Wilo Drain TM 25_6: Installation and operating instructions
Installation and operating instructions: Wilo Drain TM 25_6
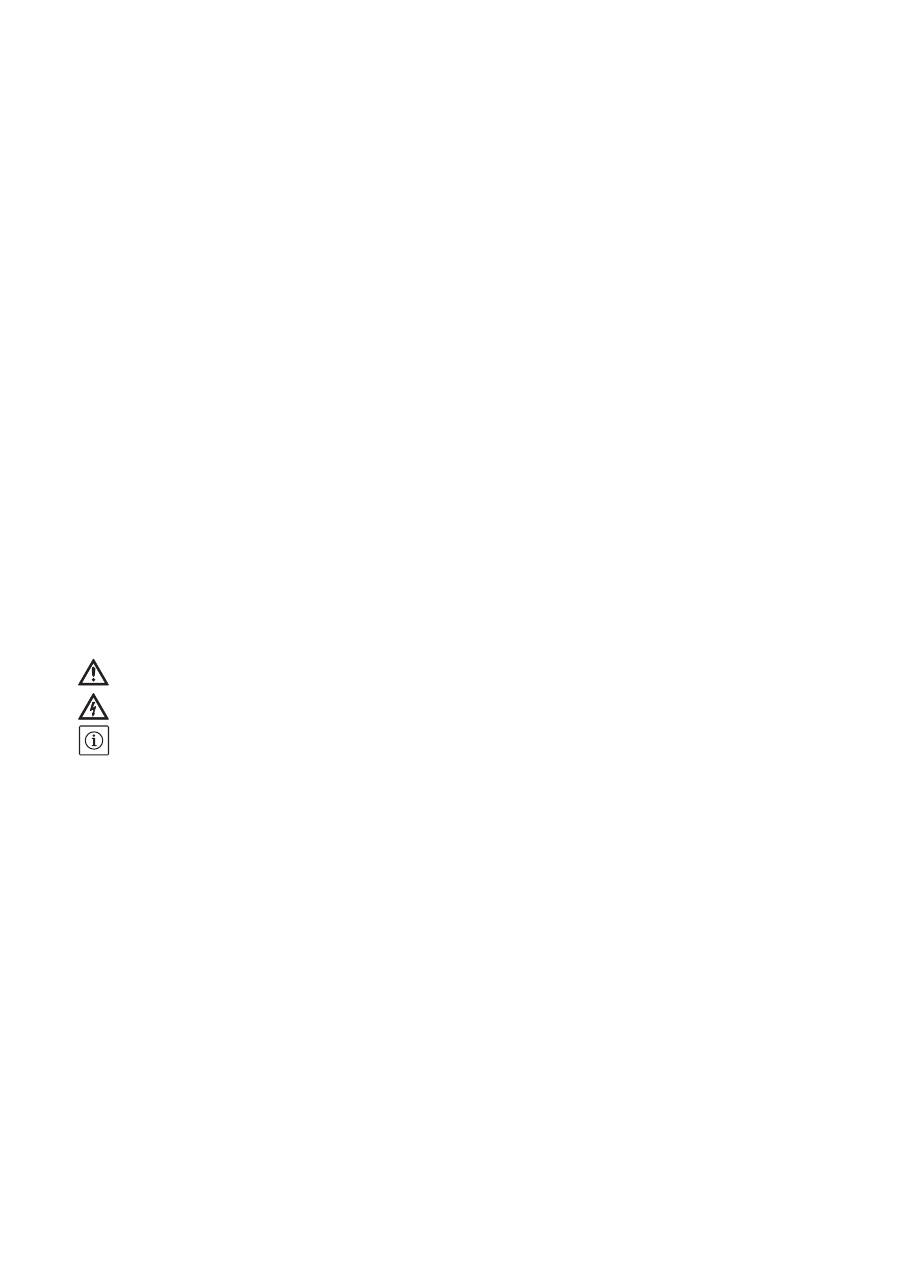
English
8
WILO AG 10/2006
Installation and operating instructions
1 General
1.1 About this document
These Installation and Operating Instructions are
an integral part of the product. They must be kept
readily available at the place where the product is
installed. Strict adherence to these instructions is
a precondition for the proper use and correct
operation of the product.
These Installation and Operating Instructions cor-
respond to the relevant version of the product and
the underlying safety standards valid at the time
of going to print.
2 Safety
These operating instructions contain basic infor-
mation which must be adhered to during installa-
tion and operation. For this reason, these
operating instructions must, without fail, be read
by the service technician and the responsible
operator before installation and commissioning .
It is not only the general safety instructions listed
under the main point "safety" that must be
adhered to but also the special safety instructions
with danger symbols included under the following
main points .
2.1 Designation of information in the operating
instructions
Symbols:
General danger symbols
Danger due to electrical voltage
NOTE: ...
Signal words:
DANGER!
Acutely dangerous situation.
Non-observance results in death or the most
serious of injuries.
WARNING!
The user can suffer (serious) injuries. 'Warning'
implies that (serious) injury to persons is proba-
ble if this information is disregarded.
CAUTION!
There is a risk of damaging the pump/unit.
'Caution' implies that damage to the product is
likely if the information is disregarded.
NOTE:
Useful information on using the product. It draws
attention to possible problems.
2.2 Personnel qualifications
The installation personnel must have the appro-
priate qualification for this work.
2.3 Danger in event of non-observance of the
safety instructions
Non-observance of the safety instructions can
result in risk of injury to persons and damage to
pump/unit. Non-observance of the safety
instructions can result in the loss of any claims to
damages.
In detail, non-observance can, for example, result
in the following risks :
• Failure of important pump/unit functions,
• Failure of required maintenance and repair proce-
dures
• Danger to persons from electrical, mechanical and
bacteriological influences,
• Property damage
2.4 Safety instructions for the operator
The existing directives for accident prevention
must be adhered to.
Danger from electrical current must be eliminated.
Local directives or general directives [e.g. IEC, VDE
etc.] and local power supply companies must be
adhered to.
2.5 Safety instructions for inspection and
installation work
The operator must ensure that all inspection and
installation work is carried out by authorised and
qualified personnel, who are sufficiently informed
from their own detailed study of the operating
instructions.
Work to the pump/unit must only be carried out
when at a standstill.
2.6 Unauthorised alteration and spare part
production
Alterations to the pump/unit are only permissible
after consultation with the manufacturer. Original
spare parts and accessories authorised by the
manufacturer ensure safety. The use of other
parts can nullify the liability from the results of
their usage.
2.7 Unacceptable operating modes
The operating safety of the supplied pump/unit is
only guaranteed for conventional use in accord-
ance with Section 4 of the operating instructions.
The limit values must on no account fall under or
exceed those specified in the catalogue/data
sheet.
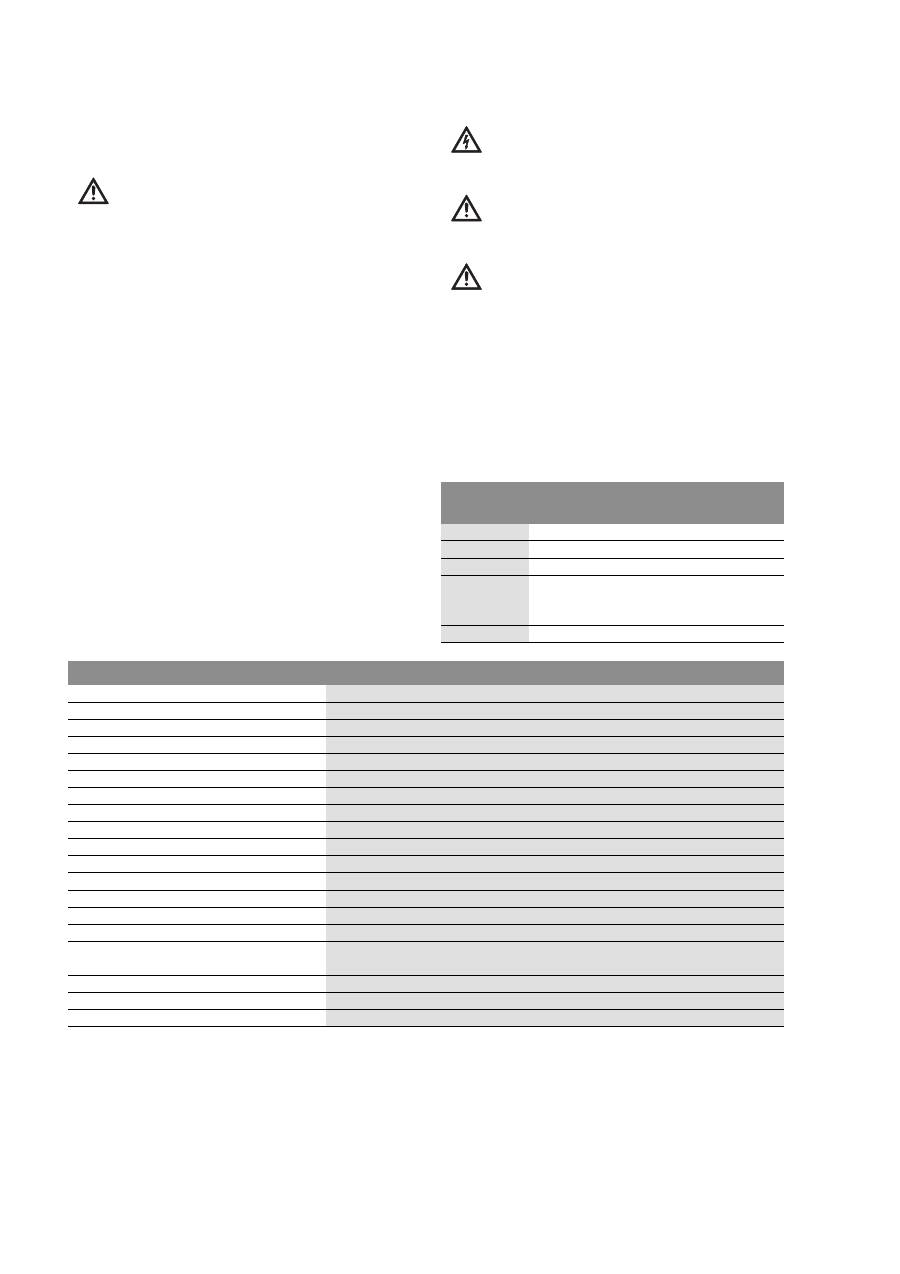
English
Installation and operating instructions Wilo-Drain TM 25/6
9
3 Transport and interim storage
On receipt of the product immediately check for
transport damage. If damage has occurred, take
the necessary steps, within the defined periods,
with the transport company.
CAUTION! Danger of material damage!
There is a danger of damage if the product is
incorrectly handled during transport or storage.
• For transport, the pump may only be lifted or
carried using the brackets intended for that pur-
pose. The cable should never be used for lifting!
• During transport and temporary storage, the
pump must be protected from moisture, from
frost and from mechanical damage.
4 Intended use
The Wilo-Drain-TM submersible pumps are used
• to automatically drain pits and shafts („TM...A“),
• to keep out buildings and cellars at risk of flooding
dry,
• to lower surface water,
so far that waste water can't flow into the sewage
system via a natural gradient.
The pumps are suitable for slightly soiled water,
rainwater containing solids of max.
∅
3 mm and
suds.
The pumps are usually installed flooded
(immersed) and can only be installed vertically,
whether fixed or mobile.
Submersible motor pumps with connection lines
of less than 10 m are only approved (according to
EN 60335) for use within buildings, not for out-
door use.
WARNING! Risk of fatal injury!
The pump may not be used to empty swimming
pools / garden ponds or similar locations if there
are people in the water.
WARNING! Health risk!
Owing to the materials used, the pumps are not
suitable for drinking water! Polluted waste
water presents a health risk.
CAUTION! Danger of material damage!
Pumping materials which are not approved can
lead to damage to the product.
The pumps are not suitable for water containing
coarse impurities such as sand, fibres or faeces,
flammable liquids or for use in areas at risk of
explosion.
5 Details about the product
5.1 Type key
5.2
Technical data
5.3 Scope of delivery
Every pump is delivered with
• 5/10 m connection cable,
• a mains power plug,
• connected float switch („TM...-A“),
• hose connection (in steps Ø 20, 25 mm, R1“),
• coupling (Rp 1 / Rp 1¼) with integrated non-
return valve,
• installation and operating instructions.
5.4 Accessories
Accessories must be ordered separately (see cat-
alogue)
Examples:
TM 25/6 A 5MKA, TM 25/6 5MKA
TM 25/6 A 10MKA, TM 25/6 10MKA
TM
series: submersible pump
25
nominal diameter of the pressure port [mm]
/6
max. head of water [m] for Q=0m³/h
A
A = with float switch
- = not specified:
no float switch
10M KA
length of connection cable [m]: 5, 10
max. permissible grain size:
3 mm
supply voltage:
1~ 230 V, ± 10 %,
supply frequency:
50 Hz
protection class:
IP 68
speed:
max. 2900 ¹/min (50 Hz)
max. current consumption:
0,8 A
power consumption P
1
:
0,18 kW
nominal motor power P
2
:
0,1 kW
max. flow rate:
see name plate
max. head of water:
see name plate
operating mode S1:
200 hours of operation per year
operating mode S3 (optimum):
intermittent duty, 25 % (2.5 min. operation, 7.5 min. pause)
recommended switching frequency:
20 times/h
max. starts per hour:
50 times/h
nominal diameter of the pressure port:
25 mm
permissible temperature range of the
pumped liquid:
+3 to 35°C
max. immersion depth:
5 m
level suction to
5 mm
noise level at min. level
< 57 db(A)

English
10
WILO AG 10/2006
6 Description and function
6.1 Description of the pump (Fig. 2)
The pump can be completely immersed in the liq-
uid to be pumped. The pump housing is made of
plastic. The electric motor is protected from the
pump cavity by a shaft seal ring sealing the oil
cavity and by a mechanical seal which seals the oil
cavity from the water. To ensure that the
mechanical seal is always lubricated and cooled,
even when running dry, the mechanical seal
chamber is filled with oil.
The motor is cooled by the surrounding fluid.
The motor is equipped with integrated motor pro-
tection, which switches off on overload and auto-
matically switches on again after cooling down.
The pump is installed on the base of a shaft. When
in a fixed installation it is screwed to a fixed pres-
sure line. For a mobile installation it is connected
to a hose.
The pump is operated by plugging in the power
supply plug.
If the waste water line does not allow any inter-
ruptions, then a 2nd pump (automatic standby
pump) in conjunction with the necessary switch-
gear (accessories) increases the reliability in case
of a fault with the 1st pump.
6.2 The pump functions
Pump with a float switch:
The „TM...-A“ (Fig. 1) pumps work automatically
in that a float switch turns the pump on, via the
free cable length, once the water reaches a certain
level and turns it off again when it reaches a min-
imum water level.
Pump without a float switch:
The versions without a float switch are suitable for
use with external switching, for example using
switchgear (accessories). Level suction to 5 mm
(Fig. 1).
7 Installation and electrical connection
DANGER! Risk of fatal injury!
Improper installation and improper electrical
connections can result in a risk of fatal injury.
• The installation and electrical connections
should only be done by properly skilled staff and
in compliance with applicable regulations!
• Follow all accident prevention regulations!
7.1 Installation
The pump was deigned both for fixed and for
mobile installation.
CAUTION! Danger of material damage!
Danger of damage due to improper handling.
Lift the pump using a chain or a rope attached to
the handle. Never lift using the power / float
switch cable or on the pipe / hose connection.
The installation site and shaft for the pump must
be frost-free. The shaft must be such that the
float switch („TM...-A“) is guaranteed free move-
ment. The diameter of the pressure pipe (pipe /
hose connection) may not be less than the diame-
ter of the pump's pressure port. To avoid loss of
pressure, make the pipe connection one size
larger.
Connection of the pressure pipe
•
Pipe connection:
For a fixed pump installation, we
recommend the use of the coupling supplied (Rp
1 / Rp 1¼) with an integrated non-return valve.
Seal the pipe connections to the pump pressure
port with Teflon tape. Constant leaks in this area
lead to the destruction of the non-return valve
and the screwed connection.
To prevent any flow back from the public sewer,
the pressure pipe should be arched so as to pass
above the locally determined backflow level (usu-
ally street level).
•
Hose connection:
The hose nozzle enables a hose
(Ø 20 or 25 mm) to be connected. The diameter of
the hose nozzle may have to be adapted by cut-
ting off the upper part to correspond to the diam-
eter of the hose.
With a mobile installation, the pump should be
secured in the shaft concerned to prevent it from
falling over or wandering off. (e.g. fix the chain
with a small amount of tension).
NOTE: When used in a pit without a firm base, the
pump must be put on a sufficiently large plate or
hung from a rope or a chain in a suitable position.
Pos.
Description of component
1
housing
2
stator (winding)
3
handle
4
sheet metal screw
5
O-ring
6
sheet metal screw
7
radial shaft sealing ring
8
mechanical seal
9
O-ring
10
cover plate
11
seal housing
12
screw
13
seal
14
O-ring
15
shaft seal ring
16
O-ring
17
pump housing
18
spacing ring
19
impeller
20
suction basket
21
washer
22
spring washer
23
nut
25
connection cable
26
hose nozzle Ø 20, 25 mm
27
seal
28
float switch
29
coupling
30
non-return valve
31
fixing for non-return valve

English
Installation and operating instructions Wilo-Drain TM 25/6
11
7.2 Electrical connection
DANGER! Risk of fatal injury!
If the electrical connection is not made properly,
there is a risk of fatal injury from an electric
shock.
The electrical connection must be made by an
electrician approved by the local energy supply
company in compliance with the applicable local
regulations [e.g. VDE regulations].
• The type of power supply and its voltage must
correspond to the specifications on the name
plate,
• Fuse in the power supply: 10 A, slow blow,
• Earth the system as required by regulations,
• We recommend the installation of a protective
residual current device (RCD) with a trip current of
< 30 mA (this is mandatory, when used outdoors!).
• To connect the pump to switchgear, the power
supply plug has to be cut off and the connection
cable then has to be wired as follows:
The power socket or switchgear must be installed
in a dry space that can not be flooded.
8 Commissioning
CAUTION! Risk of damage to the pump!
The pump must not run dry. Running dry
shortens the life of the motor and of the
mechanical seal.
You must ensure that the float switch is com-
pletely free to move (TM...-A). You must ensure
that the float switch is completely free to move.
Adjusting the switch level of the float switch
The switching level (point to switch on/off) can be
adjusted by sliding the cable to the float switch
within the holding ring.
If necessary, water can be pumped away to a level
of at least 5 mm by manually lifting the float
switch.
The inward flow of water in the shaft should not
be aimed directly at the pump's suction basket.
This can cause air bubbles to be introduced into
the pump, preventing the pump from working
properly when starting.
The maximum flow rate into the shaft must not
exceed the maximum pump flow rate. Observe the
shaft closely during the commissioning.
9 Maintenance
WARNING! Danger of electric shock!
Dangers from electrical energy must be elimi-
nated
• For all maintenance and repair work on the
pump, it must be electrically isolated and unau-
thorised switch-on must be prevented.
• Any damage to the connection cable must
always be repaired by a properly qualified elec-
trician.
To prevent the pump from seizing, owing to
longer periods of disuse, its proper working should
be checked at regular intervals (every 2 months)
by manually lifting the float switch or by directly
switching it on, to let the pump run briefly.
Even a small amount of wear on the shaft seal ring
or the mechanical seal can lead to pollution of the
pumped liquid, owing to oil leaking from the oil
chamber.
The encapsulated motor may only be opened by
specialist companies or by Wilo customer service.
9.1 Cleaning the pump
Depending on how the pump is used, impurities
can be deposited within the suction basket or
impeller. After use, wash the pump down under
running water.
1. Remove the power. Remove the power plug!
2. Empty the pump
3. The suction basket snaps into the pump hous-
ing. Use a screwdriver to push the catches
back and remove the suction basket.
4. Clean the basket under running water.
5. Undo the 4 screws on the lower part of the
pump housing and remove the housing. Take
care with the O-ring between the pump hous-
ing and the motor housing.
6. Clean the impeller and pump housing under
running water. The impeller must turn freely.
7. Damaged or worn parts must be replaced with
original spare parts.
8. Reassemble the pump in the reverse order.
Wire:
Terminal
brown
L1
blue
N
green/yellow
PE
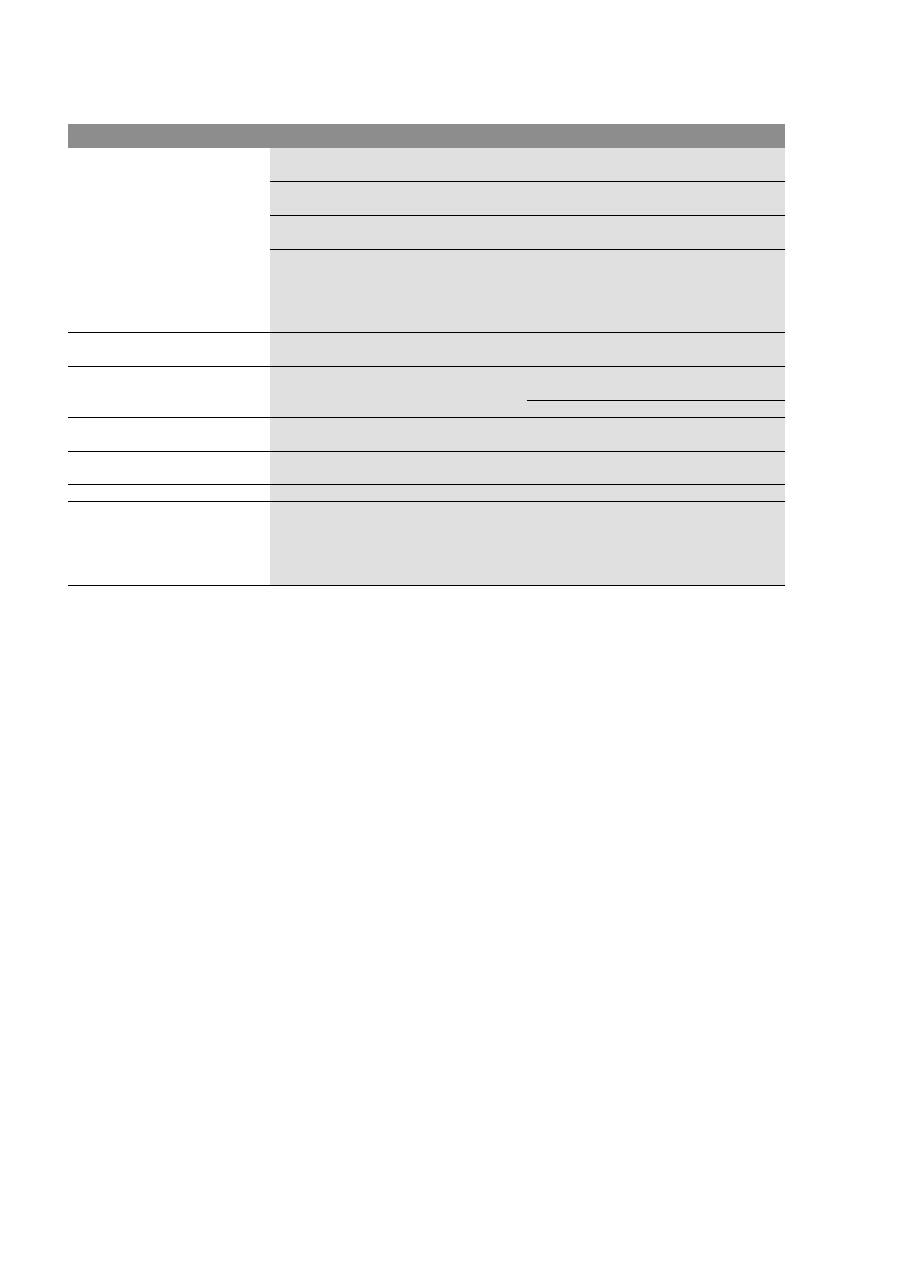
English
12
WILO AG 10/2006
10 Faults, their causes and remedies
If the fault can't be fixed, please contact your
local specialist or your nearest Wilo customer
service location or representative.
11 Spare parts
Spare parts can be ordered from your local spe-
cialist and/or via Wilo
customer service.
To avoid queries and incorrect orders, always pro-
vide all of the details on the name plate with every
order.
We reserve the right to make technical changes!
Fault
Cause
Remedy
The pump won't start or stops
during operation
Interruption to the power
Check fuses, cables and electrical connec-
tions
Motor protection switch has tripped
Allow the pump to cool down; it will restart
automatically
The temperature of the pumped liquid is too
high
Allow to cool down
Pump is silted up or seized
Remove power from the pump and pull it
out of the shaft
Remove the suction basket and wash down
the suction basket and impeller under run-
ning water
The pump doesn't turn on/off
Float switch is jammed or cannot move
freely
Check the float switch and make sure that it
can move freely
The pump doesn't pump properly
Air in the system can't escape
Bleed air from the system, emptying if nec-
essary
Check the switch off level
The water level is below the suction opening If possible, submerse the pump more deeply
(note switch-off level)
The non-return valve in the pump port is
sticking
Check that it is working properly
Kink in the hose / Stop valve closed
Unkink the hose / open the stop valve
The flow rate decreases during
operation
The suction basket is blocked / the impeller
is jammed
Remove power from the pump and pull it
out of the shaft
Dismantle the suction basket / centrifugal
device, wash down suction basket / impeller
under running water.
Оглавление
- Einbau- und Betriebsanleitung
- Installation and operating instructions
- Notice de montage et de mise en service
- Instrucciones de instalación y funcionamiento
- Istruzioni di montaggio, uso e manutenzione
- Manual de instalação e funcionamento
- Montaj ve kullanma k ı lavuzu
- Οδηγίες εγκατάστασης και λειτουργίας
- Monterings- och skötselanvisning
- Asennus- ja käyttöohje
- Monterings- og driftsvejledning
- Beépítési és üzemeltetési utasítás
- Instrukcja montażu i obsługi
- Návod k montáži a obsluze
- Инструкция по монтажу и эксплуатации
- Paigaldus- ja kasutusjuhend
- Instalē anas un ekspluatācijas instrukcijas
- Montavimo ir naudojimo instrukcija
- Návod na montáž a obsluhu
- Navodila za vgradnjo in vzdrževanje
- Instrucþiuni de montaj ºi exploatare
- Инструкция за монтаж и експлоатация
- TM 25
- EN 809, EN 12050-2, EN 12050-4, EN 60034-1, EN 60204-1 EN 60335-2-41, EN 61000-6-3, EN 61000-6-4.
- Wilo – International
- Wilo-Vertriebsbüros