchirés et/ou déformés.
Des impuretés et de l’humidité dans de telles fissures conduisent le courant électrique. Ceci peut
entraîner une électrocution si un défaut d’isolation survient dans l’outil et/ou dans la machine.
Remarque: nous renvoyons en outre aux prescriptions de prévention des accidents.
5 Accessoires
Vous trouverez les accessoires appropriés et un formulaire de commande page 147 et suivantes.
6 Elimination des déchets
Certaines pièces de l’appareil sont recyclables et peuvent donc faire l’objet d’un traitement
de recyclage. Des entreprises de recyclage agréées et certifées sont disponibles à cet effet.
Renseignez-vous auprès de votre administration de déchets compétente pour l’élimination non
polluante des pièces non recyclables (par ex. déchets électroniques).
Pour les pays européens uniquement:
Ne pas jeter les appareils électriques dans les ordures ménagères ! Conformément à la
directive européenne 2012/19/CEE relative aux déchets d‘équipements électriques et
électroniques et sa transposition dans la législation nationale, les appareils électriques
usagés doivent faire l‘objet d‘une collecte sélective ainsi que d‘un recyclage respectueux
de l‘environnement.
FRANÇAIS34
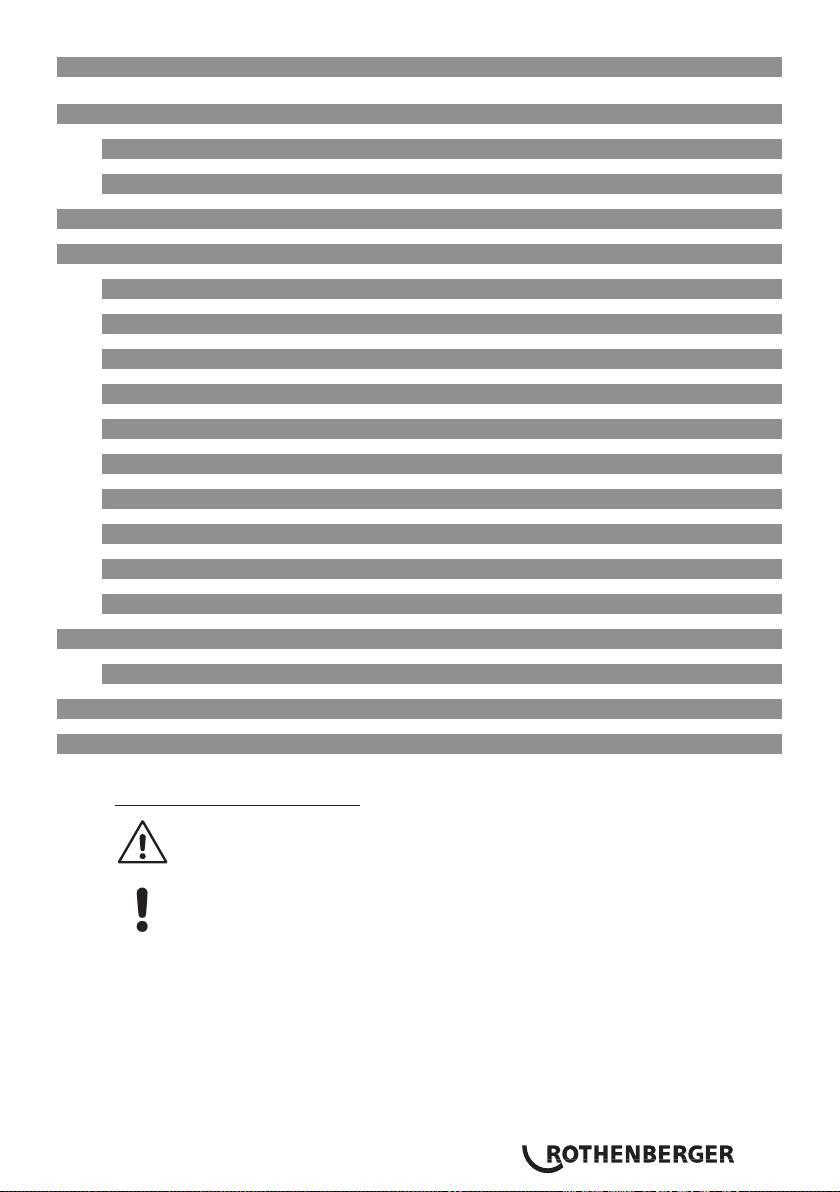
Índice Página
1 Indicaciones de seguridad 36
1.1 Uso apropiado de la máquina 36
1.2 Indicaciones generales de seguridad 36
2 Datos técnicos, consulte el folleto „Datos técnicos“
3 Funcionamiento del aparato 38
3.1 Descripción del aparato 38
3.1.1 Máquina base (fig. A) 38
3.1.2 Grupo hidráulico (fig. B) 38
3.2 Instrucciones de manejo 39
3.2.1 Puesta en servicio 39
3.2.2 Medidas a tomar para la preparación de la soldadura 40
3.2.3 Soldadura 43
3.2.4 Puesta fuera de servicio 43
3.3 Requisitos generales 44
3.4 Avisos importantes a los parámetros de soldadura 44
4 Limpieza y mantenimiento 44
4.1 Limpieza de máquina y herramienta 45
5 Accesorios 45
6 Eliminación 45
Marcaciones en este documento:
Peligro!
Este símbolo avisa de que el usuario corre peligro de lesionarse.
Atención!
Este símbolo avisa de que hay peligro de causar daños materiales o medioambientales.
Requerimiento de actuar
ESPAÑOL 35
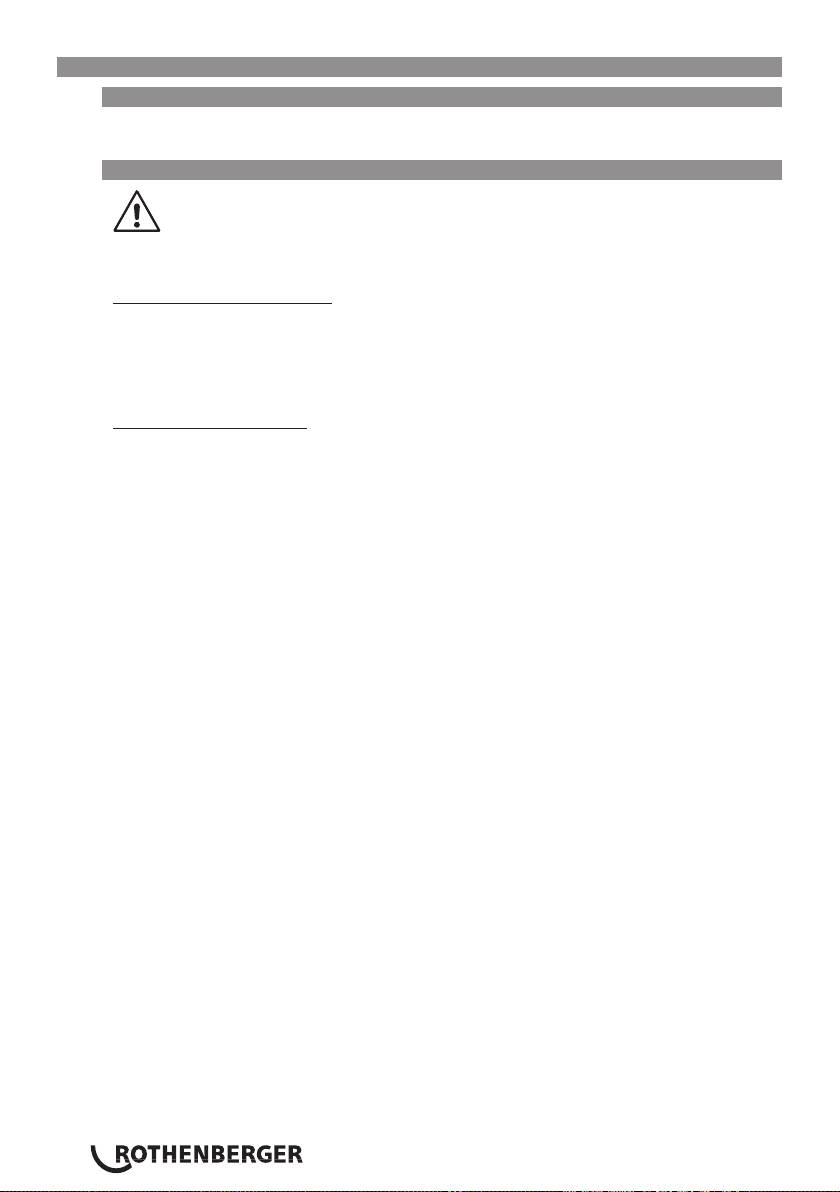
1 Indicaciones de seguridad
1.1 Uso apropiado de la máquina
Las máquinas ROWELD P160-630/5-24B Plus Professional se emplearán sólo para la produc-
ción de uniones soldadas de tubos PE - PP y PVDF conforme a los datos técnicos.
1.2 Indicaciones generales de seguridad
¡ATENCIÓN! En la utilización de herramientas eléctricas se observarán las siguientes
medidas básicas de seguridad para evitar la electrocución, lesiones e incendios.
Lea todas las indicaciones antes de utilizar esta herramienta eléctrica y conserve las
advertencias de seguridad en lugar seguro.
Mantenimiento y reparación:
1 Limpieza, mantenimiento y lubricación periódicas. Antes de realizar ajustes y
operaciones de mantenimiento o reparación desconecte el aparato de la corriente eléctrica.
2 Las reparaciones del equipo sólo las ha de realizar personal cualificado y con
recambios originales. Con ello queda garantizada la seguridad del equipo.
Trabajar de forma segura:
1 Mantenga su zona o puesto de trabajo ordenado. El desorden puede ser la causa de un
accidente.
2 Tenga en cuenta las influencias ambientales. No exponga las herramientas eléctricas a
la lluvia. No utilice las herramientas eléctricas en un entorno húmedo o mojado. Procure que
la zona o puesto de trabajo esté bien iluminado. No utilice las herramientas eléctricas donde
exista peligro de incendio o de explosión.
3 Protéjase contra la electrocución. Evite tocar, con cuaquier parte del cuerpo, las piezas
puestas a tierra (p. ej., tubos, radiadores, cocinas eléctricas, frigoríficos).
4 Haga que terceras personas se mantengan alejadas. No permita que terceras personas,
especialmente niños, toquen la herramienta eléctrica o el cable. Haga que se mantengan
alejados de la zona de trabajo.
5 Conserve las herramientas eléctricas que no vaya a utilizar en un lugar seguro. Las
herramientas eléctricas que no se vayan a utilizar deben depositarse en un lugar seco, alto o
que se pueda cerrar con llave, fuera del alcance de los niños.
6 No sobresolicite su herramienta eléctrica. Las herramientas eléctricas ofrecen mejores
prestaciones y son más seguras trabajando dentro de sus márgenes de potencia.
7 Utilice la herramienta eléctrica adecuada. No utilice herramientas de poca potencia para
trabajos que requieran mayor potencia. No utilice la herramienta eléctrica para fines para los
que no ha sido prevista. Utilice, p. ej., una sierra circular de mano para cortar troncos o leña.
8 Lleve ropa adecuada. No se llevará ropa holgada o joyas, podrían quedar atrapadas en las
piezas móviles. Si se trabaja en el exterior se recomienda llevar calzado antideslizante. Si tiene
el pelo largo, llévelo sujeto y cubierto.
9 Utilice los equipos de protección. Lleve gafas de protección. Utilice mascarilla en los
trabajos en los que se genere polvo.
10 Conecte el dispositivo de aspiración. Si existen conexiones a un dispositivo de aspiración o
de recogida de polvo, cerciórese de que están conectados y de que funcionan correctamente.
11 No utilice el cable para fines para los que no se ha previsto. No utilice el cable para
desacoplar el conector de la toma de corriente tirando del mismo. Proteja el cable de altas
temperaturas, del aceite y de bordes cortantes.
ESPAÑOL36
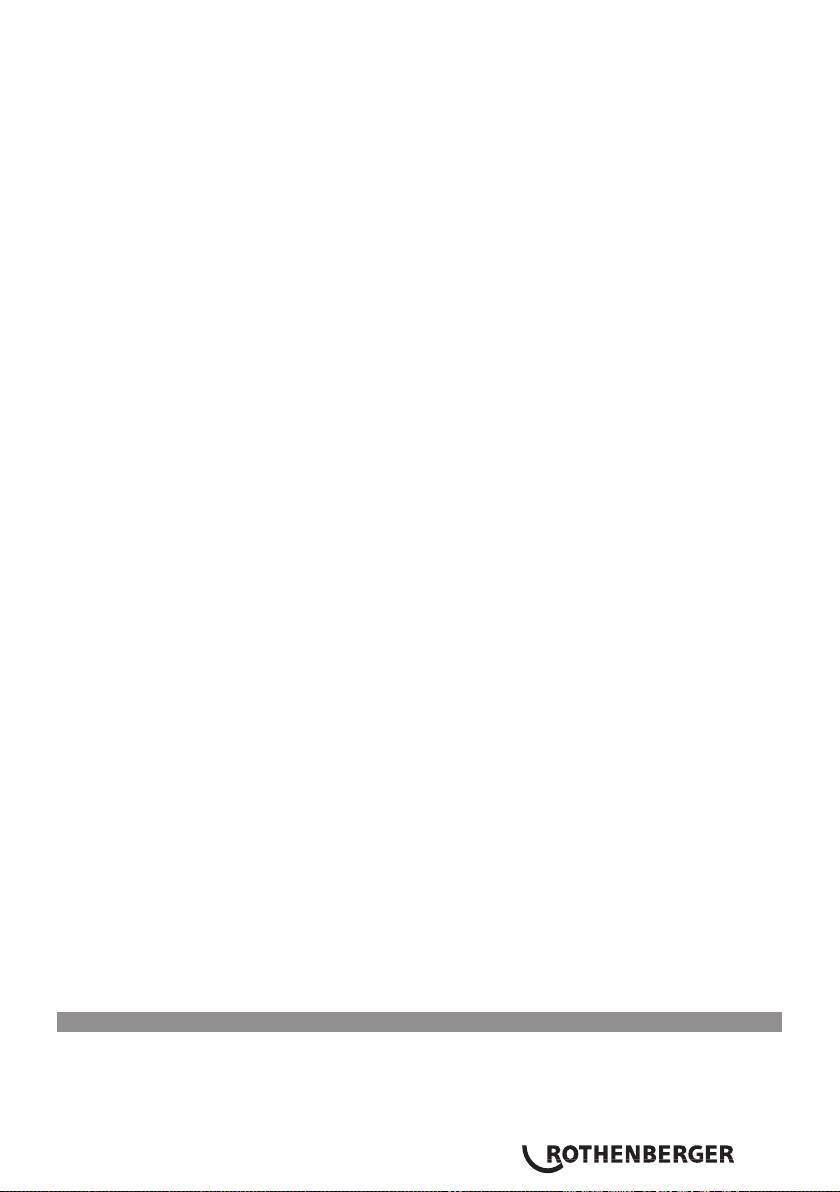
12 Fije la pieza de trabajo de forma segura. Utilice dispositivos de sujeción o un tornillo de
banco para fijar la pieza de trabajo. De este modo estará más segura que si la sujeta con la
mano.
13 Evite trabajar en una postura corporal forzada. Procure trabajar en posición firme y sin
perder el equilibrio en ningún momento.
14 Conserve la herramienta debidamente. Mantenga sus herramientas de corte afiladas
y limpias, de este modo trabajará mejor y con mayor seguridad. Siga las indicaciones para
la lubricación y el cambio de útil. Compruebe periódicamente el cable de conexión de
la herramienta eléctrica y en caso de detectar daños, haga que la repare un especialista
homologado. Compruebe los cables de prolongación periódicamente y sustitúyalos cuando
resulten dañados. Los mangos y asideros deben estar secos, limpios y sin manchas de aceite o
grasa.
15 Desacople el conector de la toma de corriente. Por ejemplo, cuando no se utilice la
herramienta eléctrica, antes de realizar tareas de mantenimiento y al cambiar útiles, como
pueden ser hojas de corte, brocas o fresas.
16 No deje las llaves de la herramienta puestas. Antes de encender la herramienta
compruebe que haya retirado la llave y el útil de ajuste.
17 Evite el funcionamiento sin supervisión. Asegúrese de que el conmutador está en
posición de apagado al acoplar el conector a la toma de corriente.
18 Utilice un cable de prolongación para trabajar en el exterior. En el exterior utilice sólo
cables homologados y con el distintivo correspondiente para uso en el exterior.
19 Este siempre atento. Concéntrese en lo que está haciendo. Realice los trabajos con sentido
común. No utilice las herramientas eléctricas si no puede concentrarse en el trabajo.
20 Compruebe la herramienta eléctrica con respecto a posibles daños. Antes de utilizar
la herramienta eléctrica se tendrá que comprobar que los dispositivos de protección y
los componentes que estén ligeramente dañados cumplan su función correctamente.
Compruebe que todas las piezas y componentes móviles funcionen correctamente, que
no se atascan y que no estén dañados. Todas las piezas y componentes tienen que estar
correctamente montados y cumplir todos los requisitos que garanticen el funcionamiento
correcto de la herramienta eléctrica.
Los dispositivos de protección y los componentes que presenten daños tienen que ser
sustituidos o reparados pertinentemente en un taller especializado homologado, siempre y
cuando no figure lo contrario en las instrucciones de uso. Los conmutadores o interruptores
dañados tienen que ser sustituidos en un taller del cliente.
No utilice las herramientas eléctricas cuyos conmutadores de encendido y apagado no
funcionen correctamente.
21 Atención. Si se utilizan otras herramientas u otros accesorios se corre el riesgo de sufrir
lesiones.
22 Haga reparar sus herramientas eléctricas en talleres de electricidad o por personal
electricista. Esta herramienta eléctrica cumple con las normas de seguridad pertinentes. Las
reparaciones las debe realizar sólo personal electricista, utilizando recambios originales, de lo
contrario el usuario corre el riesgo de sufrir o provocar un accidente.
2 Datos técnicos, consulte el folleto „Datos técnicos“
ESPAÑOL 37
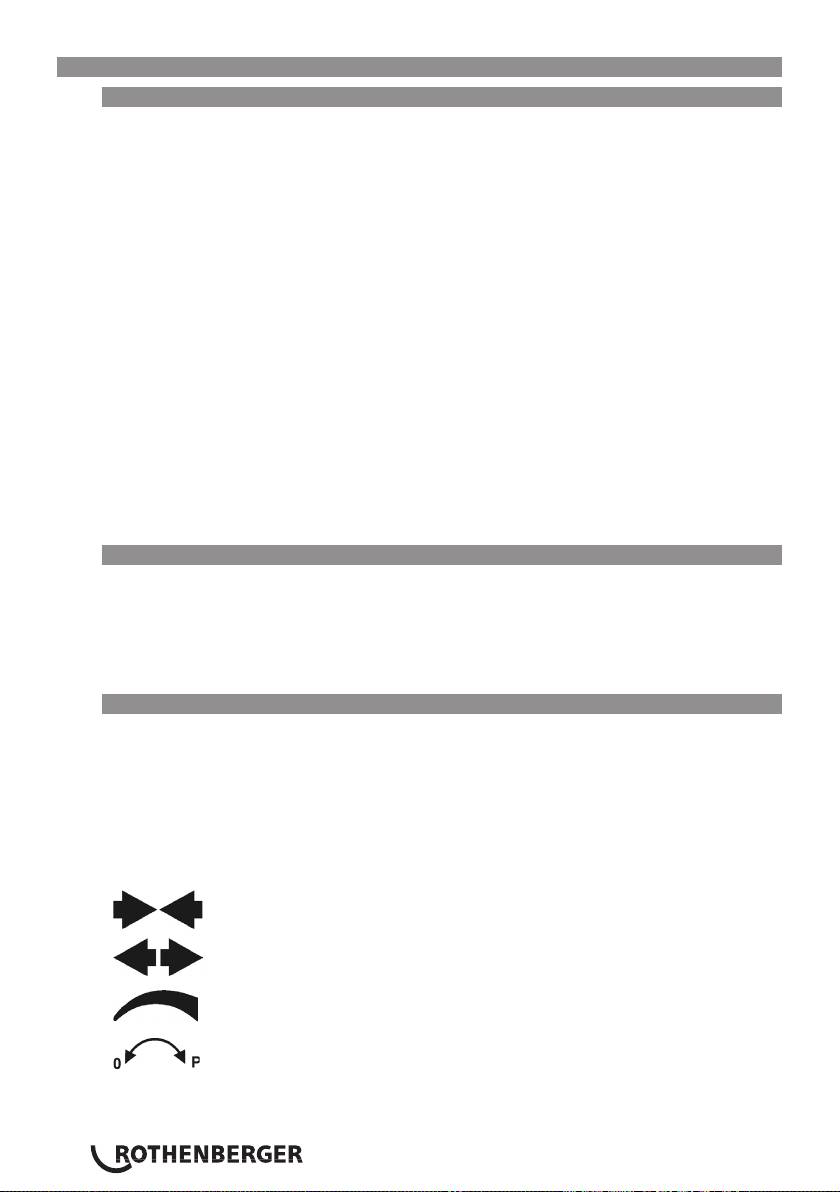
3 Funcionamiento del aparato
3.1 Descripción del aparato
Las máquinas ROWELD P160-630/5-24B Plus Professional son máquinas de soldar a tope con
elemento calefactor compactas y fácilmente transportables, que fueron concebidas especialmente
para el uso en obras – y aquí especialmente en zanjas de tubos -. Naturalmente las máquinas
también se pueden usar en talleres.
Debido a la versatilidad de las máquinas de soldadura ”tipo ROWELD“ pueden realizarse con
seguridad las siguientes uniones soldadas de tubos de PE - PP y PVDF con diámetros exteriores de
40-630mm/1 1/4-24“ en todos los campos de aplicación:
I. Tubo - Tubo
II. Tubo - codo de tubo
III. Tubo - Pieza en T
IV. Tubo - cuello de soldadura previa
Las máquinas se componen esencialmente de:
Máquina base, piezas tensoras reductoras, grupo hidráulico, instalación fresadora, elemento
calefactor, caja de ajuste.
Al soldar cuellos de soldadura previa se debe usar el adaptador de bridas a la venta como
accesorio.
ROWELD P160-250/5-8B: Al soldar codos de tubo del diámetro máx. de la máquina con curvas
de unión estrechas se deberá utilizar la parte superior de la herramienta de sujeción biselada
adquirible como accesorio.
ROWELD P500-630/18-24B Plus: Para elevar y expulsar la fresadora y el elemento calefactor
puede usarse el dispositivo de elevación eléctrico a la venta como accesorio.
3.1.1 Máquina base (fig. A)
1 Elementos tensores móviles 5 Elemento tensor desmontable
2 Elemento tensor desplazable 6 Tornillos de fijación arriba
3 Pieza distanciadora con muescas de anclaje 7 Distanciador
Dispositivo de extracción del elemento
4
8 Tornillos de fijación abajo
calefactor
3.1.2 Grupo hidráulico (fig. B)
1 Empalme carga aceite y sonda de nivel 5 Cable de red
2 Conectador acoplamiento rápido 6 Manómetro
3 Válvula de descarga 7 Palanca de mando, Hacia la izquierda :
cierre, Hacia la derecha: apertura
4 Manguito acoplamiento rápido 8 Válvula ajuste presión
El grupo hidráulico permite realizar las operaciones marcadas con los símbolos siguientes de la
máquina soldadora:
Para juntar las mordazas, mover la palanca de control hacia la izquierda. La
velocidad de avance y de formación de presión dependen del ángulo de giro.
Para separar las mordazas, mover la palanca de control hacia la derecha. La
velocidad de avance depende del ángulo de giro.
Válvula de ajuste de presión para las presiones de fresado, igualación,
calentamiento y unión. La presión seleccionada se muestra en el manómetro.
Válvula de descarga, mediante giro a la izquierda puede disminuirse la presión. La
velocidad de disminución de presión depende de la cantidad de vueltas. Giro hacia
la derecha mantener la presión .
ESPAÑOL38
OIL
Tubuladura de carga tapa de cierre con aceite – sonda de nivel