Labconco VACUUBRAND Diaphragm Pump 7393000: Replacing diaphragms and valves
Replacing diaphragms and valves: Labconco VACUUBRAND Diaphragm Pump 7393000
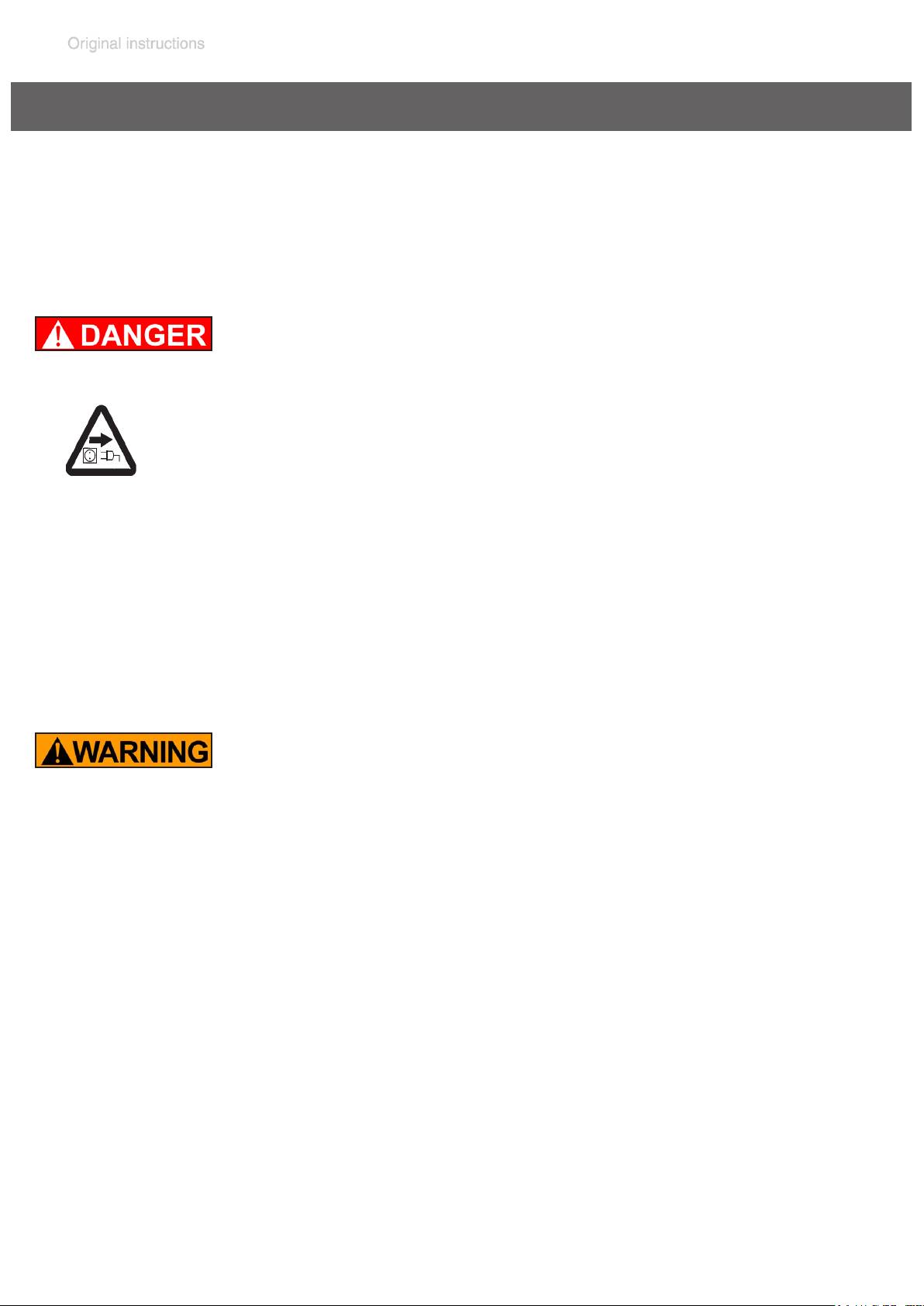
page 52 of 74
Replacing diaphragms and valves
+ Please read section ”Replacing diaphragms and valves” com-
pletely before starting maintenance.
The pictures may show other versions of pumps. This does not change
the method of replacing diaphragms and valves.
➨ Never operate the pump if covers or other parts of
the pump are disassembled.
➨ Before starting maintenance, disconnect the electri-
cal power cord. Wait two minutes after isolating the
equipment from AC power to allow the capacitors to
discharge.
➨ Ensure that the pump cannot be operated accidentally.
➨ Note: The pump might be contaminated with the pro-
cess chemicals that have been pumped during oper-
ation. Ensure that the pump is decontaminated before
maintenance.
➨ Avoid the release of pollutants.
+ Never operate a defective or damaged pump.
+ Take adequate precautions to protect people from the
effects of dangerous substances that may have con-
taminated the pump and may be released upon dis-
assembly. Ensure that the maintenance technician is
familiar with the safety procedures which relate to the
products processed by the pumping system.
Use appropriate protective clothing, safety goggles and
protective gloves.
+ Check every motor capacitor regularly by measuring its
capacity and estimating its service life. Replace old ca-
pacitors early enough to prevent a failure. The capaci-
tors must be replaced by a trained electrician.
+ Allow sufcient cooling of the pump before starting
maintenance. Drain condensate, if applicable.
+ Vent the pump and isolate it from the vacuum sys-
tem before you start maintenance.
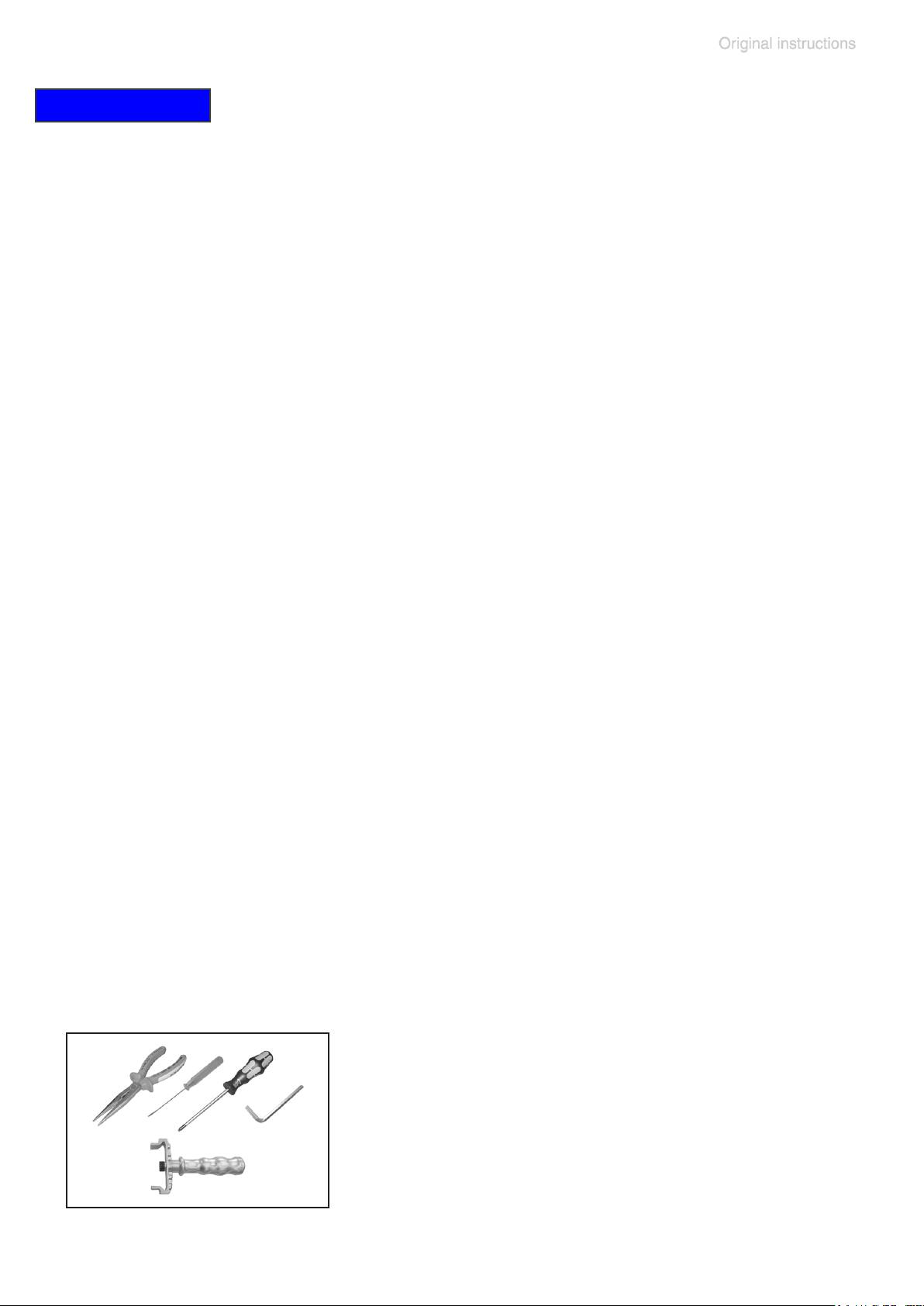
page 53 of 74
Ensure that maintenance is done only by suitably
NOTICE
trained and supervised technicians.
The valves and diaphragms as well as the motor capac-
itors are wear parts. If the rated ultimate vacuum is no
longer achieved or in case of increased noise level, the
pump interior, the diaphragms and the valves must be
cleaned and the diaphragms and valves must be checked
for cracks or other damage.
All bearings are encapsulated and are lled with long-life
lubricant. Under normal operating conditions, the drive
system is maintenance free.
In demanding circumstances, it may be efcient to
check and clean the pump heads on a regular basis. In
normal use, the lifetime of the diaphragms and valves
is more than 10,000 operating hours.
- Prevent internal condensation, transfer of liquids or
dust. The diaphragms and valves will be damaged if
liquid is pumped in signicant amount.
- Carry out maintenance frequently if the pump is ex-
posed to corrosive media or in case of deposits.
- Regular maintenance will improve the lifetime of the
pump and also protect both users and the environment.
Service kit for ME 2C NT ............................................................................696878
Service kit for ME 4C NT ............................................................................696864
Service kit for MZ 2C NT / PC 201 NT .......................................................696869
Service kit for MD 4C NT / PC 201 NT ..................................................... 696870
Service kit for ME 8C NT ............................................................................696867
Diaphragm key (width 66 mm) ....................................................................636554
Tools required (metric):
- Torx driver T20
- 5 mm wide Allen key
- 2.5 mm wide slotted screwdriver
- Flat pliers
- Diaphragm key width 66 mm
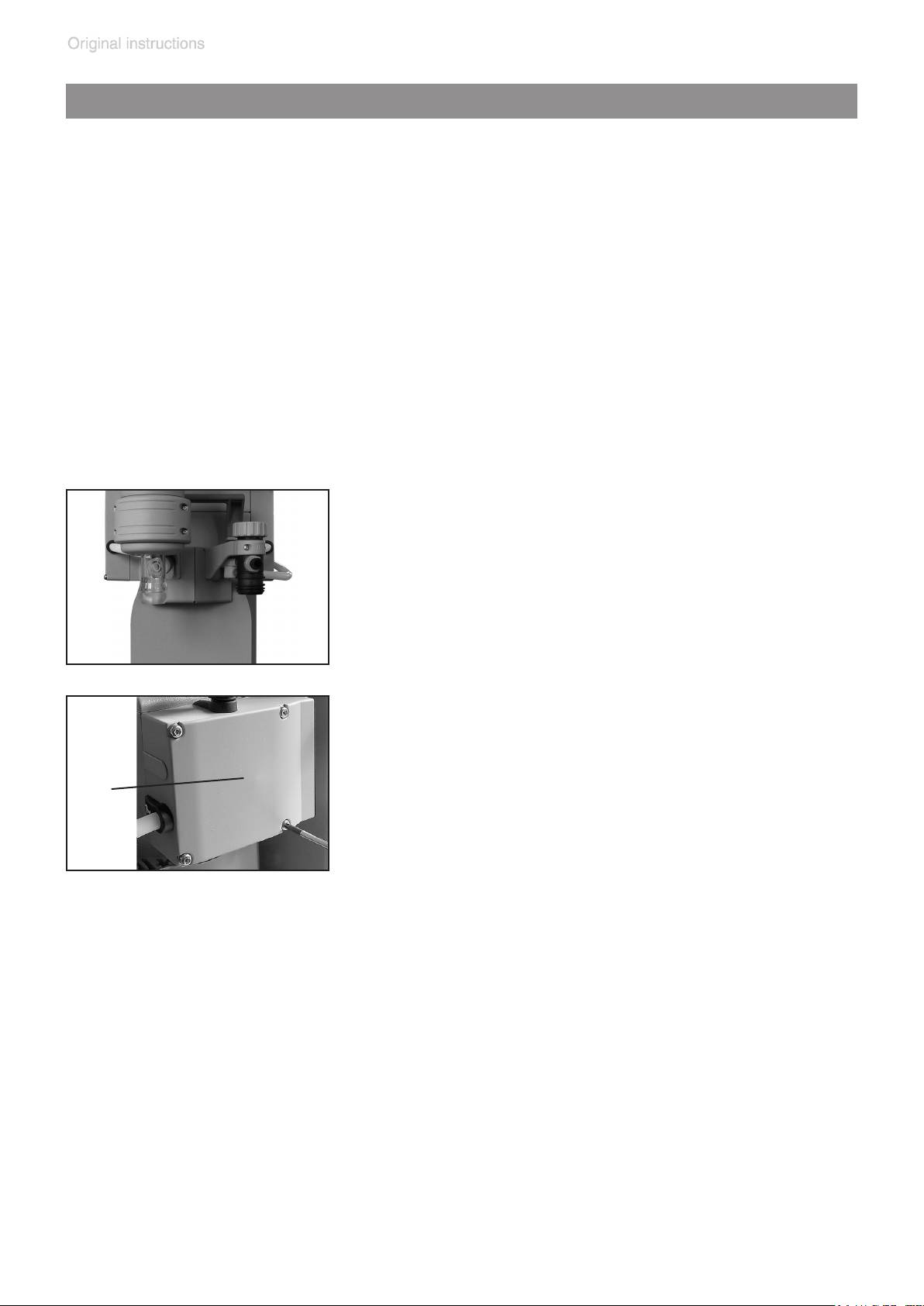
page 54 of 74
Cleaning and inspecting the pump heads
The replacement of the diaphragm and the replacement of the valves can
be carried out separately.
+ To replace the valves, remove the head covers of one side of the pump
along with the assembled valve heads and ttings.
+ To maintain the diaphragms, the valve heads and the ttings need not
be disassembled. The head covers can be removed along with the as-
sembled valve heads and ttings.
+ Service only one side of the pump at a time to avoid the mixing of
parts.
Pump on pump support:
➨ Remove catchpots (9) at inlet and outlet (see
”Use and operation”, page 38).
➨ Remove the 4 screws afxing the head cov-
er cowling (W) with a Torx driver T20. Pay
attention to the washers under the screws
W
and remove.
➨ Pull off head cover cowling (W) carefully. Do
not tilt.
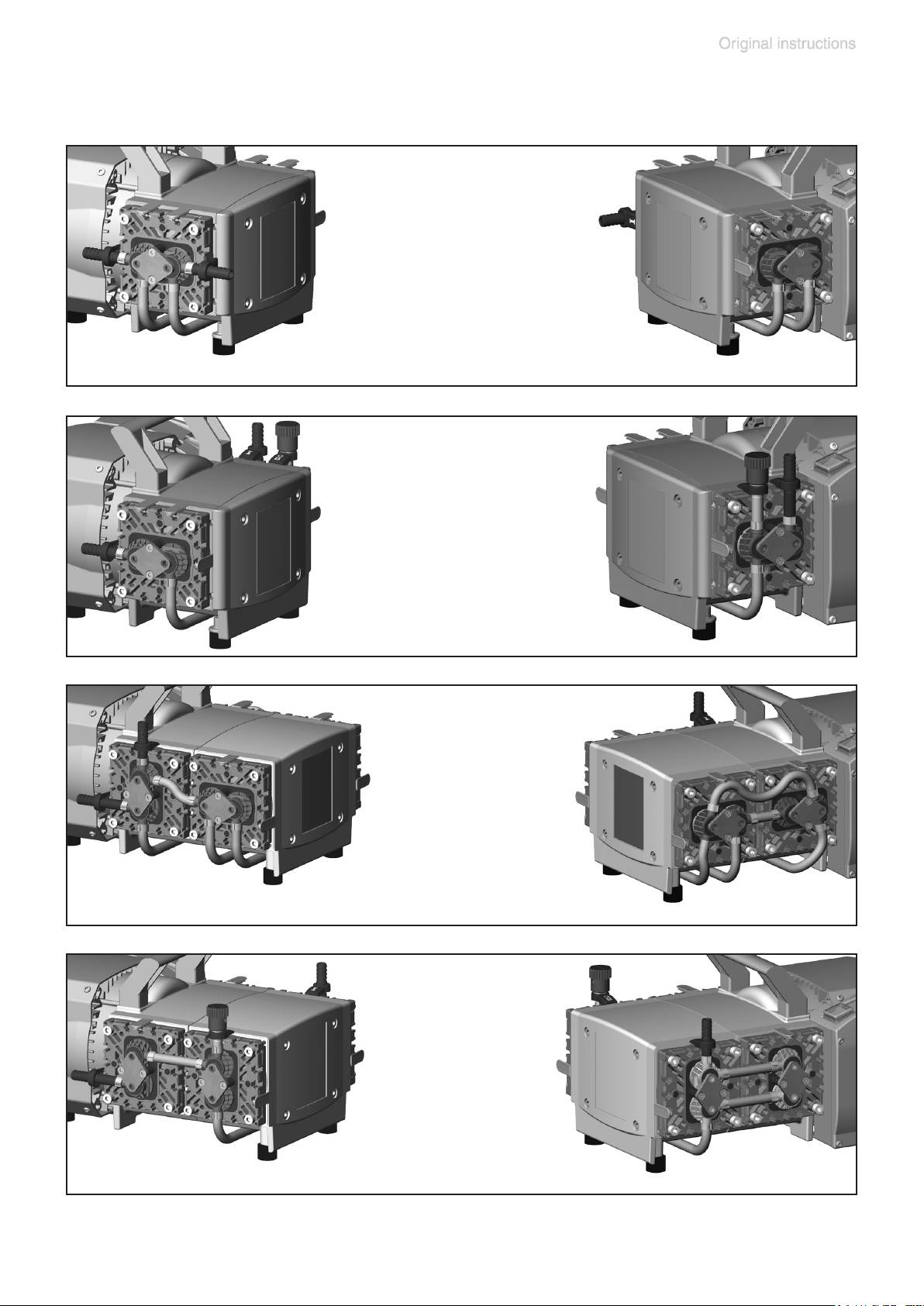
page 55 of 74
Fittings and tubing of the different pump models:
ME 4C NT
MZ 2C NT
ME 8C NT
MD 4C NT

page 56 of 74
MZ 2C NT 2AK
MZ 2C NT AK + EK
MZ 2C NT AK SYNCHRO + EK
PC 101 NT
MD 4C NT 2AK
MD 4C NT AK + EK
MD 4C NT AK SYNCHRO + EK
PC 201 NT
ME 8C NT + 2 AK
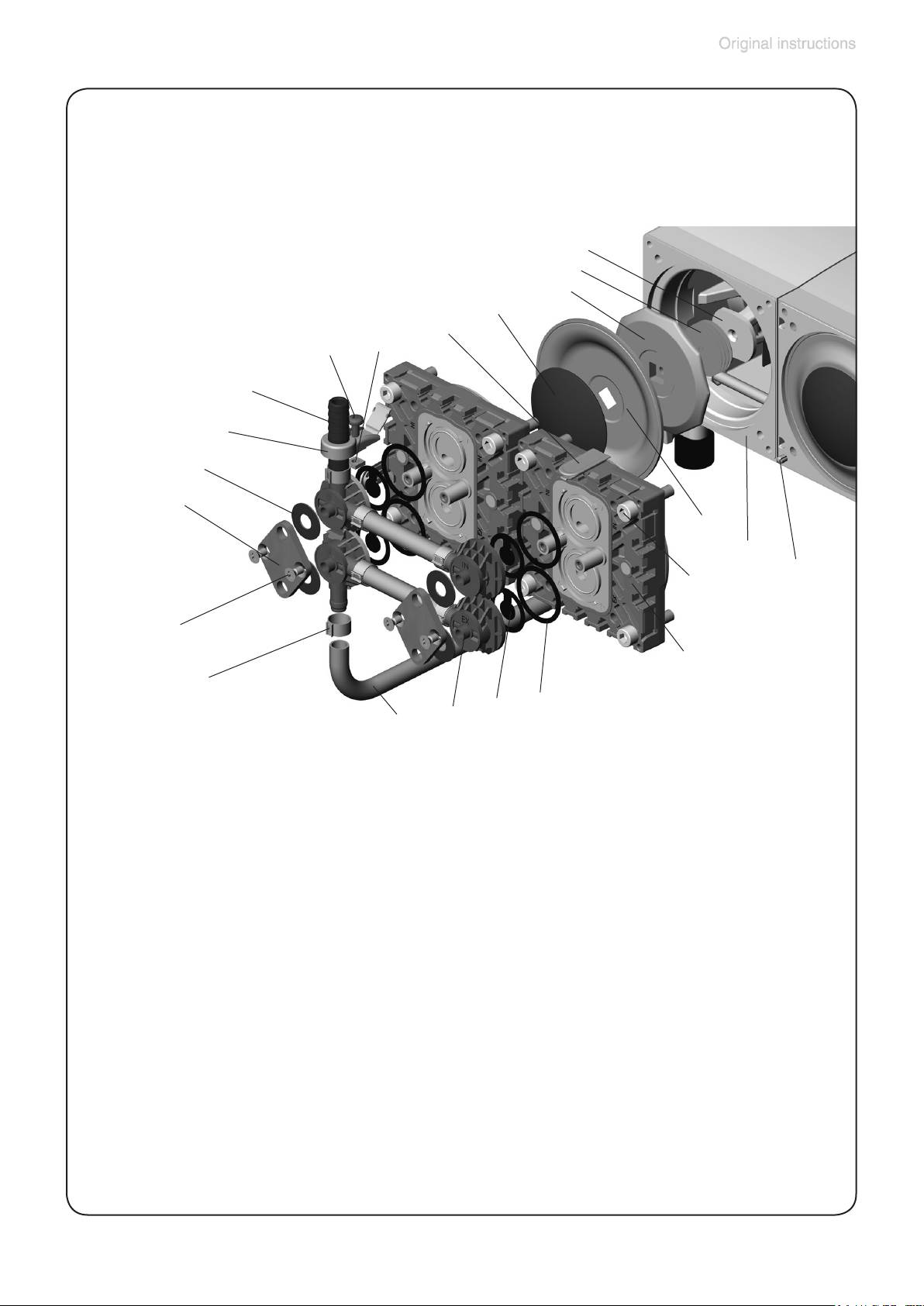
page 57 of 74
View of the disassembled pump head parts
(g.: MD 4C NT)
B
D
E
G
I
K
L
P
Q
R
S
F
C
A
H
T
J
U
M
N
O
V
A: Head alignment pin / mark
L: Fillister head screw
B: Connecting rod
M: O-ring
C: Housing
N: Valve
D: Washer
O: Valve head
E: Diaphragm support disc
P: Hose nozzle
F: Diaphragm
Q: Connection fastener
G: Diaphragm clamping disc
with hinged cover
with square head screw
R: Disc spring
H: Allen screw
S: Clamping bracket
I: Cap
T: Countersunk screw
J: Head cover
U: Hose clip
K: Square nut
V: Connection tube
This labeling is used throughout the following pages.
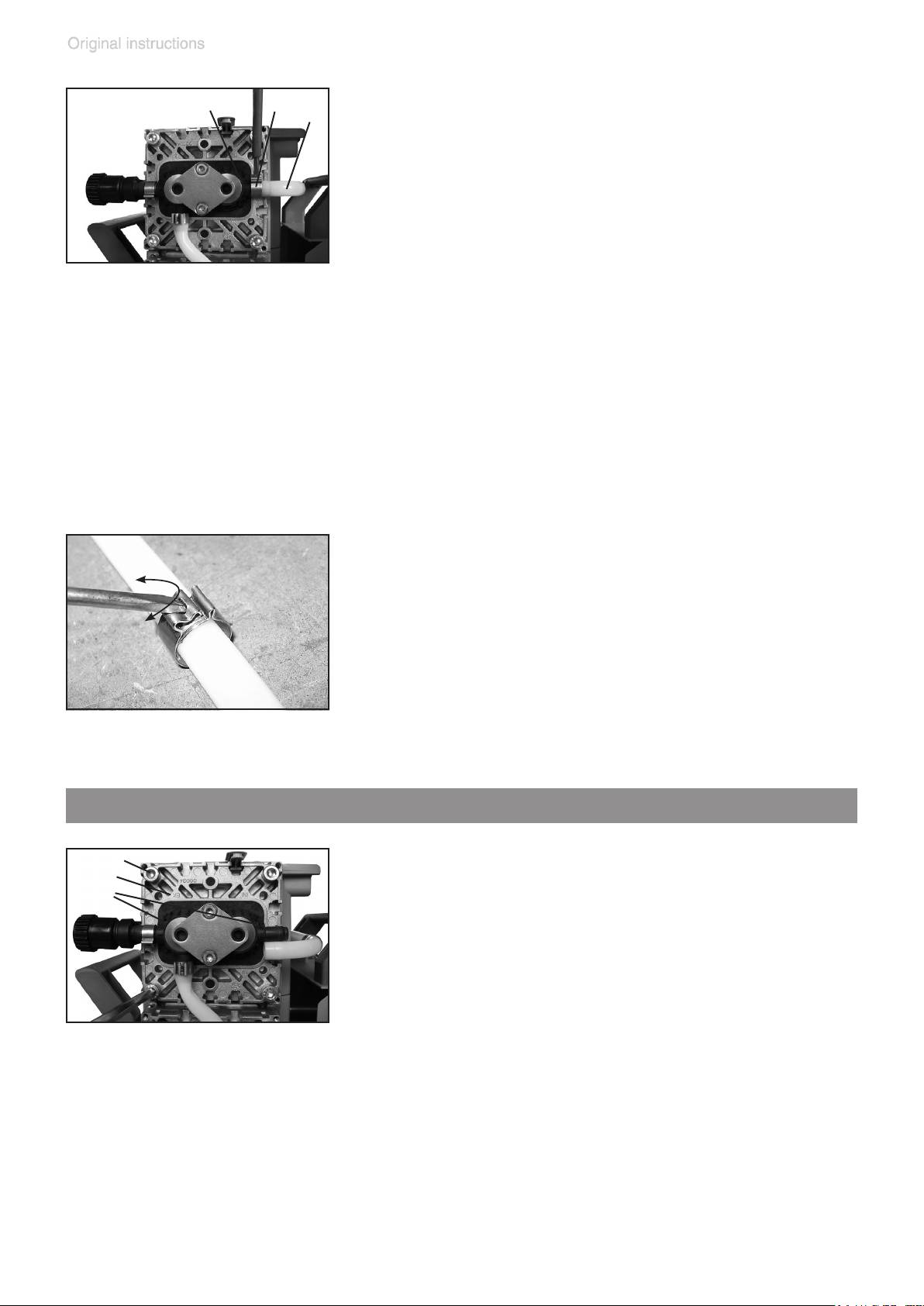
page 58 of 74
O
U
Detach the coupling of the connection tube (V)
V
to the other side of the pump at the valve head
(O).
Pump at pump support:
Detach the coupling of the connection tube (V)
to the other side of the pump as well as the
hose connection to the inlet/outlet of the vacu-
um system at the valve head (O).
➨ Open the hose clip (U) with a slotted screw-
driver.
➨ Pull the tubing off the hose connector.
Opening the hose clip:
➨ Apply slotted screwdriver as shown and
turn.
Replacing the diaphragm
H
➨ Disassemble head covers (J) to check the
J
O
diaphragm (F).
➨ Unscrew four (pump with one/two heads) or
eight (pump with four heads) Allen screws
(H) with a 5mm wide Allen key. Remove both
head covers (J) (pumps with one/two heads:
only one head cover) together with valve
heads (O) and connections.
+ It is not necessary to disassemble the valve
heads (O), the connection fasteners (Q), or
the hose connection between the adjacent
head covers (pumps with four heads).
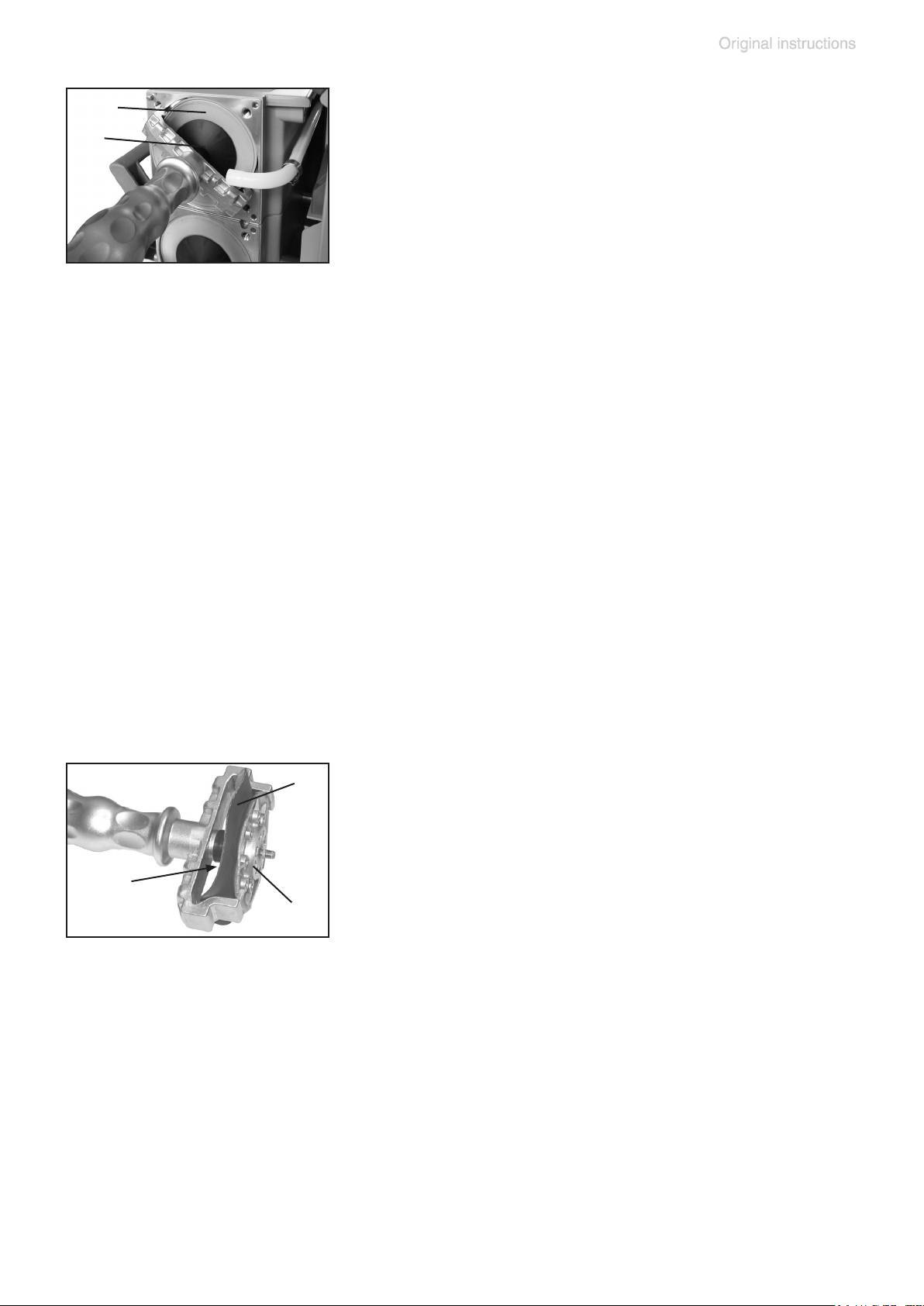
page 59 of 74
+ Check diaphragm (F) for damage and re-
F
G
place if necessary.
➨ Lift diaphragm carefully sidewise.
+ Never use a pointed or sharp-edged tool to
lift the diaphragm.
➨ Use the diaphragm key to grip the diaphragm
support disc (E) below the diaphragm.
➨ Unscrew diaphragm support disc (E) with diaphragm (F) and dia-
phragm clamping disc (G).
➨ Check for washers (D) between the diaphragm support disc (E) and
the connecting rod (B). Do not mix the washers from the different pump
heads, since these are set at the factory to ensure proper pump per-
formance. Make sure that the original number is reassembled at the
individual pump head.
+ Too few washers: The pump will not attain vacuum specication. Too
many washers: Diaphragm clamping disc will hit head cover, causing
noisy operation and possibly causing the pump to seize up.
+ If the old diaphragm is difcult to separate from the diaphragm support
disc, immerse assembly in naphtha or petroleum ether. Do not inhale
vapors!
➨ Position new diaphragm (F) between dia-
F
phragm clamping disc with square head
screw (G) and diaphragm support disc (E).
+ Note: Position diaphragm with pale side to-
G
wards diaphragm clamping disc (facing pump
E
chamber).
+ Make sure that the square head screw of the diaphragm clamping disc
is correctly seated in the guide hole of the diaphragm support disc.
➨ Lift the diaphragm at the side. Place the diaphragm carefully together
with diaphragm clamping disc and diaphragm support disc in the dia-
phragm key.
+ Avoid damage of the diaphragm: Do not excessively bend or crease
the diaphragm.
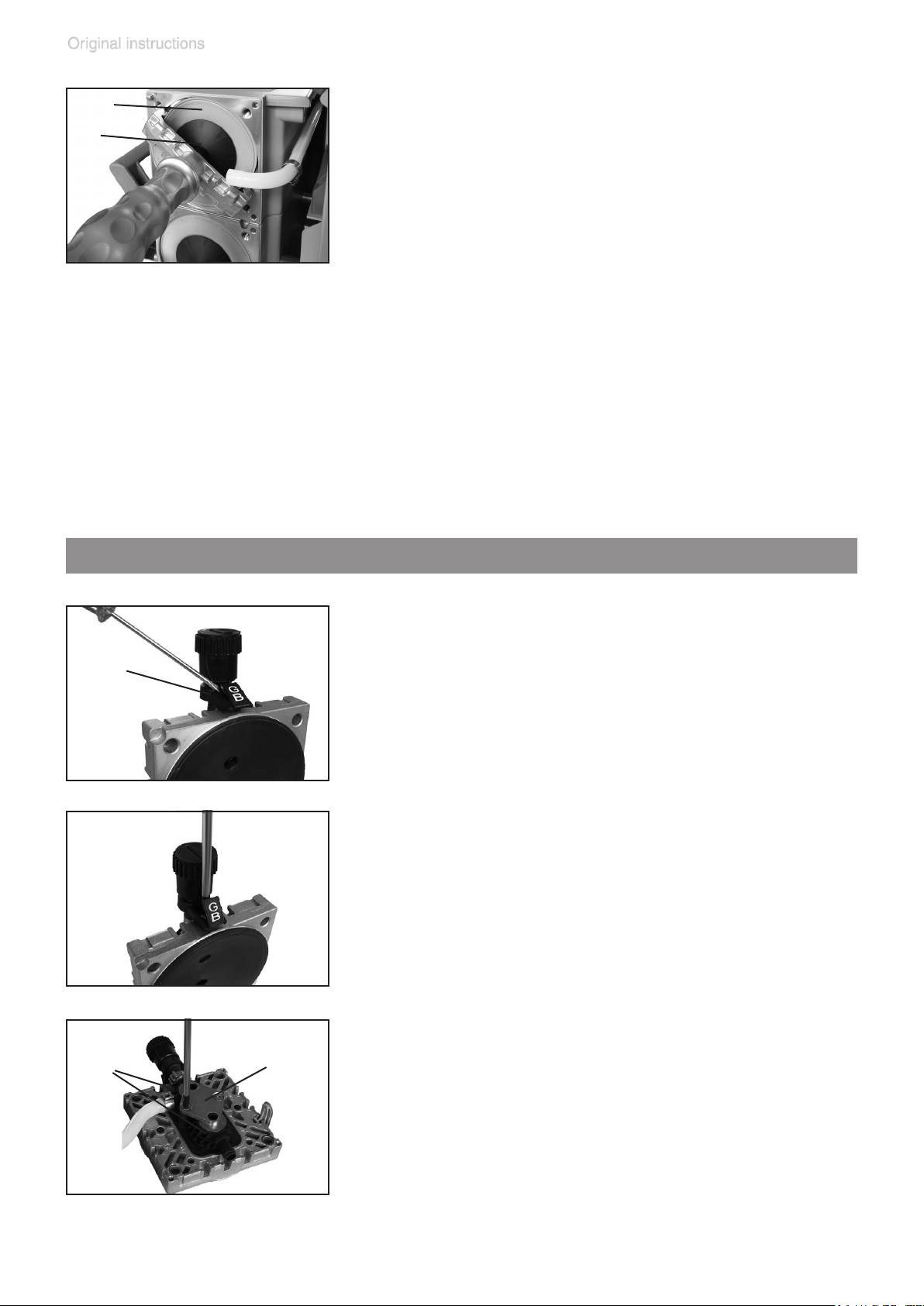
page 60 of 74
F
+ Assemble the original number of washers
G
(D) between diaphragm support disc (E) and
connecting rod (B).
➨ Screw diaphragm clamping disc (G), dia-
phragm (F), diaphragm support disc (E), and
washers (D) to connecting rod (B).
.
➨ Optimum torque for the diaphragm support disc: 4.4 ft
lb
(6 Nm), it is
f
recommended to use a torque wrench. Attach torque wrench to dia-
phragm key (hexagonal bolt 6 mm wide).
Note: Never use the diaphragm key with any additional tools like tongs
or Allen keys without appropriate torque limitation.
Replacing the valves
➨ Open the hinged cover of the connection
fastener (Q) with a slotted screwdriver.
Q
Loosen connection fastener slightly.
➨ Turn the llister head screw (L) with a Torx
driver T20 at most one turn.
+ Do not detach the llister head screw from
the square nut (K).
Loosen the clamping brackets (S) on the valve
S
heads (O).
O
➨ Unscrew at each clamping bracket the two
countersunk screws with a Torx driver T20.
Remove the clamping brackets.

page 61 of 74
➨ Remove valve heads (O) along with the disc
O
Q
springs (R), connection tube if applicable,
hose nozzles (P) and connection fasteners
(Q) or move the valve heads carefully aside.
R
Note position and orientation of the valve
N
heads.
+ Note position and alignment of valves (N).
➨ Check valves (N) and O-rings (M) for damage and soiling.
➨ Replace valves or O-rings if necessary.
➨ Use petroleum ether or other industrial solvent to remove deposits. Do
not inhale vapors.
➨ Insert O-rings (M) and valves (N). See gure
for the correct position of the valves:
EX
+ Inlet side (IN):
IN
Marked ”IN” next to the valve seat. The valve
M
tongue points at the kidney-shaped orice in
N
the valve seat.
+ Outlet side (EX):
Marked with ”EX” next to the valve seat. The
valve is oriented the same direction as the
valve at the inlet side.
➨ Position valve heads (O), with hose nozzle
O
(P), if applicable, connection tube or connec-
tion fastener (Q), and disc springs (R) on the
valve seats. Position disc springs with large
opening downwards. Pay attention to the
R
correct orientation of the valve heads.
+ Center the valve head with respect to the
valve seat. The valve head must lie at on
the valve seat.

page 62 of 74
Valve head with gas ballast or hose nozzle connection:
➨ Insert square nut (K) in the groove of the head cover (J) or position
square nut in the groove and then screw on connection fastener.
+ Loosely fasten llister head screw (L).
➨ Position clamping bracket (S) with counter-
S
sunk bores facing upwards.
➨ Align the countersunk bores with the thread-
ed pegs.
➨ Loosely fasten the countersunk screws and
correct the alignment of the valve heads if
necessary.
➨ Tighten countersunk screws with Torx screwdriver T20.
.
+ Torque: 2.2 ft
lb
(3 Nm).
f
➨ Bring the diaphragms (F) into a position, in
which they are in contact with the housing
(C) and centered with respect to the bore.
➨ Put on head cover (J) with valve heads (O)
and connections attached.
+ Pay attention to the correct orientation of the
head covers:
Housing with head alignment pin: The head
alignment pin (A) at the pump housing (C)
has to t into the recess at the head cover
(J).
Housing with mark (A): Align the recess at
the head cover with the mark at the pump
housing.
➨ Loosely screw in the Allen head screws (H)
H
at the head covers diagonally at rst slightly
with a 5 mm wide Allen key, then tighten.
.
+ Recommended torque: 8.9 ft
lb
(12 Nm).
f
➨ Slide the caps (I) into the head cover.

page 63 of 74
Afx the connection tube (V) to the other side of
the pump at the valve head (O).
Pump on pump support:
Afx the connection tube (V) to the other side
of the pump, as well as the hose connection to
the inlet or outlet of the vacuum system at the
valve head (O).
➨ Slip connecting tube (V) onto hose connection of valve head.
➨ Slide on the tube and the hose clip (U) until touching the nose at the
valve head.
➨ Close hose clip (U) with at pliers.
➨ Put head cover cowling on.
I
➨ Slide the head cover cowling in the grooves
of the caps (I) and under the connection fas-
teners (Q).
Q
➨ Install the washers. Use a Torx driver T20 to
attach the 4 screws holding the head cover
cowling.
➨ Tighten the llister head screws (L) of the
connection fasteners (Q) with a Torx driver
T20.
➨ Close the hinged covers.
Replace diaphragms and valves of the opposite side of
the pump in the same way!
Pump at pump support:
➨ Assemble catchpots (9) with joint clips.
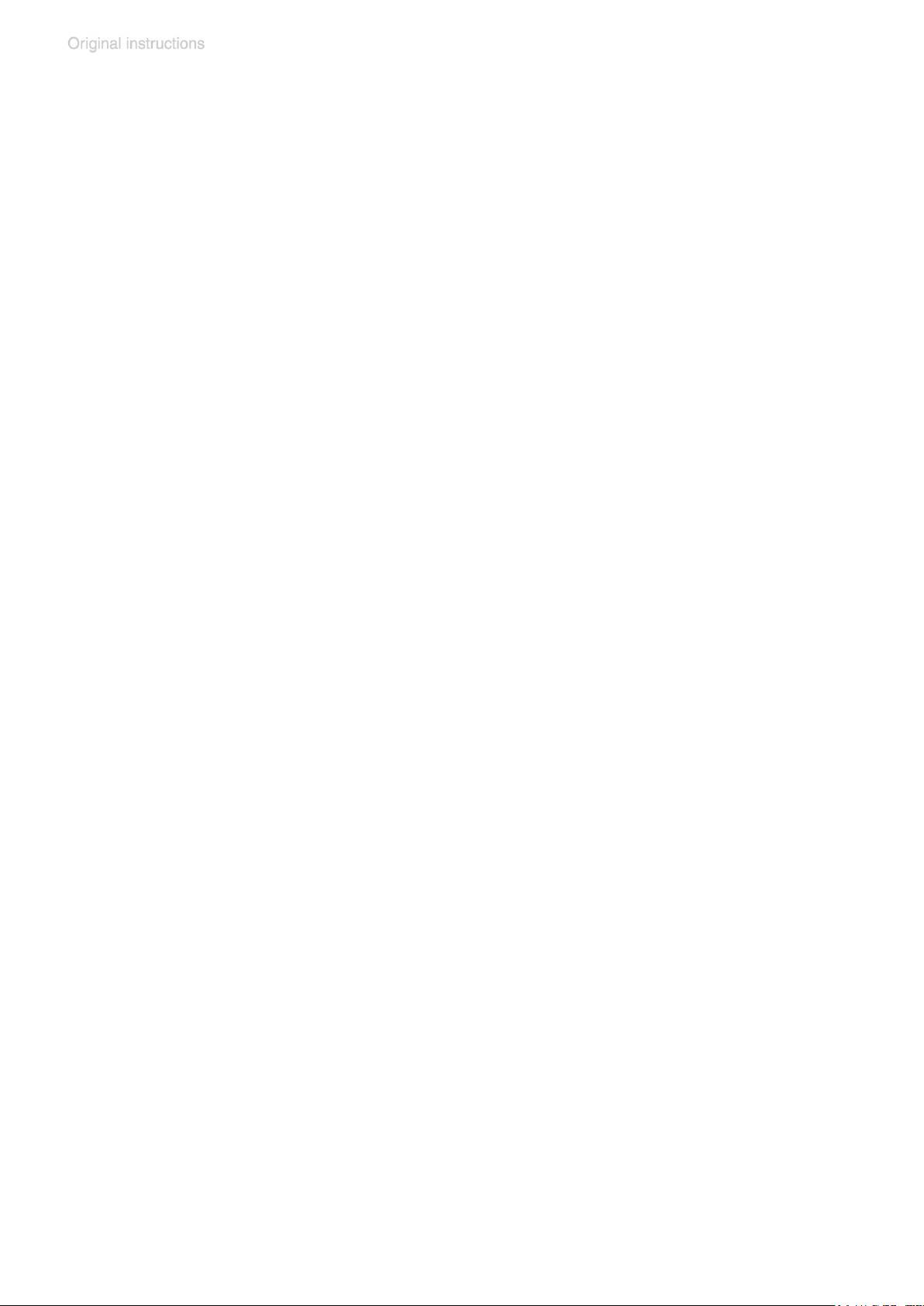
page 64 of 74
Checking the ultimate vacuum
➨ After any intervention at the equipment (e.g., repair / maintenance)
the ultimate vacuum of the pump has to be checked. Only if the pump
achieves its specied ultimate vacuum, the pump’s leak rate is low
enough to ensure that no explosive atmospheres will occur in the inte-
rior of the equipment.
If the pump does not achieve the ultimate vacuum:
- Whenever the diaphragms and valves have been replaced, a break-in
period of several hours is required before the pump achieves its ulti-
mate vacuum.
- In case of an unusual noise, switch off pump immediately and check
clamping disc positions.
If the specied ultimate vacuum is not achieved, and if this does not
change after the break-in period:
Check hose connectors at pump heads for leaks. If necessary recheck
valve seats and pump chambers.
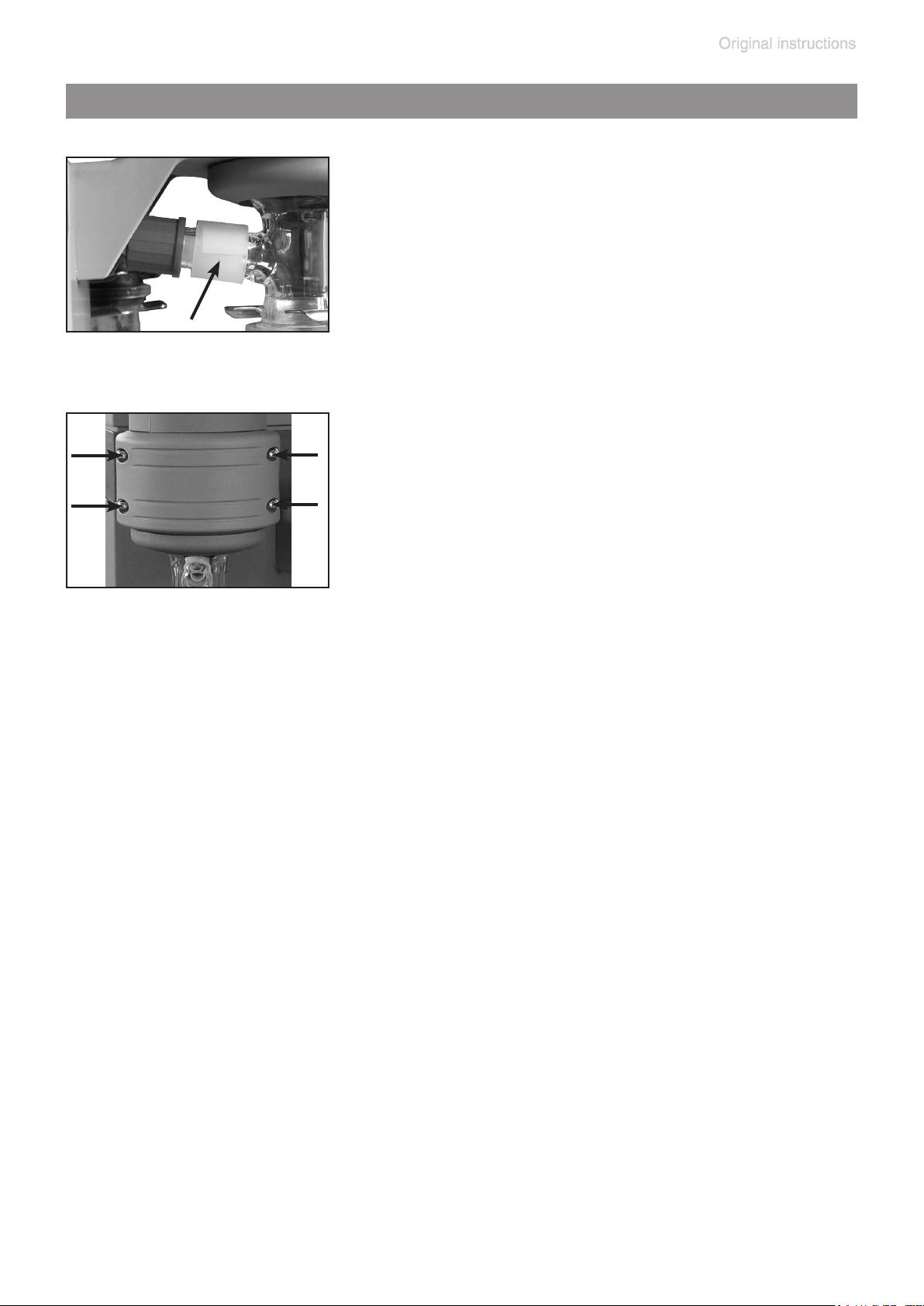
page 65 of 74
Replacing the overpressure safety relief device
Overpressure
safety relief device ............................ 638821
(at exhaust waste vapor condenser)
➨ Remove catchpot (9) at outlet (see ”Use and
operation”, pg. 38).
➨ Loosen the union nut at the inlet of the ex-
haust vapor condenser.
➨ Remove the 4 screws afxing the counter
holder of the exhaust vapor condenser with
a Torx driver T10. Remove the exhaust va-
por condenser. In doing so pull the PTFE
hose out of the inlet of the exhaust vapor
condenser.
➨ If necessary, pull off the old pressure relief
valve and install the new one. Check for cor-
rect position of the PTFE-foil under the pres-
sure relief valve.
➨ Feed the PTFE hose into the inlet of the ex-
haust vapor condenser. Mount the condens-
er with the counter holder (Torx screws T10)
to the pump. Fasten union nut.
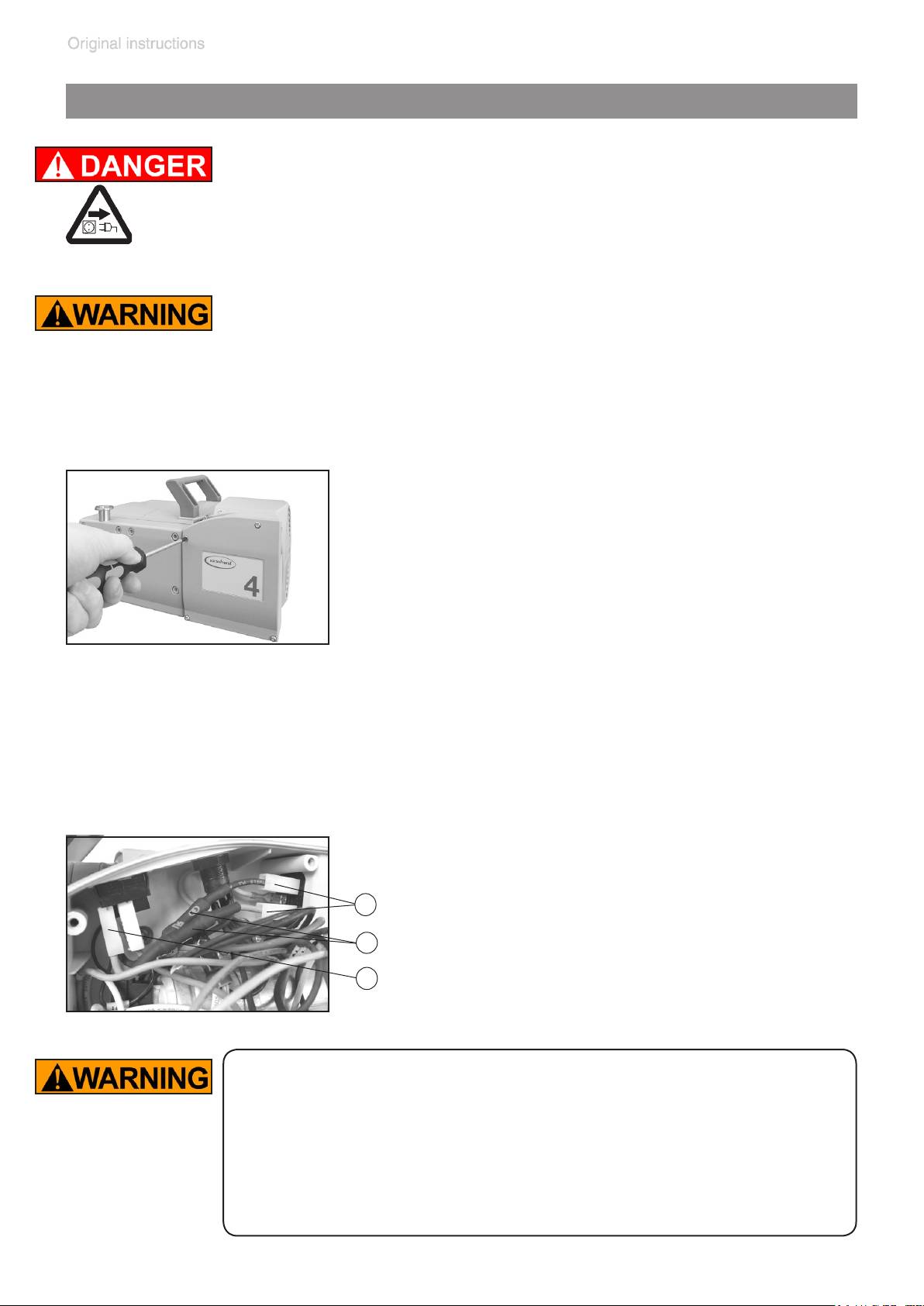
page 66 of 74
Replacing the fuse
➨ Switch off the pump.
➨ Disconnect the electrical power cord before opening
the terminal box. After disconnecting from power, wait
two minutes to allow the capacitors to discharge.
+ The replacing of the fuse has to be carried out by a
trained electrician.
+ After replacing the fuse, the pump must be checked for
electric safety (see below)! Identify and eliminate the
cause of failure before switching on the pump again.
The pigtail fuses are integrated into wires ((1),
black and blue) inside the terminal box.
To replace the fuses it is necessary to replace
both wires completely (xed with at pin bush-
ings (2)).
➨ Open the terminal box. Unscrew the four screws with a Torx driver
T20. Remove the terminal box cover. Remove both wires with inte-
grated fuses (xed with at pin bushings (2), see gure). Mount the
new wires (at pin bushings) and close the terminal box. Fasten the
cover with the four screws.
Order-no. Set of fuses NT............................636542
2
1
2
Important: Check operability and safety of the pump
after repair and after replacing the device fuse.
Check the electrical safety (protective conductor resis-
tance, insulating resistance, high voltage test) according
to IEC 61010 and national regulations.
Оглавление
- Contents
- Safety information!
- Technical data
- Use and operation
- Accessories
- Troubleshooting
- Replacing diaphragms and valves
- Notes on return to the factory
- Warranty