HEIDENHAIN ND 200: 4 Installation
4 Installation: HEIDENHAIN ND 200
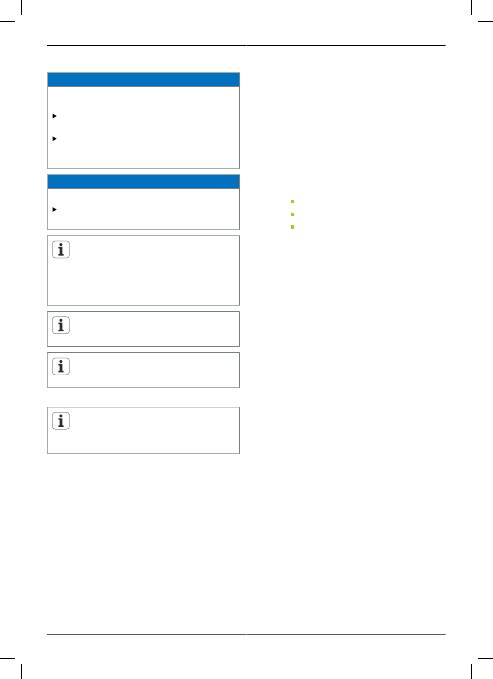
Installation Instructions
en
ND 200
20
4 Installation
NOTICE
Disturbances caused by lack of grounding or improper
grounding!
Never operate the unit without proper ground
connection.
Connect the ground connector on the rear panel to
the central grounding point of the unit.
Minimum cross section of the conductor: 6 mm
2
.
NOTICE
Risk of damage to internal components!
Do not engage or disengage any connecting elements
while the unit is under power.
Depending on the unit's equipment, the
installation may differ from the procedure
described in this chapter. If the Addendum
shipped with the product contains information
on the installation, the information given in
the Addendum takes precedence over the
information in this chapter.
The safety of any system incorporating the
use of this product is the responsibility of the
assembler or installer of the system.
The illustrations of pin layouts always show the
pin assignments of the connections on the unit,
and not of the connectors.
Personnel requirement
The following steps are only to be performed by
qualified personnel!
For more information: see "Personnel
qualification", page 16.
4.1 Product overview
Rear panel
See Figure "A" on the front fold-out page. The figure
shows the rear of the ND 287. The ND 287 and ND 280 are
identical in their design, except for the additional connection
possibilities provided by the ND 287, which are listed below.
1
Power switch
2
Power connector
3
Line fuse
4
Ground
X1
15-pin D-sub connection for HEIDENHAIN
encoder with
11 µA
PP
interface or 1 V
PP
interface or EnDat interface (purely serial)
Only ND 287 (option)
:
Replacing the encoder module by an analog
module for connection of an analog sensor
X31
Serial 9-pin D-sub connection RS-232-C/V.24
for data transmission
X32
Serial USB connection type B (UART) for da-
ta transmission
Only ND 287:
X41
25-pin D-sub connection for switching in-
puts and outputs
X2
Option: Addition of an expansion module
(as for connection X1)
X26(X27)
Option: Addition of an Ethernet expansion
module (100baseT) for network connection
via TCP/IP protocol
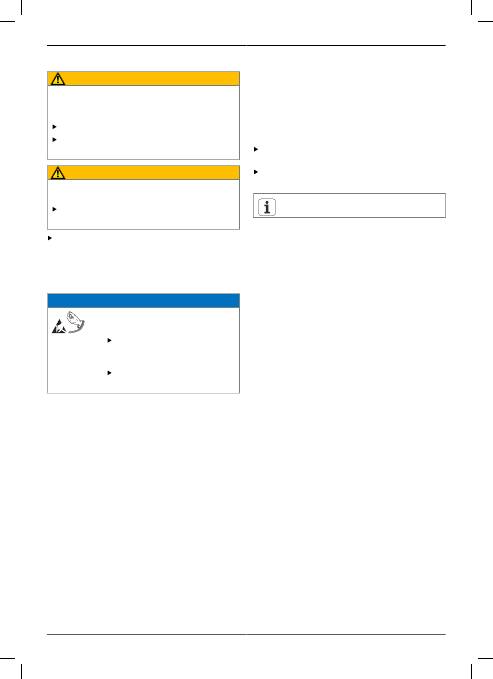
ND 200
Installation Instructions
en
21
4.2 Connecting the line voltage WARNING
Risk of electric shock!
Improper grounding of electrical devices involves a risk of
serious injury or death by electric shock.
Always use 3-wire power cables.
Make sure the ground wire is correctly connected to
the ground of the building's electrical installations.
WARNING
A risk of fire exists if a power cord not meeting minimum
specifications is used!
Use only power cables that fulfill or exceed the
specified minimum requirements.
Use the supplied power cable to connect the power
connection to a 3-wire grounded power outlet. For
information about the location of the power connection
on the rear panel, see "Rear panel", page 20
4.3 Electrostatic discharge NOTICE
This product contains components
that can be destroyed by electro-
static discharge (ESD).
It is essential to observe the safety
precautions for handling ESD-sensiti-
ve components.
Never touch connector pins without
ensuring proper grounding.
4.4 Connecting encoders Connections
Encoders are connected to the encoder inputs X1 (X2)
provided on the rear panel. For information on the location
of the connections, see "Rear panel", page 20.
The number and type of connections available for encoders
may vary depending on the type of unit.
Connecting the encoder cables
Connect the cables of the encoders tightly to the
respective connections on the rear panel.
If the cable connectors include mounting screws, do not
overtighten them.
Vacant pins or wires must not be used.
Pin layout X1 (X2)
For pin layout for 11 µA
PP
, 1 V
PP
and EnDat 2.1, see "H" in
the Appendix.
Only ND 287: For pin layout if an analog module is being
used, see "M" in the Appendix.
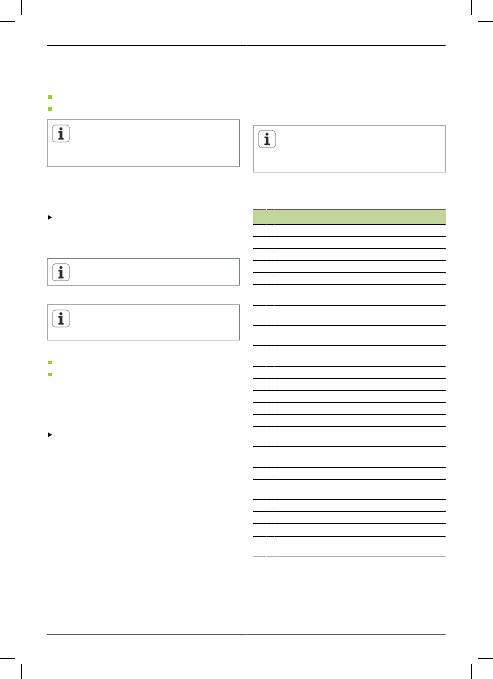
Installation Instructions
en
ND 200
22
4.5 Connecting computers and printers
The unit provides two serial interfaces for bidirectional data
communication:
X31: 9-pin RS-232-C/V.24 D-sub interface
X32: USB interface (UART)
You can use only one serial interface for data
transfer at a time.
Software updates can only be transferred to the
unit via the USB interface X32.
Connecting computers or printers via the RS-232-C/V.24
interface
A computer or a printer with a serial RS-232-C/V.24 data
interface can be connected to connection X31.
Use a serial cable (see "Accessories", page 19) to
connect the COM port of the computer or printer to
connection X31. For information on the location of the
connections, see "Rear panel", page 20.
Make sure the cable is securely attached. Do not
overtighten the connector screws.
RS-232-C/V.24: Pin layout X31
The wiring of the connecting cable depends
on the device being connected (see technical
documentation for external device).
Pin layout:
With handshake: See Figure 1 in "I" in the Appendix.
Without handshake: See Figure 2 in "I" in the Appendix.
For signal level, see "Specifications", page 24.
Connecting a computer via USB
A computer can be connected to connection X32 via the
USB interface.
Connect the USB port of the computer to connection
X32 using a USB cable (see "Accessories", page 19). For
information on the location of the connections, see "Rear
panel", page 20.
USB Type B (UART): Pin layout X32
For pin layout, see "J" in the Appendix.
4.6 Only ND 287: Wiring of switching inputs and outputs
The wiring of the switching inputs and outputs depends
on the customer's peripherals (see manufacturer's
documentation).
Personnel requirement
Depending on the peripherals to be connected,
the connection work may need to be carried out
by an electrical specialist.
Example: SELV exceeded.
Connection X41
Functional assignment of the 25-pin D-sub connection
(I = switching input, O = switching output):
Pin Function
1
0 V
2
I Reset, clear error message
3
I Set axis / coupled axes to value for datum point
4
I Ignore reference mark signals (X1)
5
I Start series of measurements / f(X1,X2) display
6
I Externally select display value for series of measure-
ments / X1 display
7
I Display minimum value of series of measurements /
X2 display
8
I Display maximum value of series of measurements /
X1+X2 display
9
I Display difference Max-Min of series of measure-
ments / X1-X2 display
10
0 V
11
Vacant
12
Do not assign
13
Do not assign
14 O Display value is zero
15 O Measured value is greater than or equal to trigger li-
mit A1
16 O Measured value is greater than or equal to trigger li-
mit A2
17 O Measured value is less than the lower sorting limit
18 O Measured value is greater than the upper sorting li-
mit
19 O Error
20
Vacant
21
Vacant
22 I Pulse: Measured value output,
see Figure 1 in "L" in the Appendix
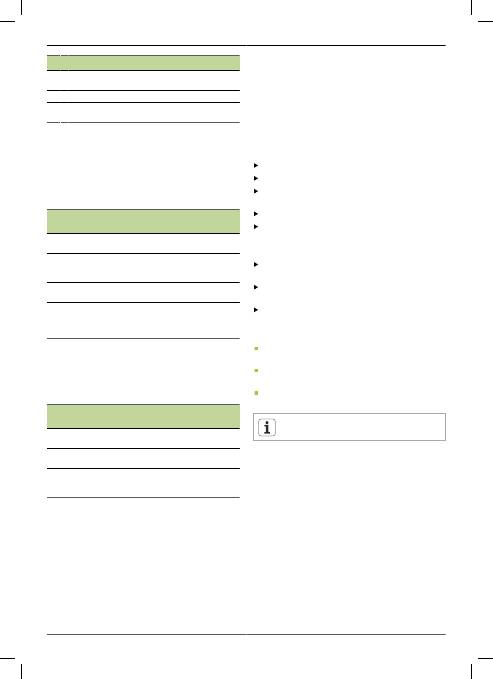
ND 200
Installation Instructions
en
23
Pin Function
23 I Contact: Measured value output,
see Figure 1 in "L" in the Appendix
24 I Ignore reference mark signals (X2, optional)
25 I Enable or disable REF mode (current REF status is
changed)
For pin layout, see "L" in the Appendix.
Switching inputs for measured value output
See Figure 1 in "L" in the Appendix.
The respective switching input is active when a Low signal
U
L
is applied (contact or pulse to 0 V).
Input signals: Signal Value
Internal
pull-up resistor
1 k
Ω
, active Low
Activation
Trigger by making contact against
0 V or by low-level signal over TTL
logic device
Delay time for
preset/reset
t
V
≤
2 ms
Minimum pulse du-
ration for all signals
(except for pin 22
and pin 23)
t
min
≥
30 ms
For signal level of inputs, see "Specifications", page 24.
Open-collector outputs
See Figure 2 in "L" in the Appendix.
The unit features open-collector outputs that switch to 0 V
(= active Low).
Output signals: Signal Value
Open-collector out-
puts
Active Low
Delay until signal out-
put
t
V
≤
20 ms
Signal duration of ze-
ro crossover, trigger
limit A1, A2
t
0
≤
180 ms
For signal level of outputs, see "Specifications", page 24.
4.7 Only ND 287: Installing optional expansion modules
For information on the location of the slots, see "Rear
panel", page 20.
Installing expansion modules
See "D" on the front fold-out page.
1
2
Ethernet expansion module
Analog module or encoder module
Switch the unit off and disengage the power plug.
Loosen the Torx screws of the selected input.
Remove the cover from the slot, or remove any module
that might be inserted.
Insert the new input assembly.
Re-tighten the Torx screws:
Tightening torque 1.5 Nm.
Connecting connectors
Connect the connector tightly to the respective
connection on the rear panel.
X1, X2: If the connectors include mounting screws, do
not overtighten them.
X26(X27): Insert the terminal of the RJ-45 connector so
that it engages.
Pin layouts
X1, X2: For connection of analog module, see "M" in the
Appendix.
X1, X2: For connection of the 11 µA
PP
/1 V
PP
/EnDat 2.1
module, see "H" in the Appendix.
X26(X27): For connection of the Ethernet module, see
"K" in the Appendix.
Vacant pins or wires must not be used.
Оглавление
- 1 Zu dieser Anleitung
- 2 Sicherheit
- 3 Montage
- 4 Installation
- 5 Technische Daten
- 1 About these instructions
- 2 Safety
- 3 Mounting
- 4 Installation
- 5 Specifications
- 1 A propos de cette notice
- 2 Sécurité
- 3 Montage
- 4 Installation
- 5 Caractéristiques techniques
- 1 Informazioni contenute nel presentemanuale
- 2 Sicurezza
- 3 Montaggio
- 4 Installazione
- 5 Dati tecnici
- 1 Acerca de este manual
- 2 Seguridad
- 3 Montaje
- 4 Instalación
- 5 Características técnicas
- 1 Om denna manual
- 2 Säkerhet
- 3 Montage
- 4 Installation
- 5 Tekniska data
- 1 Over deze handleiding
- 2 Veiligheid
- 3 Montage
- 4 Installatie
- 5 Technische gegevens
- 1 O tomto návodu
- 2 Bezpečnost
- 3 Montáž
- 4 Instalace
- 5 Technické parametry
- 1 この説明書について
- 2 安全
- 3 組立て
- 4 設置
- 5 技術仕様
- 1 O niniejszej instrukcji
- 2 Bezpieczeństwo
- 3 Montaż
- 4 Instalacja
- 5 Dane techniczne
- 1 Acerca destas instruções
- 2 Segurança
- 3 Montagem
- 4 Instalação
- 5 Dados técnicos
- 1 О настоящей инструкции
- 2 Безопасность
- 3 Монтаж
- 4 Установка
- 5 Технические параметры
- 1 Bu kılavuz hakkında
- 2 Güvenlik
- 3 Montaj
- 4 Kurulum
- 5 Teknik Veriler
- 1 關於這些手冊
- 2 安全
- 3 安裝
- 4 安裝
- 5 規格
- 1 关于这些说明
- 2 安全
- 3 安装
- 4 系统安装
- 5 技术参数
- *I_1126432-90*