Xylem e-NSCS: 2 Transportation and Storage
2 Transportation and Storage: Xylem e-NSCS
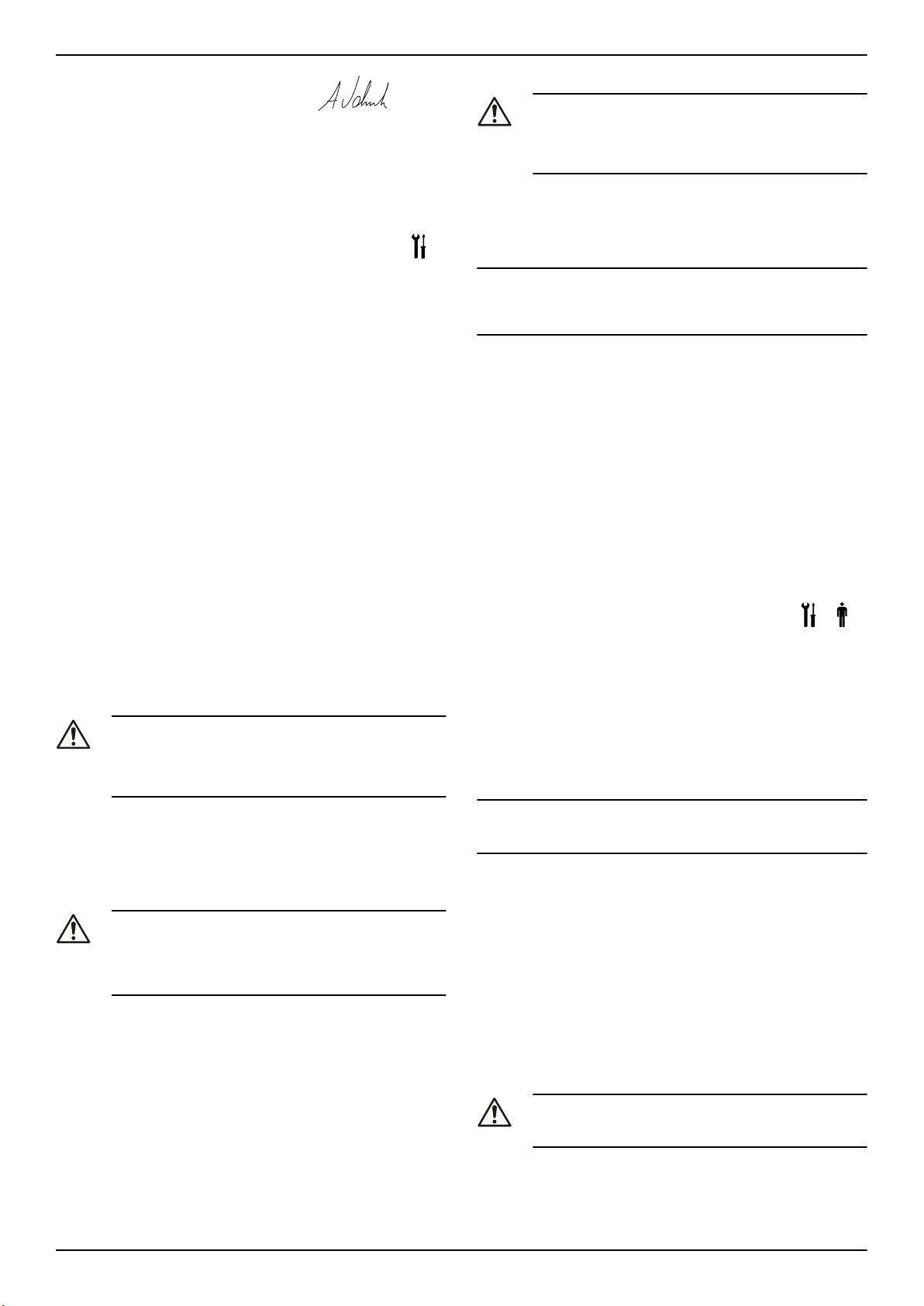
en - Translation of the original instructions
MONTECCHIO MAGGIORE,
Unit without motor
XX.04.2014
WARNING:
AMEDEO VALENTE
A pump and motor that are purchased separately and then
(DIRECTOR OF ENGINEERING AND R&D)
coupled together results in a new machine under the Machi-
rev.01
nery directive 2006/42/EC. The person making the coupling
is responsible for all safety aspects of the combined unit.
Lowara is a trademark of Xylem Service Italia S.R.L., subsidiary of Xy-
2.3 Storage guidelines
lem Inc.
Storage location
The product must be stored in a covered and dry location free from
2 Transportation and Storage
heat, dirt, and vibrations.
2.1 Inspect the delivery
NOTICE:
• Protect the product against humidity, heat sources, and mechani-
1. Check the outside of the package for evident signs of damage.
cal damage.
2. Notify our distributor within eight days of the delivery date, if the
• Do not place heavy weights on the packed product.
product bears visible signs of damage.
Unpack the unit
2.3.1 Long-term storage
1. Follow applicable step:
If the unit is stored for more than 6 months, these requirements apply:
• If the unit is packed in a carton, then remove the staples and
• Store in a covered and dry location.
open the carton.
• Store the unit free from heat, dirt, and vibrations.
• If the unit is packed in a wooden crate, then open the cover
• Rotate the pump shaft by hand several times at least every three
while paying attention to the nails and straps.
months.
Treat bearings and machined surfaces so that they are well preserved.
2. Remove the securing screws or the straps from the wooden base.
Refer to the drive unit and coupling manufacturers for their long-term
2.1.1 Inspect the unit
storage procedures.
For questions about possible long-term storage treatment services,
1. Remove packing materials from the product.
please contact your local sales and service representative.
Dispose of all packing materials in accordance with local regula-
tions.
Ambient temperature
2. Inspect the product to determine if any parts have been damaged
The product must be stored at an ambient temperature from -5°C to
or are missing.
+40°C (23°F to 104°F).
3. If applicable, unfasten the product by removing any screws, bolts,
or straps.
For your personal safety, be careful when you handle nails and
3 Product Description
straps.
4. Contact the local sales representative if there is any issue.
3.1 Pump design
The pump is a horizontal single stage pump with volute casing close
2.2 Transportation guidelines
coupled to standard electric motors. The pump can be used for han-
dling:
Precautions
• Cold or warm water
WARNING:
• Clean liquids
• Aggressive liquids which are not chemically and mechanically ag-
• Observe accident prevention regulations in force.
gressive to the pump materials.
• Crush hazard. The unit and the components can be
heavy. Use proper lifting methods and wear steel-toed
The product can be supplied as a pump unit (pump and electric motor)
shoes at all times.
or only as a pump.
Check the gross weight that is indicated on the package in order to se-
NOTICE:
lect proper lifting equipment.
If you have purchased a pump without motor, make sure that the motor
is suitable for coupling to the pump.
Position and fastening
The pump or pump unit can be transported only horizontally. Make
Intended use
sure that the pump or pump unit is securely fastened during transpor-
The pump is suitable for:
tation and cannot roll or fall over.
• Water supply and water treatment
WARNING:
• Cooling and hot water supply in industries and building services
Do not use eyebolts screwed on the motor for handling the
• Filter systems, and so on.
whole electric pump unit.
• Irrigation and sprinkler systems
• Drainage systems
Do not use the shaft end of the pump or of the motor to han-
• Heating systems
dle the pump, the motor or the unit.
• Condensate transportation
• Eyebolts screwed onto the motor may be exclusively used to han-
Additional uses for optional material:
dle the individual motor or, in case of a not balanced distribution
• District heating
of weights, to partially lift the unit vertically starting from a horizon-
• General industry
tal displacement.
• Food and beverage industry
Pump unit must always be fixed and transported as shown in Figure 4 ,
and the pump without motor must be fixed and transported as shown
Improper use
in Figure 5 .
WARNING:
• Remove cover plates 681 from drive lantern 341 and cross the
lifting tackles. To transport the pump/pump set suspend it from the
Improper use of the pump may create dangerous conditions
lifting tackle as shown.
and cause personal injury and damage to property.
An improper use of the product leads to the loss of the warranty.
Examples of improper use:
e-nscs Installation, Operation, and Maintenance Manual 13

en - Translation of the original instructions
• Liquids not compatible with the pump construction materials
Standard/
Material
Material
EN733
Extension
• Hazardous liquids (such as toxic, explosive, flammable, or corro-
Optional
code
casing/
range
range
sive liquids)
impeller
32–125 to
200–250,
• Potable liquids other than water (for example, wine or milk)
150-400
200–315,
Examples of improper installation:
250–315
• Hazardous locations (such as explosive, or corrosive atmos-
Standard CC Cast iron /
X
pheres).
Cast Iron
• Location where the air temperature is very high or there is poor
ventilation.
Standard CB Cast Iron /
X
• Outdoor installations where there is no protection against rain or
Bronze
freezing temperatures.
Standard CN Cast Iron /
X
DANGER:
Stainless
Do not use this pump to handle flammable and/or explosive
Steel
liquids.
Standard DC Ductil Iron /
X
Cast Iron
NOTICE:
Standard DB Ductil Iron /
X
• Do not use this pump to handle liquids containing abrasive, solid,
Bronze
or fibrous substances.
• Do not use the pump for flow rates beyond the specified flow
Standard DN Ductil Iron /
X
rates on the data plate.
Stainless
Steel
Special applications
Standard NN Stainless
X
Contact the local sales and service representative in the following cas-
Steel / Stain-
es:
less Steel
• If the density and/or viscosity value of the pumped liquid exceeds
Optional RR Duplex / Du-
X X
the value of water, such as water with glycol; as it may require a
plex
more powerful motor.
• If the pumped liquid is chemically treated (for example softened,
deionized, demineralized etc.).
3.6 Mechanical seal
• Any situation that is different from the ones that is described and
Unbalanced single mechanical seal acc. EN 12756, version K Dimen-
relate to the nature of the liquid.
sions. See Table 10 .
3.2 Pump description
3.7 Application limits
See Figure 6 for an explanation of the description code for the pump
and one example.
Maximum working pressure
This flow chart shows the maximum working pressure depending on
3.3 Nameplate
the pump model and the temperature of the pumped liquid.
The nameplate is a metal label that is located on the bearing bracket.
The name plate lists key product specifications. For more information,
see Figure 7
The nameplate provides information regarding the impeller and casing
material, the mechanical seal and their materials. For more informa-
tion, see Figure 8 .
IMQ or TUV or IRAM or other marks (for electric pump only)
Unless otherwise specified, for products with a mark of electrical-relat-
ed safety approval, the approval refers exclusively to the electrical
pump.
3.4 Design structure
• Dimensions according EN 733 and additional not standardized
extension sizes
• Volute casing pump with back pull out power end
• Single stage
P
1max
+ P
max
≤ PN
• For horizontal assembly
P
1max
Maximum inlet pressure
Part
Description
P
max
Maximum pressure generated by the pump
Casing • Radial split volute casing with radial discharge
PN Maximum operating pressure
• Replaceable wear ring
Liquid temperature intervals
Impeller • Closed radial impeller with wear rings on both
sides
Version
Gasket Minimum Maximum
Shaft seal • Single mechanical seal acc. EN 12756
Standard EPDM -20°C (-4°F) 140°C (284°F)
• Optional cartridge mechanical seal
Optional FPM (FKM) -10°C (14°F) 90°C (194°F)
Bearings • Radial ball bearings of motor
• Grease lubrication
For special requirements, contact the Sales and Service Department.
See the sectional drawing Figure 9 .
Maximum number of starts per hour
3.5 Material
kW
0.25 -
4.00 -
11 - 22 30 - 37 45 - 75 90 – 160
The metallic parts of the pump that come in contact with water are
3.00
7.50
made of the following:
Starts
60 40 25 16 8 4
per hour
Noise level
See the measuring surface sound pressure levels L
pA
in Table 11 .
14 e-nscs Installation, Operation, and Maintenance Manual
Оглавление
- 1 Introduzione e sicurezza
- 2 Movimentazione e stoccaggio
- 4 Installazione
- 5 Messa in funzione, avvio,
- 7 Risoluzione dei problemi
- 1 Introduction and Safety
- 2 Transportation and Storage
- 4 Installation
- 5 Commissioning, Startup,
- 6 Maintenance
- 1 Introduction et sécurité
- 2 Transport et stockage
- 4 Installation
- 5 Contrôle de réception,
- 7 Recherche des pannes
- 1 Einführung und Sicherheit
- 2 Transport- und Lagerung
- 4 Montage
- 5 Inbetriebnahme, Anfahren,
- 6 Wartung
- 7 Fehlerbehebung
- 1 Giriş ve Güvenlik
- 2 Taşıma ve Depolama
- 4 Montaj
- 5 Devreye alma, Başlatma,
- 6 Bakım
- 1 Подготовка и техника
- 2 Транспортирование и
- 4 Установка
- 5 Ввод в эксплуатацию, запуск,
- 7 Устранение