Stiebel Eltron SBB WP SOL с 12.05.2008: .CZ`<<`.HC
.CZ`<<`.HC: Stiebel Eltron SBB WP SOL с 12.05.2008
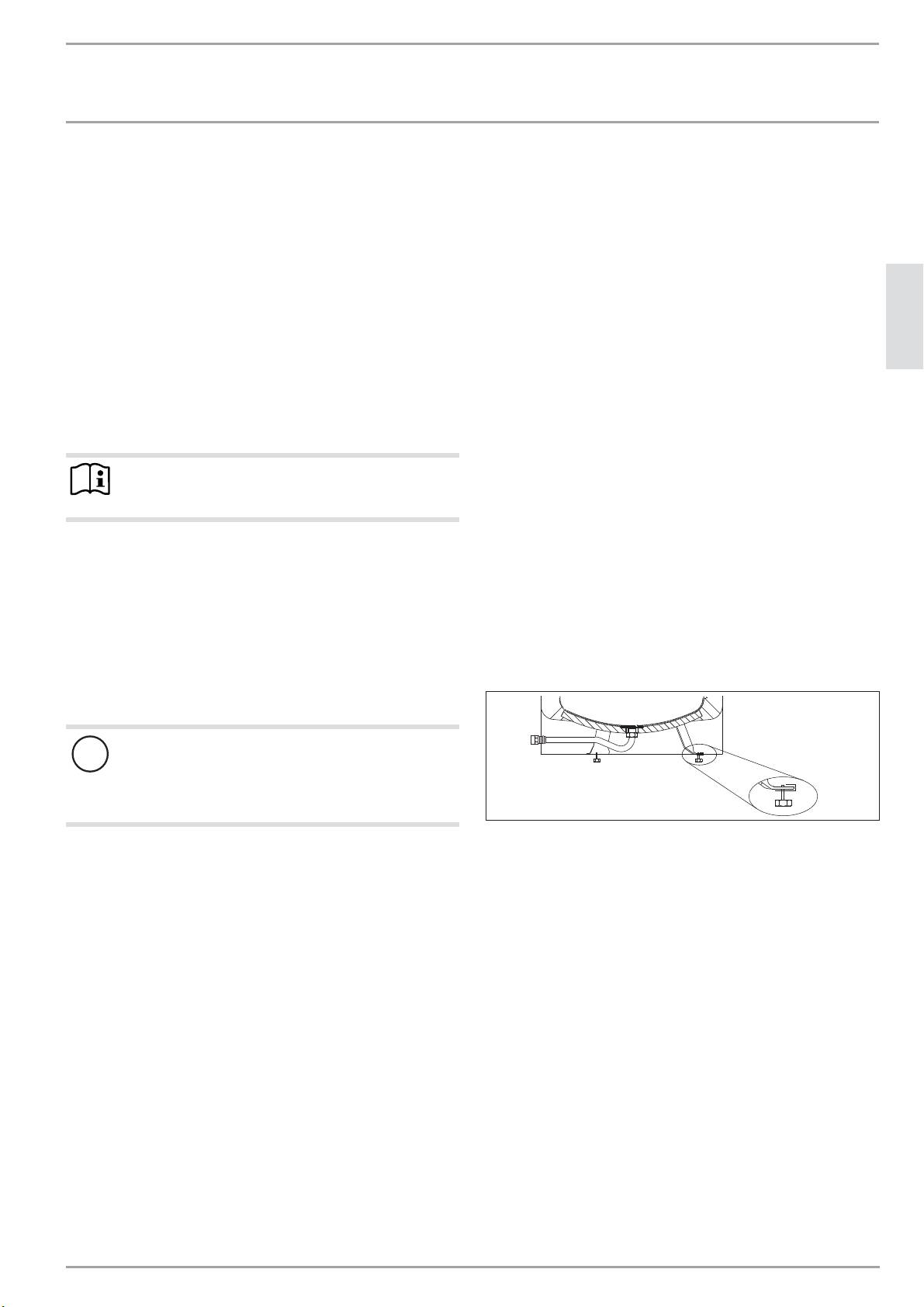
.CZ`<<`.HC
Z|ϼŒź
7. Appliance description
.CZ`<<`.HC
7.1 Standard delivery
Delivered with the appliance:
6. Safety
- Cold water inlet pipe with flat gasket
Only a qualified contractor should carry out installation, commis-
- Adhesive rosettes for connecting lines
sioning, maintenance and repair of the appliance.
-DHW sensor
- Adjustable feet
6.1 General safety instructions
ENGLISH
- Fixing straps with closure element
We guarantee trouble-free operation and operational reliability
- Thermometer (in its delivered condition located in the DHW
only if the original accessories and spare parts intended for the
outlet)
appliance are used.
7.2 Accessories
6.2 Regulations, standards and instructions
Depending on the static pressure, safety assemblies and pressure
reducing valves are available. These type-tested safety assemblies
Note
protect the appliance against unacceptable excess pressure.
Observe all applicable national and regional regulations
and instructions.
If it is not possible to fit an anode rod from above, install a seg-
mented signal anode.
Flanged immersion heaters are available as accessories.
6.3 Water installation
6.3.1 Cold water line
8. Preparations
Steel or copper pipes or plastic pipework are approved materials.
8.1 Installation site
A safety valve is required.
Always install the appliance in a room free from the risk of frost
6.3.2 DHW line
and near the draw-off point.
Copper, stainless steel or plastic pipework are approved materials.
Material losses
If a flanged immersion heater is fitted and plastic pipe-
work systems are used at the same time, observe the
maximum permissible temperature/ the maximum per-
missible pressure in chapter “Specification/ Data table”.
26_03_20_0008
f Use the adjustable feet to compensate for any unevenness in
Operate the appliance only with pressure-tested taps and valves.
the floor.
ŷŷŷĪńŒê¼¼ùé¼ùŒļĒĉĪĒă ZŗƃĜéÑƃĜqTZH<ĜŌ
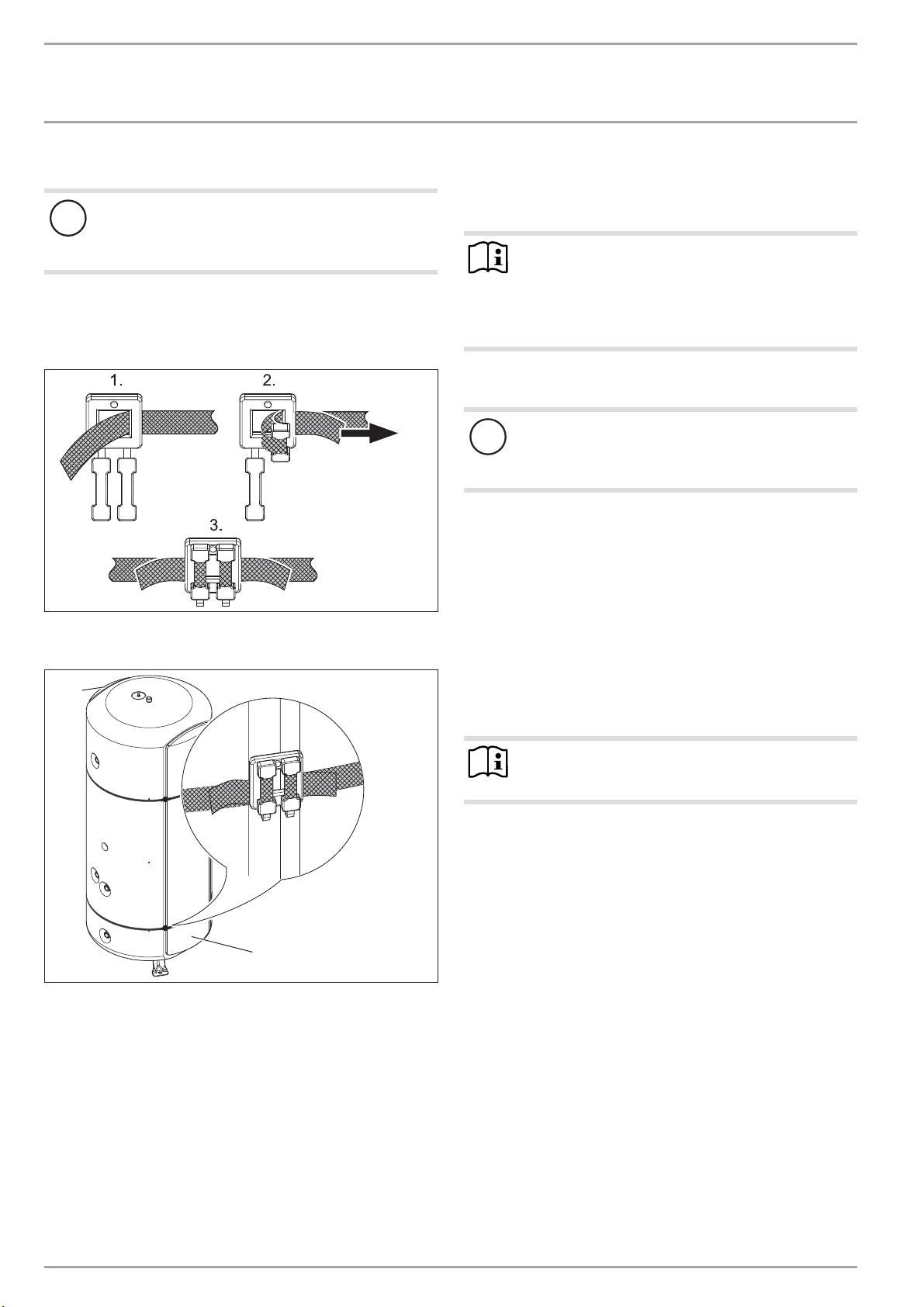
.CZ`<<`.HC
Tļ¼Ĥ|ļêĉÖÏĒļêĉńŒ|ùù|ŒêĒĉ
8.2 Transport
9. Preparing for installation
Material losses
9.1 Removing / fitting the cylinder casing
We recommend removing the cylinder casing for trans-
portation to the installation location to prevent it from
Note
becoming dirty or damaged.
Open or remove the cylinder casing before fitting the DHW
circulation and indirect coil lines.
Fit the cylinder casing before fitting a flanged immersion
SBB 501 WP SOL
heater.
f Both side insulation sections can be removed for transporta-
The plinth trim should be fitted after the tightness check.
tion in tight spaces. To do this, remove the cylinder casing.
9.2 Checking the signal anode
Material losses
The appliance must not be operated without a consump-
tion indicator or with a damaged one, otherwise water
will leak out once the anode is depleted.
9.3 Heating installation
f Flush the indirect coils with water before connecting the
heating water pipes.
26_03_20_0003
SBB401WPSOL | SBB 501 WP SOL without solar installation
f You may connect both indirect coils to the “heat pump heat-
f Use the fixing straps to refit the thermal insulation sections
ing return” and “solar flow” (see chapter “Specification /
after transportation.
Dimensions and connections”).
1
9.4 Fitting the water connection and the safety
assembly
Note
Carry out all water connection and installation work in
accordance with regulations.
f Flush the line thoroughly.
f Connect the DHW outlet and the cold water inlet lines with
the safety assembly. Bear in mind that, depending on the
static pressure, you may also need a pressure reducing valve.
1
26_03_20_0004
1 Side thermal insulation section
f Ensure that the closures are in the joint between a side
thermal insulation section and the thermal insulation of the
cylinder.
ĜÄZŗƃĜéÑƃĜqTZH< ŷŷŷĪńŒê¼¼ùé¼ùŒļĒĉĪĒă
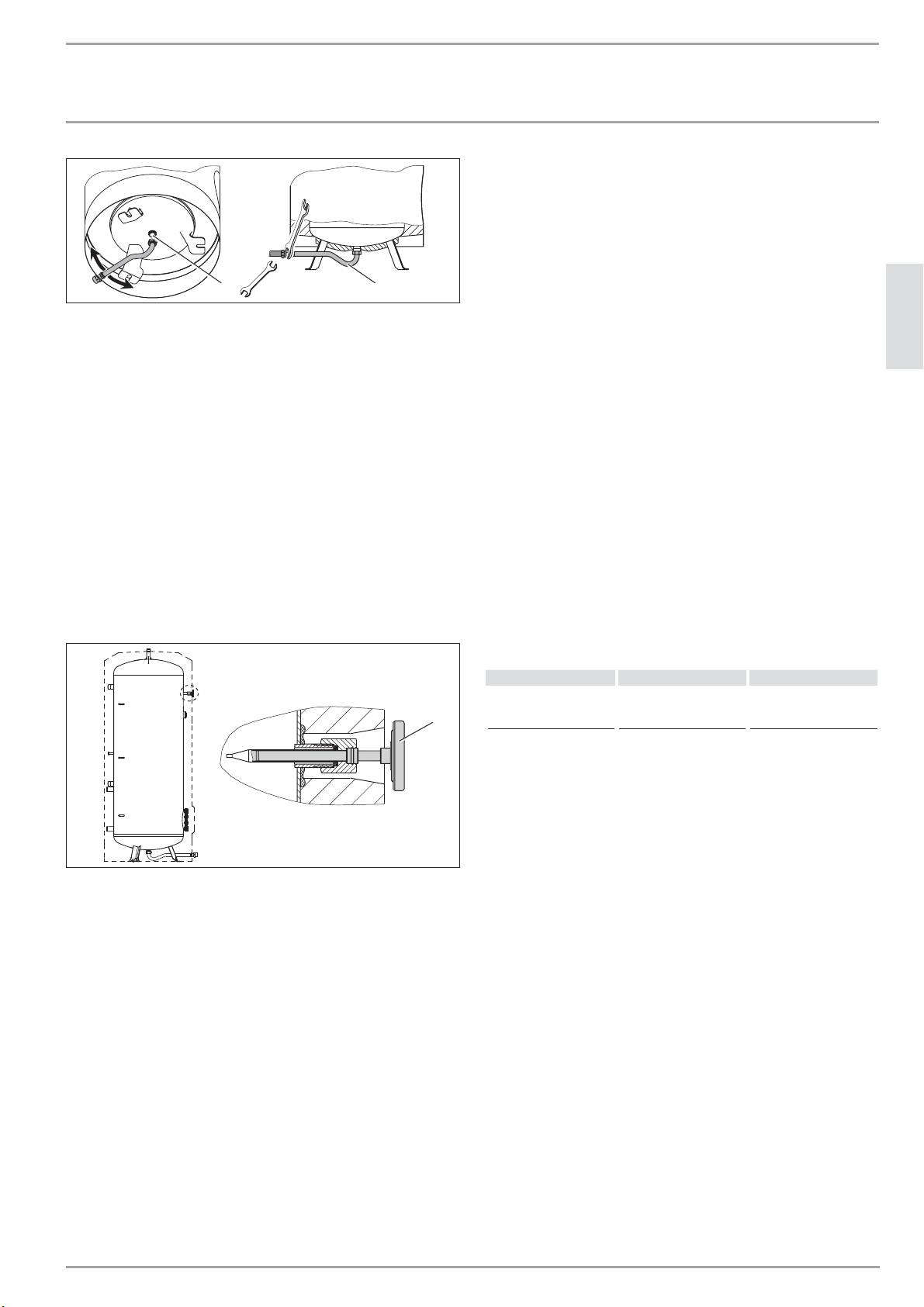
.CZ`<<`.HC
ĒăăêńńêĒĉêĉÖ
10. Commissioning
f Open a downstream draw-off point until the appliance has
filled up and the pipes are free of air.
f Vent the indirect coils after filling the heat pump system.
f Fit the accessories and check them if necessary.
f Check the function of the safety valve.
12
26_02_09_0035
f Check that the DHW temperature on the heat pump control
1 Cold water connection
unit is displayed correctly.
2 Cold water inlet pipe
ENGLISH
f Connect the cold water supply directly to the cylinder or with
10.1 Appliance handover
the connecting pipe routed between the cylinder feet.
f Explain the appliance function to users and familiarise them
f During fitting, counterhold the fitting with an open-ended
with its operation.
spanner (size 36).
f Make users aware of potential dangers, especially the risk of
f Check the rigidity of the connecting pipe and secure it further
scalding.
if required.
f Hand over these instructions.
f Size the drain so that water can drain off unimpeded when
the safety valve is fully opened. The blow-off aperture of the
11. Shutting down
safety valve must remain open to the atmosphere.
f Disconnect the appliance from the mains at the MCB/fuse in
f Fit the blow-off line of the safety assembly with a constant
the fuse box.
slope.
f Drain the appliance. See chapter “Maintenance / Draining the
f Observe the information in the installation instructions of the
appliance”.
safety assembly.
9.5 Fitting the thermometer and DHW sensor
12. Troubleshooting
12.1 Fault table
%|şùŒ |şń¼ V¼ă¼®ź
The safety valve drips
The valve seat is con-
Clean the valve seat.
when the heating is
taminated.
1
switched off.
26_03_20_0005
1 Thermometer
f Insert the thermometer as far as it will go and align it.
f Insert the DHW sensor as far as it will go into the well for the
heat pump flow sensor (recommended energy saving posi-
tion) or heat pump return sensor (high DHW convenience).
ŷŷŷĪńŒê¼¼ùé¼ùŒļĒĉĪĒă ZŗƃĜéÑƃĜqTZH<ĜĎ

.CZ`<<`.HC
B|êĉŒ¼ĉ|ĉ¼
13. Maintenance
14. Technische Daten
WARNING Electrocution
14.1 Dimensions and connections
Carry out all electrical connection and installation work
in accordance with relevant regulations.
SBB 301 WP
If you need to drain the appliance, observe chapter “Draining the
appliance”.
F
13.1 Checking the safety valve
f Regularly vent the safety valve on the safety assembly until a
full water jet is discharged.
K
13.2 Draining the appliance
K
L
G
WARNING Burns
Hot water may escape during the draining process.
F
K
If the cylinder needs to be drained for maintenance or to protect
the whole installation when there is a risk of frost, proceed as
follows:
L
G
f Close the shut-off valve in the cold water line.
f Open the hot water taps on all draw-off points.
F
F
f Drain the appliance via the drain valve of the safety
assembly.
13.3 Replacing the signal anode
f Replace the signal anode if it becomes depleted. Ensure
there is a good connection between the anode and the cylin-
der (maximum permissible transition resistance 0.3Ω).
L
13.4 Cleaning and descaling the appliance
D0000017377
1
F
K
K
L
G
1
26_03_01_0847
F
1 Threaded extraction holes
K
f Use the threaded lift-off holes to release the flange plate
from the flange connector.
L
For the torque of the flange screws, see chapter “Specification /
G
Dimensions and connections”.
F
f Never use descaling pumps.
F
26_03_20_0009
f Never treat the cylinder surface or the signal anode with des-
caling agents.
ŝƃZŗƃĜéÑƃĜqTZH< ŷŷŷĪńŒê¼¼ùé¼ùŒļĒĉĪĒă
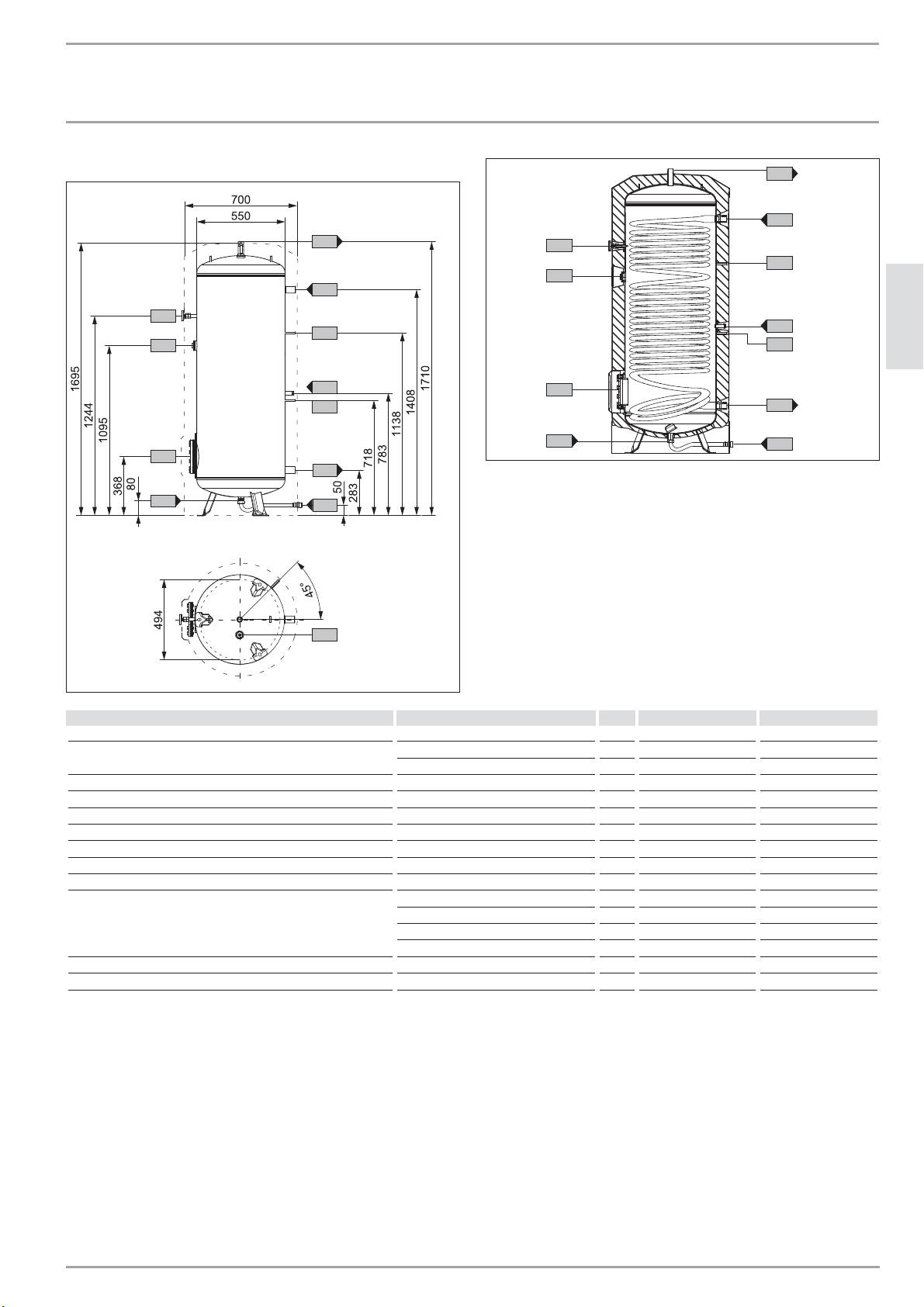
.CZ`<<`.HC
`¼äĉêńä¼|Œ¼ĉ
SBB 302 WP
F
G
F
K
K
L
G
K
F
K
ENGLISH
L
K
F
L
K
G
F
F
26_03_20_0010
L
G
F
F
L
D0000017379
ZŗƃĜqT ZŗƃŝqT
c01 Cold water inlet Male thread G 1 A G 1 A
c03 Cold water inlet pipe
Male thread G 1 A G 1 A
Torque Nm 100 100
c06 DHW outlet Male thread G 1 A G 1 A
c10 DHW circulation Male thread G 1/2 A G 1/2 A
d07 Heat pump heating flow Female thread G 1 1/2 G 1 1/2
d08 Heat pump heating return Female thread G 1 1/2 G 1 1/2
h01 Sensor heat pump flow Diameter mm 9.5 9.5
h02 Sensor heat pump return Diameter mm 9.5 9.5
h43 Thermometer Diameter mm 9.5 9.5
i01 Flange
Diameter mm 210 210
Pitch circle diameter mm 180 180
Screws M 12 M 12
Torque Nm 55 55
i07 Electric emergency/booster heater Female thread G 1 1/2 G 1 1/2
i18 Protective anode Female thread G 1 1/4 G 1 1/4
ŷŷŷĪńŒê¼¼ùé¼ùŒļĒĉĪĒă ZŗƃĜéÑƃĜqTZH<ŝĜ
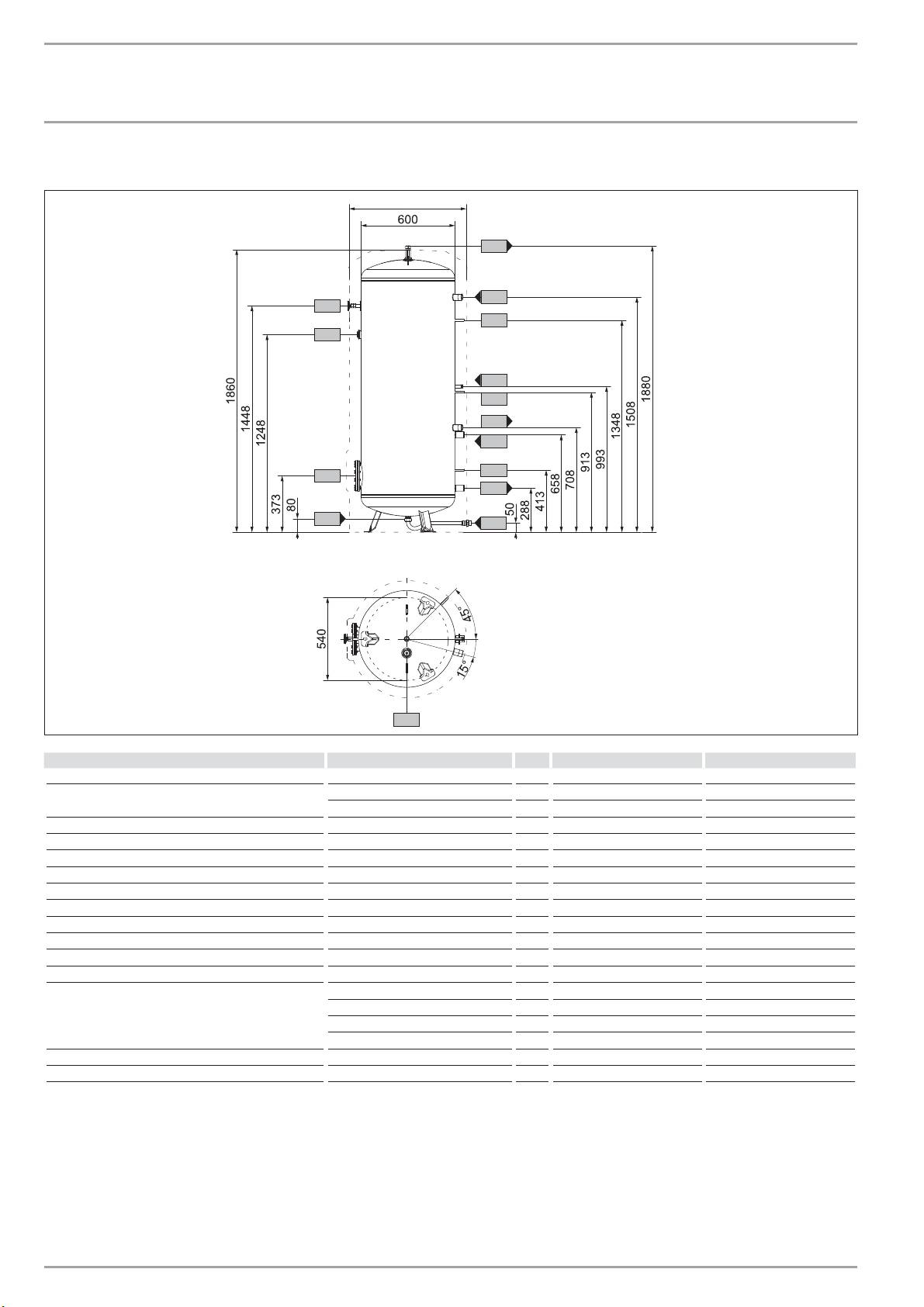
.CZ`<<`.HC
`¼äĉêńä¼|Œ¼ĉ
SBB 401 WP SOL
F
G
K
K
L
F
K
G
G
K
L
G
F
F
L
D0000017381
ZÔƃĜqTZH< ZÑƃĜqTZH<
c01 Cold water inlet Male thread G 1 A G 1 A
c03 Cold water inlet pipe
Male thread G 1 A G 1 A
Torque Nm 100 100
c06 DHW outlet Male thread G 1 A G 1 A
c10 DHW circulation Male thread G 1/2 A G 1/2 A
d07 Heat pump heating flow Female thread G 1 1/2 G 1 1/2
d08 Heat pump heating return Female thread G 1 1/2 G 1 1/2
d25 Solar flow Female thread G 1 1/2 G 1 1/2
d26 Solar return Female thread G 1 1/2 G 1 1/2
h01 Sensor heat pump flow Diameter mm 9.5 9.5
h02 Sensor heat pump return Diameter mm 9.5 9.5
h28 Sensor solar cylinder Diameter mm 9.5 9.5
h43 Thermometer Diameter mm 9.5 9.5
i01 Flange
Diameter mm 210 210
Pitch circle diameter mm 180 180
Screws M 12 M 12
Torque Nm 55 55
i07 Electric emergency/booster heater Female thread G 1 1/2 G 1 1/2
i18 Protective anode Female thread G 1 1/4 G 1 1/4
ŝŝZŗƃĜéÑƃĜqTZH< ŷŷŷĪńŒê¼¼ùé¼ùŒļĒĉĪĒă
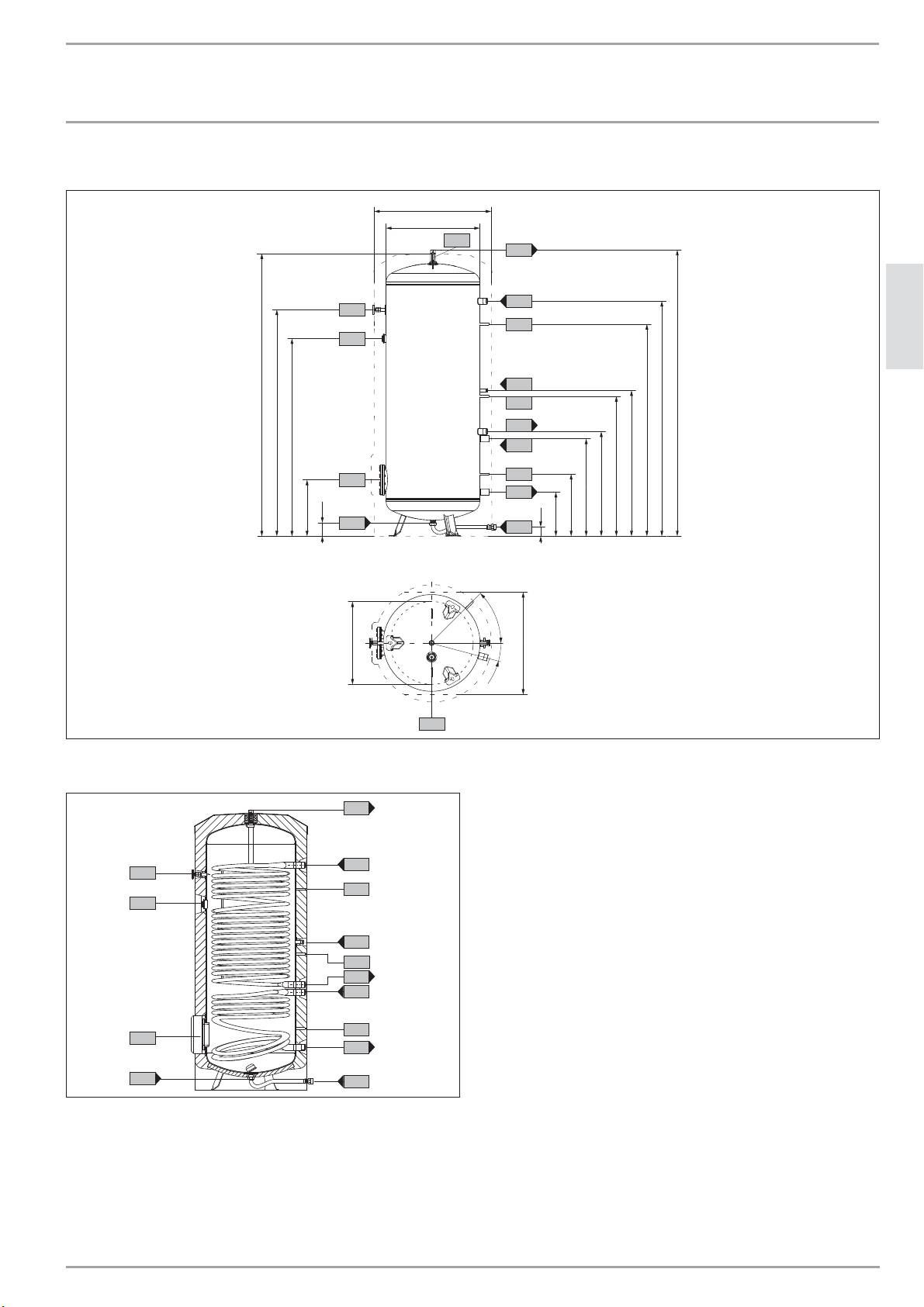
.CZ`<<`.HC
`¼äĉêńä¼|Œ¼ĉ
SBB 501 WP SOL
L
F
G
K
K
L
ENGLISH
F
K
G
G
K
L
G
F
F
L
D0000017386
SBB 401 WP SOL | SBB 501 WP SOL
F
G
K
K
L
F
K
G
G
K
L
G
F
F
26_03_20_0011
ŷŷŷĪńŒê¼¼ùé¼ùŒļĒĉĪĒă ZŗƃĜéÑƃĜqTZH<ŝŗ
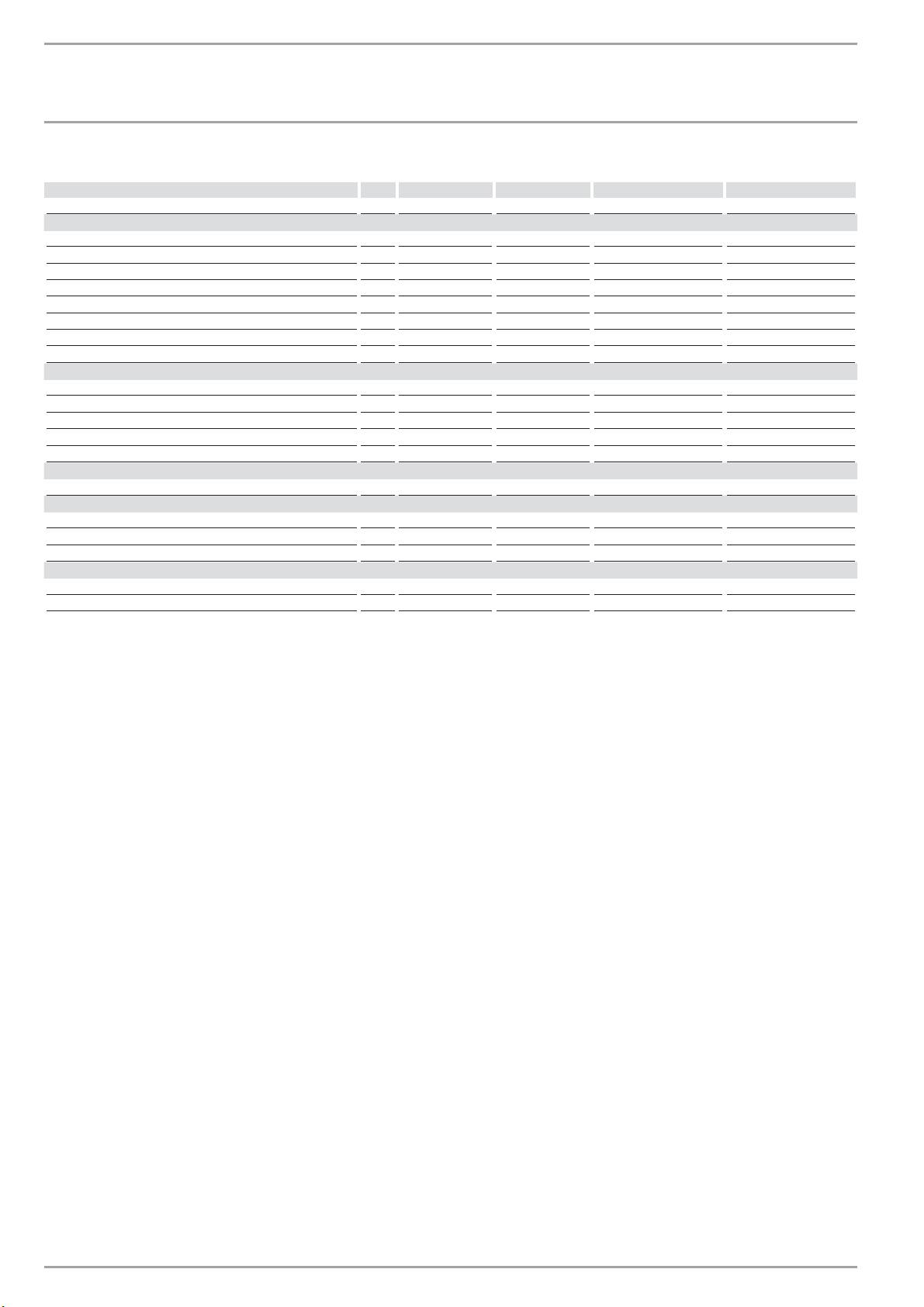
.CZ`<<`.HCqVVC`tCp.VHCBC`CVt<.C&
`¼äĉêńä¼|Œ¼ĉ
14.2 Technische Daten
ZŗƃĜqT ZŗƃŝqT ZÔƃĜqTZH< ZÑƃĜqTZH<
221360 221361 221362 227534
Hydraulic data
Nominal capacity l 300 280 400 500
Contents, indirect coil top l 20 30.1 25.1 31.3
Contents, indirect coil bottom l 8.8 8.8
Surface area, indirect coil top m² 3.2 4.8 4 5
Surface area, indirect coil bottom m² 1.4 1.4
Pressure drop at 1.0 m³/h indirect coil top hPa 37 56 47 48
Pressure drop at 1.0 m³/h indirect coil bottom hPa 17 17
Mixed water volume 40 °C (15 °C/60 °C) l 529 514 681 857
Application limits
Max. permissible pressure MPa 1 1 1 1
Test pressure MPa 1.5 1.5 1.5 1.5
Max. permissible temperature °C 95 95 95 95
Max. flow rate l/min 38 38 45 50
Max. recommended collector aperture area m² 8 10
Energetic data
Standby energy consumption/24 h at 65 °C kWh 2.1 2.1 2.3 2.3
Dimensions
Height mm 1710 1700 1875 1976
Diameter mm 700 700 750 810
Height when tilted mm 1750 1750 1930 2030
Weight
Weight (full) kg 456 464 619 660
Weight (empty) kg 156 184 219 260
Warranty
The warranty conditions of our German companies do not
apply to appliances acquired outside of Germany. In countries
where our subsidiaries sell our products, it is increasingly the
case that warranties can only be issued by those subsidiaries.
Such warranties are only granted if the subsidiary has issued
its own terms of warranty. No other warranty will be granted.
We shall not provide any warranty for appliances acquired in
countries where we have no subsidiary to sell our products.
This will not aect warranties issued by any importers.
Environment and recycling
We would ask you to help protect the environment. After use,
dispose of the various materials in accordance with national
regulations.
ŝÔZŗƃĜéÑƃĜqTZH< ŷŷŷĪńŒê¼¼ùé¼ùŒļĒĉĪĒă