Labconco VACUUBRAND Diaphragm Pump 7393000: Safety information!
Safety information!: Labconco VACUUBRAND Diaphragm Pump 7393000
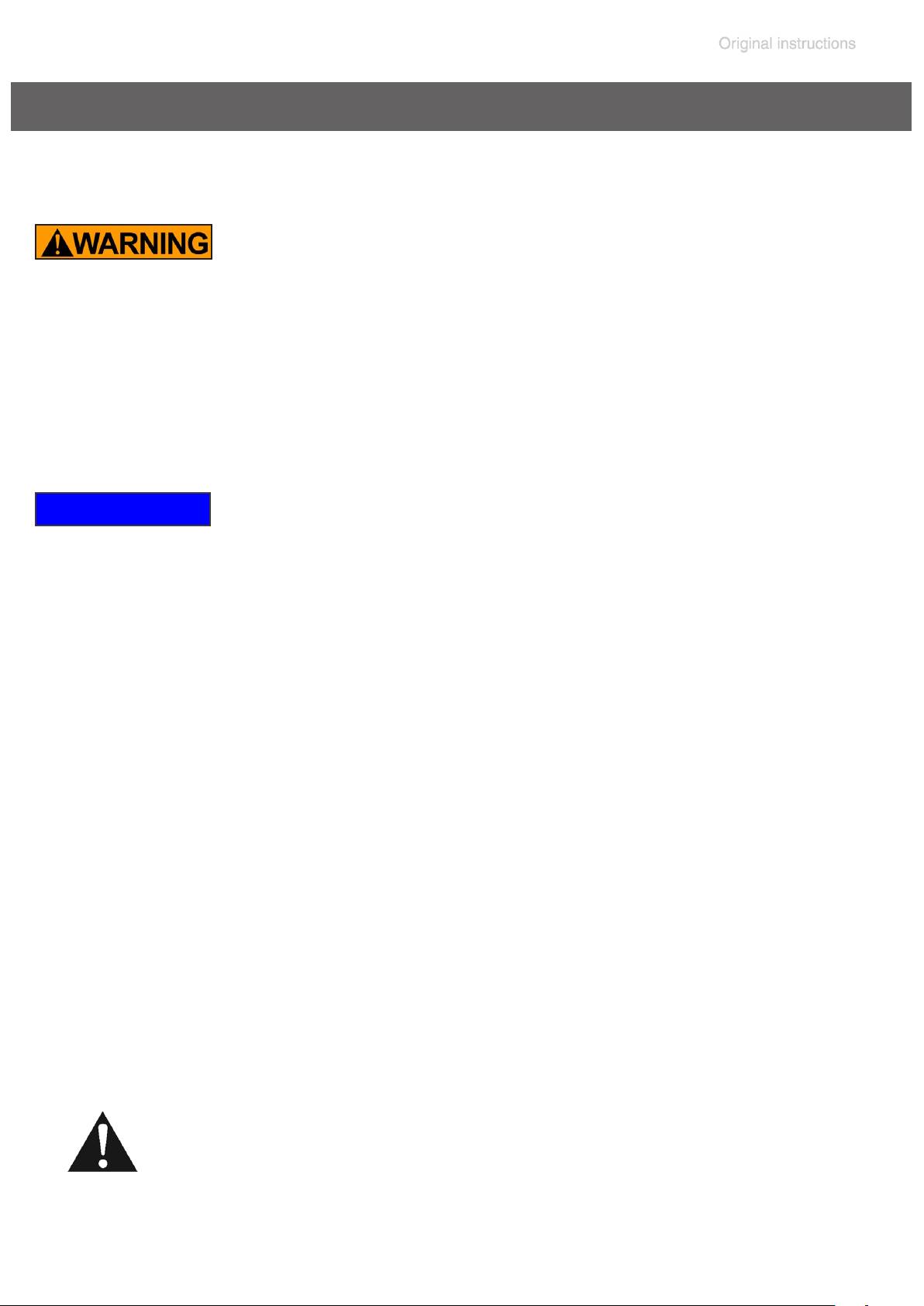
page 9 of 74
Safety information!
Important information!
+ Keep this manual complete and accessible to per-
sonnel at all times!
+ Read this manual carefully before installing or op-
erating the equipment. Observe the instructions
contained in this manual.
+ Do not modify the equipment without authoriza-
tion.
This manual is an integral part of the equipment de-
NOTICE
scribed therein. It describes the safe and proper use
of the vacuum pump.
Make operating personnel aware of dangers arising
from the pump and the pumped substances.
VACUUBRAND disclaims any liability for inappropri-
ate use of these pumps and for damage from failure
to follow instructions contained in this manual.
This manual is only to be used and distributed in its com-
plete and original form. It is strictly the users’ responsibility
to check carefully the validity of this manual with respect
to his product.
Manual-no.: 999156 / 02/14/2012
The following signal word panels and safety
symbols are used throughout this manual:
This is the safety alert symbol. It is used to alert you to po-
tential personal injury hazards. Obey all safety messages
that follow this symbol to avoid possible injury and death.
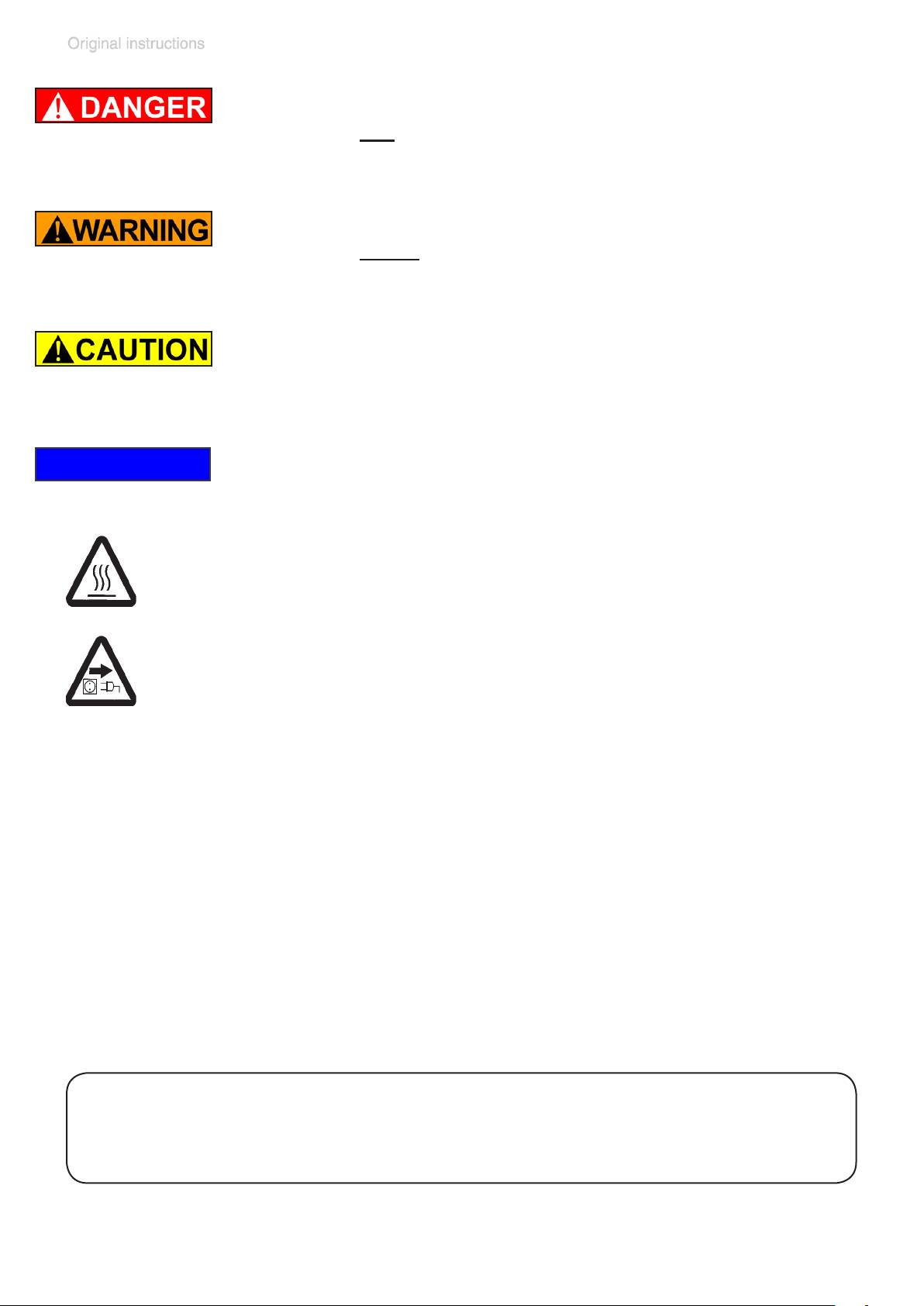
page 10 of 74
➨ DANGER indicates a hazardous situation which, if not
avoided, will result in death or serious injury.
+ WARNING indicates a hazardous situation which, if not
avoided, could result in death or serious injury.
• CAUTION indicates a hazardous situation which, if not
avoided, could result in minor or moderate injury.
NOTICE is used to address practices not related to per-
NOTICE
sonal injury.
Caution! Hot surface!
Disconnect equipment from AC power.
Formatting used in this manual:
Note: The signal word panels in all sections of this manual always refer
to all paragraphs of the same format (➨ / + / • / plain text) following each
signal word panel.
The document ”Safety information for vacuum equipment” is
part of this manual! Read the ”Safety information for vacuum
equipment” and observe the instructions contained therein!
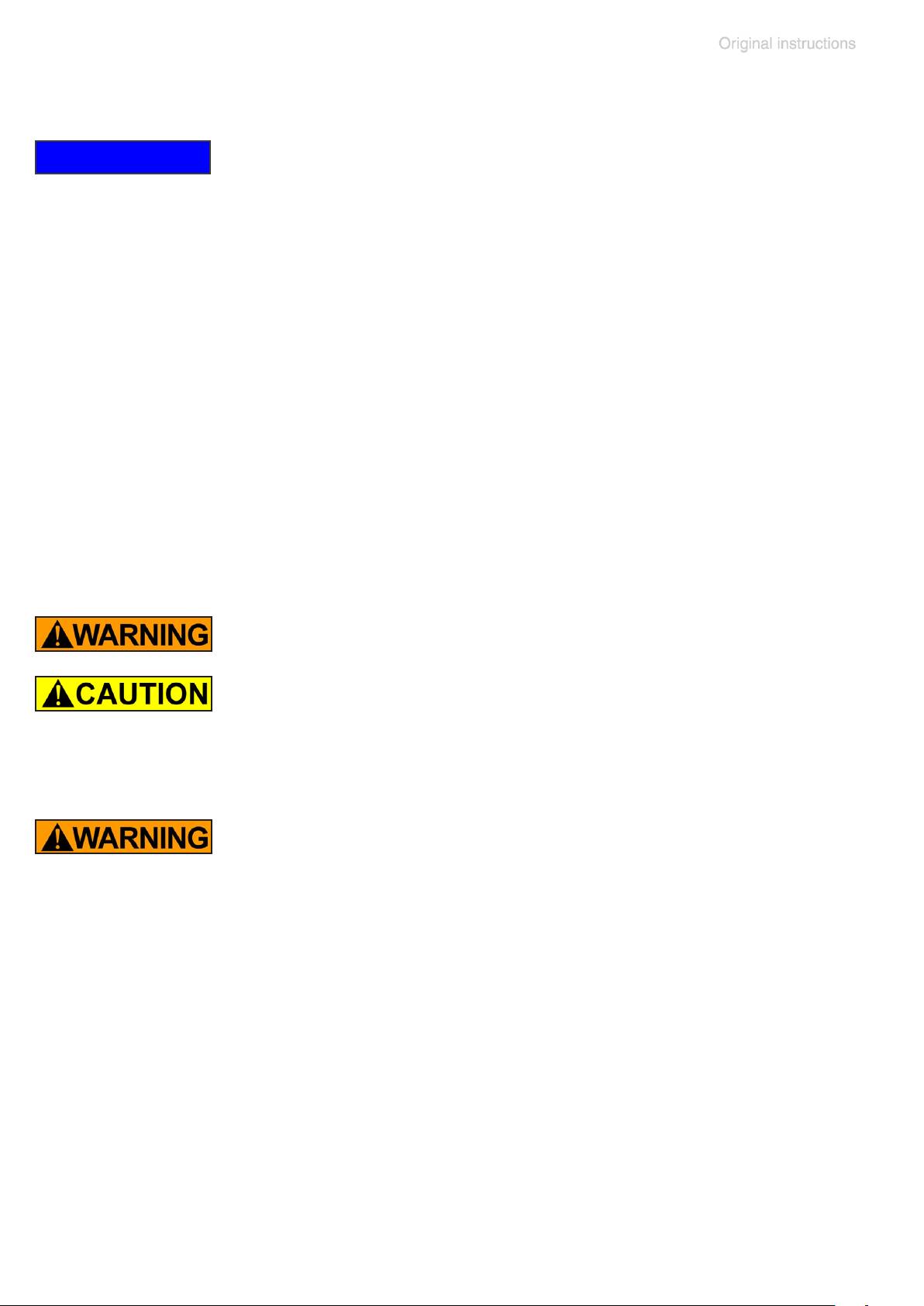
page 11 of 74
General information
Remove all packing material from the packing box. Re-
NOTICE
move the product from its packing-box and retain all pack-
aging until the equipment is inspected and tested. Re-
move the protective caps from the inlet and outlet ports
and retain for future use. Inspect the equipment promptly
and carefully.
If the equipment is damaged, notify the supplier and the
carrier in writing within three days. Retain all packing ma-
terial for inspection. State the item number of the product
together with the order number and the supplier’s invoice
number. Failure to check and give notice of damage will
void any and all warranty claims for those deciencies.
Replace the protective caps, if the equipment is not used
immediately. Store the equipment in dry and non-corrosive
conditions (see also ”Technical data”, pg. 24).
+ Do not use any damaged equipment.
• Use the mounted handle when moving the pump.
Intended use
+ Do not use the pump or any system parts on humans
or animals.
+ Prevent any part of the human body from coming into
contact with vacuum.
+ Ensure that the individual components are only con-
nected, combined and operated according to their de-
sign and as indicated in the instructions for use.
+ Comply with all notes on correct vacuum and electrical
connections; see section ”Use and operation”, pg. 38.
+ Do not use the pump to generate pressure.
+ The pumps are designed for ambient temperatures
during operation between +50°F and +104°F (+10°C
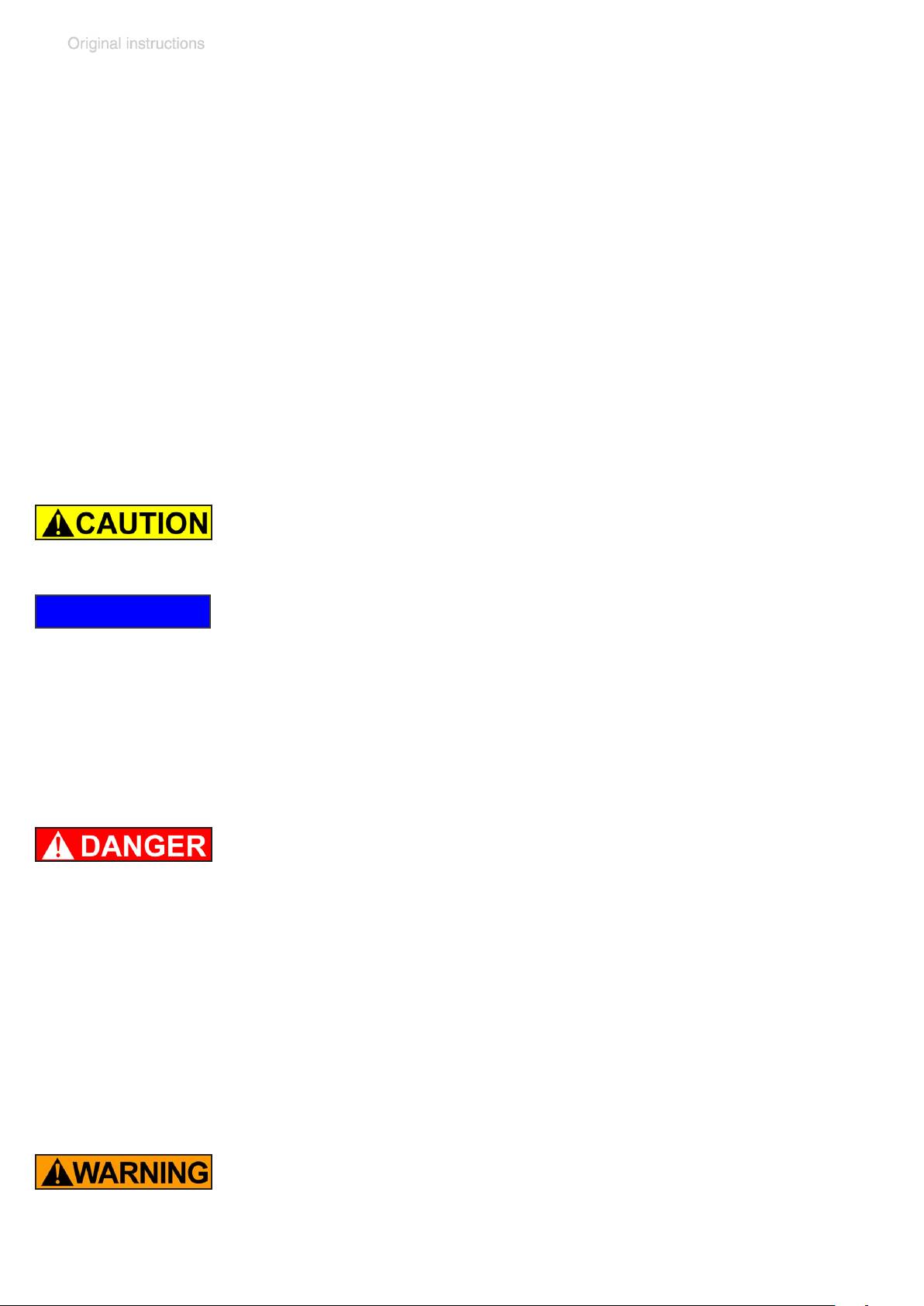
page 12 of 74
and +40°C). Periodically check maximum temperatures
if installing the pump in a cabinet or a housing. Make
sure ventilation is adequate to maintain recommended
operating temperature. Install an external automatic
ventilation system if necessary. If pumping hot process
gases, make sure that the maximum permitted gas in-
let temperature is not exceeded. The maximum permit-
ted gas inlet temperature depends on several param-
eters like inlet pressure and ambient temperature (see
”Technical data”, pg. 24).
+ Do not aspirate particles and dust.
+ Do not pump liquids.
• Ensure that the pump is chemically resistant to the
pumped substances prior to operation.
Use the equipment only as intended, that is, for genera-
NOTICE
tion of vacuum in vessels designed for that purpose. Any
other use will automatically invalidate all warranty and li-
ability claims. Remain aware of safety and risks.
Setting up and installing the equipment
➨ Equipment must be connected only to a suitable elec-
trical supply and a suitable ground point. As such,
the plug must be plugged into an outlet that is properly
grounded. Failure to connect the motor to ground may
result in deadly electrical shock.
The supply cable may be tted with a molded Euro-
pean IEC plug or a plug suitable for your local electrical
supply. The cable contains wires color coded as fol-
lows: green or green and yellow: ground; blue or white:
neutral; brown or black: hot.
+ Due to the high compression ratio, the pump may gen-
erate overpressure at the outlet. Check pressure com-
patibility with system components (e.g., exhaust pipe-
line or exhaust valve) at the outlet.

page 13 of 74
+ Do not permit any uncontrolled pressurizing. Make
sure that the exhaust pipeline cannot become blocked.
If there is an exhaust isolation valve, make sure that you
cannot operate the equipment with the valve closed to
avoid a risk of bursting!
+ Always provide a free and pressureless exhaust outlet
to avoid damage to pump valves and risk of bursting of
condenser glassware.
+ Check the overpressure safety relief device at the ex-
haust waste vapor condenser at appropriate intervals.
+ Keep the electrical power cord away from heated sur-
faces.
• Provide a rm, level platform for the equipment. Check
that the system which you are going to evacuate is
mechanically stable. Check that all ttings are secure.
Ensure a stable position of the pump without any me-
chanical contact other than the pump feet.
• Comply with maximum permissible pressures at in-
let and outlet and with maximum permissible pres-
sure differences between inlet and outlet. See section
”Technical data”, pg. 24. Do not operate the pump
with overpressure at the inlet.
• Avoid overpressure of more than 17.5 psi absolute (1.2
bar absolute) in the event that gas or inert gas is connect-
ed to the pump, to the gas ballast or to a venting valve.
• Note: Flexible elements will shrink when evacuated.
• Connect hoses gas tight at inlet and outlet of the pump.
• Ensure that no foreign objects can be drawn into the
pump.
• Check the power source and the pump’s rating plate
to be sure that the power source and the equipment
match in voltage, phase, and frequency.
• On pumps with a dual-voltage motor, check that the
voltage selection switch is set correctly. Do not change
the setting of the voltage selection switch while the
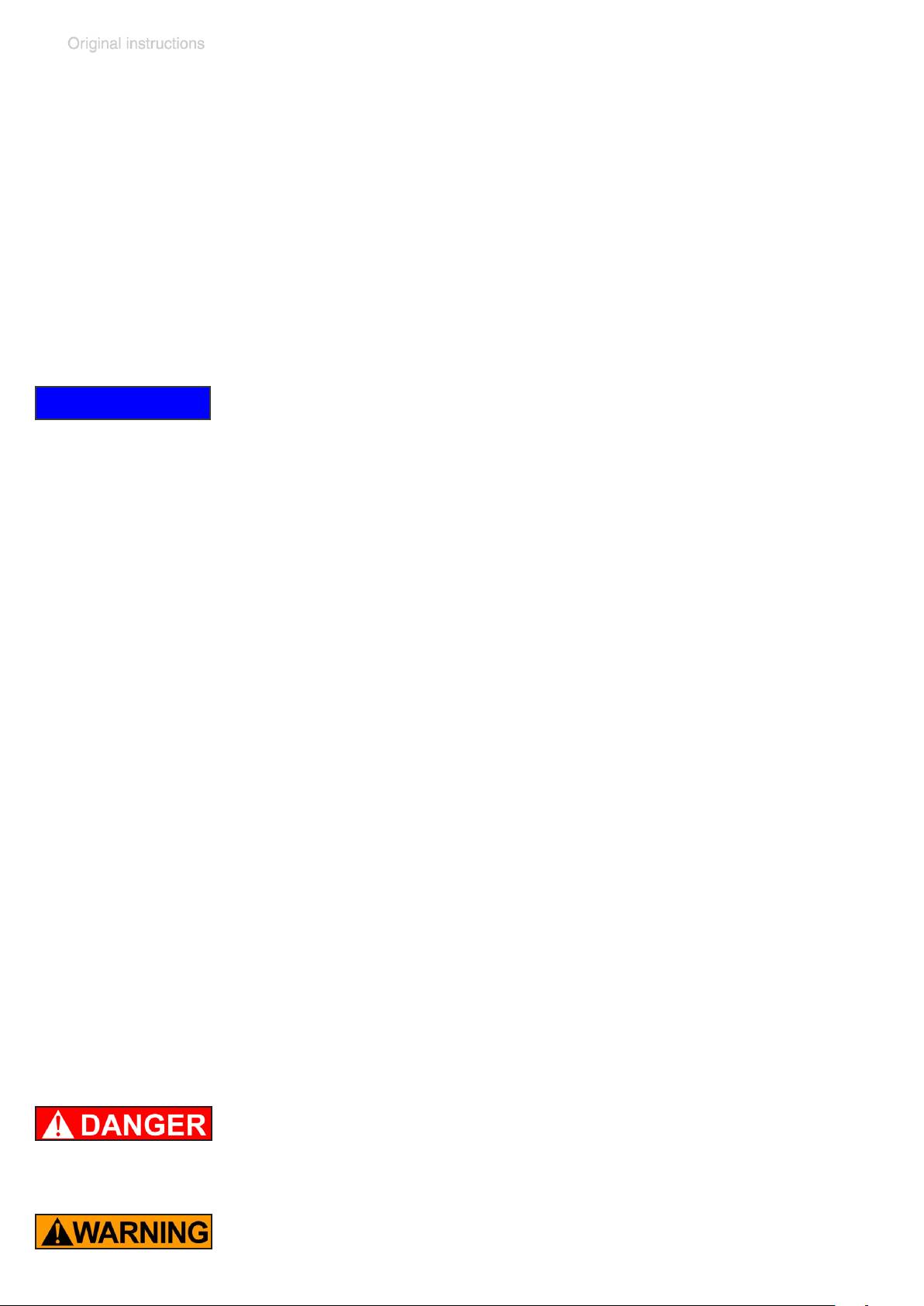
page 14 of 74
pump is connected to AC power. Unplug the pump be-
fore setting the voltage selection switch. Note: If the
pump is switched on with wrong voltage selection, the
motor may be damaged!
• Ensure that the coolant outlet pipe is always free and
that it cannot get blocked. If installing an optional cool-
ant valve, it must always be in the supply line of the
exhaust waste vapor condenser.
Keep a minimum distance of 8 in (20 cm) between the
NOTICE
cooling fan and surrounding items (e.g., housing, walls,
etc.). Check fan regularly for dust/dirt. Clean fan guard
grill if necessary to avoid a reduction of ventilation.
Use only hoses at the inlet and outlet of the pump with
an inner diameter at least as large as the diameter of the
pump’s tubing (to avoid overpressure at the outlet, and
reduction of pumping speed at the inlet).
Allow the equipment to equilibrate to ambient temperature
if you bring it from cold environment into a room prior to
operation. Notice if there is water condensation on cold
surfaces.
Secure coolant hoses at the hose nozzles (e.g., with hose
clamp) to prevent their accidental slipping.
Comply with all applicable and relevant safety require-
ments (regulations and guidelines). Implement the re-
quired actions and adopt suitable safety measures.
Ambient conditions
➨ Do not reach for this product if it has fallen into liquid.
There is a risk of deadly electrical shock. Unplug the
system immediately.
+ Do not use this product in an area where it can fall or
be pulled into water or other liquids.
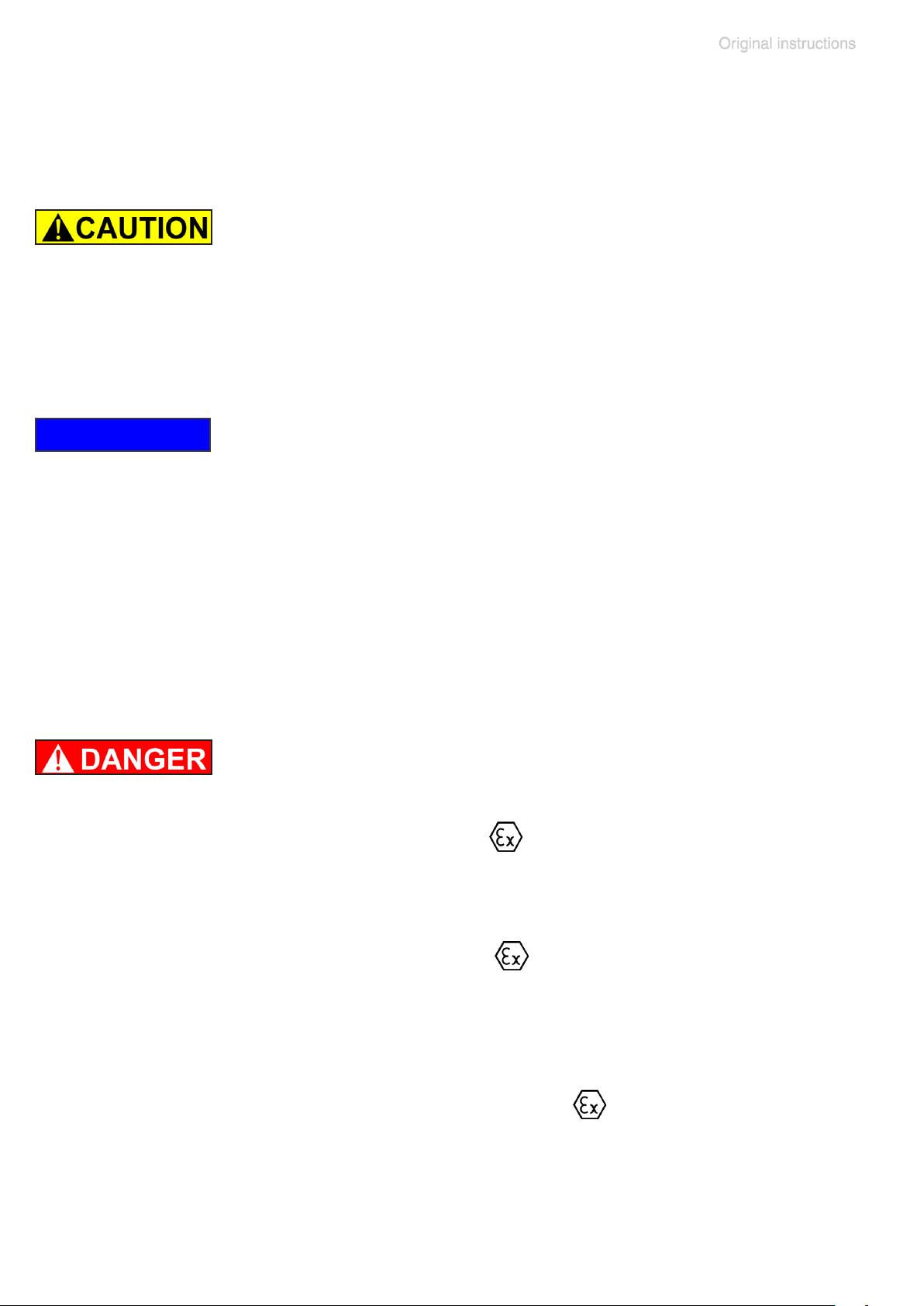
page 15 of 74
+ Pay attention to the permissible maximum ambient
and gas inlet temperatures (see ”Technical data”, pg.
24).
• Adopt suitable measures in case of differences from
recommended conditions, e.g., using the equipment
outdoors, installation in altitudes of more than 3300 ft
(1000 m) above mean sea level, conductive pollution or
external condensation on the pump.
• Do not operate this product near ames.
To the best of our knowledge the equipment is in com-
NOTICE
pliance with the requirements of the applicable EC-direc-
tives and harmonized standards (see ”Declaration of Con-
formity”) with regard to design, type and model. Directive
EN 61010-1 gives in detail the conditions under which the
equipment can be operated safely (see also IP degree of
protection, ”Technical data”, pg. 24).
Operating conditions
➨ These pumps are not approved for operation in po-
tentially explosive atmospheres. Do not operate the
pumps in potentially explosive atmospheres.
➨ Pumps without the ” ” mark on the rating plate are
not approved for the pumping of potentially explo-
sive atmospheres. Do not pump potentially explo-
sive atmospheres with those pumps.
➨ Pumps bearing the ” ” mark on their rating plates
are approved for the pumping of potentially ex-
plosive atmospheres according to their classica-
tion II 3G IIC T3 X according to ATEX, but they are
not approved for operation in potentially explosive
atmospheres (see section ” Important information:
Equipment marking (ATEX)”, pg. 22).
➨ The pumps are not suitable to pump any of the sub-
stances listed below.
Do not pump:
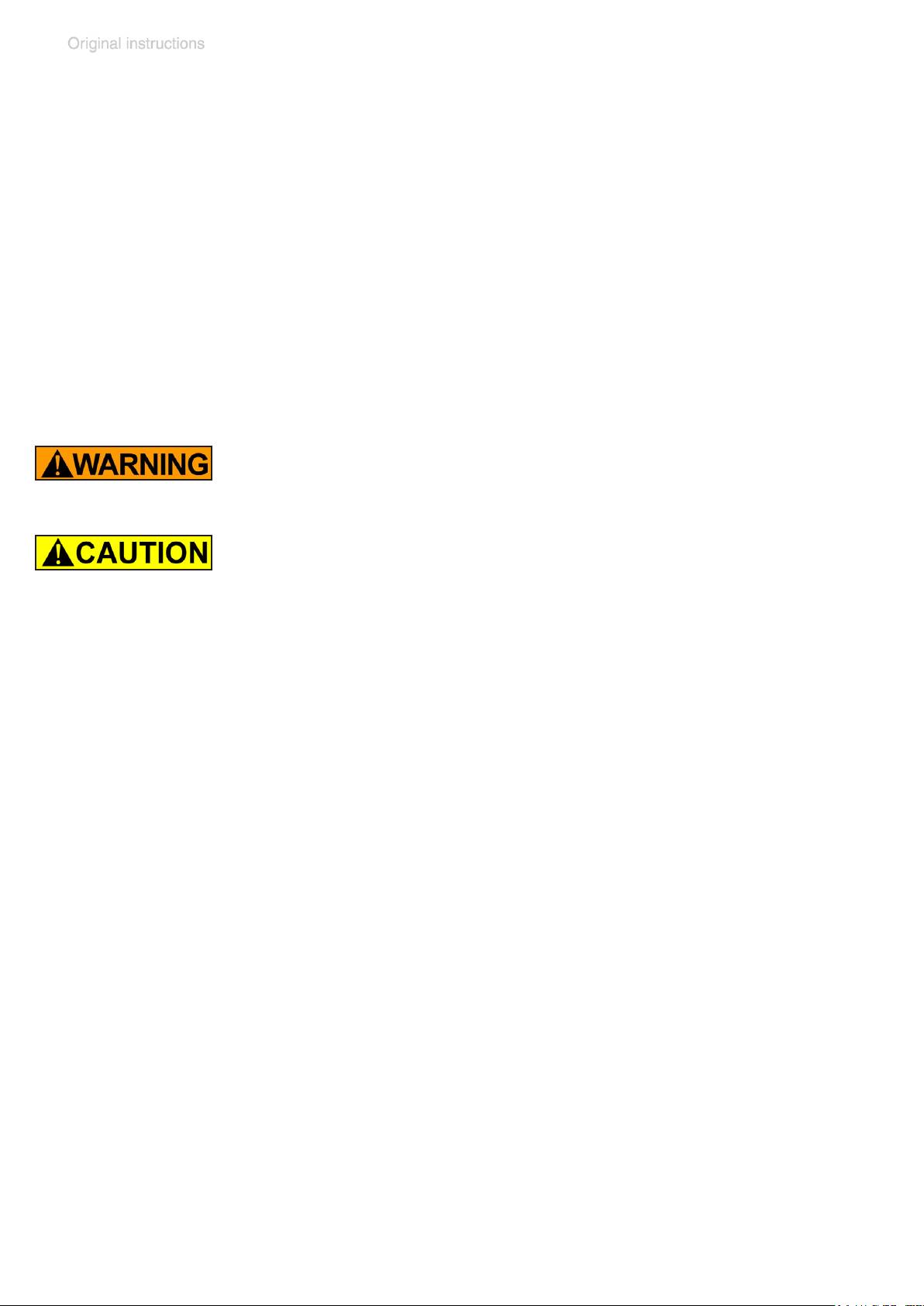
page 16 of 74
- unstable substances
- substances which react explosively under impact
(mechanical stress) without air
- substances which react explosively when being ex-
posed to elevated temperatures without air,
- substances subject to auto-ignition,
- substances which are inammable without air
- explosive substances.
➨ The pumps are not approved for operation below
ground. Do not operate the pump below ground.
+ The pumps are not suitable for pumping dust.
Do not pump dust.
• Do not pump substances which may form deposits in-
side the pump. The pumps are not suitable for pumping
substances which may form deposits inside the pump.
Deposits and condensate in the pump may lead to in-
creased temperatures even to the point of exceeding
the maximum permitted temperatures.
• Check the inlet and outlet of the pump, if there is a dan-
ger of forming deposits inside the pump, e.g., in the
pump chambers (the pump chamber is the part between
diaphragm and head cover. See section ”Replacing
diaphragms and valves”, pg. 52). Inspect the pump
chambers regularly and clean if necessary.
• Consider interactions and chemical reactions of
the pumped media. Ensure that the materials of the
pump’s wetted parts are compatible with the pumped
substances, see section ”Technical data”, pg. 24.
When changing the substances pumped, we recom-
mend purging the pump with air or inert gas prior to
changing the pumped media. Purging the pump will
pump out residues and it will reduce the possibility of
reactions of the pumped substances with each other
and with the pump’s materials.
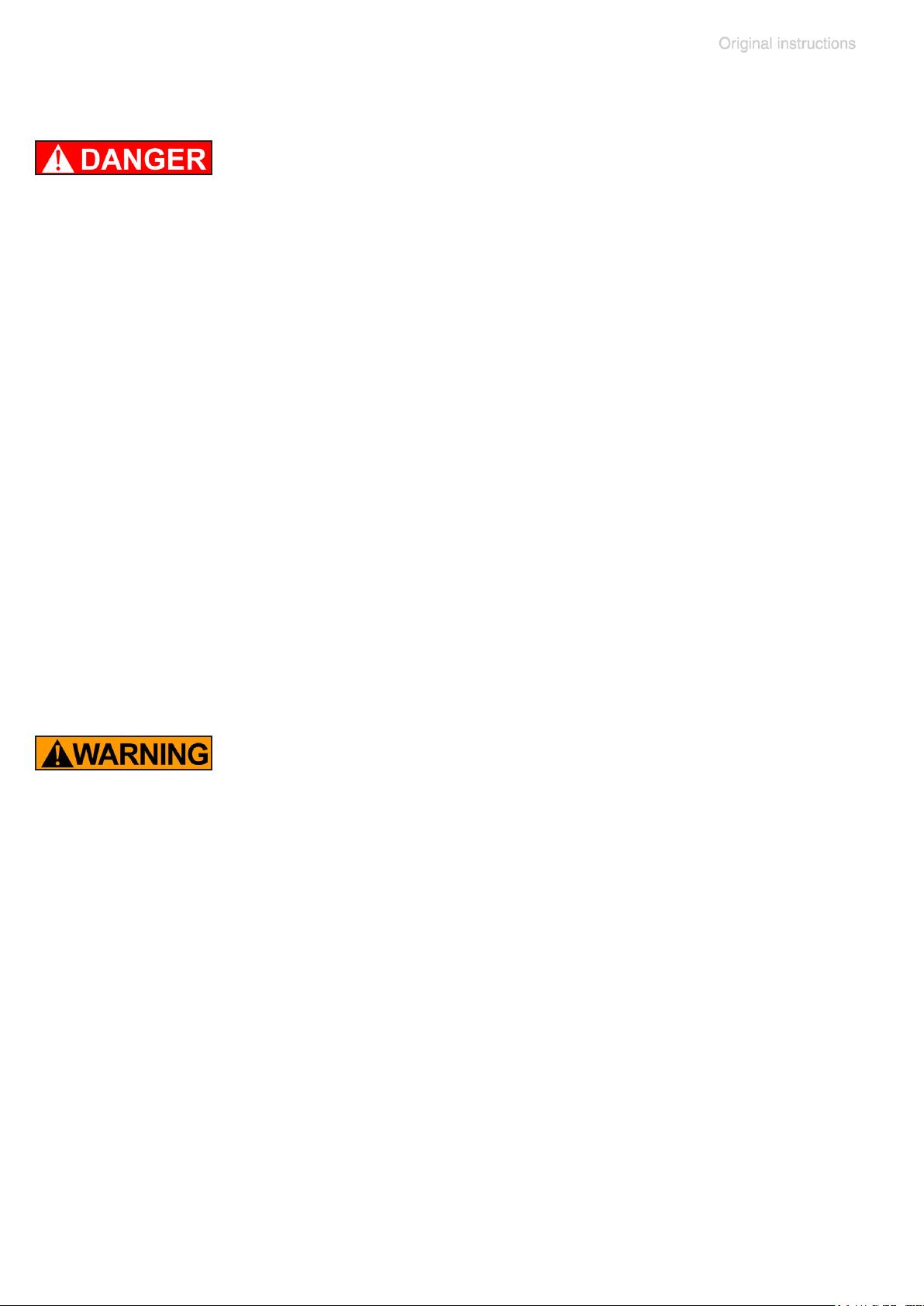
page 17 of 74
Safety during operation
➨ Adopt suitable measures to prevent the release of dan-
gerous, toxic, explosive, corrosive, noxious or polluting
uids, vapors and gases. To prevent any emission of
such substances from the pump outlet, install an ap-
propriate collecting and disposal system and take pro-
tective action for pump and environment.
➨ You must take suitable precautions to prevent any for-
mation of explosive mixtures in the pump chamber or
at the outlet of the pump. In case, e.g., of a diaphragm
failure, mechanically generated sparks, hot surfaces or
static electricity may ignite these mixtures. Use inert
gas for gas ballast or venting, if necessary.
➨ Drain appropriately or otherwise remove any potentially
explosive mixtures at the outlet of the pump, or dilute
them with inert gas to non-explosive concentrations.
➨ Never operate this pump if it has a damaged cord or
plug.
+ If the pump is not working properly, has been dropped
or has fallen into water, contact your pump service pro-
vider.
+ Prevent any part of the human body from coming into
contact with vacuum.
+ Never aspirate liquids or dust into the pump.
+ Make sure that the exhaust pipeline cannot become
blocked.
+ Check the overpressure safety relief device at the ex-
haust waste vapor condenser at appropriate intervals.
+ Comply with applicable regulations when disposing of
chemicals. Take into consideration that chemicals may
be contaminated. Take adequate precautions to pro-
tect people from the effects of dangerous substances
(chemicals, thermal decomposition products of uo-
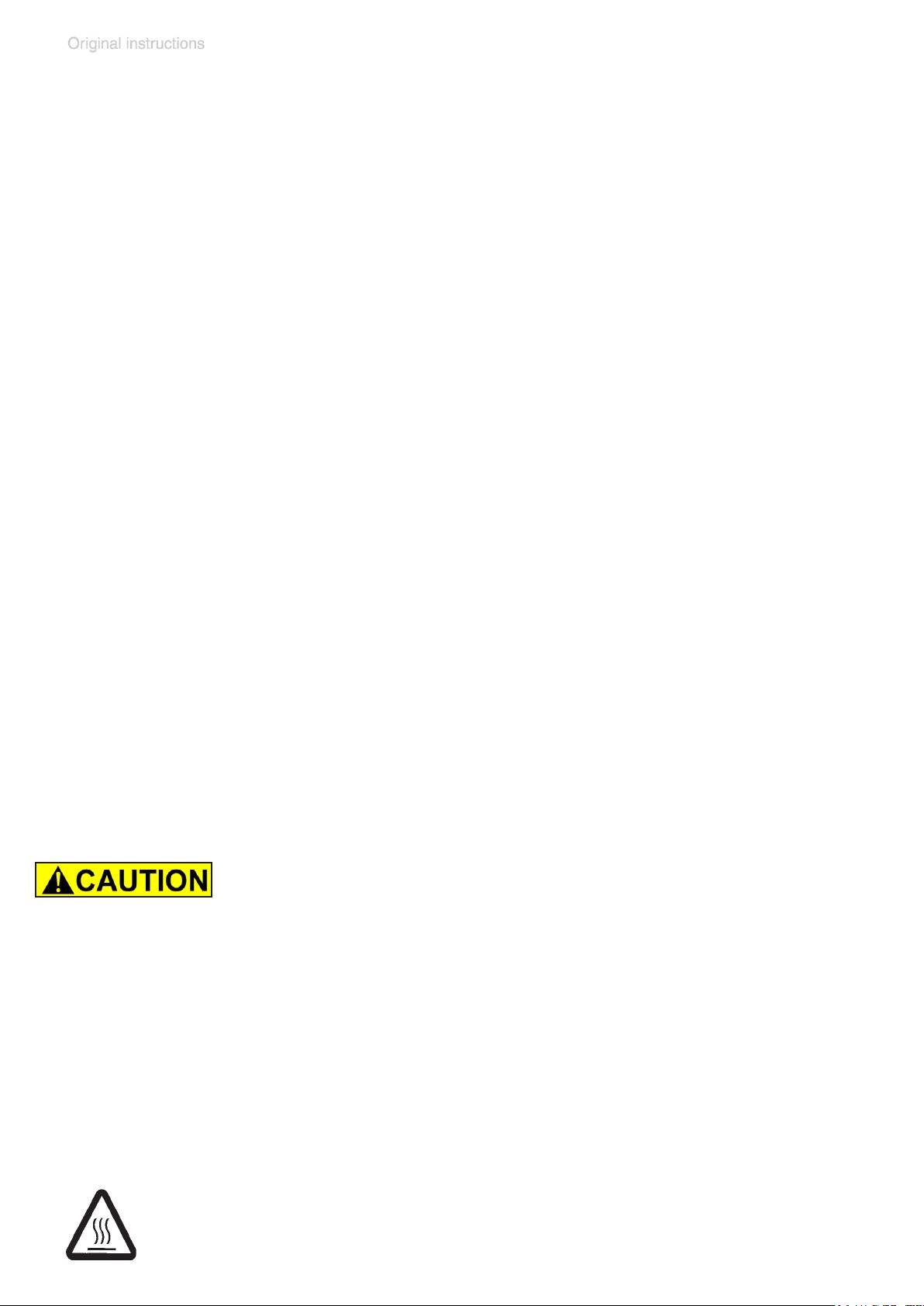
page 18 of 74
roelastomers). Use appropriate protective clothing and
safety goggles.
+ Use only original manufacturer’s spare parts and
accessories. Otherwise the safety and performance of
the equipment, as well as the electromagnetic compat-
ibility of the equipment might be reduced.
The CE mark or the cTÜVus mark may be voided if not
using original manufacturer’s spare parts.
+ Interruption of the pump (e.g., due to power failure),
failure of connected components or of parts of the sup-
ply, or change in parameters must not be allowed to
lead to dangerous conditions. In case of a diaphragm
failure or in case of a leak in the manifold, pumped sub-
stances might be released into the environment or into
the pump housing or motor.
Comply with all notes regarding proper use of the pumps,
as well as operation and maintenance guidance.
+ The residual leak rate of the equipment might render
possible an exchange of gas, albeit extremely slight,
between the environment and the vacuum system.
Adopt suitable measures to prevent contamination of
the pumped substances or the environment.
• Ensure that no parts of your clothing, hair or ngers can
be caught or drawn in at the inlet of the pump. Never
insert ngers or drop any other object into the inlet or
outlet.
• Pumping at high inlet pressure may lead to overpres-
sure at the gas ballast valve. Pumped gases or con-
densate might be expelled if the valve is open. If an
inert gas supply is connected to the gas ballast, ensure
that its inlet pipeline is not contaminated.
• Pay attention to the safety symbol ”hot surfaces” on
the equipment. Hot parts may cause burns if touched.
Adopt suitable measures to prevent any danger arising
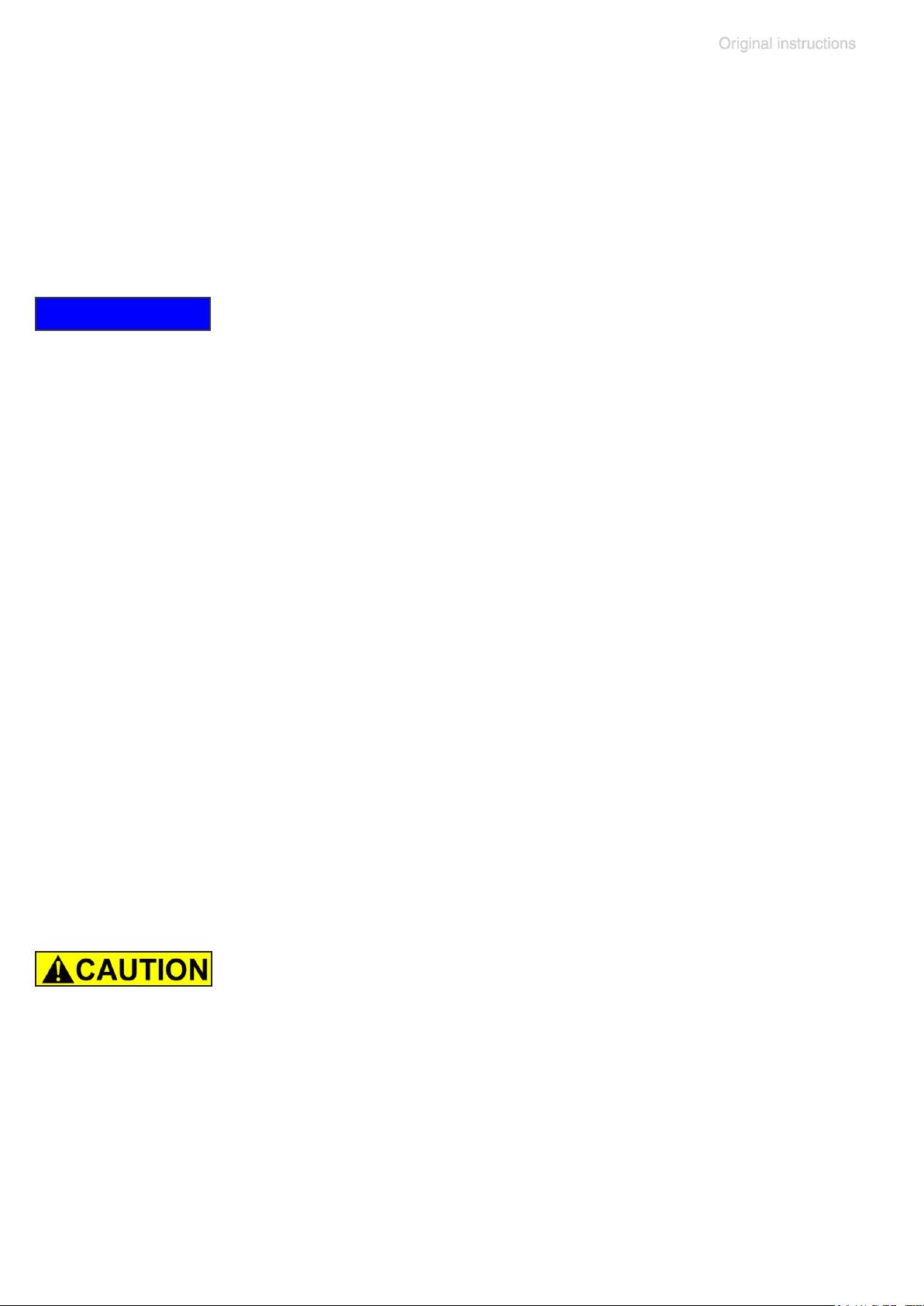
page 19 of 74
from hot surfaces or electric sparks. Ensure that hot
surfaces of the pump do not cause burns. Provide a
suitable contact guard if necessary.
• Ensure that the coolant outlet pipe at the waste vapor
condenser is always free and that it cannot get blocked.
Do not start the pump if the pressure difference between
NOTICE
inlet and outlet exceeds 16 psi (1.1 bar) at maximum.
Prevent the backpressure of gases and the backow of
condensates at the outlet.
Check the liquid level in the catchpots regularly and drain
condensate in time to prevent overlling. Install a level
sensor (see ”Accessories”, pg. 48) for monitoring, if
necessary.
Provide appropriate protective measures to allow for the
possibility of failure and malfunction. The protective mea-
sures must also allow for the requirements of the respec-
tive application.
In case of overload, the motor is shut down by a self-hold
thermal cutout in the winding.
Note: Only manual reset is possible. Switch off the pump
and disconnect from the power source. Identify and elimi-
nate the cause of failure. Wait approx. ve minutes before
restarting the pump.
• Note: In case of supply voltage below 100V, the lock
of the cutout might be impaired and the pump may
restart on its own after sufcient cooling down. Take
appropriate precautions, if an automatic restart of the
pump may lead to a dangerous situation (e.g., switch
off the pump and disconnect from the power source).
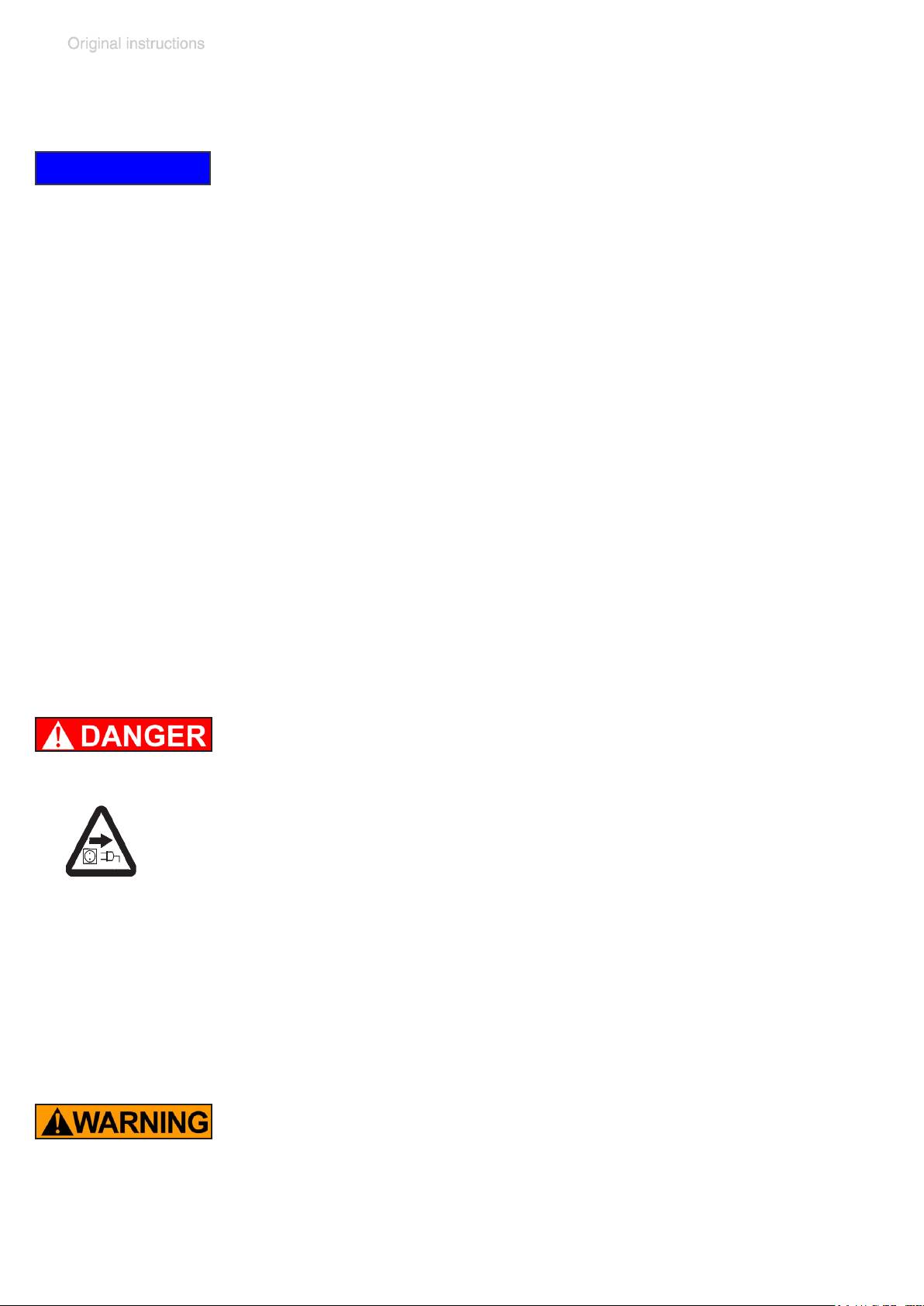
page 20 of 74
Maintenance and repair
In order to comply with laws (occupational, health and
NOTICE
safety regulations, safety at work law and regulations for
environmental protection) vacuum pumps, components
and measuring instruments can only be returned when
certain procedures (see section ”Notes on return to the
factory”, pg. 67) are followed.
Take advantage of our service seminars, which put special
focus on the maintenance and repair of vacuum pumps.
For details and for the online ”Instructions for repair” man-
ual see www.vacuubrand.com.
In case of normal wear, the lifetime of the diaphragms
and valves is > 10000 operating hours. Bearings have a
typical durability of 40000 h. Motor capacitors have a typi-
cal durability in the range of 10000 to 40000 h depending
strongly on operation conditions including ambient tem-
perature, humidity or load.
➨ Ensure that the pump cannot be operated acciden-
tally. Never operate the pump if covers or other
parts of the pump are disassembled.
➨ Switch off the pump. Disconnect the electrical pow-
er cord and wait two minutes before starting mainte-
nance to allow the capacitors to discharge.
➨ Note: The pump may be contaminated with process
chemicals, which have been pumped during operation.
Ensure that the pump is completely decontaminated
before maintenance commences.
+ Take adequate precautions to protect people from the
effects of dangerous substances if contamination has
occurred. Use appropriate protective clothing, safety
goggles and protective gloves.
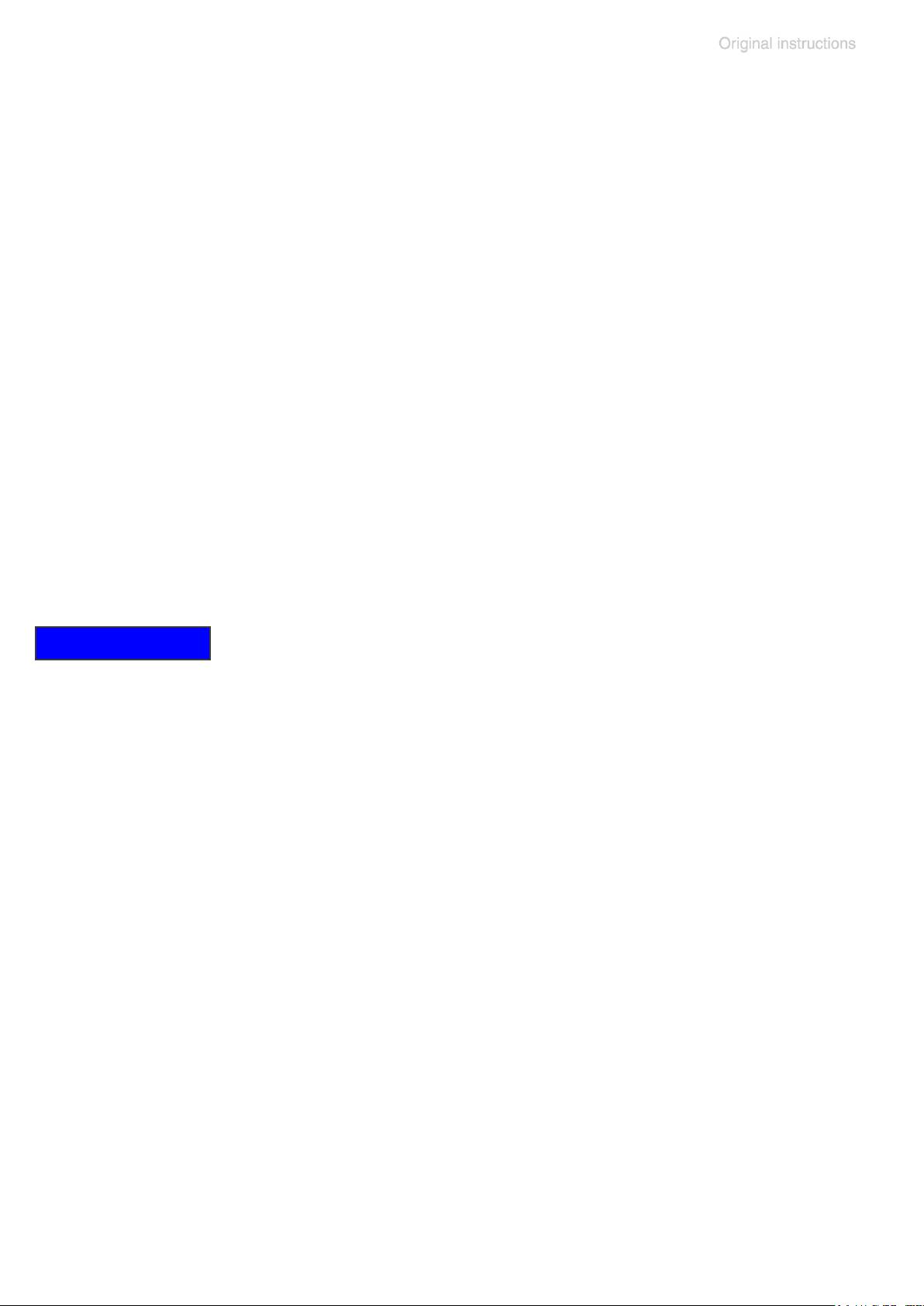
page 21 of 74
+ Wear parts have to be replaced regularly.
+ Never operate a defective or damaged pump.
+ Check every motor capacitor regularly by measuring
its capacity and estimating its time in operation. Re-
place old capacitors early enough to prevent a failure in
operation. If an old motor capacitor fails, the capacitor
may get hot. It may even melt or emit a ame, which
could be dangerous for persons and equipment in
the vicinity. The capacitors have to be replaced by an
electrician.
+ Vent the pump before starting maintenance. Isolate the
pump and other components from the vacuum system.
Allow sufcient cooling of the pump. Separate the pump
from the coolant circuit and drain condensate, if appli-
cable.
Ensure that maintenance is done only by suitably trained
NOTICE
and supervised technicians. Ensure that the maintenance
technician is familiar with the safety procedures, which re-
late to the products processed by the pumping system.
Only dismantle the pump as far as necessary.
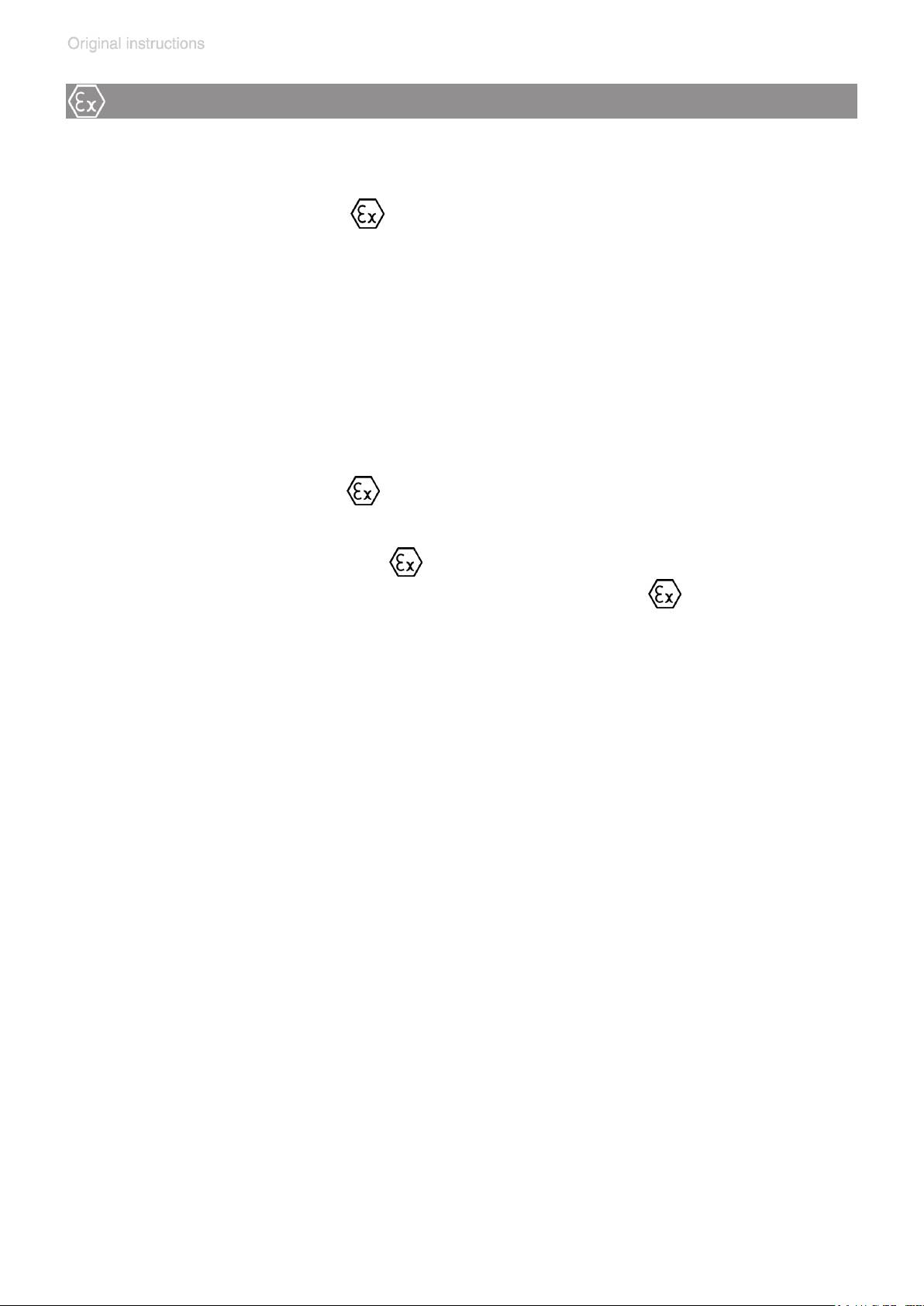
page 22 of 74
Important information: Equipment marking (ATEX)
VACUUBRAND equipment bearing mark (see rating plate)
II 3G IIC T3 X
Internal Atm. only
Tech. File Ref.: VAC-EX01
and
VACUUBRAND equipment bearing mark (see rating plate)
X see manual
For equipment labelled with „ X see manual“ the following classica-
tion according to Directive 94/9/EC (ATEX) is valid:
II 3G IIC T3 X,
Internal Atm. only, Tech. File Ref.: VAC-EX01.
The classication II 3G IIC T3 X according to ATEX is only valid for the in-
ner part (wetted part, pumped gas or vapor) of the equipment. The equip-
ment is not suitable for use in external, potentially explosive atmospheres
(environment).
The overall category of the equipment depends on the connected compo-
nents. If the connected components do not comply with the classication
of the VACUUBRAND equipment, the specied category of the VACU-
UBRAND equipment is no longer valid.
Vacuum pumps and vacuum gauges in category 3 are intended for con-
nection at equipment in which during normal operation explosive atmo-
spheres caused by gases, vapors or mists normally don’t occur or, if they
do occur, are likely to do so only infrequently and for a short period only.
Equipment in this category ensures the requisite level of protection dur-
ing normal operation.
The use of gas ballast or the operation of venting valves is only permit-
ted if thereby explosive atmospheres normally don’t occur in the interior
of the equipment or, if they do occur, are likely to do so only infrequently
and for a short period.
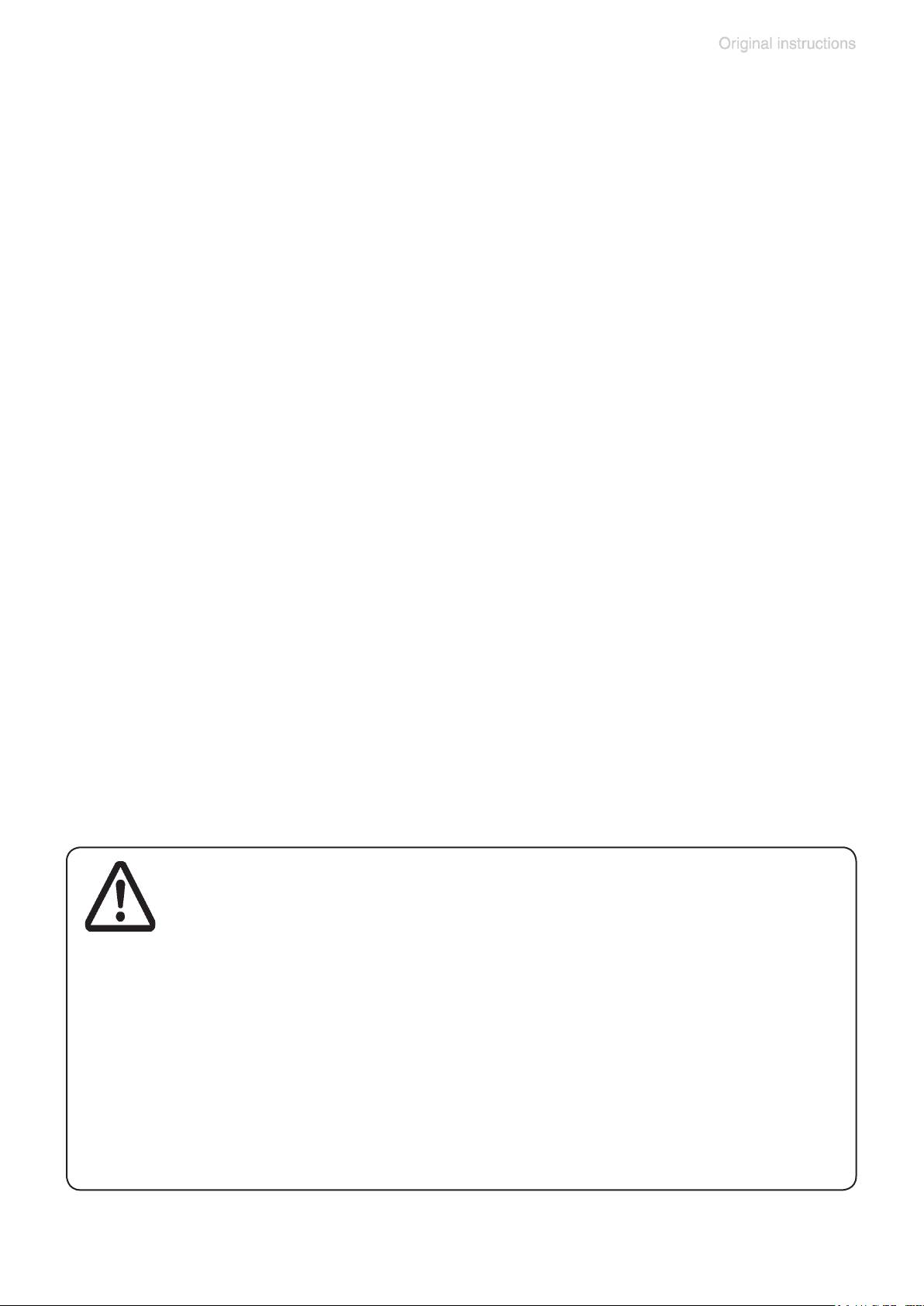
page 23 of 74
The pumps are marked with ”X” (according to EN 13463-1), i. e. restric-
tions of the operation conditions:
• The equipment is designated for a low degree of mechanical stress
and has to be installed in a way so that it cannot be damaged from
outside.
Pumping units have to be installed protected against shocks from the
outside and against glass splinters in the event of breaking (implo-
sion).
• The equipment is designated for an ambient and gas inlet tempera-
ture during operation of +10 to +40°C. Never exceed these ambient
and gas inlet temperatures. If pumping / measuring gases which are
not potentially explosive, extended gas inlet temperatures are valid,
see instructions for use, section “Gas inlet temperatures” or “Technical
data”.
After any intervention at the equipment (e.g., repair / maintenance) the ul-
timate vacuum of the pump has to be checked. Only if the pump achieves
its specied ultimate vacuum, the pump’s leak rate is low enough to en-
sure that no explosive atmospheres will occur in the interior of the equip-
ment.
After any intervention at the vacuum sensor the leak rate of the equip-
ment has to be checked.
Attention: This manual is not available in all
languages of the EU. The user must not op-
erate the device if he does not understand
this manual. In this case a technically cor-
rect translation of the complete manual has
to be available. The manual must be com-
pletely read and understood before opera-
tion of the device and all required measures
must be applied.